1. 引言
随着社会经济的发展,工业水平的提高,市场对合金材料的性能要求日渐提高。磨损是工件在使用过程中,不可避免的破坏形式,有可能造成工件使用寿命减少,工作效率低下,生产成本增加。一般来说,耐磨性取决于基体微观结构、碳化物类型和特征即尺寸、形态、分布和取向 [1],以及合金的体积分数、断裂韧度以及硬度 [2] [3],同时加载条件、摩擦学环境的特点、接触面的相对运动以及磨粒体的类型和尺寸对耐磨性的影响也十分重要 [4] [5]。对于钢铁材料,其磨损特征与其冶炼过程、热处理、碳含量、硬度以及合金元素密切相关,特别是其微观组织对耐磨性影响巨大 [6]。锰铁合金作为耐磨性材料,被广泛运用在交通工具、桥梁建筑等工业生产的方方面面,是当今全球范围内学界研究的热点话题。作为具有优良性能的耐磨性材料,锰铁合金常以中锰铸铁形式运用在生产和生活中。针对中锰合金的微合金化、组织结构、热处理工艺以及摩擦磨损性能等,国内外学者进行了研究与讨论,尤其是作为耐磨材料,其耐磨性能更是一个热点话题 [7] [8] [9]。中锰铸铁依赖于合金化和热处理以提高硬度,消除组织中的残余奥氏体以获得更多数量的马氏体和贝氏体,提高铸铁的韧性与耐磨性 [10]。研究发现,对于铸铁而言,若组织结构演变过程中产生了马氏体相变,则所形成的马氏体使得材料具有较高的硬度、强度和韧性,同时表现出良好的耐磨性能 [11]。对于拜耳法赤泥与锰矿结合还原提炼的锰铁合金,其成分复杂,无法直接用于工业生产,需要通过热处理改善其组织和性能,尤其是耐磨性能,并且对其工作时的磨损机理进行更深入的分析和研究,使其具有更优的实用性,达到更高的生产要求。
2. 实验方法
2.1. 试样制备
通过ARL iSpark 8860直读光谱仪可得到实验用中锰铸铁化学成分(质量分数)见表1。
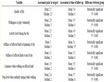
Table 1. Composition of medium manganese cast iron as cast
表1. 铸态中锰铸铁成分
试样中Si的含量较高,是抑制中锰铸铁白口倾向的重要元素,能够降低固溶体中的碳浓度,降低奥氏体的稳定性,从而促进奥氏体的分解,在一定程度上对试样的耐磨性能产生影响 [12]。同时,碳含量对试样耐磨性也存在一定影响,研究表明,合金中碳含量过高,热处理后形成高碳马氏体组织,热处理时容易形成裂纹,而碳含量过低,铸件淬透性差,硬度低,耐磨性差 [13]。
采用GP-25高频感应炉对原料进行熔炼,使用热电偶测量温度,浇铸温度大约为1500℃。将金属液浇注成金属锭,对金属锭进行不同工艺的热处理。待金属锭冷却至室温后将其切割为φ4 × 30 mm的磨损式样,用砂纸打磨以去除表面的氧化膜,对试样进行磨粒磨损试验,探究磨损性能和磨损机制。
中锰铸铁编号及热处理见表1。采用马弗炉对分组试样分别进行热处理,淬火温度为800℃、850℃、900℃,保温2 h,水冷;并配以200℃、400℃、600℃的回火处理,保温2 h,水冷。淬火的目的是将奥氏体转变为马氏体或贝氏体。同时配合不同温度回火,提高钢材的刚度、硬度、耐磨性、疲劳强度和韧性,以满足各种机械零件和工具的不同要求 [14] [15]。
2.2. 磨粒磨损试验
采用ML-100型磨粒磨损试验机对磨损试样进行磨粒磨损实验,实验原理如图1。
将试样进行超声波清洗和干燥后,使用1000目金相砂纸,载荷为10 N,对试样进行预磨损,目的是磨去试样表面氧化层,使试样露出新鲜表面。使用180目金相砂纸,载荷为15 N,对试样进行磨粒磨损实验,预磨损和磨损实验后均使用精度为0.1 mg的分析天平进行称量,并取两次称量值之差为失重量,进而计算出磨损率。
磨损率可通过下列式子求出:
(1)
式中:δ为试样磨损率,%;W1为试样磨损前的质量,mg;W2为试样磨损后的质量,mg。
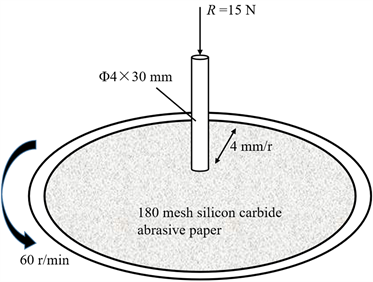
