1. 引言
烷基糖苷(以下简称APG)作为新一代“绿色”表面活性剂,具有如表面活性高、配伍性能好、去污能力强、毒性低等许多优点,被广泛应用于各行各业,是关乎国民生计的一类重要精细化学品。生产企业出于成本、利润等多方面因素考虑,多采用无机酸 [1] 作为催化剂。尽管无机酸催化剂的催化能力强、成本低,但其对反应设备易造成腐蚀,而且对环境也会造成一定的影响,不符合我国的绿色可持续发展要求,于是固体酸催化剂在APG生产中的应用成为研究热点 [2] [3] [4]。其中,碳基固体酸作为一种制备简单、催化活性高、廉价且环保的绿色催化剂越来越受到重视。这种催化剂可将稳定、可溶性好的对甲苯磺酸变成不溶性的固体酸,本课题组也制备了一系列用于合成磺基琥珀酸酯类表面活性剂的碳基固体酸催化剂 [5] [6] [7]。由于APG粘度较大,与催化剂不易分离,所以普通的碳基固体酸催化剂回收困难,影响再生使用。而磁性碳基固体酸催化剂可利用磁分离技术 [8] 将催化剂和粘性较大的物质迅速分离,回收的催化剂进行简单处理即可重复使用。本文以Fe3O4为磁基体,淀粉和对甲苯磺酸为原料,采用一步法制备磁性碳基固体酸催化剂Fe3O4/C-SO3H。以直接糖苷化法催化合成辛基葡萄糖苷(以下简称AOG)为探针,对催化剂的制备条件进行优化,为烷基糖苷的绿色化生产提供工艺简单、性优价廉的固体酸催化剂。
2. 实验部分
2.1. 试剂与仪器
四水合氯化亚铁、十二烷基硫酸钠、对甲苯磺酸:AR,上海润捷化学试剂有限公司;六水合三氯化铁、正辛醇:AR,国药集团化学试剂有限公司;氨水:AR,上海凌峰化学试剂有限公司;可溶性淀粉:AR,西陇化工股份有限公司;无水葡萄糖:AR,上海麦克林生化有限公司。
D8-Advanced型X-射线衍射仪:德国Bruker公司;AVATAR360型红外光谱仪:美国Nicolet公司;STA-449F3型同步热分析仪:德国Netzsh公司;S-4800型场发射扫描电子显微镜:日本日立公司;SQUID-MPMS3型振动样品磁强计:美国Quantum Design公司。
2.2. 催化剂的制备
2.2.1. Fe3O4磁基体的制备
采用共沉淀法制备Fe3O4 [9]。先将FeCl2·4H2O和FeCl3·6H2O按照摩尔比1:2的比例溶于超纯水中,然后加入适量表面活性剂,分别采用搅拌、超声波以及搅拌加超声波的混合分散方式,同时利用恒压滴定漏斗将氨水缓慢滴加到Fe2+和Fe3+的混合盐溶液中,然后调节溶液pH至11左右,恒温反应一段时间,整个过程通入N2保护。反应结束后,Fe3O4磁性粒子可利用强力磁铁进行分离,用乙醇和超纯水交替洗涤沉降物至滤液pH为中性且滤液为清液。80℃下真空干燥得到Fe3O4磁基体。
2.2.2. 一步法Fe3O4/C-SO3H的制备
按照一定质量比称取可溶性淀粉和对甲苯磺酸溶于超纯水中,加入适量的Fe3O4磁基体,在恒温振荡器中充分混合30 min后,利用真空旋转蒸发仪除去水分,然后把得到黏稠状液体转移至通入N2保护的管式电阻炉中焙烧一定时间。将得到磁性碳基固体酸催化剂研磨过筛后置于干燥器中保存。
2.3. Fe3O4分散性测试方法
采用ZEN3600型粒度分析仪测试Fe3O4磁性粒子的多分散指数(简称PDI,表示测试样品的粒径均一度,PDI值越小则表明粒子大小分布越集中,可反映出合成的Fe3O4的团聚情况)。样品制作:先取10 mg Fe3O4粉末分散于5 mL去离子水中,然后将其转移至特制样品池中,并且在样品池中加入1 cm3分散液,利用超声波使粉末分散均匀,最后将样品池置于分析仪中测试。
