1. 引言
选厂设计遵循原矿处理量要大、工艺流程要简化、减少入磨矿石量、最大限度地降低矿物加工过程中的能耗和其他原材料消耗,降低选矿成本等原则 [1] [2]。针对该多金属矿的复杂性和选矿技术难题,多家选矿试验单位详细研究了矿石的工艺矿物学特征,并做了矿石可磨度试验、铜锌浮选试验、细粒锡石(−0.038 mm)浮选试验和全流程试验等,并根据最佳的试验结果给出了推荐的工艺流程。设计按照新技术、新装备、新工艺的全新定位理念 [3],根据推荐的工艺流程,设计了大型的多金属选矿厂,选厂投产以来,生产状况较好,环保、节能效果显著。本文对该大型的多金属选矿厂设计和生产情况进行了分析,为高效开发回收利用复杂多金属矿山矿产资源选厂设计人员和生产技术人员提供参考。
2. 工艺矿物学研究
某多金属矿矿区矿石类型为锡石硫化物–矽卡岩型,矿物组合和化学成分比较复杂,具多金属矿化特点。矿石类型按硫化物氧化程度划分,绝大部分为原生矿、混合矿;按主金属锡、锌空间分布特征,具锡–锌共生矿石,单锡矿石和单锌矿石三种金属类别,其中以锡–锌共生矿石为主体。按矿物自然组合特征,大致分为锡石硫化物型、锡石矽卡岩型、锡石磁铁矿型,以锡石硫化物型矿石为主。原矿多元素分析结果见表1。
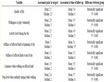
Table 1. Multi-element analysis of raw ore
表1. 原矿多元素分析
矿石中主要金属矿物有铁闪锌矿、磁黄铁矿、黄铁矿、磁铁矿、锡石、黄铜矿、毒砂等;主要脉石矿物为钙铁辉石、透辉石、绿泥石、阳起石、绿帘石、白云母、石英、萤石等。其中锡主要以锡石出现,锡石锡占全锡的80%~90%,其嵌布类型为微细粒嵌布,主要粒度范围为5~40 μm,其中−20 μm占55.67% (与硫化物紧密共生);锌以铁闪锌矿、闪锌矿为主,其次为菱锌矿、异极矿、水砷锌矿等,铁闪锌矿中富集一定量的铟、镉,铁闪锌矿的嵌布粒度较均匀,主要粒度范围为0.02~0.32 mm;铜以黄铜矿为主,主要为原生硫化矿,黄铜矿的粒度呈极不均匀嵌布,粒度分布范围较广,主要粒度范围为0.01~0.32 mm;铟主要富集在铁闪锌矿中,其次为黄铜矿、磁黄铁矿、黄铁矿,其它矿物中有微量分布,在矿石中平均含量大体上伴随锌的含量升降。
3. 选矿工艺及主要设备
选矿厂设计规模为8000 t/d,年处理矿石量256万t,选矿厂全年工作320天,每天工作3班。年产锌精矿含锌7.3万吨、铜精矿含铜2000吨、锡精矿含锡12万吨、硫精矿11万吨、回水复用率90%以上。选矿工艺采用浮选–磁选–重选联合流程;浮选选铜、锌和硫,磁选选铁,浮重磁联合选锡。选矿工艺流程示意图见图1。
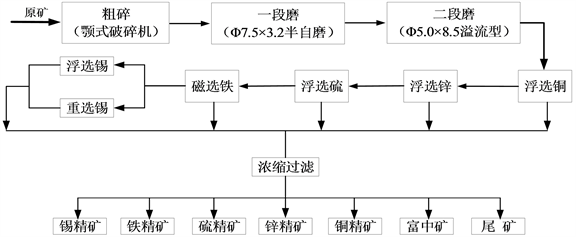
Figure 1. Schematic diagram of mineral processing process
