1. 绪论
1.1. 研究背景和意义
仓储是物流的核心功能之一,在物流系统中起着十分重要的作用。传统仓储指的是仓库进行物品的入库、储存和出库活动。现代仓储指的是在传统的基础上增加分拣等环节。
近年来,随着互联网行业的迅速发展,网购带动了电商行业的蓬勃发展,面对巨大的物流配送需求,物流仓储面临着最为严峻的考验。本文以A公司仓库为背景,分析其仓库的现状,发现其存在拣货效率低下的问题,导致这些问题的主要原因就是货位设置不合理、拣货前未对订单进行分类归纳排序和拣选路径过长,需要对该仓库存在的问题进行优化,提高仓库运作效率。
本文针对A公司仓储存在的问题及对策进行研究,根据仓库的实际情况进行分析从而得到最佳仓储系统拣选效率,达到提高企业运作的整体效率的目的。
随着经济的飞速发展,企业为了实现经济效益的最大化,需要对仓储的管理引起重视,不断地创新经营理念,争取以最低的成本来取得最高的经营利润。仓储是制造企业厂内物流的重要组成部分,仓储的运作效率影响着整个厂内物流的运作效率。通过仓储管理优化降低仓储管理的成本,间接的影响着整个制造企业的利益,而拣货作业是影响仓库运作效率的关键因素,因此,通过科学合理的方法提高拣货效率是非常必要的。所以,本文针对A公司仓储存在的问题及对策进行研究,通过货位优化、拣货前进行订单的分类归纳排序以及拣货路径优化,达到提高企业拣货效率的目的。通过对此仓库的优化,可以适用于本公司的其他仓库,在减少公司成本的同时,也会使客户的体验感更好以及有利于环境的保护。
1.2. 文献综述
根据公司仓储现在存在的问题,国内学者进行相关研究。雷斌对货位分配优化的文献进行分析整理。对货位分配优化的目标进行归纳,建立优化目标模型并介绍了适用的对象;分析相关常用算法并进行对比;探讨未来的趋势。 [1] 杨华龙根据特殊的环境下仓储货位的定价问题,分析仓储企业与客户的关系,建立货位需求的函数。以仓储企业的收益最大化作为目标,构建货位数量三种不同情形下价格收益的模型,并求得两阶段的动态定价的策略。 [2] 刘倚玮根据仓储货位优化的问题,设计了一种智能仓储的实训平台。此系统集成了管理系统应用监控和货位优化等先进的技术。 [3] 陈晓艳本文研究仓储的拣货路径规划问题。以拣货时间和拣货路径的长度作为评价的指标,采用了四种不同的算法进行了对比研究。将拣货路径优化问题转化为TSP问题,经过仿真研究,得到了适应度进化曲线和最短路径。经过实验测试发现当拣货数量较多时,蚁群算法所得到的最短路径距离相比于其他三种算法更为优化,并且蚁群算法的拣货时间更短。 [4] 时鹏针对仓储的拣货作业中,以缩短拣货人员的行走距离、提高拣货效率为研究对象,根据拣货作业中的存在的问题和解决的方案进行讨论和综述。 [5] 杨文强对带过道的仓储作业进行优化的问题,提出一种多物种协同的进化算法,通过多物种竞争共生的捕食策略,让每一个物种在适应环境方面的能力都得到增强。与此同时引入了变异机制,让全部物种种群多样性能够得到协同改善,提高了每个物种的进化能力,并且提高了求解的效率,而且通过实例验证了这种算法的有效性。 [6] 农官彬本文研究的是怎样从员工的角度,使传统仓储中人工分拣更加高效。 [7] 宋书琴结合配送中心的运作情况,对产品的出入库现状去进行分析。了解出入库效率与不同品类的产品储存位置之间的关系,然后按照ABC的分类法将产品去进行划分,然后再结合EIQ的方法对实际作业中的统计分析,并运用管理思想对配送中心的仓储布局中存在的问题去进行分析,获得优化后的仓储布局结构。 [8] 张锌雨针对G公司的零部件仓库进行了研究,针对零部件仓库仓储布局存在的问题,从功能区布局优化与存储区货位优化两方面展开研究。 [9] 徐宁结合物联网技术中的应用优势,进一步探讨此技术在仓储管理中所能体现出的具体应用。 [10] 路晓娟结合智能立体仓库当前的发展现状,主要针对其货品出入库调度优化及货位优化进行了深入的研究分析。 [11] 李雪主要对优化物流仓储管理的策略进行了分析。 [12] 赵建军针对自营物流在仓储管理方面存在的问题,提出了有针对性的解决措施,提升自营物流的服务质量。 [13] 郑斌采用遗传算法,通过优化备货拣选路径,实现提高仓储管理中的备货效率。 [14] 张敏首先阐述库存控制与仓储管理的概念,然后对库存控制与仓储管理现状进行分析,最后提出针对性的优化措施。 [15] 左佳昕针对中小企业仓储现状所产生的问题提出了优化方案,提高仓库的工作效率与企业效益。 [16] 张玲玲阐述了物流仓储管理的现状和存在的主要问题,提出了解决仓储管理的基本措施。 [17] 季爱迅主要是对电商企业在引用ABC分析法时,缺少针对这三类不同货物的具体库存管理策略,从出入库流程、库存控制、货位分配和运输资源配置角度针对这三类货物提出差异化管理策略,这种差异化管理法操作简便,可对库存物品进行合理控制的同时更便捷地周转库内的货物。 [18] 张静溶对A公司D零部件仓库现状进行分析,发现其存在部分货架稳定性差、零部件货损成本高、拣货做功多的问题,导致这些问题的主要原因就是货位分配不合理,由此根据具体实际情况,设计了合理有效的货位优化方案。 [19] 陈荣首先运用FP-Tree算法获取频繁项集,并构建了以减少订单拣选距离、提高货架稳定性为目标的货位优化模型,再利用理想点法,建立按照权重综合的多目标优化评价函数,最后利用遗传算法进行仿真求解。 [20] Viveros Pablo该工作解决了SKU托盘的多层次存储位置分配问题,在第一级考虑可分割的位置,以改善拣选操作,并减少与起重机路线相关的旅行时间。 [21] Ji Shou Wen采用蚁群算法建立模型,解决拣货优化问题,并以九州通医药物流中心为例,进一步验证分析结果,得到较为理想的优化路径仿真图像。 [22] Xiong-zhi Wang研究了由多个传送带和一个拣货器组成的物料搬运系统中的拣货问题 [23]。
根据对以上参考文献的学习,在本论文中,主要采用构建模型利用数学计算进行分析。
2. A公司现状分析
2.1. A公司简介
A公司位于北京市通州区,主要从事物流仓储、普通货运等业务。公司拥有不同载重量的车辆80多辆,还配备了不同类型的配套起重装卸设备。面对市场竞争日趋激烈,新的形势和新的任务,公司始终以“为客户提供好的产品、良好的技术支持、健全的售后服务”为宗旨,在干部职工的共同努力下,固本强基,开拓市场,开源增效,连年圆满完成生产经营和各项工作任务,企业规模不断壮大,目前有三个仓库,平均每个仓库占地一千平方米左右,随着订单量的增加,盈利水平大幅度提高,但在订单增加的同时,拣货的效率有所下降,根据数据的统计和分析,公司目前出现货位设置不合理、拣货前未对订单进行分类归纳排序、拣选路径过长的问题,存在仓储系统拣选效率低的情况。
2.2. 仓储现状分析
A公司将近70%从事零售行业的仓储,该行业的仓储特点是物品的种类较多,仓库中的仓储货位摆放密集。随着互联网时代的快速发展,正朝着小批量、多批次、多品种、短周期的方向发展,零售行业的订单多而杂,同时,对发货速度的要求越来越高了,导致出入库频率高。拣选的过程包括订单分批、合理安排货品拣选顺序等,所以拣选作业是仓储作业中运营成本较高、劳动较为密集的环节。A公司因货位设置不合理、拣货前未对订单进行分类归纳排序、拣选路径过长而造成的物流仓储效率低下问题。
如图1所示,这是统计2020年8月的每日订单数量和拣货速率之间的关系,在每日订单数量为2000件时,平均每单的拣货时间为20秒;订单数量2500件时,平均每单的拣货时间为21秒;在每日订单数量为3000件时,平均每单的拣货时间为23秒;在每日订单数量为3500件时,平均每单的拣货时间为24秒。
资料来源:作者整理自制。
Figure 1. Average order picking rate
图1. 订单平均拣货速率
2.3. 现有仓储拣货路径问题描述
对A公司2020年8月3日仓库拣货情况以及订单的拣货路径进行分析,经过统计、绘图、计算发现该仓库的拣货过程存在货位设置不合理、拣货前未对订单进行分类归纳排序、拣选路径过长的这三个问题,影响了公司的拣货效率。