2.4. AOG的合成
根据参考文献 [10],在配有搅拌、控温和分水装置的四口烧瓶中加入正辛醇和自制催化剂,然后分批加入碾磨烘干的无水葡萄糖,整个反应过程通入N2保护。其中,催化剂用量为7 wt%葡萄糖,n(正辛醇):n(葡萄糖) = 9:1,反应温度为140℃。每隔1 h测定反应体系的残糖量 [11],并计算葡萄糖的转化率,转化率基本稳定时视为反应终点。
2.5. 催化剂酸含量测定
采用酸碱中和滴定法对催化剂的酸含量进行测定 [12]。
3. 结果与讨论
3.1. Fe3O4磁基体的制备工艺优化
3.1.1. 表面活性剂种类对分散性的影响
在Fe3O4磁性粒子的制备过程中,可添加少量的表面活性剂对Fe3O4进行表面修饰,减少Fe3O4分子间团聚现象的发生,提高Fe3O4的分散性。在初定表面活性剂用量为摩尔比n(Fe2+):n(表面活性剂) = 1:0.5,分散方式为搅拌和超声波相结合的混合分散方式,超声功率为50 W,反应时间为0.5 h,反应温度为60℃的基础上,考察五种表面活性剂对于Fe3O4分散性的影响,所用表面活性剂分别为十二烷基硫酸钠(以下简称SDS)、烷基糖苷(以下简称APG)、溴化十六烷基三甲铵(以下简称CTMAB)、脂肪醇聚氧乙烯醚(以下简称AEO)、聚乙二醇(以下简称PEG),结果见表1。
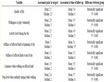
Table 1. PDI values of different surfactants
表1. 不同表面活性剂种类下的PDI值
由表1可知,不同的表面活性剂对于Fe3O4分散性的影响不同。若在合成过程中不添加任何表面活性剂,则Fe3O4磁性粒子的PDI值最大,团聚情况也最严重。添加表面活性剂有利于Fe3O4分散性提高,通过不同表面活性剂之间的对比发现,SDS可显著提高Fe3O4磁性粒子的分散性,因此表面活性剂确定为SDS。
3.1.2. 表面活性剂用量对分散性的影响
以SDS为表面活性剂,在初定分散方式为搅拌加超声波的混合分散方式,超声功率为50 W,反应时间为0.5 h,反应温度为60℃的基础上,考察不同SDS用量对于Fe3O4分散性的影响,结果见表2。
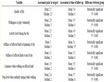
Table 2. PDI values under different dosage of SDS
表2. 不同SDS用量条件下的PDI值
由表2可知,随着SDS的用量的增加,Fe3O4磁性粒子的PDI值呈现先降低后升高的趋势。这表明在Fe3O4的制备过程中,适当增加SDS的用量可减小Fe3O4分子间的相互作用力,提高其分散性。但SDS用量继续增大后,PDI值相应增大,这可能是表面活性剂的过量添加导致Fe3O4粒径增大,不利于缓解Fe3O4的团聚情况 [13]。因此SDS最佳用量确定为n(Fe2+):n(SDS) = 1:0.4。
3.1.3. 分散方式对分散性的影响
以上述确定的最优条件,在初定超声功率为50 W,反应时间为0.5 h,反应温度为60℃的基础上,考察搅拌、超声波以及搅拌和超声波相结合的三种混合分散方式对于Fe3O4分散性的影响,结果见表3。