Figure 1. Principle of abrasive wear test
图1. 磨粒磨损实验原理图
3. 结果与讨论
3.1. 热处理对耐磨性能的影响
磨粒磨损实验结果如表2。
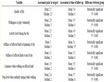
Table 2. Experimental results of abrasive wear
表2. 磨粒磨损实验结果
Bansal等人的研究表面,淬火后铸铁中残余奥氏体的存在大幅度增加了材料的冷作硬化性能和冲击韧性,从而提高了材料耐磨性能,但是磨损表面粗糙 [16]。可以观察到,和铸态试样相比,经过热处理后的试样整体磨损率增加,耐磨性减弱。在相同的淬火温度下,随着回火温度的增加,由于残余奥氏体逐渐分解,碳化物逐渐减少,试样磨损率逐渐增大,耐磨性减弱。在二体式磨粒磨损中,磨粒的切削收到周围磨粒的限制,基体对碳化物起到保护作用,当磨粒硬度较大时,切削宽度收到碳化物的限制,若碳化物数量增加,则它们的间距就会减少,磨粒侵入基体深度减小,即碳化物对基体起到保护作用 [17]。而当碳化物减少,即使得基体失去保护,耐磨性减弱。
而在相同的回火温度下,随着淬火温度的增加,试样的磨损率逐渐增大,耐磨性能逐渐减小。当850℃淬火600℃回火时,试样耐磨性能最差。这是由于,淬火的主要目的是使奥氏体化后的工件获得尽量多的马氏体,而马氏体的形成降低了起始与结束温度,且微观结构中残余奥氏体的数量引起体积膨胀,此时在高应力磨损下,马氏体组织的磨损性能是奥氏体组织的2~3倍 [3]。
3.2. 磨损表面形态分析
图2(a)~(i)对应第一组到第九组不同热处理试样的磨粒磨损表面。结合磨损试样表面形貌图于热处理工艺和磨损率表,可以观察到热处理后的磨损试样表面犁沟都较为明显且分明,整体来看热处理后的磨损试样表面分布着不同数量和程度的裂纹,尤其是在高温淬火时,试样磨损表面出现较多由磨料引起的凹凿坑、剥落以及裂纹,犁沟不连续,整体较为破碎。
在高温回火的条件下,试样磨损表面变形严重,出现了不同程度的剥落、凹坑、孔洞以及裂纹。由图2(c)、图2(f)、图2(i)可以观察到由磨料引起的凿削坑、碳化物脱落后留下的凹坑,以及由于疲劳变形产生的鱼鳞状磨屑,周围犁沟较深,但同时犁沟两侧卷曲较少,即试样塑性较差,试样的耐磨性较差。图2(f)为850℃淬火高温回火处理后的磨损试样,试样表面在磨料的作用下产生了更严重的磨屑堆积和塑性变形,犁沟中断,并且分布着大量的裂纹和碳化物脱落留下的凹坑以及孔洞。图2(i)为900℃淬火高温回火处理的磨损试样,犁沟整体破碎不连贯,有较多碳化物脱落留下的凹坑以及磨损产生的裂纹,但由磨料产生的磨屑堆积较少,和第3组、第6组试样相比,耐磨性较好。结合磨损实验数据和图像可以看出,在高温回火的条件下,试样耐磨性较差,并且850℃淬火600℃回火的试样磨损性能最差。
因此在高温回火的条件下,试样整体耐磨性能较差,随着淬火温度的增加,试样的表面磨损变形逐渐严重,耐磨性逐渐变差。
由图2(a)、图2(d)、图2(g)在低温回火的条件下,磨损试样犁沟较为平整且连贯,相比高温回火的条件下的磨损试样,其犁沟较浅,耐磨性能整体较好。从图中可以看出,磨痕的主要形式是犁沟,并伴随着一定量的裂纹、卷曲和凹坑,犁沟两侧存在着由于塑性变形产生的卷曲。并且在低温回火的条件下,随着淬火温度的升高,试样磨损表面由于磨损出现了明显的裂纹和剥落,试样塑性逐渐变差,同时犁沟逐渐变得明显且深,两侧卷曲和剥落严重,最后在900℃淬火时出现了较大形变和大量凹坑、空洞,耐磨性逐渐下降。
对于不同淬火温度分组下,可以观察到相同淬火温度的条件下,当回火温度增加时,试样磨损表面变形逐渐严重,出现了大量卷曲和剥落,以及凹凿坑。尤其是在900℃时,如图2(g)~(i),回火温度变化对试样磨损性能影响严重,当高温回火时,犁沟不连贯,表面破碎,磨损性能差。
3.3. 磨损机制分析