图1. 选矿工艺流程示意图
设计碎磨流程为半自磨 + 球磨 + 顽石破碎流程,半自磨系统采用一台Φ7.5 × 3.2 m的半自磨机,装机功率为2600 kW,其排矿端带有圆筒筛,筛上产品采用NO.2带式输送机运至顽石破碎厂房,顽石破碎采用一台Φ1.0 m × 0.3 m的高压辊磨机,高压辊磨机排矿采用NO.3带式输送机返回至半自磨机给矿NO.1带式输送机,球磨回路采用一台Φ5.03 × 8.5 m溢流型球磨机与两组Φ500-9 (其中一组备用)水力旋流器组构成闭路磨矿,球磨机装机功率3500 kW,磨矿产品细度为−0.074 mm占75%~80%。
选矿工艺采用浮选–磁选–重选联合流程,设计浮选选铜回路粗选段采用一次粗选、两次扫选的流程结构,共采用7槽70 m3充气机械搅拌式浮选机,按照3-2-2进行阶梯布置,铜粗精矿经过一次混精选后进行再磨(有闭路分级),混精选采用2槽30 m3充气机械搅拌式浮选机,再磨选用一台Φ1800 mm、装机功率250 kW的立式螺旋搅拌磨机。粗精矿经再磨后进行一次浮选机精选和两段浮选柱精选,一次精选采用4槽16 m3充气机械搅拌式浮选机,二次精选采用一台Φ3.0 m × 10 m浮选柱,三次精选采用一台Φ2.2 m × 10 m浮选柱,产出最终铜精矿并自流至铜精矿浓缩机。选铜尾矿进入浮选选锌回路,设计浮选选锌粗选段采用一次粗选、三次扫选的流程结构,共采用13槽70 m3充气机械搅拌式浮选机,按照4-3-3-3进行阶梯布置,锌粗选精矿先经过一次浮选机混精选,混精选设计采用4槽30 m3充气机械搅拌式浮选机,其精矿进行再磨(有闭路分级),设计选用3台(2台工作,一台备用) Φ1800 mm、装机功率250 kW的立式螺旋搅拌磨机。粗精矿经再磨后再进行三段浮选柱精选,三段浮选机精扫选,一段精选采用2台Φ4.3 m × 8.5 m浮选柱,二段精选采用2台Φ3.66 m × 8.5 m浮选柱,三段精选采用1台Φ4.3 m × 8.5 m浮选柱,产出最终锌精矿并自流至锌精矿浓缩机,精扫选共选用10台16 m3充气机械搅拌式浮选机,按照4-3-3水平布置。精扫选尾矿采用1台CTB-718永磁磁选机磁选,磁选精矿即为铁精矿自流至铁精矿浓缩机,磁选尾矿自流至尾矿浓缩机。选锌后的尾矿采用永磁磁选机进行一次粗选和一次精选选铁,粗选采用4台CTB-1230永磁磁选机,精选采用1台CTB-718永磁磁选机,磁选精矿即为铁精矿自流至铁精矿浓缩机,磁选尾矿进入旋流器分级作业。旋流器分级采用1组Φ250-24旋流器组,旋流器沉砂(+0.037 mm)先采用浮选工艺选硫,设计浮选选硫采用一次粗选、两次扫选、两次精选的流程结构,粗扫选采用7槽30 m3充气机械搅拌式浮选机,按照3-2-2进行水平布置,精选一采用3台16 m3机械搅拌式浮选机,精选二采用2台16 m3机械搅拌式浮选机,浮选精矿即为硫精矿并自流至硫精矿浓缩机。