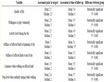
Table 3. PDI values under different dispersion modes
表3. 不同分散方式条件下的PDI值
由表3可知,不同的分散方式对Fe3O4分散性影响不同。采用超声和搅拌相结合的混合分散方式有利于提高Fe3O4磁性粒子的分散性。因此,分散方式确定为超声波加搅拌的混合分散方式。
3.1.4. 超声功率对分散性的影响
以上述确定的最优条件,在初定反应时间为0.5 h,反应温度为60℃的基础上,考察超声功率对于Fe3O4分散性的影响,结果见表4。
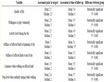
Table 4. PDI values under different ultrasonic power conditions
表4. 不同超声功率条件下的PDI值
由表4可知,随着超声功率的增加,Fe3O4的分散指数在不断降低。这可能是由于超声功率越大,在相同反应时间内Fe3O4吸收的能量也就越多,就能更快的达到最佳的分散状态 [14]。因此,在实验条件的限制下,本次研究确定超声功率为50 W。
3.1.5. 反应时间对分散性的影响
以上述确定的最优条件,在初定反应温度为60℃的基础上,考察反应时间对于Fe3O4分散性的影响,结果见表5。
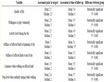
Table 5. PDI values under different reaction time conditions
表5. 不同反应时间条件下的PDI值
由表5可知,适当延长反应时间可降低Fe3O4的PDI值,提高分散性,不过当反应时间过长后,分散性降低。这是因为Fe3O4的制备主要涉及两个阶段,一是达到一定程度过饱和度时的迅速成核,二是晶核表面的缓慢生长 [15],反应时间越长则Fe3O4的粒径也越大,分子间相互吸引力也随之增大,团聚现象也越明显。因此,反应时间确定为1.5 h。
3.1.6. 反应温度对分散性的影响
在上述确定的最优表面活性剂及其用量、分散方式、超声功率和反应时间的基础上,考察反应温度对于Fe3O4分散性的影响,结果见表6。
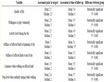
Table 6. PDI values at different reaction temperatures
表6. 不同反应温度条件下的PDI值
由表6可知,适当反应温度可提高Fe3O4磁性粒子的分散性。这是因为温度的控制对于Fe3O4的粒径有很大的影响,适当提高反应温度有利于降低Fe3O4的粒径,并且获得的Fe3O4晶体结构良好 [16]。因此,反应温度确定为70℃。
3.1.7. 最优制备工艺下Fe3O4的粒径分布图
通过对Fe3O4制备工艺的探究,确定其最优的制备条件为:以十二烷基硫酸钠作为表面活性剂,用量为n(Fe2+):n(SDS) = 1:0.4,分散方式为超声波加机械搅拌的混合分散方式,超声功率为5档/50 W,反应温度为70℃,反应时间为1.5 h。对最优条件下制备的Fe3O4磁性粒子进行粒度分析,测得PDI值为0.209,其粒径分布见图1。
