1. 引言
在生产用于核燃料元件的锆合金包壳管的技术条件中,氢化物取向因子已作为一项检测要求 [1]。测定氢化物取向因子需制备获得渗氢管材。锆合金渗氢方法包括电解渗氢、气相渗氢和高压釜渗氢。电解渗氢的最大优点在于可减轻表面氧化,制备的试样可进一步用于检测力学性能;缺点在于制备流程较繁琐,渗氢后的管材需进一步热处理使富集在表层的氢均匀分布在整个基体中 [2] [3]。气相渗氢的基本原理是在氢气氛围中进行热处理,理论上通过单次实验便能制备氢含量很高的试样,因此操作简便 [4] [5]。高压釜渗氢为常用的渗氢方法,基本原理为使用一定介质的溶液加速锆材的氧化,氧化的同时基体吸氢形成氢化物 [6] [7]。
针对锆合金包壳管材氢化物取向因子出厂检验,对相关生产检测单位而言,操作最方便的渗氢工艺为气相渗氢和高压釜渗氢。在行业内,气相渗氢和高压釜渗氢通常也被称作干法渗氢和湿法渗氢。目前已有大量研究关注如何使用这两种渗氢工艺针对不同锆材制备不同氢含量的试样 [5] [8],但两种工艺针对同种锆材获得的渗氢试样的特征差异还未有相关报道。这两种工艺在工业生产检测中的稳定性和可靠性等是否存在显著差异,值得进一步研究 [9]。
本实验利用Zr-4包壳管开展干法渗氢和湿法渗氢实验,对渗氢均匀性、工艺重复性和氢化物分布进行了系统分析,以期为锆合金包壳管材氢化物取向因子出厂检验提供理论指导。
2. 材料和实验方法
实验使用再结晶退火状态的成品Zr-4管材为研究对象。管材由西北锆管有限责任公司提供。
参照标准ASTM G2/G2M,试样酸洗后置于静态高压釜中,用LiOH·H2O配制Li浓度为0.4~0.6 mol/L的溶液,在360℃/18.6 MPa条件下开展湿法渗氢试验。
使用专用的气相渗氢设备开展干法渗氢试验。设备基本结构为配备了气体管路的普通真空热处理炉。试样清洁后置于炉腔中,在氢气体积分数为1.8%~2.2%的氢氩混合气氛中加热到400℃保温不同时间。
通过化学分析法和图谱法分析氢含量。对获得的管材取样冷镶制备金相测定氢化物取向因子。参照
标准ASTM B 811,依据公式
计算氢化物取向因子,其中N40为与管材径向方向成0˚~40˚内的
氢化物总条数,N0为与管材径向方向成0˚~90˚内的氢化物总条数。
3. 试验结果和分析
3.1. 渗氢均匀性
对于湿法渗氢,试样不同部位氢化物金相特征十分接近,在高压釜均温区内不同位置处的试样的氢化物金相特征也没有显著差异,如图1所示。对多批次湿法渗氢试样的氢含量分析表明,同一高压釜中试样间氢含量差异不超过20 ppm (1 ppm = 1 μg/g)。这说明,湿法渗氢工艺下,试样渗氢均匀,试样在均温区中的位置对渗氢结果没有显著影响。
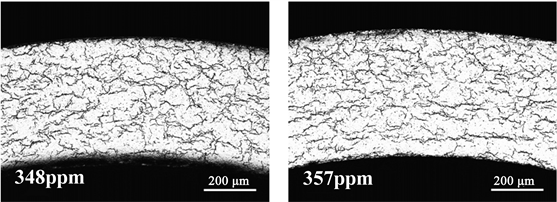
Figure 1. Optical microstructures for hydrides of samples in different locations of the same autoclave
图1. 同一高压釜中不同位置处试样的氢化物金相
