1. 引言
近些年,随着新能源行业的发展,半导体器件在风力发电、电动汽车等新能源行业的应用中占据日益重要的地位。半导体器件的功率和频率更高,集成规模也越来越大。与传统的树脂基片材料相比,氮化铝陶瓷材料具有较大温度范围内使用无异常、导热系数高、硬度大、耐腐蚀等优点,是优质半导体器件的最佳材料。氮化铝陶瓷材料的导热系数与氧化铍相差无几且无毒无害,热膨胀系数与硅相近;强度高,并且强度随温度升高变化微小;介电常数低,与氧化铝不相上下;化学性质稳定,可不被铜等金属侵蚀。氮化铝广泛应用于新一代半导体基片和电子器件封装材料,因此氮化铝的研究对于经济发展以及行业进步的意义重大 [1] [2] [3] [4]。本文介绍了氮化铝陶瓷的性能、及近些年氮化铝陶瓷的成型技术和烧结技术的发展状况,并探讨了氮化铝陶瓷的未来发展方向,希望可以为氮化铝陶瓷进一步的研究以及应用探索提供参考。
2. 氮化铝
氮化铝(AlN)是强共价化合物,被F. Briegler和A. Geuther于1862年发现 [5]。氮化铝是二元Al-N系中唯一稳定存在的化合物,具有六方纤锌矿的特点,在AlN晶胞中,每个Al原子填充在以4个N原子为顶点的四面体空隙中,形成[AlN4]四面体。在氮化铝晶体中,Al-N键的平均键长为0.1885 nm,而[001]方向的Al-N键键长为0.1917 nm,相较其他三根Al-N键,所以形成了一个畸变的[AlN4]四面体结构,其空间群为P63mc,晶格常数为a = 0.311 nm,c = 0.978 nm [6]。
AlN具有以下四个方面的优异性能:
1) 热学性能。单晶氮化铝的热导率理论值可达320 W/(m·k),室温下其热导率是Al2O3的数倍,与氧化铍的热导率(理论值为350 W/(m∙k))相近,并且无毒无害。随着温度升高,氮化铝的导热性能会逐渐优于氧化铍 [7]。在常温下氮化铝的热膨胀系数(4.5 × 10−6˚C)与硅的热膨胀系数(3.5~4 × 10−6˚C)接近。
2) 电学性能。常温下,氮化铝是优良的绝缘材料,其电阻率约为1014 Ω∙cm并且击穿电压可达到15 kV/mm;氮化铝与氧化铝的介电常数相近,可达8.9 F/m (1 MHz),氮化铝的介电损耗约为(3~10) × 10−4 (1 MHz)。
3) 力学性能。常温下,氮化铝陶瓷硬度约为12 GPa,密度理论值约为3.26 g/cm3,杨氏模量为308 GPa,莫氏硬度为7~8。氮化铝在2200℃左右分解,室温下抗弯强度可达到300 MPa。氮化铝的强度受温度的影响不大,如温度为1300℃时,氮化铝的高温强度比室温下的强度降低约20%,而氧化铝和氮化硅在高温下下,其强度总体要减少50% [8]。
4) 化学性能。氮化铝材料耐高温抗腐蚀,可以稳定存在于砷化镓等化合物的熔盐中,并且铝、铜、镍等金属也无法浸润氮化铝材料。氮化铝开始发生氧化的温度约为700℃~800℃,常温下使用氮化铝材料不用考虑器件被氧化的问题。氮化铝容易与空气中的水蒸气发生反应,因此需要在干燥阴凉处保存。
3. 氮化铝陶瓷成型技术
AlN陶瓷的成型方法有干压、等静压、粉末注射成型和流延成型等。根据产品不同的性能要求以及生产成本的控制,需选择合适的成型方法。
3.1. 干压成型
干压成型由于操作简单可实现连续生产的优点,在工业生产中得到了广泛的应用,在原料混合均匀后,加入适量的结合剂进行造粒,向模具中加入一定量的造粒后的粉料,在压片机上加压形成一定形状的坯体,所施加的压力与所要求的成品性能相关。