由图1可知,Fe3O4的粒径分布图曲线较窄,这表明Fe3O4磁性粒子大小比较均匀,团聚情况不明显,分散性较好。此外,在合成过程中需通入N2保护,因为Fe3O4本身并不稳定,通入N2不仅可以防止Fe3O4转化成γ-Fe2O3,而且还能在一定程度上减小Fe3O4的粒径 [17]。
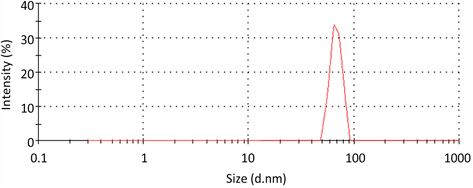
Figure 1. Particle size distribution of Fe3O4
图1. Fe3O4的粒径分布图
3.2. 一步法Fe3O4/C-SO3H的制备优化
3.2.1. 淀粉用量的影响
在初定对甲苯磺酸用量为m(Fe3O4):m(对甲苯磺酸) = 1:2,焙烧温度为300℃,焙烧时间为4 h的基础上,考察淀粉用量对于葡萄糖转化率以及催化剂酸含量的影响,实验结果见图2。
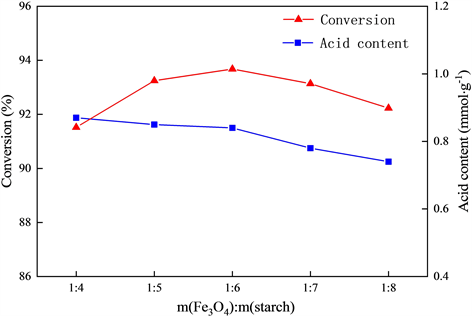
Figure 2. Effect of starch dosage on catalyst activity
图2. 淀粉用量对于催化剂活性的影响
由图2可知,葡萄糖的转化率会随着淀粉用量的增加先升高然后降低,而催化剂的酸含量则随之持续降低。这表明淀粉用量的适当增加可能会有助于催化剂孔道结构的构建,增强催化剂的活性,提高葡萄糖转化率。但是,过量的淀粉则会使葡萄糖转化率和催化剂酸含量的降低,这可能是由于过量的淀粉使得Fe3O4的包裹层增厚,在焙烧过程中造成介孔堵塞,导致催化活性降低。因此,确定淀粉的最佳用量为:m(Fe3O4):m(淀粉) = 1:6。
3.2.2. 对甲苯磺酸用量的影响
以上述考察确定的最佳淀粉用量m(Fe3O4):m(淀粉) = 1:6,在初定焙烧温度为300℃,焙烧时间为4 h的基础上,考察对甲苯磺酸的用量对于葡萄糖转化率以及催化剂酸含量的影响,实验结果见图3。
由图3可知,随着对甲苯磺酸用量的增加,葡萄糖的转化率也随之提高,并且逐渐趋于平缓,催化剂的酸含量也随着对甲苯磺酸用量的增加而不断增加。这表明增加对甲苯磺酸可增强催化剂的催化能力。但是,对甲苯磺酸的用量与葡萄糖转化率并不以线性关系存在,当磺酸基团的负载量达到饱和,添加过量的对甲苯磺酸对提高葡萄糖转化率的作用并不明显。对甲苯磺酸的过量使用不仅会造成原料浪费,而且还会使反应的后处理过程更为复杂。因此,确定对甲苯磺酸的最佳用量为:m(Fe3O4):m(对甲苯磺酸) = 1:2.5。
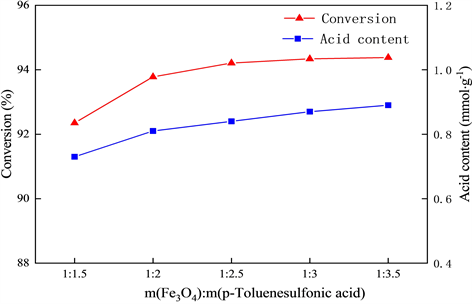
Figure 3. The effect of p-toluenesulfonic acid dosage oncatalyst activity
图3. 对甲苯磺酸用量对于催化剂活性的影响
3.2.3. 焙烧温度的影响
在m(Fe3O4):m(淀粉) = 1:6,m(Fe3O4):m(对甲苯磺酸) = 1:2.5的基础上,初定焙烧时间为4 h,考察焙烧温度对于葡萄糖转化率以及催化剂酸含量的影响,实验结果见图4。

Figure 4. The effect of calcination temperature on catalyst activity
图4. 焙烧温度对于催化剂活性的影响
