1. 引言
轴承是机械设备的基础零件。21世纪以来,现代工业技术不断进步,各行各业对轴承的要求越来越苛刻 [1] - [6]。轴承泛应用于矿山机械、精密机床、冶金设备与重型装备等重大装备领域和风力发电、高铁动车及航空航天等新兴产业领域 [7] [8] [9]。轴承主要有内外套圈、滚动体(包括滚珠、滚柱和滚针),都是由轴承钢制造。轴承的工作环境较为恶劣,主要受到拉力、压力、剪力和摩擦力等各种交变应力,因此轴承钢必须具有较高且均匀的硬度,较好的耐磨性及高的弹性模量,抗腐蚀性能和良好的加工性。轴承钢的使用环境及其对钢质量的要求如表1所示 [10] [11] [12]。所以,目前急需发展高洁净度轴承钢的冶炼工艺理论与控制技术,提升我国高品质轴承钢的生产制造水平。
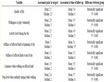
Table 1. Requirements for bearing steel in different environments [10] [11] [12]
表1. 不同环境对轴承钢的要求 [10] [11] [12]
2. 轴承钢分类
常见的轴承钢有高碳铬轴承钢、渗碳轴承钢、高温轴承钢、不锈轴承钢以及特种轴承钢等 [13]。
1) 高碳铬轴承钢适用于内外套圈和滚动体,回火硬度为HRC61~64。常用牌号与GCrl5、GCr5SiMn、GCr4、GCrl5SiMo、GCrl8Mo 等。其中GCrl5使用最为广泛,其C和Cr的含量分别为1.0%和1.5%,具有良好的淬透性、高接触疲劳强度和高耐磨性。要求钢中P、S含量不大于0.025%,并限制Ni、Cu等残余元素含量﹐钢中氧含量控制在12∙10−6之内。
2) 高温轴承钢在航空航天领域应用较多,工作环境温度较高,常常在200℃以上,并具有较高的高温硬度(大于50HRC)主要分为高温高速工具轴承钢、高温渗碳轴承钢以及高温不锈轴承钢三类 [14]。国内使用的高温轴承钢中有Crl4Mo4、W9Cr4V2Mo、Cr4Mo4Ni4V、W18Cr4V、W12Cr4V5Co5等牌号,其中Cr4Mo4V 和Cr4Mo4Ni4V牌号使用最为广泛 [15]。
3) 渗碳轴承钢是轴承钢进行了表面渗碳处理,表面硬度和耐磨性会提高,但心部仍具有良好的韧性,能够承受较高的冲击载荷,主要适用于制造在高冲击负荷下运行的大中型轴承零件,属于低碳合金结构钢。国内使用的渗碳轴承钢主要有G20CrMo、G20CrNiMo、G20CrNi2Mo、G20Cr2Ni4、G10CrNi3Mo、G20Cr2Mn2Mo。
4) 不锈轴承钢适用于有不锈和抗大气腐蚀的轴承以及精密微型轴承。常用的不锈钢轴承钢有G102Cr18Mo、G95Cr18等,为高碳高铬马氏体型钢。
5) 特殊轴承材料适用于有防磁和抗特殊介质腐蚀的轴承,如G52合金、G60合金以及自润滑石墨钢等。
3. 影响轴承钢洁净度因素
影响轴承钢冶金质量的因素有很多,例如化学成分、非金属夹杂物、微观组织等。非金属夹杂物的存在是导致轴承失效的主要原因。钢中化学成分影响夹杂物的种类,夹杂物的存在影响组织均匀性,最终都会影响轴承的使用寿命。因此,轴承钢必须严格控制轴承钢中的非金属夹杂物的含量、种类和尺寸指标,化学成分,碳化物粒度和分布等 [16] [17]。
3.1. 非金属夹杂物
夹杂物为钢中不可避免的缺陷,会在多方面对钢质量产生影响。图1为一些典型大型夹杂物形貌图 [18]。
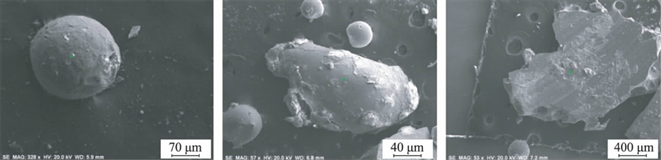
Figure 1. Topography of large inclusions [18]
图1. 大型夹杂物形貌图 [18]