1) 货位设置不合理
随着公司的业务增加,订单也随之增多,导致出货频率增高,因为货位设置不合理,出现货物出库拥堵现象,而且拣货效率低下。每一货架为同一种类商品,不同货架的日平均订单数如下表1所示,所占比例图如图2所示。
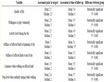
Table 1. Average daily order statistics
表1. 日平均订单数统计
资料来源:作者整理自制。
资料来源:作者整理自制。
Figure 2. Ratio of average daily orders by shelf classification
图2. 根据货架分类的日平均订单数比例
2) 拣货前未对订单进行分类归纳排序
拣货员完全按照客户下单的先后顺序进行拣货。如图3所示,订单A为1号货架区域一内的货格先下单,订单B为2号货架区域二内的货格后下单,会先去拣选A货品,再原路返回拣选B货品,再去按照订单上的顺序去拣选下一个货品,没有明确的拣货路径,走过很多重复路,影响了拣货的效率。
资料来源:作者整理自制。
Figure 3. Schematic diagram of picking path
图3. 拣货路径简图
3) 拣选路径过长
拣货人员每次从拣货口出发,拣货路线呈s型穿梭在巷道中,对巷道中货架上的货物进行拣选,拣选完毕之后到下一个巷道继续拣货。在此过程中,拣货人员随意的挑选路径进入下一巷道进行挑选,走过了许多重复路,造成路径浪费,会带来不必要的时间上的浪费。如图4所示,仓库采取人工拣货方式,在订单的拣货总耗时中,拣货员行走的时间占拣货总耗时的50%左右。拣货路径的不合理会造成设备资源的过多损耗,同时也会造成员工积极性下降,以至于拣货效率的下降。
资料来源:作者搜集整理。
Figure 4. Comparison of the total time spent on order picking at different stages
图4. 订单拣货总耗时各阶段时长对比
3. A公司仓储优化措施
3.1. 拣货路径优化
1) 常见的仓储拣货路径
根据我们不断地进行归纳总结,仓储的拣货路径一般有下面的六种:
① 穿越式路径:拣货员从拣货口出发,进入巷道后开始对两侧货架进行拣货,一直走到巷道的尽头,再进入下一个巷道,从下一个巷道继续开始,直到穿越了所有需要拣货的巷道后,再返回拣货口。
② 分拣式路径:是在实际的工作中,常见的一种拣货路径的规划策略。为了减少行走的距离,这种方法首先需要根据客户的订单排序出拣货的顺序,再利用启发式的算法进行路径优化,这是一种基于智能算法的较为科学的拣货路径。
③ 中点回转路径:让巷道以中线为界线,划分为上下两个区域。拣货员从拣货口出发,进入巷道开始拣货,到达中线后原路返回,然后再进入下一个巷道,下一个巷道也是同样的到达中线后返回,都只在下区域拣货,直到走到最后一个需要拣货的巷道,然后在最后一个拣货的巷道走过中线,然后进入到上区域拣货,也是不经过中线,如同下区域拣货一样,直到回到最后一个需要拣货的巷道,然后返回拣货口。
④ 最大间隙路径:将待拣货物到达两端过道的距离与待拣货物之间的距离进行对比,选择较短距离的路径进行拣选,当货物间的距离大于货物距两端过道的距离时,不需穿过中线,直接回转进入到下一个巷道。
⑤ 分割回转路径:与中点回转路径类似,需要将巷道划分为前后两个部分,但是分割点不局限于中点。
⑥ 回转路径:拣货员只进入有待选货物的巷道,从巷道的一端进入开始对其中一侧的货物进行拣选,之后原路返回拣选另一侧,然后从进入巷道的一端出去,进入到下一个巷道,也是和上一个巷道同样的拣选方式。
2) 模型的一般假设
A公司仓库布局不变,所有货架的大小一样,承受的重量相同,并且每个货架的货源充足。拣货车以安全稳定的速度匀速运行,每次以拣货口为起点,依次经过每一个货架,再回到拣货口。货品在拣取过程中所耗费的时间忽略不计,只考虑拣货车所走过路径用的时间。
3) 变量表示