对于干法渗氢,试样不同部位的氢含量可能存在较大差异,如图2所示。氢含量分析表明,本实验中试样不同部位氢含量最大差异为55 ppm。金相和氢含量分析进一步证实,同一炉次渗氢试样普遍存在渗氢量差异大的问题。对多批次干法渗氢试样的氢含量分析表明,相同炉次典型位置试样之间的渗氢量最大差异为101 ppm。
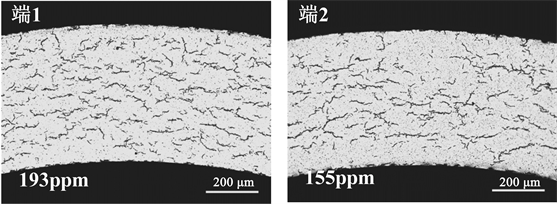
Figure 2. Optical microstructures for hydrides in typical parts of a sample obtained with the dry hydrogenating technology
图2. 干法渗氢试样典型部位氢化物金相
3.2. 工艺重复性
对于干法渗氢,试样不同部位渗氢量存在明显差异,试样位置对渗氢量也有显著影响,工艺重复性很差。干法渗氢工艺重复性差的原因可能在于,试样之间存在屏蔽的效果 [4] [6],炉腔内不同试样处的气体浓度存在差异。
对于湿法渗氢,相同Li浓度下,渗氢量与保温时间并未呈现出明显的正相关特性,难以用渗氢时间验证工艺重复性。氢在锆中的固溶度很低,当温度增加至200℃时固溶度才约15 ppm,此后固溶度随着温度增加显著变化 [6]。在低于保温温度(360℃)的升降温过程中,试样便有一定的渗氢量。在本实验中,由于不同釜次实验升降温过程存在显著差异,自然会导致上述现象。
为了获得外观良好的渗氢试样便于后续观测,兼顾工业生产检验效率,湿法渗氢实验中Li浓度为0.4~0.6 mol/L。Li浓度为0.4 mol/L时,单位增重与渗氢量呈线性相关特征,见图3 (实心黑点)。进一步验证实验证实,Li浓度0.4 mol/L下的试样单位增重与渗氢量对应的数据点(图3中红色方框)均落在拟合线(图3中黑色虚线)附近,说明单位增重与渗氢量线性正相关。
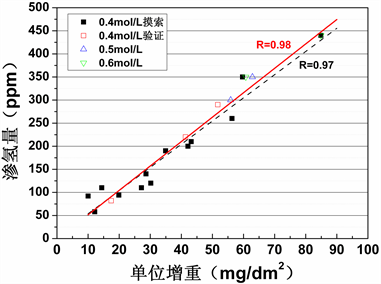
Figure 3. The relationship between the weight gain and the amount of absorbed hydrogen
图3. 单位增重与渗氢量关系
实验进一步发现,Li浓度为0.5 mol/L和0.6 mol/L时,试样单位增重与渗氢量对应的数据点(图3中三角形)也落在Li浓度0.4 mol/L的拟合线附近。这说明,当Li浓度为0.4~0.6 mol/L时,渗氢量与腐蚀增重的关系可用共同的关系式来表达。通过拟合Li浓度为0.4~0.6 mol/L下所获得的相关数据(图3中红色实线),可得到对应的关系式:
式中,
——渗氢量,ppm;
——腐蚀增重,mg/dm2。
对于Zr-4管材的氢化物生产检验,如果每次渗氢试验能保证升降温过程没有显著差异,通过建立保温时间与腐蚀增重的关系,便能建立保温时间与氢含量的关系。对于锆材生产检测单位,湿法渗氢几乎都是使用特定的高压釜,釜体组件和控温系统相对稳定,因此建立保温时间与腐蚀增重的关系具有很强的可操作性。综合上述分析,湿法渗氢工艺比干法渗氢工艺更稳定,更具有重复性。
3.3. 氢化物分布