轴承钢中主要夹杂物包括两类:氧化物夹杂物与析出物夹杂,其中氧化物夹杂通常生成于钢液中,包括尖晶石、钙铝酸盐和硅酸盐等;析出物夹杂通常生成于凝固过程中,包括氮化钛和硫化锰等。在国际上一般将夹杂物分五类,分别为:A类夹杂、B类夹杂、C类夹杂、D类夹杂和Ds类夹杂。其中,A类夹杂主要是硫化物(FeS、MnS、CaS),B类夹杂主要是氧化铝类氧化物(Al2O3),C类夹杂是硅酸盐类夹杂物(SiO2, 2FeO-SiO2, CaO-SiO2),D类夹杂是球状氧化物(Al2O3-CaO),Ds类为单颗粒球类夹杂。在轴承钢中常见的夹杂物除了上述五类之外,还存在含钛的碳、氮化物等夹杂物。
夹杂物对轴承钢质量的危害,主要是影响其疲劳寿命和韧性。其影响因素主要从以下三个方面分析:
1) 钢中每类夹杂物的热膨胀系数各不相同,因此,在轴承工作发热到停止冷却过程中会产生不同于基体的张应力和压应力而导致破坏的出现 [19]。
2) 夹杂物大都是脆性的,会导致钢中应力集中并发展,因此会产生裂纹。即使存在单一的不破碎夹杂物,也可能导致机械性能的不均匀从而改变局部的应力分布,进一步影响钢的疲劳寿命 [20]。相同类型和尺寸的夹杂物,曲率半径较小的夹杂物会引起更严重的应力集中。
3) 非金属夹杂物与基体存在弱的结合界面。在钢的变形处理过程中沿塑性应变方向上,夹杂物存在的界面处会产生不变形张力,这将导致空洞的形成进而影响钢的质量和性能 [21]。
表2 [21] 统计了国内某厂轴承钢成品检测中各类夹杂物来源和比例。
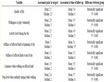
Table 2. Source and distribution of inclusions in bearing steel of a certain factory [22]
表2. 某厂轴承钢中夹杂物来源与分布 [22]
从表2可以看出氧化物夹杂仅占18.15%,其中脱氧夹杂占12%,变性夹杂占35%,卷渣夹杂占53%。变性和卷渣夹杂是大型氧化物夹杂的主要来源。超过一半的夹杂物都是硫化物,特别是CaS系夹杂。因为钛夹杂的含量也不低,在夹杂物总量中占到14.2%,说明钢中钛含量较高。
根据夹杂物对疲劳寿命的影响,如下图2所示,TiN和Ti(C,N)对钢的滚动接触疲劳影响最大,然后是氧化物(特别是球状的钙尖晶石和铝氧化物)和硫化物 [23] [24]。脆性氧化物夹杂比具有高变形系数的硫化物夹杂对疲劳失效更有害,硅酸盐夹杂物的危害介于脆性氧化物和硫化物之间。其中氧化物夹杂危害程度降低的顺序依次为铝酸钙、氧化铝和尖晶石,与这些夹杂物的平均热膨胀系数增加的顺序是对应的 [25] [26] [27] [28] [29]。
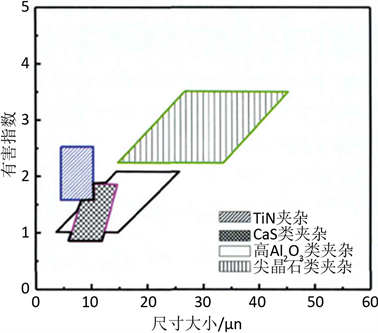
Figure 2. The influence of inclusions on fatigue life [23] [24]
图2. 夹杂物对疲劳寿命的影响 [23] [24]
国内外生产实践证实,各种炉外精炼方法(真空的或非真空的),加强对钢液的搅拌,都能将氧含量降到很低的程度,氧化物夹杂的数量,主要指Al2O3夹杂的数量大大减少。然而要降低A类夹杂物和D类夹杂物的数量则主要依赖于精炼渣的化学成分。
3.2. 微观组织
轴承钢组织的不均匀会降低其性能和寿命,而微观组织中尤其以碳化物的影响最大。碳化物的大小、形状、数量和分布都影响轴承钢的疲劳寿命。各种碳化物的形成原因、特点和危害如下表3 [30] [31] [32] [33] [34]。
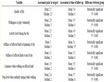
