1. 引言
再流(回流)焊工艺作为表面组装技术SMT (Surface Mounted Technology)重要的一环,决定了印刷电路板PCB (Printed Circuit Board)的质量,进而直接影响电子产品的可靠性和焊接质量 [1]。回流焊机负责完成整个回流焊的过程,通过传送带将PCB板缓慢送至炉膛中完成指定焊点的焊接。回流焊机的回流焊温度曲线直接影响PCB板焊接质量 [2]。回流焊温度曲线受回焊炉参数所控制,参数设置不当会导致元件变形,断裂等,使成品率下降。SMT在近20年取得了飞速的发展和应用,并向着更高密度、超微型化方向发展。与此同时,对组装的工艺范围要求也越来越窄,对回流焊曲线要求更严格,即满足电路可靠连接的情况下,保证越来越轻薄的PCB板受热性良好,不易变形 [3]。
为了优化对回流焊工艺曲线的控制,国内外学者针对回流焊温度曲线控制进行了研究。冯志刚 [4] 研究了温度曲线受回流焊工艺参数的影响,张辉华 [5] 在混装氮气回焊炉中优化了回流焊温度曲线控制,Gabriel Takyi [6] 利用田口方法优化回流焊温度曲线。传统的经反复试验和调整来控制回流焊温度曲线的方法越来越不能满足上述要求。同时,传统方法会耗费大量时间与经费,不能适应当前电子产品更新速度快、竞争日益激烈的要求。作为一种简单实用的回流焊温度曲线控制方法,对回流焊工艺建模和仿真得到了广泛的关注 [7]。目前回流焊温度曲线计算机仿真和预测系统主要是以F. Sarvar为代表 [8]。国内的龚雨兵也通过数值建模与仿真获取了优化的回流焊温度曲线控制。Transient Thermal是有限元软件ANSYS Workbench的热瞬态分析模型,支持三维建模分析并提供各个时态的温度场,便于形成目标温度曲线 [9]。将数学模型与Transient Thermal相结合,可以提高回流焊温度曲线控制的精度与效率 [10]。
本文以回流焊炉为研究对象,针对回流温度曲线,以满足工艺要求并且实现最大经济效益为目标,以热传递为理论基础,基于Thermal Transient仿真建立模型,通过调整控制小温区以及过炉速度,实现满足工艺需求基础上利益最大化,为回流焊温度曲线控制提供决策支持。
2. 数据来源与模型假设
数据来源于2020高教社杯全国大学生数学建模竞赛。
[http://www.mcm.edu.cn/html_cn/node/10405905647c52abfd6377c0311632b5.html]
由于回流焊炉的品牌与类型的不同,加热的种类、热电偶放置位置有差异,故选择题目数据作为研究对象进行假设与建模。
以题目中的某回流焊炉为例,回流焊炉构造如图1所示。该回流焊炉内部设置有11个小温区,即11个加热源。它们从功能上可分为四大温区:预热区、恒温区、回流区和冷却区。一个大温区可能包括多个小温区。每个小温区长30.5 cm,相邻小温区之间的间隙长为5 cm,炉前区域和炉后区域长均为25 cm。实际生产时,通过调节各温区的设定温度和传送带的过炉速度,来优化回流焊温度曲线。结合实际情况以及经验,调整时要求小温区1~5中的温度,小温区8~9中的温度都要保持一致,小温区10~11中的温度保持25℃。各温区设定温度以及传送带过炉速度需要满足特定的工艺要求,才能实现回流温度曲线的优化,进而高质量高效率的生产PCB板 [11]。具体工艺要求映射成对回流焊温度曲线的约束,这写约束被称为制程界限,如表1所示。
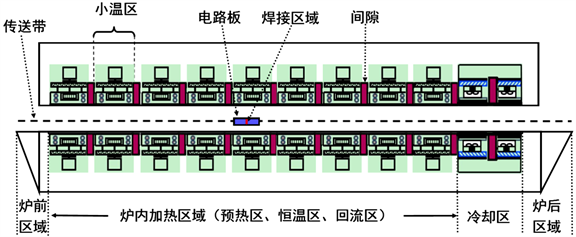
Figure 1. Section diagram of reflow oven
图1. 回焊炉截面示意图
