1. 引言
随着我国交通量的增加及车辆超载现象的出现,许多混凝土桥梁出现了疲劳裂纹,对结构造成一定的安全隐患,亟待维修加固 [1]。碳纤维增强复合材料(CFRP)凭借其轻质高强、耐腐蚀、抗疲劳及施工方便等优势在混凝土结构加固领域中备受关注 [2] [3]。在CFRP外贴加固混凝土结构技术中,CFRP-混凝土界面是加固结构应力传递的关键部位,且界面剥离破坏是加固结构的主要破坏模式 [4] [5]。为了保障加固结构能正常安全的服役,有必要对CFRP-混凝土界面进行损伤识别 [6]。
压电陶瓷材料具有集传感和驱动一体化、频响范围宽、响应快、线性关系好等优点,能够有效测量结构的阻抗。压电阻抗法的测量原理为:对压电陶瓷传感器进行正弦交流电压的激励,由于压电陶瓷的逆压电效应,结构主体和压电陶瓷会一起振动。而同时结构本身的振动对压电陶瓷进行干扰并产生反作用力,压电陶瓷在外力作用下会产生电极化而输出电流,被阻抗分析仪采集。当结构出现损伤时,其刚度和阻尼会产生变化,结构的机械阻抗会发生变化。因此,能利用压电陶瓷测出结构损伤前后的阻抗值并进行对比能有效识别结构的损伤 [7] [8] [9]。已有学者对混凝土框架结构 [10]、钢框架 [11] [12]、钢管混凝土柱 [13] [14] 以及带有模拟损伤的碳纤维加固混凝土梁 [15] 进行了损伤识别研究,均证明了阻抗法能够有效识别界面损伤。
目前,应用压电阻抗技术对荷载作用下的CFRP加固混凝土结构的界面损伤监测研究较少 [16]。在此背景下,本文对疲劳荷载作用下CFRP加固混凝土梁的黏接界面剥离过程进行了监测,通过阻抗曲线和RMSD值对加固梁的界面剥离过程进行了定性和定量分析,并对比应变分析结果,进一步验证了该技术的有效性。
2. 试验概况
2.1. 试验梁设计及制作
本文设计了1根CFRP板粘贴加固的混凝土梁来监测疲劳荷载作用下的界面损伤过程。试验梁的尺寸均为100 × 200 × 1500 mm,采用C30预制商品混凝土浇筑,主筋直径为12 mm的螺纹钢,型号为HRB400,箍筋直径为6 mm,箍筋间距为120 mm,上部构造钢筋直径为8 mm,如图1所示。CFRP板采用Lica碳纤维板,尺寸为1000 × 50 × 1.4 mm。粘结剂采用Lica环氧树脂胶。
参照相应的材料力学性能试验方法,对标准混凝土圆柱体进行轴心压缩实验,测得圆柱体抗压强度为34.82 MPa,弹性模量为33.98 Gpa。对主筋、CFRP板和粘结剂三种材料进行了拉伸试验,测得钢筋的屈服强度为450 MPa,抗拉强度为610 MPa,弹性模量为206 GPa;CFRP的抗拉强度为2560 MPa,弹性模量为173 GPa;粘结剂的抗拉强度为55.8 MPa,弹性模量为3.13 GPa。
在混凝土梁浇筑完成并养护28天后,将混凝土梁底面进行打磨至刚刚露出粗骨料,随后用无水乙醇将CFRP板表面及混凝土打磨区域清洗干净,再按胶粘剂厂家提供的配合比将各组分充分搅拌均匀并涂抹于打磨区域,最后将CFRP粘贴于混凝土梁底面。为保证界面胶层厚度统一为2 mm,胶粘剂在搅拌时掺合直径为2 mm的玻璃珠(重量占胶粘剂重量的2%)。在正式试验之前,将制作好的加固试验梁在室温条件下加压养护7天。
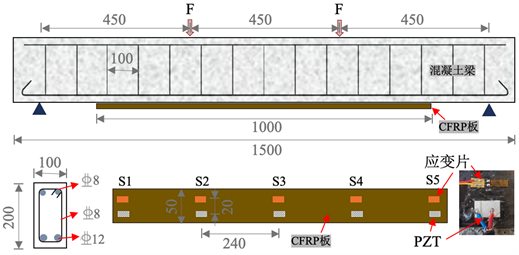
Figure 1. Specimen dimensions and measuring points layout (Unit: mm)
图1. 试件设计尺寸及测点布置(单位:mm)
2.2. PZT传感器制作及粘贴
为了方便在结构表面粘贴PZT进行损伤监测,试验选用了工程结构检测中一种常见的翻边式的锆钛酸铅压电陶瓷片(Pb(ZrTi)O3,即PZT)作为传感器,其振动模式为沿厚度方向的伸缩振动,规格为15 × 10 × 0.3 mm。