Table 3. Causes, characteristics and hazards of various carbides [30] [31] [32] [33] [34]
表3. 各种碳化物的形成原因、特点和危害 [30] [31] [32] [33] [34]
当碳化物颗粒细小且均匀的分布时,对钢的不利影响较小,轴承钢的各项指标均较好;当碳化物粗大且分散不均匀时,轴承钢的硬性、疲劳寿命等性能变差 [35]。因此,轴承钢通常要求碳化物颗粒细小,形状规则且分布均匀。碳化物不均匀性的根源在于凝固组织的均匀性,所以对凝固工艺的研究是控制碳化物不均匀性重点 [36] [37] [38]。衡量碳化物均匀性的指标是液析碳化物、带状碳化物、网状碳化物评级的级别。
常用于解决轴承钢中碳化物问题的方法如下:
1) 液析碳化物一般是通过高温扩散退火处理进行消除,但是时间不能过长。因此,在保证铸坯不会过烧的同时还需要对加热炉加热速率、保温温度、保温时间等进行系统的研究,从而对各参数进行精确的控制,最终实现液析碳化物的消除(减轻)和改善偏析的目的 [39] [40]。
2) 带状碳化物一般是从根源上消除或降低铸坯凝固过程中的枝晶偏析。在生产中,主要通过控制如降低浇铸温度,改直通水口为旋流水口、提高末端电磁搅拌结晶器的电流和浇铸速度 [41] 等工艺参数来减轻枝晶偏析状况。
3) 网状碳化物析出形成的主要阶段在轧制及轧后冷却和退火冷却处理过程。因此,可以通过对终轧温度和冷却速率两个工艺参数的优化来进行控制 [39]。
3.3. 化学成分
钢中的化学成分直接影响到钢的物性、组织和性能。其中影响最大的元素有O、S、N、Ti、H这几种元素,必须严格控制其含量水平以提升钢的性能。
氧含量的控制是提高轴承钢冶金质量关键因素,氧含量与钢中氧化物成正比,而氧化物夹杂易使钢在压延过程中产生裂纹并使钢材产生各向异性破坏钢基体连续性。采用顶底复吹转炉(BOF)→精炼→真空脱气等工艺流程生产GCr15轴承钢,出钢过程中加钢芯铝进行深脱氧,在精炼工艺中造高碱度精炼渣,进行真空脱气等技术手段使铸坯中全氧含量T.[O]为0.0012% [42]。
氢含量对轴承钢的性能有着极其重要的影响,随着钢中氢含量的增加,轴承钢的强度,特别是塑性和韧性显著下降,使钢逐渐变脆。氢还是轴承钢内部的小裂纹产生的直接原因。针对GCr15轴承钢氢含量较高的情况,某钢厂通过对潮湿的物料进行烘烤及精炼过程严格控制软吹过程氩气量,制定合理的RH真空保持时间、极限真空度范围等工艺处理钢液温度,真空处理后中包内钢液的平均[H]为由原来的1.69 ppm降低到1.34 ppm,同比下降了20.71%,效果显著 [43]。
硫是有害元素,不仅引起钢的热脆,还会增加表面裂纹、硫化物应力腐蚀裂纹,造成韧性下降,轴向性能恶化 [16] [44]。硫含量增加,轴承钢中硫化物和碳化物分布的平均尺寸增加 [45]。文献称 [46],含硫量低于0.040%时,随含硫量提高接触疲劳寿命提高;含硫量高于0.040%时,会使寿命降低。
氮、钛和一定量的碳,易形成TiC和Ti(C,N)而易引起疲劳裂纹。鞍钢通过优化转炉及精炼操作、加强连铸保护浇铸、控制钢铁料及合金料中的钛含量、优化钢中酸溶铝及精炼渣中氧化钛的含量,最终将轴承钢中的氮含量由0.005 0%降至0.003 8%,钛含量由0.004 5%降至0.001 3% [47]。
4. 生产工艺发展现状
目前世界上轴承钢的产量和质量处于领先地位的是日本和瑞典。它们生产工艺技术及轴承钢质量水平代表着当今轴承钢的最高水准,是各国轴承钢发展和追赶的方向。在瑞典和日本,70年代就普遍采用炉外精炼,氧含量降低到20 ppm以下 [48]。80年代中期至90年代,GCr15轴承钢的氧含量已经降低到20 ppm以下,现在日本山阳厂生产的超纯轴承钢氧含量己达到4~5 ppm。文献称 [49],当轴承钢氧含量从30 ppm降至15 ppm 时,其疲劳寿命提高5倍;若降至10ppm,疲劳寿命可至15倍;进一步降至5 ppm时,疲劳寿命可提升30倍。