选硫尾矿采用2台CTB-1230永磁磁选机磁选,磁选精矿即为铁精矿并自流至铁精矿浓缩机,磁选尾矿进入粗粒锡石重选作业。锡石重选先采用螺旋溜槽进行粗选,采用86台Φ900 mm (四头)螺旋溜槽,螺旋溜槽粗选得到三个产物依次为精矿、中矿和尾矿。螺旋溜槽尾矿采用1组Φ250-10旋流器分级,旋流器溢流进入−37 μm旋流器脱泥二作业,旋流器沉砂进入尾矿摇床作业。螺旋溜槽中矿进入摇床重选作业,共采用136台摇床。锡石浮选回路粗选段采用一粗三扫的流程结构,粗扫选采用11槽16 m3充气机械搅拌式浮选机,按照4-3-2-2进行水平布置,精选一采用4槽16 m3充气机械搅拌式浮选机,精选二采用3槽16 m3充气机械搅拌式浮选机,精选三采用2槽16 m3充气机械搅拌式浮选机,精选三精矿由于锡石品位较低,故采用两段细泥摇床进行重选,一段为8台细泥摇床,二段为4台细泥摇床,重选精矿即为细粒锡石精矿自流至锡石精矿浓缩机,重选尾矿为细粒锡石富中矿,锡石浮选扫选尾矿自流至尾矿浓缩机。
4. 选矿厂设计分析
4.1. 选厂总图布置
从选厂总图布置方面来看,各厂房标高为:磨矿车间1391.70 m;浮选车间1384.70 m;重选车间1376.70 m和1370.70 m;精矿浓缩机1354.90 m;精矿过滤厂房1340.00 m。厂房间的相互高差为7~16 m,最大限度地实现矿浆及尾矿自流输送。厂房成南北纵向布置,有效利用东西风向,减少厂房间的相互干扰,改善了环境。另外,原始地形为坡地,南北纵向设计,有效利用了地形高差,合理划分了厂房台段,从高台段向低台段依次布置工艺流程,同时采用楼层设计摆放占地面积较大的714张摇床,且规模大的选矿厂难以找到适于单层阶梯式布置的坡地。因此,受地形、投资成本等的限制,摇床选锡车间采用多层式布置,缩短了矿浆运输距离,使总平面布置更紧凑,节约土地,降低投资。其中分台段布置的方式,大量减少了场地的土石方工程量,降低了工程造价 [4]。总体来说,合理的台段标高,紧凑的平面布置,这是坡地建厂竖向设计的成功之处。
4.2. 厂房内部空间布置
从厂房内部空间布置来看,功能分区明确,利于生产管理。浮选车间利用钢结构制造地势高差,使错综复杂的设备看着非常整齐,层次感鲜明。在大型设备的上部利用钢网铺设操作平台,有效利用了上层空间,节约了用地面积,也使整个车间宽敞明亮,具有更好的通风效果,但这样的设计对于设备维修还是具有一定的局限性,尤其是大型的零件更换。另外,厂房内部的工艺矿浆输送管道、药剂管道、压缩空气管道及用电线路的布置井然有序,厂房内部和各厂房间的楼梯设置也非常顺畅。
4.3. 设备配置情况