仓库的布局及数据如图5所示:A公司仓库有两条过道A、C和五条巷道a、b、c、d、e。图中左下角为仓库拣货口,中线上方为区域一,中线下方为区域二,每一个小的方格代表着一个货架。
通过对A公司的考察和测量,获得了仓库的相关数据。巷道的宽度D1 = 2 m,货架的宽度D2 = 4 m,货架的长度为D3 = 1 m,过道的长度为D4 = 5 m。
资料来源:作者搜集整理。
Figure 5. Warehouse data diagram
图5. 仓库数据图
3.2. 构建模型
拣货路径优化模型
在满足上述假设后,拣选作业可能会遇到若干种情况,满足了货位优化以及拣货前对订单进行分类归纳排序的前提,建立拣货路径优化的路径最短模型:
1) 货物都在同一巷道内
如图6所示,拣货员由拣货口出发,由过道C向过道A方向开始拣选,拣选完毕后原路返回,回到拣货口。
资料来源:作者整理自制。
Figure 6. Goods are all in the same roadway
图6. 货物都在同一巷道内
2) 货物在不同巷道内,但在同一区域内
如图7所示,拣货员由拣货口出发,先从a巷道到e巷道方向开始选择巷道拣货,然后再从过道C或者过道A方向向中线拣货,由远离中线的位置向中线的位置顺序拣货,拣货完成后,原路返回,再向下一个巷道开始拣货,直到全部的货物拣完后,再回到拣货口。
资料来源:作者整理自制。
Figure 7. Goods in different laneways, but in the same area
图7. 货物在不同巷道内,但在同一区域内
3) 货物在不同巷道内,且不在同一区域内
如图8所示,这种情况是假设拣货员从拣货口出发,从过道C端进入巷道,从简图中a巷道向e巷道的方向去拣选物品,分析所经过的所有货格的数量;货架中货格数的最大值用Z表示。假设小巷道所需拣选的货品所在的货格最大值L1与编号大的巷道所需拣选的货品所在货格最小值L2和最大值L3。
资料来源:作者整理自制。
Figure 8. Goods in different roadways and not in the same area
图8. 货物在不同巷道内,且不在同一区域内
构建比较模型如下:
①
②
比较①和②的大小
当① < ②时,则从过道进入巷道开始拣货,拣完该巷道的所有商品后不经过中线,原路返回,然后进入下一个巷道进行拣货;
当① > ②时,则从过道进入巷道开始拣货,拣完该巷道后经过中线,经过整个巷道,从另一个端口出去,然后进入下一巷道进行拣货。
3.3. 结果展示
3.3.1. 货位优化
在进行路径优化之前,根据实际情况,首先我们需要进行货位优化。根据上面的图2和表1可以看出,应该对仓储的货位进行优化,将一些出入库频繁的货物安排在距离拣货口的货位,这些距离拣货口最近的位置称为重点货位,其中包括的是1号、2号、3号、4号货架。距离拣货口稍远位置的一些货架称为次重点货位,其中包括的是5号、6号、7号、8号货架。距离拣货口最远的货架称为一般货位,其中包括的是9号、10号货架。
仓储中的货位优化之前,9号货架、4号货架和5号货架的订单数相对较多,应当安排为距离拣货口近的重点货位。8号货架和3号货架的订单数相对较少,应当安排为距离拣货口较远的一般货位。其他的货架按照日平均订单数的多少进行依次排列。优化后的排序结果如表2所示。
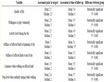
Table 2. Daily average order statistics
表2. 日平均订单数统计
资料来源:作者整理自制。
3.3.2. 路径优化
从拣货员在仓库的日常拣货习惯中可以观察到,拣货员在拣货的过程中大多数具有随机性,他们拣货仅仅按照订单上所显示的货物的顺序,可能会多次走过同一个巷道,这样的拣货路径会走许多多余的路。在2020年8月3日的一次实际的操作中,拣货员按订单上的物品顺序逐次捡取(A、B、C、D、E),拣货路线如下图9所示:
资料来源:作者整理自制。