本文根据上述条件,将回焊炉内部简化整合,得到图2回焊炉简化结构图。
1~11为小温区的加热区域,即小温区的热源,下面为对称结构。T1~T5为5个大温区的设定温度。回流焊炉内部长度为385.5 cm,总长为435.5 cm,具体内部结构数值根据背景已标注在结构图中。
建立数学模型之前,进行如下假设:
1) 回流焊机内部传热左右对称,只考虑横截面上二维传热,方式为自然传热。
2) 传送带上的炉内温度近似等于小温区下端边沿为水平线上的温度。
3) 回焊炉小温区加热源为整体,稳定时内部各点及边界的温度一致。
4) 不考虑空气流动对回流温度曲线的影响。
5) 传送带温度变化敏感,无延迟和突变。
6) 环境温度为恒温25℃。

Figure 2. Simplified structure of reflow oven
图2. 回焊炉简化结构图
3. 模型建立与求解
基于Transient Thermal的回流焊温度曲线控制方法的流程图如图3所示。方法通过建模求解出炉内温度曲线,结合Transient Thermal仿真最终获得回流焊温度曲线。炉内温度曲线规定为PCB板在某一时刻下的环境温度。回流焊温度曲线是PCB板温度随时间变化的曲线。炉内温度曲线不同于回流焊温度曲线,前者为PCB板的周围环境的温度曲线,后者为PCB板的真实温度曲线。工艺规定当炉内温度达到稳定时,才将PCB板放到传送带输入端(最左端),并记为炉内温度曲线开始的零时刻。基于一维热传导方程进行建模可以求解出回焊炉稳定后的小温区之间间隙温度分布曲线,结合各小温区加热源已知温度,求解出炉内温度随位置变化的分布曲线。通过传送带速度将炉内位置温度曲线映射到传送带某一点炉内温度随时间变化的曲线,即炉内温度曲线。根据建模求得的炉内温度曲线设定PCB板环境温度,基于Transient Thermal进行仿真分析,最终得到PCB板的回流焊温度曲线。

Figure 3. Flow chart for method based on Transient Thermal
图3. 基于Transient Thermal方法流程图
3.1. 稳定后间隙温度建模与求解
回焊炉启动后,会在短时间内达到稳定,此后回焊炉才能放入PCB板进行焊接工作。虽然稳定后小温区的边缘温度能确定,但是小温区的间隙内各位置的温度不确定。确定两恒温源之间的温度分布曲线需要通过热传导方程进行建模求解。以下为热传导方程:
(1)
小温区的间隙两边都是稳定已知温度,而且间隙两边长度远远大于间隙,可视为无限大恒温热源平面。如图4,建立间隙温度模型,通过一维热传导方程求解稳定后各点的间隙温度分布规律。
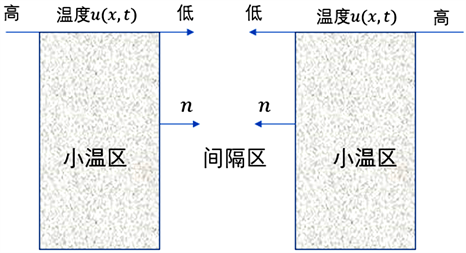
Figure 4. Gap between temperature zone model
图4. 小温区间隙模型
假设两小温区为无限大恒温热源平面,相距0.2 m,左温区平面恒为40℃,右温区平面恒为20℃。根据一维热传导偏微分方程组,每隔一定时间得到一组解,对比不同时间下的各点位置对应温度。如图5小温区间隙温度分布按时间从左至右排列,发现最终稳定时,间隙各点温度在空间上从40℃到20℃线性递减。通过上述规律可以推导出:在回焊炉温度稳定后,小温区之间的间隙温度随位置呈线性关系,由间隙左边的小温区的温度与右边的小温区的温度确定。结合已知炉内各小温区区域的恒温温度,可以进一步求解稳定后炉内温度曲线。
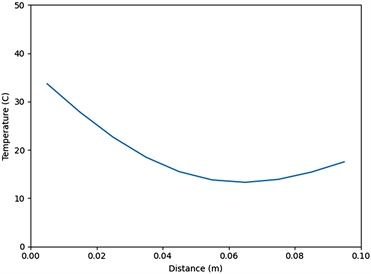
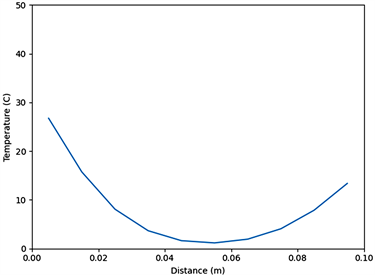