由图4可知,不断升高焙烧温度,葡萄糖转化率和催化剂酸含量均呈现先升高后降低的趋势,当超过400℃后,葡萄糖的转化率有明显下降的趋势。这可能是由于过高的焙烧温度可能引起了催化剂的烧结,使得催化剂的催化活性减弱。然而,焙烧温度过低会使得淀粉碳化程度不够,未能形成多孔的碳架结构,不利于活性体的负载,导致催化活性降低。因此,最佳焙烧温度确定为400℃。
3.2.4. 焙烧时间对于催化剂活性的影响
在上述考察确定的最优制备条件下,考察焙烧时间对于葡萄糖转化率以及催化剂酸含量的影响,实验结果见图5。
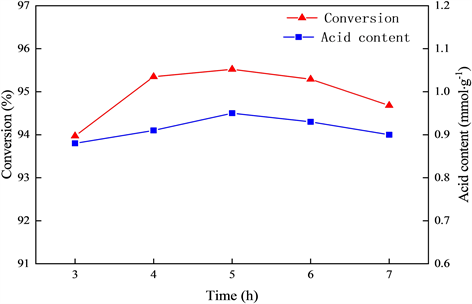
Figure 5. The effect of calcination time on catalyst activity
图5. 焙烧时间对于催化剂活性的影响
由图5可知,随着焙烧时间的延长,葡萄糖的转化率提高,催化剂的酸含量也随之增加,但继续延长焙烧时间,葡萄糖转化率和催化剂酸含量则会缓慢下降。这主要是因为焙烧时间的延长,使得淀粉有充足的时间进行碳化,有助于形成多孔的碳架结构,使磺酸基能更好的与淀粉载体结合,提高催化剂的活性。但当焙烧时间继续延长后,可能会造成碳架结构的崩塌,导致磺酸基的脱落,催化剂活性也会相应减弱。因此,催化剂的最佳焙烧时间确定为5 h。
3.3. 结构表征结果
3.3.1. SEM表征
利用扫描电镜对Fe3O4和Fe3O4/C-SO3H的表面形貌进行观察分析,图6(a)、(b)分别为Fe3O4、Fe3O4/C-SO3H的SEM表征图。由图6(a)可知,采用化学共沉淀法制备的Fe3O4磁性粒子为不规则的球状颗粒,粒径分布较为均匀,且存在一定的团聚情况。由图6(b)可知,通过一步法制备的Fe3O4/C-SO3H为无定形颗粒物,具有一定的多孔结构,比表面积较大,这有利于磺酸基团的负载。Fe3O4磁性粒子埋藏于催化剂内部,使得催化剂具有磁性,能满足磁性分离的需求。
3.3.2. XRD表征
图7为Fe3O4和Fe3O4/C-SO3H的XRD谱图以及标准PDF对比卡片(JCPDS, No.99-0073)。由图7可知,Fe3O4/C-SO3H和Fe3O4分别在2θ为30.1˚、35.4˚、43.1˚、53.3˚、57.0˚、62.5˚处附近出现了6个特征衍射峰,这些峰的位置与Fe3O4标准PDF卡片上的位置基本一致,分别对应Fe3O4的(220)、(311)、(400)、(422)、(511)和(440)晶面,这表明在焙烧后Fe3O4的晶型结构没有发生改变,并且保留良好的磁学性能。
3.3.3. FT-IR表征
Fe3O4和Fe3O4/C-SO3H的FT-IR谱图见图8。由图8可知,565 cm−1和572 cm−1附近的峰属于Fe-O的伸缩振动峰,1625 cm−1、1638 cm−1处的峰归因于芳香环的骨架振动,3398 cm−1和3416 cm−1附近的峰属于O-H的伸缩振动峰。Fe3O4经焙烧后其特征峰的位置由565 cm−1变成572 cm−1,其位置偏移不大,
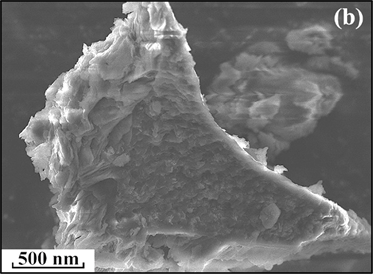
Figure 6. SEM image of Fe3O4 and Fe3O4/C-SO3H
图6. Fe3O4和Fe3O4/C-SO3HSEM图
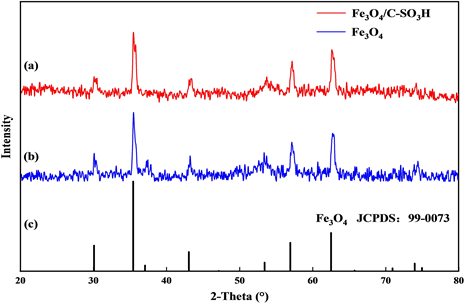