干压成型具有工艺简单效率高、在工业应用中容易进行连续生产等优点;但是在压片过程中容易形成应力分布不均造成坯体密度不均,组织结构的均匀性相对较差,会产生开裂、分层等现象;另外模具的造价较高,连续的轴向压制对模具的损害较大导致生产成本上升。
3.2. 等静压成型
等静压成型是将粉体放入高压容器中,利用液体对粉末施加压力,粉体受到来自各个方向并且相等的力,所以冷等静压工艺制备的样品密度高且均匀。等静压成型根据加压过程中的温度可分为冷等静压、温等静压、热等静压。一般情况下,粉体主要采用冷等静压成型,压力范围为100~400 MPa。等静压成型过程可以分成三个阶段:初期压力较小,粉体颗粒开始承受压力进行一定程度的重新堆积;中期压力升高,颗粒发生局部流动,部分团聚粉体出现碎化现象;后期压力达到峰值,排出气体,体积进一步压缩,坯体达到致密化。Watari等 [9] 通过以Y2O3,CaO,Li2O为复合烧结助剂,将AlN粉末通过冷等静压在200 MPa下压制60 s成型烧结制备得到了较高热导率的AlN陶瓷。
等静压成型可以生产具有复杂形状的AlN陶瓷,制备出的坯体密度高且均匀。但由于生产成本较高、生产效率较低,等静压成型在工业生产中的应用较少。
3.3. 粉末注射成型
粉末注射成型是一种结合现代高分子注塑理论与陶瓷制造技术的成型方法,是将氮化铝粉末与有机粘结剂等原料均匀混合,原料混合后在一定温度、一定压力下被高速送入注塑成型室内进行成型,成型后采用合适的方法脱除坯体中的粘结剂,最后经烧结获得产品,工艺流程如图1所示。
陶瓷粉末注射成型可以制造形状复杂、尺寸精度要求高的产品。鲁慧峰等 [10] 采用质量分数为95%的氮化铝粉末和5%的氧化钇添加剂,两者混合均匀后加入酒精溶剂进行造粒,在注射压力为60 MPa~70 MPa、注射温度为150℃~170℃条件下,以热脱脂的方式脱除有机粘结剂,置于真空碳管加热炉中,在流动氮气气氛下进行高温烧结,制得了AlN陶瓷零件。
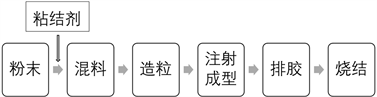
Figure 1. Process flow chart of injection molding
图1. 注射成型的工艺流程图
注射成型具有成型样品精度高表面粗糙度小、密度均匀、强度高、易实现连续生产等优点,注射成型技术广泛应用于电子信息工程、生物医疗、钟表业以及航空航天等工业领域。但是注射成型主要用于制备小型精密部件,在大部件的制造中成本仍然较高。
3.4. 流延成型
流延成型是将氮化铝粉料与各种添加剂均匀混合制成浆料,而后浆料经漏斗传送至载带上,通过载带和刮刀的相对移动形成素坯膜。在配制浆料过程中需要加入分散剂来避免浆料中的粉末进行团聚沉降,加入粘结剂来保证干燥后生带的成型,加入增塑剂来使生带具备一定的柔韧性 [11]。分散剂与粘结剂的作用是相反的,不可同时加入,要分先后次序。流延工艺的流程中分散剂、粘结剂、增塑剂的选择及含量配比很关键,都会影响最终产品的性能。
桂如峰等 [12] 采用流延成型工艺制成素坯,以无水乙醇和丁酮为混合溶剂,以三油酸甘油酯为分散剂制备浆料,制得了形貌良好、柔韧性符合要求的氮化铝生坯,而后经排胶并高温常压烧结后,最终获得了致密度达98%的AlN陶瓷。
流延法成型具有工艺简单、生产效率高、经济效益高等优点,但是流延法成型更适用于制作片状材料,无法实现AlN陶瓷复杂形状的成型。
3.5. 3D打印成型
3D打印是一种可快速成型的增材制造技术,要首先在电脑上创建数字模型,而后将模型数据导入3D打印机中,采用粉末状金属或塑料等可粘合可流动的材料,按照数据模型进行逐层构建整个物体。在陶瓷成型的应用中,光固化3D成型技术应用最为广泛。Belmonte等 [13] 采用3D增材制造技术,获得了气孔率在45%~64%之间的氮化铝多孔陶瓷,研究发现长方体陶瓷的有效导热系数表现出各向异性,纵向的导热系数大约是横向的六倍,这一现象和多孔结构的解离变化有关。