PZT传感器在制作过程中,先用酒精将PZT的表面擦拭干净,接着采用两芯屏蔽线分别焊接翻边式PZT同一表面的正负极。然后用Araldite AB胶将CFRP板和PZT传感器进行粘贴,待胶水干燥后在PZT表面再涂一层Araldite AB胶水,对PZT进行静电绝缘和物理保护,粘贴好的PZT传感器见图1。
2.3. 疲劳加载方案及测量方案
前期试验测得同批CFRP加固混凝土梁的极限承载能力Pu = 95 kN。为了加速疲劳荷载对界面的不利影响,且保证疲劳加载过程中试件的稳定,本文的疲劳荷载范围选为0.1~0.7 Pu,即9.5 kN~66.5 kN。疲劳试验为四点弯曲加载,采用SDS500型电液伺服动静万能试验机进行,疲劳加载频率为0.1 Hz,次数为320次。
为了得到不同疲劳次数下加固梁的阻抗值,采用LCR高精密测试仪(IM3536)对不同疲劳次数下PZT的界面阻抗进行采集。参考相关研究 [17],选用激励信号的频率范围为100 kHz~250 kHz,步长为1 kHz。
在正式疲劳加载前,先对试验梁进行一次阻抗采集,并视为健康状况下的阻抗值。随后开始正式疲劳加载,以80次疲劳加载为一个周期,并对第1次和320次疲劳上下限,第80次、第160次和第240次疲劳上限荷载作用下的阻抗值和CFRP板应变进行采集,同时对混凝土梁的裂纹扩展及界面剥离情况进行观察记录。PZT和应变片的布置如图1所示。
3. 试验结果及分析
3.1. 试验现象
试验梁在经受320次疲劳损伤后的裂缝开展如图2所示,其中试验梁上绘制的字母A、B、C分别表示在第1次、第80次和第160次达到疲劳上限值时的裂纹扩展情况。试验过程中发现,当荷载第一次加载到32 kN时,混凝土梁跨中出现了第一条裂缝。当荷载继续增加至疲劳上限66.5 kN时,混凝土梁底部出现大量裂缝,同时观察到混凝土裂缝处的黏接界面也产生了裂纹,但CFRP板仍与混凝土梁接触紧密。纯弯段内混凝土裂缝基本往竖向发展,剪弯段内混凝土裂缝逐渐往加载点方向发展,最长的混凝土斜裂缝出现在CFRP板两端附近。
在达到第80次疲劳过程中,发现S1测点处(CFRP端部)出现了裂纹,并延伸到混凝土梁形成了较长的横向新裂缝;S5侧点处的混凝土梁同样出现了一条新斜裂缝;S4测点处的混凝土裂缝长度出现了少量增长,但其他大部分的裂缝长度基本维持不变。在达到第160次疲劳过程中,试验梁S5位置处的斜裂缝出现较大扩张,并有较长的延伸。而在后续80次的疲劳过程中,试验梁再未发现新的裂纹扩展情况。
S1和S5测点处界面在经受了320次疲劳后的损伤情况如图3所示,可以发现,试验梁S1测点处的界面出现了裂纹,且开裂后CFRP板上带有一层较薄的混凝土,而S5测点附近混凝土裂缝开口增大,但CFRP板仍与混凝土梁粘结完好。
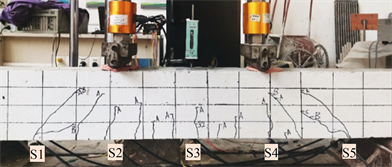
Figure 2. Failure mode after fatigue damage
图2. 疲劳损伤后试验梁形态
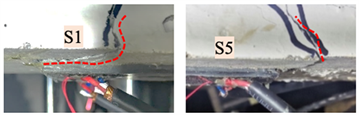
Figure 3. Failure mode after fatigue damage
图3. 疲劳损伤后试验梁形态
3.2. 界面疲劳损伤定性分析
定性分析是以阻抗图形分析为基础,通过对比健康状况下和损伤状态下的阻抗曲线变化趋势,两者的偏差情况可初步判断结构是否发生损伤。图4展示了不同测点的阻抗曲线。