国内外主要轴承钢生产厂家所采用的工艺流程和钢中部分微量元素含量如表4所示 [50]。国外比较典型的轴承钢生产工艺流程主要有瑞典OVAKO钢铁公司的生产工艺,和日本山阳特殊钢公司SNRP超纯净轴承钢生产工艺。
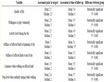
Table 4. The production process of bearing steel in various countries in the world and the content of trace elements in the steel [50]
表4. 世界各国轴承钢生产工艺及钢中微量元素含量 [50]
1) 瑞典OVAKO
瑞典OVAKO厂生产超洁净轴承钢的工艺流程如图3所示,该工艺主要流程是:废钢采用电炉熔化,偏心炉底出钢(EAF)过程中添加Fe-Al、Fe-Si合金进行初步脱氧,进入ASEA-SKF钢包工作站后扒渣。之后,钢包被送入精炼站,添加合成渣进行二次脱氧,同时进行合金化操作。真空处理除去H2、N2等气体杂质,再加热后进行模铸。通过该工艺其钢的氧含量可控制在4~6 ppm,轴承钢的极限疲劳强度和韧性在轧向和径向等各个方向基本相同。
该工艺着重于控制夹杂物的形状和分布,为控制钢中大型夹杂物采取以下措施:
1、电炉冶炼精选废钢和各种材料,提高钢质纯净度。
2、精炼时彻底脱硫,控制w(S) ≤ 20 ×10−6,延长脱气时间,增加真空精炼专有工艺。
3、铸锭注重用氩气屏蔽,执行保护浇铸。
4、延长加热炉均热时间,降低因成分偏析生成的夹杂物。
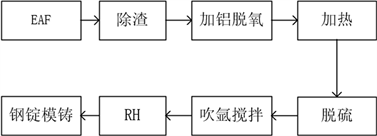
Figure 3. Process flow of Sweden OVAKO for producing ultra-clean bearing steel
图3. 瑞典OVAKO生产超洁净轴承钢的工艺流程
2) 日本山阳特殊公司
山阳特钢采用EAF-LF-RH-连铸-连轧工艺生产的轴承钢,该工艺的主要目标是彻底去除CaO∙n Al2O3 + MgO∙Al2O3系大型夹杂,尽量减少MgO∙Al2O3和卷渣夹杂,对比钢中大型夹杂物的来源,如图4 [24] 所示。LF精炼中大量产生MgO系夹杂,RH精炼后MgO夹杂大部分转变为CaO系夹杂,随真空时间延长至60 min夹杂总量降至最低,软吹后略有增加,浇铸中又全部转变为MgO夹杂。在精炼过程中MgO夹杂显著降低,根据这个规律制定了SNRP生产工艺。
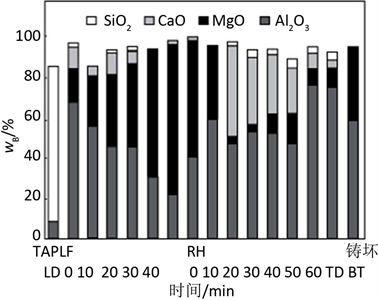
Figure 4. Evolution of inclusions during refining [24]
图4. 精炼过程夹杂物演变规律 [24]
其工艺流程如图5所示。具体的工艺要点为:
1、电炉偏心炉底出钢时将氧化性渣彻底扒除,渣中的(FeO+MnO)含量降低到0.5%以下;
2、中间包采用无渣浇铸;采用高碱度渣(%CaO/%SiO2: 4.5-7.2)精炼,精炼过程保护气氛搅拌强度,ε = 120~150 W/t;
3、RH真空脱气,去氢、去夹杂,真空处理时间为40~60 min;
4、采用密封中间包浇铸和立式连铸工艺,促进凝固中夹杂物上浮。
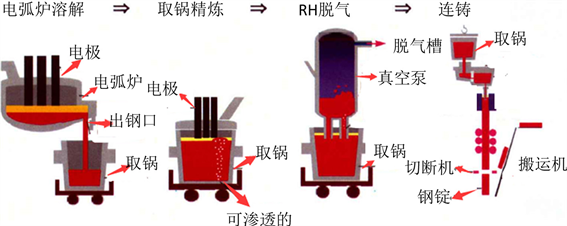