Figure 9. Schematic diagram of picking route
图9. 拣货路线简图
如图10中所画的红色的为拣货员的拣货路线,拣货员从拣货口出发,进入了巷道a,走了10格,拣选了1号货架上的货品A。之后原路返回走了9格,拣选了2号货架上的货品B。然后走完巷道a后从过道C端出去,进入了巷道b,走了10格,拣选了4号货架上的货品C。走完该巷道后从过道A端出,经过过道A,进入了巷道c,走了6格,拣选了在5号货架上的物品D。走完该巷道后从过道C端出,经过过道C,进入了巷道e,走了3格,到达了E物品所在的位置,拣取了9号货架3格上的物品E。由此可得本次所经的货格数为10 + 9 + 10 + (2 + 7) + (5 + 3) = 46格。
运用本文所构建的模型优化拣货路径,拣货前首先要对订单进行分类归纳排序,然后根据待拣货物的位置进行分析,对所有需要拣取的货品进行合理的路线规划,以节约拣货的时间。
资料来源:作者整理自制。
Figure 10. Schematic diagram of picking route
图10. 拣货路线简图
如图10所示,首先拣货前对订单进行分类归纳排序。拣货员从拣货口出发,进入了巷道a,因为货品A和货品B都在巷道a内,先走1格拣选了货架2上的货品B,然后向中线方向走10格拣选货品A。因为巷道b的货品C与货品A都在区域一,所以属于同一区域,拣货员从巷道a过道A端出去,经过过道A,进入到巷道b,走3格拣选货品C。因为货品D与货品C在不同巷道内且不在同一区域内,那么需要运用构建的数学模型进行比较,其中①为(10 − 1) + 6 = 15,其中②为(12 − 10) + (12 – 6 + 1) = 9,因为15 > 9,所以原路返回到过道A端口出,经过过道A,进入到巷道c,走7格拣选货品D。之后因为货品D与货品E都在区域二,属于处在同一区域内,所以拣货员从过道C端出,经过过道C,进入到巷道e,走3格拣选货品E,拣选完成后返回拣货口。经过计算之后,拣货的顺序为B、A、C、D、E,拣货路径的总格数为1 + 9 + (2 + 3) + (2 + 7) + (5 + 3) = 32格。
综上所述,在未经优化路径之前所经过的货格总数为46,总路程为106 m,优化路径之后所经过的货格总数为32,总路程为92 m,节约了14格,节约了14 m。节约了13%的路程,假设拣货员的速度是不变的情况下,经过路径优化的拣货路线比之前用时缩短了13%。
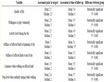
Table 3. Comparison before and after optimization
表3. 优化前后对比
资料来源:作者整理自制。
根据表3和图11所示,优化之前所走路径长度为46格,106 m,优化之后所走路径长度为32格,92 m。节约路径长度14格,14 m。
以A公司仓库2020年8月3日一天的拣货情况为例,仓库内拣货车耗电0.15度/公里,速度为10 km/h,每日的订单数为3000单,电费为0.5元/度。
资料来源:作者整理自制。
Figure 11. Comparison of savings before and after optimization
图11. 优化前后节约情况对比
1) 从企业的成本角度上分析:每次拣货路线节约14格,14 m,每辆车每天即可以节省电费3元,每年就可以节省1095元电费,每个仓库有5个拣货车,A公司有3个类似情况的仓库,倘若每天的每次订单都能够优化后进行拣选,那么一年将会为仓库减少一笔不小的开支。
2) 从客户的体验角度上分析:从速度上面讲,客户越早的接收到货物,体验感会越好。每单少走14 m,每辆车每天少走路程42 km,每天每辆车就可以节省时间4.2小时,每次拣货的时间都减少,后面的货物可以更早的进行拣选,使所有的订单都可以更快的完成。