相对于其他成型方法,光固化成型技术以数字化模型为基础,可以制造具有高精确度、形状复杂的氮化铝陶瓷器件。随着研究的不断深入,3D打印在航天、汽车、生物医疗等领域的应用将会不断扩大。3D成型技术的在陶瓷中的应用关键在于要配制高固含量和低粘度的陶瓷浆料,目前可以用于3D打印的陶瓷浆料很少,这就很大程度限制了3D成型技术的在陶瓷中的应用发展。
4. 氮化铝陶瓷烧结技术
烧结过程是陶瓷制备过程中的关键,直接影响陶瓷产品的显微结构如晶粒尺寸与分布、气孔率等参数进而影响陶瓷产品的使用性能。在AlN陶瓷制备中常用的烧结技术有无压烧结、热压烧结、放电等离子烧结、微波烧结等。
氮化铝陶瓷的烧结过程可以概括为四个阶段:一、烧结前期,坯体中的颗粒在空间中多以点为接触,颗粒间的距离较大。二、烧结初期,温度逐渐升高,颗粒之间的键合发生变化,颗粒相互靠近发生重排,此时颗粒之间仍以点接触为主,但是颗粒间的距离与烧结初期相比有所减小。三、烧结中期,温度进一步升高,颗粒间开始以面接触为主,形成晶粒网络,传质过程开始,但气孔间仍相互联通。四、烧结后期,随着传质过程的进行,晶粒继续发育长大,气孔变形缩小为相互孤立的闭气孔,最后迁移到陶瓷表面而消失;还有一小部分的微小气孔留在了烧结制品中。随着烧结的进行,大量的气孔发生由大到小、由内部到表面再到最后消失的过程,陶瓷的体积不断减小,陶瓷完成致密化过程。
4.1. 无压烧结
无压烧结是指在常压下,将具有一定形状的坯体放在一定温度和气氛条件下经过物理化学过程,烧结成致密、体积稳定、具有一定性能的块状固体的过程。一般烧结温度在1600℃~2000℃之间。
Watari等 [9] 以Y2O3、CaO和Li2O为添加剂,采用无压烧结在1600℃保温2 h,AlN烧结体密度为3.3 g/cm3;保温6 h后,AlN试样的热导率达到135 W/m∙K,研究发现Li2O与Al2O3形成低共熔液相,浸润AlN晶粒,从而有效地降低烧结温度;最后Li2O被烧失,在烧结产品中没有引入更多的杂质相。
无压烧结法工艺简单,不同形状、大小尺寸的物件都可采用此法烧结,温度制度便于控制。但是在烧结过程中无法避免烧结样品与空气接触被氧化,因此不可用于制备不能被氧化的制品。
4.2. 热压烧结
热压烧结是指对模具中的粉体同时加热并加压,随着温度升高粉料转变为热塑性状态,发生晶界滑移的传质过程,粉料承受压力进而发生挤压蠕变的传质过程。这两种传质过程同时进行,显著促进颗粒之间的传质过程,可达到降低烧结温度和提高产品致密度的目的。在一定的压力下进行烧结,材料可快速地达到高致密度的状态,其晶体结构以及分子状态可能产生一些变化,从而热压烧结产品能够具有在无压烧结工艺下所达不到的性能。
Jiang H等 [14] 以CeO2-CeF3为复合添加剂,采用了热压烧结,制备了导热系数为191.9 W/m∙K的AlN陶瓷。由于复合添加剂使得AlN陶瓷中晶界相和氧杂质大量减少,以及烧结过程中的碳污染导致AlN陶瓷电阻率降低,所以热压烧结能有效提高AlN陶瓷的导热系数,改变其电学性能。
热压烧结由于加热加压同时进行,有助于颗粒间的接触扩散和传质过程的进行,还能降低烧结温度、缩短烧结时间,可得到力学及电学性能良好的产品。但是热压烧结的缺点是工艺过程及设备复杂,模具材料要求高,不易于生产控制,能源消耗大,生产效率较低,生产成本较高。
4.3. 放电等离子烧结