从设备配置方面来讲,选厂设备具有大型化、高效化、统一性等优点。设计采用立式搅拌磨和浮选柱等国外的先进高效设备,同时配备了自动取样筛分及品位分析设备以及自动化控制系统,在这些有利因素的协同作用下,不仅提高了生产指标,而且操作方便,减少了人员投资,生产及设备故障问题也可以得到及时解决。第一,设备大型化:φ7.5 × 3.2半自磨机、φ5.03 × 8.5溢流型球磨机、KYF-70 m3充气机械搅拌浮选机等大型化设备的应用,一方面可以减少设备台数,使配置更为紧凑,从而节省了厂房面积,降低了基建投资;另一方面由于设备台数的减少,使得动力消耗降低以及相应的运输设备及辅助设施减少,同时,也利于仪表化及自动化控制的实现 [5]。第二,设备型号统一:浮选铜粗扫选作业与选锌粗扫选作业、铜混精作业与锌混精作业、铜精选一作业与锌精扫选作业及−0.037 mm硫粗扫选作业在设备配置上具有统一性。同类设备,在满足工艺要求的前提下,型号的统一,使得设备维护方便、减少备件量,同时也有利于矿山进行设备管理。第三,先进技术及新设备的应用:半自磨–球磨工艺的应用及立式螺旋搅拌磨机、浮选柱等新型设备在新田选矿厂得到了较好地应用。新工艺,新设备因其具有高效、节能、减少流程段数、占地面积少、基建投资低等优势,有效提高了选厂的现代化水平,同时这也是选厂设计的发展方向 [6]。
5. 选厂生产情况分析
5.1. 生产过程与工艺对指标的影响
从试生产过程及指标来看,第一,生产综合回收了铜、锌、铁、硫、锡,且铜、锌、铁、硫四个产品均达到合格产品要求,锡精矿未能达到合格品位,但也得到了较好地回收;第二,锌精矿里含铟达500 g/t,这为后续冶炼加工提供较好的原料。这说明整个生产工艺流程是比较合理的,尤其是−0.037 mm采用三组水力旋流器脱泥、重选溢流浓密机的设置以及大部分重选作业尾矿返回再选等,体现了对资源的充分回收。但对锡矿选别流程还需进行必要的流程考察,对其进行合理改进,尽量提高锡精矿的指标。
生产过程中影响锡矿物回收的原因主要是,第一,选厂在整个选别流程中采用了三段磨矿,而细粒级锡矿物的回收难度较大;第二,摇床车间各个分泥斗的矿浆进料不均;第三,分级箱未能较好地分级和均匀给矿;第四,细粒级锡石浮选工艺,粗粒级锡精矿脱硫工艺设计缺少合理依据。
生产采用重–浮联合流程选别锡石,浮选的效果决定了锡精矿的指标。对细粒级锡矿,采用先脱硫–锡石浮选–摇床精选的工艺流程,虽然采用了三段水力旋流器脱泥,但浮选指标仍较差。可能需要更深入的试验研究,选择更好的矿泥分散剂和捕收剂来提高精矿品位。对于粗粒级锡矿,设计采用重选–脱硫的工艺流程,最终也不能获得合格产品。设计采用小型立式搅拌磨对粗精矿进行再磨,但因为该段作业不连续,立式搅拌磨重启时总出现故障而停用,使锡矿未能较好的单体解离,脱硫作业并不太顺畅。因此,粗粒级锡矿的选别工艺及设备还有待进一步验证,为接下来的技术改造提供更充分的依据。推荐工艺流程图及工艺指标分别见图2,表2。根据矿石的工艺矿物学性质,研究认为采用铜与易浮脉石一起浮选再分离的工艺,能较好地解决了滑石对浮选工艺的影响,同时对锌浮选尾矿中−0.038 mm级别进行了细粒锡石浮选的研究,使细粒级别的锡得到了有效回收。
5.2. 矿浆分级对生产指标的影响