Figure 5. Production process of Sanyang Special Steel for high clean bearing steel
图5. 山阳特钢生产高洁净轴承钢工艺图
3) 国内轴承钢生产工艺
大冶钢厂、上钢五厂和江阴兴澄钢厂等几个优特钢企业是国内轴承钢生产技术先进、质量优良的厂家。在氧含量控制这方面以江阴兴澄钢厂为例,其主要生产工艺为:转炉→LF→VD→CC,在精炼钢包内采用Al块进行沉淀脱氧和扩散脱氧形成白渣精炼,精炼结束进入真空前采用变渣操作形成低碱度渣,在VD炉67 Pa的真空度下进行保真空处理15分钟,真空处理结束进行弱吹氩处理,然后采用连铸保护浇注。该工艺下生产的轴承钢氧含量可达5 ppm左右,达到极高的纯净度目标 [10]。
目前,国内轴承产品与发达国家相比还存在一定的差距,国产的优质轴承钢氧含量虽然可以达到接近世界先进水平,但是在夹杂物的形态、数量、组成、尺寸以及分布等方面的控制还极不稳定。其次,在钢种数量、产品质量以及热处理设备和工艺等方面还有很多不足。
通过这些工艺已经能生产很好的轴承钢,但是为了满足一些具有特殊要求的轴承钢,通常利用电渣重熔工艺来进一步提高轴承钢的冶金质量。电渣重熔通过渣洗提高轴承钢的纯净度,获得均匀细小的新生夹杂物,并通过水冷结晶器获得均匀的组织,质量稳定性高 [51]。
电渣重熔过程主要是自耗电极熔化、金属汇聚成熔滴、熔滴在渣池中穿落、形成金属熔池和金属凝固结晶的过程,其原理如图6 [31] 所示。
1 自耗电极;2 水冷结晶器;3 渣池;4 熔池;5 电渣锭;6 短网;7 变压器;8 护锭板;9 水箱;10 绝缘橡胶板
Figure 6. Principle diagram of electroslag remelting [31]
图6. 电渣重熔原理图 [31]
与其他精炼工艺相比,电渣重熔具有以下特点:由于钢液与熔渣接触的比表面积很大,钢液与熔渣反应充分,同时在洛伦兹力的作用下熔渣得到充分搅拌,钢渣界面得以不断更新,有利于熔渣对非金属夹杂物的吸附;重熔过程中熔渣和钢液具有较高的过热度,高温的熔池促进一系列的物理化学反应的进行,提高钢液的纯净度;金属熔化、浇注和凝固始终在液态渣层下进行而与大气隔绝,减少了钢的污染;液态金属在铜制水冷结晶器中凝固而不与耐火材料接触因而避免了普通冶炼和铸造方法因为耐火材料而造成的污染;自上而下的顺序凝固条件保证了重熔金属铸锭结晶组织的致密与均匀等。
抚顺特钢 [52] 采用控制钢中残余元素、VD精练结束前高拉铝、采用保护气氛浇注、使用保护气氛电渣炉等工艺,生产的大规格风电轴承钢G20Cr2Ni4A控制氧含量在15 ppm左右,B细类夹杂物 ≤ 1.0级。
攀钢通过电炉(EBT) + 精炼炉(LF) + 真空脱气(VD) + 浇注电极棒 + 电渣重熔(ESR))这一工艺流程,提高了渗碳轴承钢的洁净度,使氧含量 ≤ 15 ppm,电极棒氢含量 ≤ 2 ppm,电渣锭锻后无白点;夹杂物八项和 ≤ 2级,B细 ≤ 1级,D细 ≤ 1级。
随着工业制造领域不断发展,这对国内轴承钢的研发制造提出了新的挑战,高洁净轴承钢的研发生产成为当前国内轴承行业亟待解决的问题之一。
5. 总结
总体来看,中国轴承行业经过近几十年的发展已有了显著提升,但在高端轴承领域,由于对钢中夹杂物、碳化物的尺寸与分布以及低倍组织缺陷的控制精细程度不足,使高品质轴承产品的质量稳定性得不到保障。基于此,对氧含量和夹杂物的控制应更严格;针对碳化物问题应通过控扎控冷、球化退火等先进工艺消除碳化物偏析,提高其分布均匀性,最终实现组织细化与均匀化。
基金项目
本文来自四川省科技厅重点项目(2019YFG0511)的支持。