Figure 7. XRD spectrums of Fe3O4/C-SO3H and Fe3O4
图7. Fe3O4/C-SO3H和Fe3O4的XRD谱图
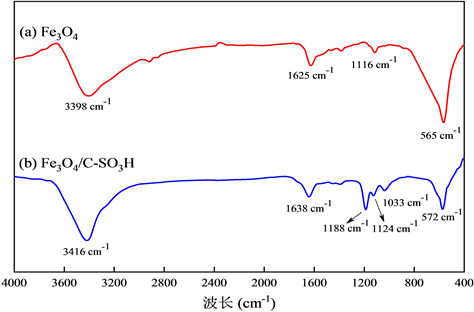
Figure 8. FT-IR spectrums of Fe3O4 and Fe3O4/C-SO3H
图8. Fe3O4和Fe3O4/C-SO3H的红外光谱图
这也表明Fe3O4的结构没有改变。Fe3O4/C-SO3H在1033 cm−1、1124 cm−1和1188 cm−1的位置出现3处明显的特征峰,这主要由磺酸基团上的S=O键弯曲振动导致的,这说明了催化剂中具有磺酸基团。
3.3.4. TG表征
Fe3O4/C-SO3H的TG谱图如图9所示。由图9可知,催化剂在30℃~400℃温度区间内失重缓慢,重量减少约6%,这是由于催化剂受热释放出诸如水和气体之类小分子。而在400℃~800℃温度区间催化剂重量损失超过30%,失重明显。这是因为随温度不断升高,催化剂中的磺酸基团开始发生热分解,导致催化剂重量迅速下降。由此可见,在400℃以下催化剂具有良好的热稳定性。
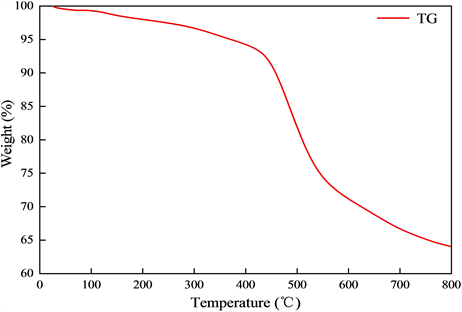
Figure 9. TG spectrum of Fe3O4/C-SO3H
图9. Fe3O4/C-SO3H的TG图
3.3.5. VSM表征
Fe3O4和Fe3O4/C-SO3H的VSM谱图如图10所示。由图10可知,Fe3O4/C-SO3H相比于Fe3O4的磁性强度要小,这主要是由于Fe3O4在焙烧过后被淀粉和对甲苯磺酸包裹,其裸露在外的晶面减少,磁化强
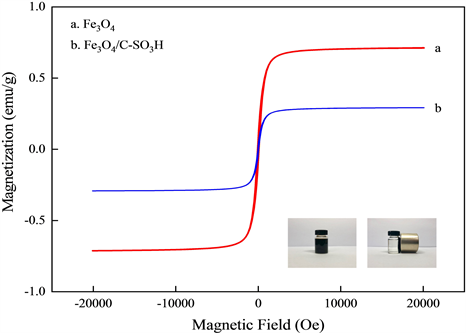
Figure 10. VSM spectrums of Fe3O4 and Fe3O4/C-SO3H
图10. Fe3O4和Fe3O4/C-SO3H的VSM图
度有所下降。为了研究催化剂的分离性能,将Fe3O4/C-SO3H分散于辛醇溶液中,然后在其附近放置一块磁铁。由图10中照片可见:当没有外加磁场时,溶液呈现混浊状,当在溶液外部加入磁场后,催化剂迅速从溶液中分离出来,被吸引到有磁铁的一侧,溶液呈现透明状,当撤去磁铁后,可重新分散至初始状态。这种现象反映了通过施加磁场可以很好地分离并回收催化剂。
4. 结论
本文采用化学共沉淀法制备了Fe3O4磁性粒子,结果表明加入一定量表面活性剂SDS可有效提高Fe3O4的分散性,在超声波加搅拌的混合分散方式下所制备的Fe3O4分散性最好,分散指数PDI达0.209。
一步法制备了磁性碳基固体酸催化剂Fe3O4/C-SO3H,并以辛醇和葡萄糖的糖苷化反应为探针,实验结果发现,在m(Fe3O4):m(淀粉) = 1:6,m(Fe3O4):m(对甲苯磺酸) = 1:2.5,焙烧温度为400℃,焙烧时间为5 h的条件下,催化剂的催化效果最好,葡萄糖转化率可达95.4%。
通过XRD、FT-IR、TG、SEM和VSM等一系列表征手段对催化剂的结构进行分析,结果表明催化剂为无定形颗粒物,而且具有一定的多孔结构,酸含量为0.91 mmol/g,在400℃下具备良好的热稳定性能。此外,在催化剂的制备过程中,Fe3O4的晶体结构没有发生明显变化,依然保留着良好的磁学性能,在外加磁场的作用下能迅速从体系中分离出来。