从图4中可以看出,阻抗曲线总的趋势表现为阻抗值随频率增加而降低。当荷载第一次达到下限时,由于混凝土没有开裂各测点的阻抗曲线基本没有变化。当荷载第一次达到疲劳上限值时,测点S3的阻抗曲线发生了明显向下的整体偏移,而测点S2和S4的偏移相对较小。主要的原因为跨中位置的结构的变形最大,结构的刚度和阻尼变化最为明显,从而导致试验梁局部的振动响应发生了变化。尽管在第一次疲劳加载中S1和S5测点附近出现了斜裂纹,但测点界面并未发现有明显损伤,因此其阻抗曲线和健康状况下的几乎重合。
随着疲劳循环次数的增加,端部测点S1和S5的阻抗曲线的形状发生变化。这是由于CFRP端部测点处在疲劳循环过程中发生了界面的剥离导致该测点附近结构的固有频率,刚度和阻尼发生较大的改变,从而引起结构的机械阻抗改变,在图7中表现为经过320次疲劳损伤后,阻抗曲线在频率范围130 kHz~250 kHz间出现了小的弯折突变和偏移。而这种现象在端部测点S5中最为明显,该测点的阻抗曲线产生了明显的新波峰波谷,说明疲劳损伤后加固梁右侧端部测点的剥离损伤更为严重。
而对于测点S2、S3和S4,从第1次到第320次疲劳损伤,测点的阻抗曲线没有出现明显的新波峰和波谷而曲线仅有小的偏移和弯折出现。值得注意的是对于测点S3,到达第320次疲劳循环的下限(9.5 kN)时,测点的阻抗曲线回复到与健康状态下的阻抗曲线相似,这说明了疲劳损伤对加固梁跨中测点的界面残余损伤较小,跨中位置没有发生界面的剥离。从各测点的阻抗曲线图可以看出,试验梁在循环荷载作用下各测点位置先后产生了不同程度的损伤,但阻抗曲线的表现形式不一样。试验梁跨中虽然出现了界面裂纹,但CFRP板仍与混凝土梁紧密接触,结构在PZT厚度方向的振动模式影响不大,则阻抗曲线表现为整体偏移不会出现新波峰波谷。而CFRP板端部的界面损伤会导致CFRP板与混凝土主梁连接减弱,结构振动受的较大影响,从而阻抗曲线会形成新的波峰波谷并出现局部偏移。
从以上分析可以发现不同测点的阻抗曲线图能够直观地判断是否出现界面损伤,但无法对不同程度的损伤做出进一步量化。
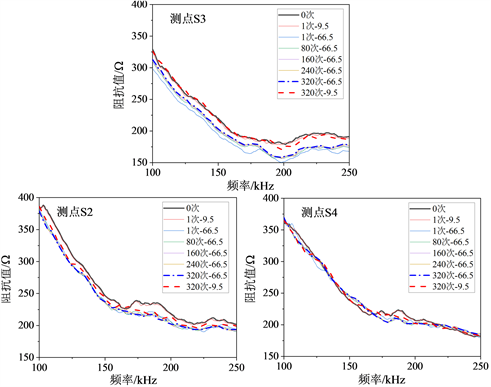
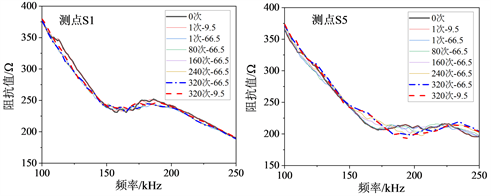
Figure 4. Impedance curve at different measure points during fatigue
图4. 疲劳过程中不同测点阻抗曲线图
3.3. 界面疲劳损伤定量分析
为更精准的运用压电阻抗法检测结构损伤,需引入量化的损伤指标来定义结构损伤程度。工程上常用的主要损伤量化指标有三种,分别为均方根差值(RMSD值)、百分比绝对平均值(MAPD值)和相关系数值(CCD值)。根据前期研究结果 [11],发现RMSD值作为损伤指标对于CFRP加固混凝土梁黏接界面的剥离较为敏感。RMSD值是将健康状态下和损伤状态下不同频率点的阻抗值做对比,能有效地反映损伤前后阻抗数据的偏移程度,从而量化损伤程度。当RMSD值越大,表明结构的损伤程度越高。RMSD值的计算如式(1)所示:
(1)
式中,i表示扫描频率段内的第i个点,N表示扫描频率范围内取点的总数,
表示第i个频率点健康状态下的基准阻抗值,
表示进行损伤检测时第i个频率点的阻抗值。
不同疲劳次数下的各测点的RMSD值分布如图5所示。
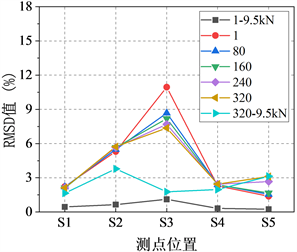
Figure 5. RMSD value of CFRP monitoring points
图5. CFRP板监测点RMSD值分布