放电等离子烧结是利用脉冲电流产生的脉冲能、放电脉冲压力和焦耳热来使得烧结温度迅速升高,进而获得烧结产品。其过程大概是首先将坯体直接装入石墨等可导电材质制成的模具内,压头施加适当的压力,电极通入电流使坯体升温烧结,坯体升温后再进行热塑成型和水循环冷却等步骤,获得高性能陶瓷材料。放电等离子烧结过程中的压头压力,电场以及快速形成的温度场都加速了烧结的进行。
Hyoung-Won S等 [15] 采用放电等离子烧结法,加入质量分数为2%的MgF2为添加剂,在N2气氛中烧结至2000℃,制备了半透明AlN陶瓷。研究发现添加MgF2后,AlN陶瓷的透射率显著提高。
放电等离子烧结具有升温速度快、烧结时间短、烧成温度低、生产效率高、制品组织均匀、节能环保等工艺优势,还可制备具有烧结梯度的材料和外形复杂的器件。但是放电等离子烧结的设备需要改进,以适应更大尺寸的产品烧结。
4.4. 微波烧结
微波烧结是指材料坯体本身具有的微观结构,可以吸收微波特殊波段的能量,从而使坯体自身的温度不断升高,其加热过程在整个坯体内同时进行。此外,微波烧结是一种自内而外的活化烧结过程,所以无论是加热升温还是产品烧结完成所需要的时间都大大缩短 [16]。由于烧结过程的快速完成所以可有效阻碍制品内的晶粒生长,从而获得晶粒细小、组织均匀并且性能优良的产品。
卢斌等 [16] 采用微波烧结法,使用高纯度的氮化铝微粉原料,不使用烧结添加剂,烧结至1700℃并保温2 h,制备出致密度达到99.7%的氮化铝陶瓷。
微波烧结是一种快速升温的烧结方法,具有烧结周期短、生产效率高、环保节能等优点。但是在烧结过程中难以准确控制温度的变化,实际温度曲线会有所波动,难以保证制品的均匀性,制品尺寸越大这一现象发生的频率也就越高。
4.5. 不同烧结方式对比
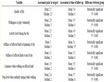
Table 1. Comparison of different sintering methods
表1. 不同烧结方式对比
综合来看(表1),上述几种烧结方法中,无压烧结制品的致密度较低;热压烧结能耗大;微波烧结存在烧结不均匀的问题;放电等离子烧结当前的设备水平以及生产可控性远不能满足工业化生产的需要。环保节能高效是未来烧结技术进步的主基调,生产中既兼顾经济效益又能实现保护环境的目的。
5. 展望
近几年以及未来较长一段时间内,新能源、电子产品、互联网、信息数字化等为人们提供便捷的同时也会更加深入影响着人们的日常生活,因而对于一个国家的发展同样至关重要。那么贯穿其中的基础就是性能更加优良的半导体产品的开发及应用。
氮化铝陶瓷基板既具有优异的热学性能、电学性能、力学性能以及化学稳定性;并且生产制备氮化铝的原料丰富,有可观的经济效益。从氮化铝粉体的制备到最后氮化铝器件的生产,都有大量的人员参与到研究中,为科学技术更进一步而努力。从这些研究成果以及行业生产现状来看,目前被广泛应用到生产中的技术,生产效率较高,经济效益好但是产品的质量还有很大的提升空间,生产耗能较大;而新兴的制备技术,虽然制品的质量更优,生产过程也更节能环保但是一般生产设备复杂昂贵,无法大批量生产。
因此如何改进现有生产技术既降低能耗又能保证产品质量和产量;如何将新兴技术更好地与实际生产相结合;如何将旧技术与新技术相结合应用到生产中;是否可以实现从粉体的制备到最终制品产出的一体化生产,都将是有助于行业进步的研究方向。进步来源于不断地探索,行业发展既要有“金山银山”也要保证“绿水青山”,有助于国家发展,有助于人类未来。
基金项目
感谢河南省科技厅自然科学项目(172102210227)的资助。