图4给出了两种渗氢工艺典型氢浓度下的氢化物金相。从图中可以看在,当氢含量较低时(低于100 ppm),干法渗氢工艺获得的氢化物均匀分布,湿法渗氢工艺获得的氢化物便存在局部富集的现象。当氢含量进一步增加至200 ppm附近时,湿法渗氢工艺获得的氢化物已大量连接在一起,呈现出网状特征;干法渗氢工艺获得的氢化物仍均匀分布。当氢含量增加至300 ppm附近时,湿法渗氢工艺获得的管材在横截面内仍存在大量尺寸约100 × 50 μm的区域没有尺寸大于10 μm的氢化物。这说明,相对而言,干法渗氢工艺获得的氢化物分布更为均匀;类似氢含量下,干法渗氢工艺获得的氢化物尺寸更为均匀。
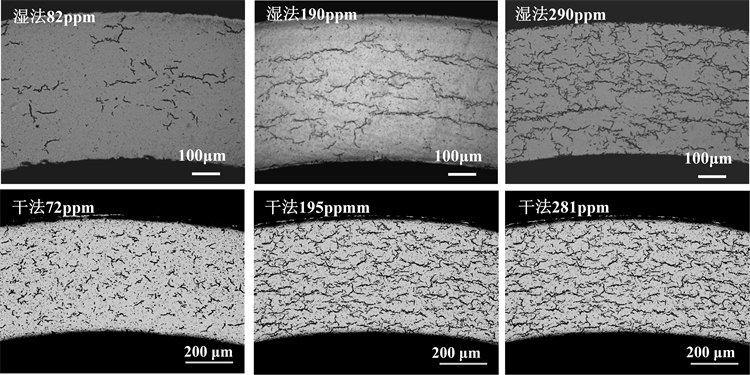
Figure 4. Optical microstructures for hydrides with typical amounts of absorbed hydrogen
图4. 典型渗氢量下的氢化物金相
图5给出了典型渗氢量试样的氢化物取向因子。
对于干法渗氢管材,内中外三层氢化物取向因子十分接近,最大差值约0.1;对于湿法渗氢管材,内中外三层氢化物取向因子差异明显,最大差值约0.3。管材氢化物的形成涉及冷却过程中的形核和长大。湿法渗氢工艺因为冷却速度更慢,氢化物更容易在早期的形核点处长大,生长更充分,更容易连接成长条状分布,内中外三层统计的氢化物取向因子容易出现较大差异。干法渗氢工艺因为冷却速度较快,形核点更多,更容易在锆基体中形成分布和尺寸均匀的氢化物,
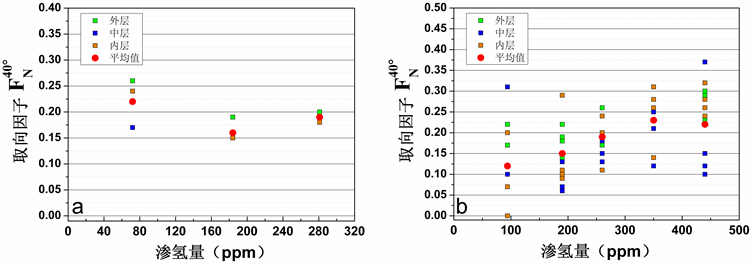
Figure 5. Hydride orientation of tubes with typical hydrogencontents obtained by (a) dry and (b) wet hydrogenating technology
图5. (a) 干法和(b) 湿法渗氢典型氢含量下的氢化物取向因子
导致内中外三层统计的取向因子差异较小。分析了氢化物取向因子的试样,干法渗氢试样渗氢量在约70~300 ppm范围内,湿法渗氢试样渗氢量在约90~440 ppm范围内,氢化物取向因子平均值均低于0.25。虽然这两种渗氢工艺下获得的渗氢管材氢化物取向因子平均值均满足绝大部分生产厂家对成品Zr-4管材的技术要求,但从内中外三层氢化物取向因子的波动来看,湿法渗氢下氢化物分布对内外壁的缺陷或应力等更敏感。再结合前面对渗氢均匀性和工艺重复性的分析,湿法渗氢更适合用于成品管材检验。
4. 结论
利用Zr-4管材开展了干法渗氢和湿法渗氢,对渗氢均匀性、工艺重复性和氢化物分布进行了研究,得到的主要结论为:
1) 对于湿法渗氢工艺,试样渗氢均匀,试样在高压釜均温区中的位置对渗氢结果没有显著影响。对于干法渗氢工艺,试样不同部位渗氢量可能存在明显差异,试样位置对渗氢量也有显著影响。
2) 湿法渗氢工艺比干法渗氢工艺更稳定,更具有重复性。使用LiOH·H2O配制溶液开展湿法渗氢时,当Li浓度为0.4~0.6 mol/L,单位增重(ΔW, mg/dm2)与渗氢量(ΔHs, ppm)对应的关系为
。
3) 两种渗氢工艺下氢化物分布存在明显差异,湿法渗氢获得的管材内中外三层的氢化物取向因子差异更大。在本实验的氢含量范围内,两种渗氢工艺获得的渗氢管材氢化物取向因子
平均值均低于0.25。
4) 湿法渗氢工艺更适合用于成品管材检验。
NOTES
*通讯作者。