从图5可以看出,疲劳损伤过程中各测点RMSD值的分布的总体趋势为跨中位置最大,然后向CFRP两侧端部递减。当第一次达到加载上限时,跨中S3测点的RMSD值达到了10.95%,S2测点次之为5.30%,而S1、S4、S5测点的RMSD值均在3%以下。这是由于第一次加载后跨中出现大量的竖直裂缝且该位置的变形最大,因此测点S3处结构的机械阻抗变化最大。另外,CFRP跨中和板端测点随着疲劳循环次数的增加的RMSD值变化如图6所示。CFRP板端左侧测点S1的RMSD值从第1次加载上限时明显增加(从0.44%增加至2.23%),之后随着疲劳循环次数的增加RMSD值基本保持稳定。对于板端右侧测点S5,到第一次加载上限时,RMSD值从0.24%增加至1.38%,之后随着疲劳次数的增加而逐渐增加,320次循环后RMSD值到达3.13%。相较于S5测点疲劳损伤后RMSD值的大幅增加,S1测点的增加幅度较小,主要的原因是右侧板端在疲劳过程中的界面开裂情况更为明显,则与图2中加固梁的裂缝开展情况一致。跨中处界面经疲劳荷载反复作用后使得胶层发生塑性变形,导致界面裂纹对局部振动的影响减弱,因此S3测点的RMSD值表现出少量下降的趋势。
另外,从图6可以发现,经过320次疲劳损伤荷载卸载到疲劳的下限后,跨中测点S3的RMSD值下降至1.97%,而板端测点S1和S5基本没有变化,这说明了疲劳损伤能对CFRP板端造成不可逆的剥离损伤。而对于加固梁跨中,卸载后加固梁的挠度基本恢复,同时由于粘结界面没有发生剥离,变形和裂缝开展造成的跨中界面损伤可以恢复。
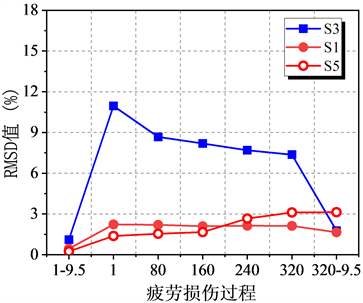
Figure 6. RMSD value of CFRP mid-span and plate-end
图6. CFRP板跨中和板端监测点RMSD值发展
对于CFRP加固钢结构,界面裂纹的产生会导致CFRP板的应变发生改变,不同疲劳次数下的应变变化在一定程度上能反映出界面损伤 [18]。为了对比应变监测和PZT监测对界面损伤判别的有效性,将不同疲劳次数下各测点的应变变化情况记录如图7所示。从图中可以看出,在第一次达到疲劳上限值时,CFRP跨中应变明显增加,而CFRP端部由于变形较小,其应变只有100 μɛ左右。经过80次的疲劳损伤后,CFRP端部处界面发生损伤以及斜向裂缝的开展,应变传递效率减弱,CFRP端部的应变减少。测点S1和S5的应变分别下降至59.7和58.8 μɛ,而同时测点S5的应变下降更为明显这与前面的损伤发展过程一致。CFRP跨中由于界面损伤不明显,其应变基本不变。而当疲劳次数从80次达到320次的过程中,各测点应变基本稳定,当荷载卸载到疲劳下限时,CFRP板端的应变与第一次加载下限时的应变基本相同,说明应变监测不能反映出疲劳损伤对CFRP端部剥离的不可逆性。
通过分析各测点在不同疲劳次数的应变变化可基本判断是否有界面损伤产生,且一定程度上能反应局部范围内的损伤大小。然而,对比图6和图7,可以发现RMSD值能更加直观清晰的反映出加固梁粘结界面累积损伤的过程。而且与应变监测相比,基于PZT的界面损伤监测灵敏度要更高并能很好的反映出疲劳损伤对CFRP端部的不可逆损伤。
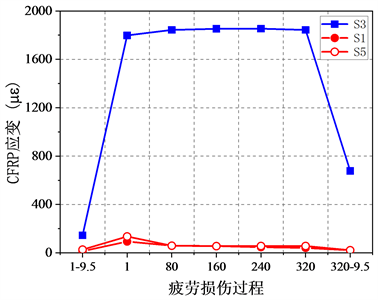
Figure 7. Relationship between fatigue times and CFRP strain
图7. 疲劳次数-CFRP应变关系图
4. 结论
1) 跨中界面损伤会导致阻抗曲线出现整体偏移,而端部界面损伤会导致阻抗曲线出现新的波峰波谷,据此可以定性地判断出疲劳荷载作用下界面是否存在损伤。
2) 基于压电阻抗法的损伤监测技术能直观清晰地反映出粘结界面在疲劳荷载下的损伤累积过程,并具有很高的灵敏度。CFRP端部测点的RMSD值随着疲劳循环次数的增加而增加。S1和S5测点RMSD值在界面的裂纹产生后分别增加了407%和475%。
3) 通过应变分析和压电阻抗分析均可监测加固梁界面疲劳损伤的状况,但压电阻抗法能反映出疲劳循环对CFRP端部的不可逆损伤。说明采用压电阻抗法监测CFRP-混凝土界面疲劳损伤过程更为真实、有效。
NOTES
*通讯作者。