3) 从环境的保护角度上分析:保护环境人人有责,这是每个公民的职责。根据专家测算,当我们每节约1度电的时候,相应的可节省大约400克的标准煤、4升水,减少约272克粉尘、997克二氧化碳、30克二氧化硫、15克氮氧化物等污染物的排放。
其中标准煤是一种标准能源的表示方式,我们的生活从衣食住行到文化娱乐都离不开能源,它能够为我们提供照明、交通、餐饮、供暖等等方面,同时煤燃烧会产生大量的二氧化碳和尘,对环境危害很大。其中水是生命之源,人的生命一刻也离不开水,同时工业、农业等各个方面也离不开水,水是我们人类生存和发展的重要资源。其中粉尘对人体有危害,而且大量的粉尘悬浮于空气中,能降低大气可见度,影响了人们的视线,降低了生产的效率。其中二氧化碳对环境的危害很大,二氧化碳会导致温室效应,二氧化碳具有保温作用,使地球的温度升高。同时二氧化碳过多还会导致海平面升高,这样对于动物的生存有很大的影响。其中二氧化硫的污染可能形成酸雨,给土壤、森林等带来了严重危害。其中氮氧化物会加重空气质量污染,可以造成酸沉降现象,导致形成酸雨现象。
路径优化之后一年可以节约876 kg标准煤,节约8760升水,降低595.68 kg的粉尘排放量,降低2183.43 kg的二氧化碳排放量,降低65.7 kg的二氧化硫排放量,降低32.85 kg的氮氧化物排放量。这只是考虑一辆拣货车的节约情况,那么让A公司的全部仓库进行优化,节约的数字将会更加客观。如果我们所有的企业都进行优化,从每一个小的细节做起,从节约一度电开始做起,这样就会积少成多,在所有人的共同努力下,会是一个非常可观的数字,逐渐的降低对环境的污染,我们的环境问题将会有所改善。
3.4. 本章小结
本章通过数据统计,利用订单数量的多少进行货位优化,然后在拣货前对订单进行分类归纳排序,在此基础上,构建比较模型进行比较,得到优化后的最短路径。
通过对比优化前和优化后的拣货路径,相同订单情况下,分别进行计算,然后对比整理成表格。分别从企业的成本、客户的体验和环境的保护这三个角度上分析,确定本次的优化是有意义的。
4. 结语与展望
4.1. 结语
随着互联网的飞速发展,消费多样化的时代到来了,物流配送效率成为了电子商务的重中之重。拣货是仓储的重要环节,拣货的速度决定着物流配送的效率。为了降低仓储的管理成本,提高效益,对仓储存在的问题进行合理的优化还是十分必要的。
本文根据A公司出现的拣货效率低的问题,发现了其主要的原因有货位设置不合理、拣货前未对订单进行分类归纳排序、拣选路径过长这三个问题,通过对这三个问题的分析,进行了优化。
货位设置不合理问题:通过对货位号和日平均订单数的分析,根据订单出库数量的多少进行划分,订单多的货位号靠近离拣货口近的位置,而订单少的货位号位于拣货口较远的位置。拣货前未对订单进行分类归纳排序问题:拣货前对订单进行分类,将同一类货物放在一起,再根据货位号进行归纳排序,获得最优的拣货顺序。拣货路径过长问题:这个问题属于仓储中拣货的路径规划问题,这是本文研究的重点,需要综合考虑仓储中的各个因素,构建模型需要根据公司目前的实际情况,本文通过数学计算对A公司的拣货路径进行优化。合理的对拣货路径进行优化是十分必要的,不仅可以减少了拣货路程,缩短了拣货时间,同时还能够减少拣货车的损耗等。
通过对仓储存在的三个问题进行优化之后,再根据同一订单情况下进行优化前后的对比,分别从企业的成本、客户的体验和环境的保护这三个角度上分析, 降低了企业的成本,客户的体验更好,更有利于保护环境,证明了此次的优化是有意义的。
本文主要以A公司的仓储情况为例,对仓储存在的问题进行分析,搜集相关数据,利用数学计算,得到优化后更佳的拣货策略。
4.2. 研究不足与展望
为了方便计算,本文只考虑了拣货车辆经过的路程所用的时间,并未考虑车辆的容积、拣货过程所用的时间等等。对于研究不够深入。
希望可以将拣取货物过程中消耗的时间、车辆的容量、货源充足等因素加入到研究中,深入研究节约时间、设备资源等方面,将会使研究更加的贴近现实,期待拣货路径优化问题会得到更深入的研究。
基金项目
北京石油化工学院北京市URT项目2021J00070。