就分级设备而言,水力旋流器具有分级效率高,占地面积小等优点,是按矿物的比重来进行分级的设备。结合矿石性质,原矿摇床次精矿和中矿进行分级后再磨,由于锡矿石比重较大,导致部分已单体解离的、合格粒级的锡矿物进入沉砂,进行再磨后产生过磨现象。因此,该选厂现场可对该段水力旋流器的产品进行更进一步的粒度分析以及沉砂单体解离度分析。水力旋流器操作时可适当减小沉砂口直径,减小水力旋流器的给矿压力,增加给矿浓度,调整水力旋流器的结构参数,使较重的合格粒级锡矿物通过溢流进入下一段作业,以减少锡矿物的过磨。在后续生产中可考虑选用高频振筛进行对比试验,分析是否具有更好地分级效果。
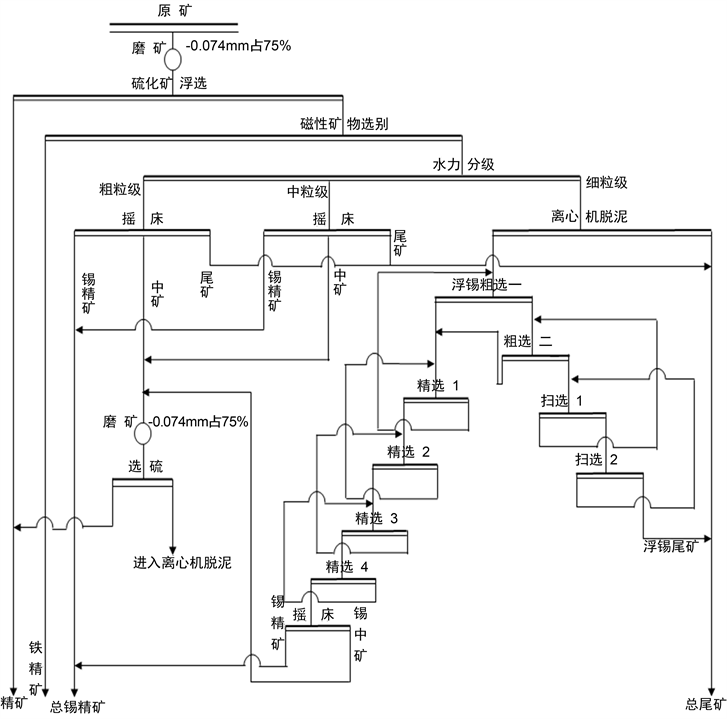
Figure 2. Recommended process flow chart
图2. 推荐的工艺流程图
5.3. 矿浆流量稳定性对指标的影响
从矿浆稳定性来讲,矿浆的波动不但对摇床选别影响严重,而且不利于现场工人的操作控制。合理、稳定的给矿量能提高分级箱的分级效率,而较好的分级效果是摇床选别成功的关键。从锡石摇床选别车间的设备配置来看,摇床的配置由粗到细,摇床的给矿由分级箱分级后依次给入各台摇床,分级箱与分泥斗联合使用,分泥斗起到稳定矿浆的作用,使分级箱较好地分级,从而提高摇床的选别效率。笔者认为,设备配置合理,但还存在可改进的地方。观察矿浆管道布置可发现,重选车间矿浆分配器的矿浆由管道运至分泥斗,管道的走向、距离及坡度不同,这就导致矿浆流量不均匀,使分泥斗内的矿浆量也不尽相同。给矿管道短且坡度大的分泥斗进料量太大,矿浆还未有效浓缩就由溢流堰流出,造成细粒级的损失。给矿管道长且坡度小的分泥斗进料不够,分泥斗并未起到浓缩作用,而且分泥斗液面较低,压力不够,给入分级箱的矿浆量也减少。
通过分析知道,分泥斗矿浆给料不均导致后续作业不稳定,致使锡石选别受到了影响。特别是微细泥摇床,当分泥斗内矿浆压力小时,分级箱的给矿量也随之减小,矿浆厚度较薄,大部分细粒级矿物进入粗粒级摇床选别,不能得到较好的回收,微细泥摇床也未能得到有效利用。这可能是微细粒锡矿物无法回收的原因之一。因此,现场可根据输送距离,调整矿浆管道坡度,从而调整矿浆流量。尽量使分泥斗充满,发挥浓缩矿浆作用,同时可保证分级箱给料压力稳定,才能起到稳定给矿的作用。这样也能提高分级箱的分级效率,进而使摇床效率提高,尤其是细粒级摇床。
6. 结论
1) 该选厂总图布置合理,厂房内部设计整齐、通畅、设备先进,现代化程度较高,有效节省了劳动力和管理成本。
2) 浮–重联合工艺流程,综合回收了铜、锌、铁、硫、锡多种金属,但部分细粒级锡精矿难以回收,为了更好地回收锡矿物,可以对选锡流程进一步优化。
基金项目
国家自然科学基金青年基金资助(No. 51704104);中国博士后科学基金资助(No. 2018M633637XB);省部共建复杂有色金属资源清洁利用国家重点实验开放基金项目(No. CNMRCUKF1904)。
NOTES
*通讯作者。