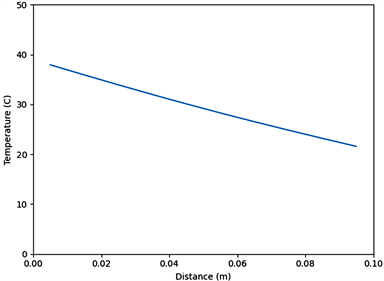
Figure 5. Temperature distribution in gap between temperature zone
图5. 小温区间隙区域温度分布
3.2. 稳定后炉内温度曲线建模与求解
炉内温度曲线,不同于回流温度曲线,表示某一时刻传送带上某一点的环境温度。得到炉内温度曲线,才能设定PCB板的环境温度,从而通过仿真最终得到回流温度曲线。如图6,当回焊炉温度稳定后,通过小温区以及间隙区温度分布规律可以得到炉内稳定后各点温度分布。通过传送带的速度,可以构建温度在各个位置的分布与传送带某一点温度随时间变化的映射。通过映射关系,得到回流焊炉内温度曲线,为基于Transient Thermal仿真提供环境温度设置的参考。
3.3. 仿真建模与求解
在炉内温度稳定的情况下,借助热力学仿真软件求解出焊接区域温度曲线,即回流温度曲线。目前用于热力学仿真的软件有ANSYS、FLUENT、Flotherm等,都采用了面向对象模拟仿真技术。本文采用ANSYS中的Transient Thermal进行建模仿真。Transient Thermal是ANSYS公司专门为研究瞬态热力学分析设计的模块,适合本文的应用场景。PCB板大部分是由铜组成,焊接区域是焊锡膏排版的区域,此处温度随时间的曲线就是回流温度曲线。故PCB以铜板进行参数设置,焊接区域的参数设置以常用焊锡膏的主要成分SnPb为准。模型假设集成电路板在放到传送带前,环境温度已经稳定,并不会受到电路板与传送带的影响。当电路板放置到传送带最左端时,就开始进行回流加热并记录回流温度曲线。电路板分析过程中所需要的所有参数可见表2。电路板的三维模型见图7。
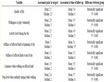
Table 2. Parameter of simulation model
表2. 仿真模型参数设置
根据表2中PCB板子尺寸参数和焊接尺寸参数对PCB电子电路板进行仿真建模,仿真模型的结构如图7所示。对仿真模型进行参数设定,将仿真模型的比热、密度、导热系数设定为铜(Cu)的参数,将仿真模型中焊锡膏部分设定为锡铅焊料(SnPb)的参数。以空气作为介质设定PCB加热环境参数。将基于一维热传递模型求解出的炉内温度曲线设置为PCB板的环境温度曲线,进行仿真最后仿真出PCB板随时间的温度变化曲线,即回流焊温度曲线。
竞赛数据附件是某次实验得到的回流温度曲线,各温区设定分别为175℃ (小温区1~5)、195℃ (小温区6)、235℃ (小温区7)、255℃ (小温区8~9)及25℃ (小温区10~11);传送带的过炉速度为70 cm/min。得到对应的环境温度后,通过Transient Thermal进行参数设置以及仿真,设置时间为400 s,得到仿真回流曲线。将附件中的数据制成回流曲线与仿真回流曲线进行比较。如图8,蓝色曲线代表仿真回流温度曲线,红色曲线代表实际回流温度曲线,分析得到两者拟合度R2 = 0.96283 > 0.95,说明基于Transient Thermal的仿真建模求解出的回流温度曲线是合理的。
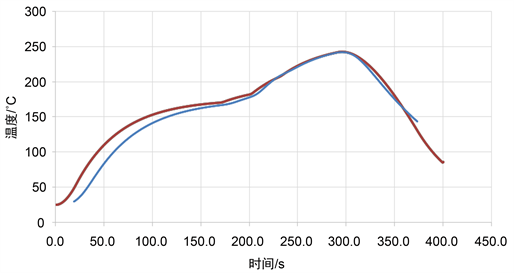
Figure 8. Verification of reflow temperature profile
图8. 回流温度曲线验证
4. 仿真模型应用
改变参数,利用Transient Thermal进行多次仿真实验,积累一定量的原始数据。本文采用逐步回归分析的方法,利用多次试验后的数据进行分析。结合表1制程界限的工艺要求,分析得到主要制程界限与5大温区温度设定T1~T5和传送带速度V的关系式,从而解决回流焊温度曲线因素过多的问题:
(2)
(3)
(4)
(5)
观察公式(2) (3) (4) (5),发现温度大于217℃的时间与前四个大温区温度设置成正比而与传送带速度成反比。温度上升过程中在150℃~190℃的时间只与传送带速度成反比。峰值温度与后两个大温区温度设置成正比而与传送带速度成反比。超过217℃到峰值温度所覆盖的面积与前四大温区成正比而与传送带速度成反比。将公式(2) (3) (4) (5)代入制程界限的范围得到多元一次不等式方程组:
(6)
求解不等式方程组(6),得到不等式方程组的解。为了使回流焊工艺取得最大的工作效率从而获得更高的经济效益,将传送带速度与取到最大值。将传送带速度带回公式(5)使得超过217℃到峰值温度所覆盖的面积最小,得到最终控制参数:
(7)
再将最终控制参数代入Transient Thermal进行仿真,仿真得到各工艺参数为:
(8)
对比表1,发现各工艺参数满足制程界限的同时,能实现传送带速度最大化,意味着在保证工艺标准的同时,能最大化提高回流焊工艺流程的速度,实现利益最大化。如图9,最优的回流温度曲线如下图所示。
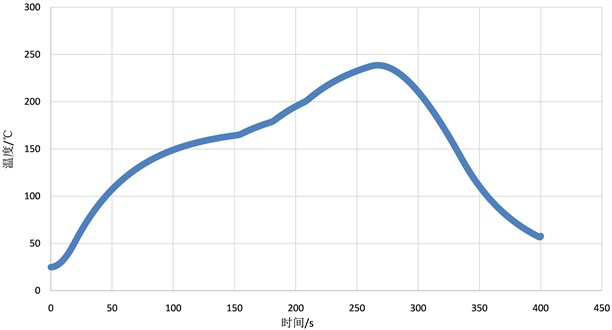
Figure 9. Optimal reflow temperature profile
图9. 最优回流温度曲线
通过建立热传递模型结合Transient Thermal仿真求解出最优参数设置:五大温区温度设置分别为165℃、185℃、225℃、265℃、25℃,传送带速度为82.44 cm/s,进一步优化了回流焊温度曲线。分析逐步回归得到的制程界限与各参数的关系式可以发现,传送带速度所占的权重相比于个温区温度设定要大很多,说明传送带速度对于回流焊温度曲线影响是最大的。优化回流焊曲线的控制,传送带速度的设定是非常重要的。传送带的速度快慢会影响回流焊的保温时间,加热因子和峰值温度,进而影响回流焊温度曲线的各项工艺指标。基于Transient Thermal的仿真建模方法可以取得高精度的传送带速度,方法从结果上看是可行的。结果分析温区设置参数,除去恒定的第五个大温区降外,可以发现前四个大温区温度全部设定在极值。前三个大温区均为温区最小值,而第4个大温区为温区最大值。标准回流焊温度曲线分为四大温区:升温区、保温区、焊接区、冷却区 [1]。第一个温区为升温区,第二第三温区一并为保温区,第四温区为焊接区,最后第五温区对应冷却区。对回流焊影响最大的温区主要是保温区与焊接区。分析制程界限也可以发现,并不是所有工艺限制可以同时满足的。大于217℃的时间与超过217℃到峰值温度所覆盖的面积或者峰值温度不能同时满足。基于Transient Thermal的仿真一次只需要3分钟,而如果要进行实物实验,整个回流焊工艺需要10分钟左右,还需要一定PCB板与焊锡膏等材料 [1]。对比说明该方法在时间上的高效率与低能耗。
回焊炉参数设置得到的结果制程界限在满足基本工艺要求的同时,优化了回流焊温度曲线的控制,提高了回流焊工艺质量与效率。满足工艺需求基础上利益最大化。
5. 结论
本文以Transient Thermal仿真软件为工具,以竞赛题目给出的回焊炉为研究对象,调整温区设置温度以及传送带速度,优化回流焊温度曲线控制。通过建立热传递模型结合Transient Thermal仿真,在一系列工艺要求下通过逐步回归分析,选择最合适的温区设置以及传送带速度,从而获得最优的回流焊温度曲线,进而满足工艺需求基础上利益最大化。
NOTES
*通讯作者。