磨粒磨损可分为切削磨损和形变磨损两个方面 [18]。其中,切削磨损是试样材料表面和磨料相互摩擦运动时,磨料对试样材料进行切削和冲刷而形成的;形变磨损是由于磨料在垂直的作用力下,挤入试样内部从而引起试样材料形变。在实际的磨损实验中,两种磨损形式同时存在,但由于具体实验条件和工况的不同,更应偏向以两者中的某一种形式为主导。
同时对于形变磨损,根据所受应力的大小不同,又可以分为凿削式磨损、高应力碾碎性磨粒磨损以及低应力擦伤性磨粒磨损。当磨料与试样表面的最大压应力超过磨料的破坏强度时,则产生高应力碾碎性磨粒磨损,从而导致脆性金属碎裂剥落,韧性金属产生形变和疲劳;反之,最大应力低于破坏强度时,产生低应力擦伤性磨粒磨损。本实验中,磨粒磨损实验采用ML-100型试验机,磨损形式以形变磨损为主,并且属于高应力碾碎性磨损。通过对试样磨损表面SEM可以观察到试样在不同热处理下,摩擦表面有着不同深度的明显犁皱形成的沟槽和塑性变形,同时表面有着不同程度的剥落和破碎,磨损破坏方式表现为犁沟切削。犁沟切削属于微观切削磨损,即法向载荷将磨料压入磨损表面后,在切向摩擦力作用下使材料表面产生切削,同时可能使得表面出现疲劳开裂区,即在接触力的作用下磨料压入磨损表面后,材料局部因疲劳而产生的磨损剥落破坏 [7]。
在ERabinnowicz [19] 的磨粒磨损模型中,如图3所示,硬材料的凸出部分或磨料被施加的压力F压入软材料中,该压力与凸出部分在水平面的投影面积之比(假设为圆形)达到软材料的压缩屈服强度时,此时压入会停止。
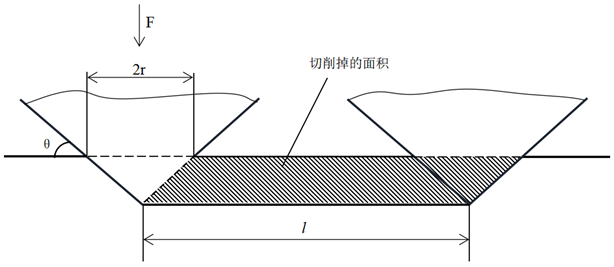
Figure 3. Simplified cutting model of abrasive wear
图3. 磨粒磨损简化切削模型
可以用公式(1)来表示。
(1)
若凸出部分与软材料表面的夹角为θ,当摩擦滑动一段较长的距离l时,软材料被切割或冲刷下来的体积为V。
(2)
(3)
其中K为系数。即磨粒磨损量收到压力、摩擦距离以及材料的硬度影响,与材料硬度成反比,还与磨粒的形状有关。在实际的实验中,并不是所有磨粒都切削产生磨屑,而是大部分磨屑嵌入材料材料表面,产生塑性变形,使之堆积在犁沟两侧。在本实验中,大部分表现为犁沟两侧卷翘堆积,并且由于磨损性能的不同,堆积卷曲的程度不同并伴随着一定的剥落。
ERabinnowicz的磨粒磨损模型表明,硬度对耐磨性能有着重要的影响。由于试样硬度和试样化学成分与显微组织有关,因此耐磨性还取决于材料的显微组织。
淬火后试样得到马氏体和贝氏体等,并且随着淬火温度增加,试样的硬度提高,但过高的淬火温度容易使得奥氏体晶粒粗大,造成硬度略有降低。由于奥氏体和20%残余奥氏体的下贝氏体有较高的应变硬化能力和延展性,奥氏体、贝氏体组织的耐磨性优于同等硬度的铁素体、珠光体和马氏体 [3]。由于马氏体有很高的强度、硬度,而残余奥氏体具有良好的塑性,能承受一定程度的塑性变形,可阻止碳化物在磨粒磨损时剥落,因此能够提高试样的耐磨性能 [20]。当试样淬火后回火使得奥氏体分解,并且随着回火温度的提高,试样的碳化物减少,试样硬度降低,且同时影响试样的耐磨性能,使得试样耐磨性降低。
4. 结论
1) 经过不同热处理的中锰铸铁整体上耐磨性能减弱。在相同的淬火温度下,随着回火温度的增加,试样磨损率增加,耐磨性减弱,试样磨损表面犁沟逐渐变深,磨料在两侧堆积情况越严重。在相同的回火温度下,随着淬火温度的增加,试样马氏体数量逐渐增加,耐磨性有一定程度的减弱,尤其是在高温回火的状态下,试样变形严重,磨损表面破碎不连贯,在磨料的作用下产生大量的形变,磨损性能较差。
2) 使用ML-100型磨粒磨损试验机,以ERabinnowicz磨粒磨损模型为基础,试样在磨粒磨损实验中,主要磨损机理是以形变磨损为主导的高应力碾碎性摩擦磨损,及伴随着碳化物的脱落和大量空洞,其磨损破坏形式主要表现为犁沟切削。同时试样的组织和硬度对试样的磨损性能也有较大影响。
基金项目
广西重大科技专项(桂科AA18242001)。