1. 引言
数字制造是智能制造的重要基础 [1],其虚拟调试是智能制造系统的关键技术。虚拟调试是在仿真模型的基础上,对系统行为和控制逻辑进行测试,便于在智能制造产线安装前发现问题并及时修正,从而缩短现场调试周期,降低调试成本 [2]。郑魁敬等 [3] 在机器人磨削系统运用了虚拟调试。高建超等 [4] 通过虚拟调试实现机器人滚边的位姿优化。许俊芳等 [5] 利用虚拟调试技术解决了车身侧围补焊线工艺规划困难、机器人位姿不可达性和设备干涉等问题。王刚等 [6] 将虚拟调试应用于白车身生产线中。Makris等 [7] 研究了装配单元虚拟验证的完整工作流程。成正勇等 [8] 提出一种基于TIA和Tecnomatix的联合虚拟调试方法。朱鸿泰 [9] 在设备设计阶段利用虚拟调试的方式实现了电机的准确选型。蓝启鑫等 [10] 开发了金属线材折弯的虚拟仿真系统,以检查机床加工动作的合理性。
超级电容是一种新型储能装置,广泛应用在新能源汽车、轨道交通等领域。基于Process Simulate (PS)平台,本文建立了超级电容模组检测线的虚拟调试模型。在虚拟环境中对超级电容模组检测线的PLC程序与机器人控制进行评估和修正,提升系统可靠性,减少现场调试的时间和成本。
2. 超级电容模组检测线虚拟调试方案
虚拟调试包括硬件在环、软件在环虚拟调试。前者使用真实的人机界面(HMI)、控制器以及现场IO设备来控制仿真设备模型,而后者则是将整体设备完全虚拟化 [11] [12]。由于超级电容模组检测线的主线与老化站各具有1个可编程逻辑控制器(PLC),通过对比两种虚拟调试方案,为了避免出现硬件问题,本文采取如图1所示的软件在环虚拟调试方案。具体来说,应用PLCSIM Advanced创建虚拟PLC实现程序逻辑控制仿真,采用Process Simulate软件实现工艺配置仿真,通过连接二者以验证工艺及控制方案的可行性,其实现流程如图2所示。
3. 超级电容模组检测线虚拟调试模型的建立
3.1. 超级电容模组检测线系统方案
首先明确物理系统的动作顺序,并根据PLC程序,导出信号的地址及输入输出类型等信号交互清单。
该检测线共有8个工位,包括上料操作(OP10)、焊点光学检测(OP20)、绝缘测试(OP30)、短接放电(OP40)、均衡老化试验(OP50)、抽检静置放电(OP60)、电容包容量测试(OP70)、下料操作(OP80)。产品采用托盘自动输送,主体采用上下双层倍速链,两端使用气缸提升机。倍速链向前运动,当托盘到达某工位时,挡停机构将托盘挡住,阻止其前进,等待顶升机构将托盘顶起。顶升机构上升后,被测模组脱离倍速链,并由检测机构完成检测项目。检测完成后,顶升机构下降,托盘回到倍速链上。挡停机构降下阻挡块,放行托盘。待托盘完全离开后,阻挡块自动回升。当托盘到达均衡老化试验站时,托盘离开主线,进入上料道。老化站主要由2套老化柜和一台搬运机器人组成。检测到上料道有托盘之后,机器人把托盘抓取至老化柜进行模组老化试验。试验完成后,再由机器人将老化柜中的托盘依次抓取放至下料道上,并返回至主线。
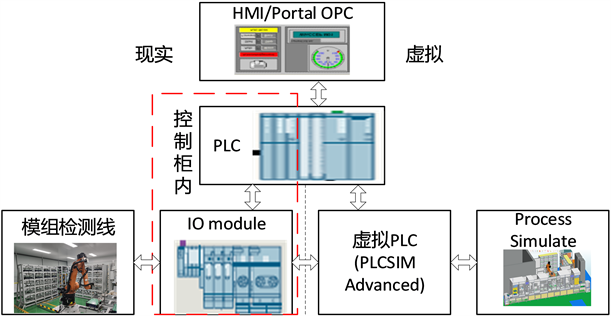
Figure 1. Software-in-the-loop virtual commissioning scheme
图1. 软件在环虚拟调试方案
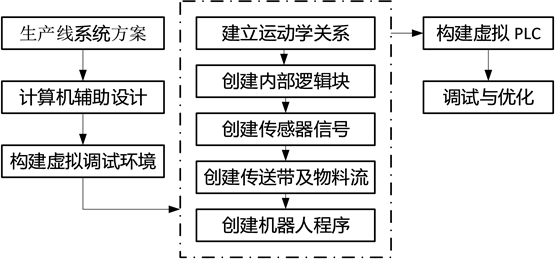
Figure 2. Software-in-the-loop virtual commissioning process
图2. 软件在环虚拟调试流程
3.2. 计算机辅助设计
可将生产线包括静态单元和动态单元。前者指没有任何移动和特定功能的结构,例如底座、轨道、电机等。后者指具有移动和特定功能的结构,例如气缸提升机、顶升机构、挡停机构等。对于动态类机构,必须为其每个动态零件绘制模型,形成三维装配体。最后导入PS,如图3所示。
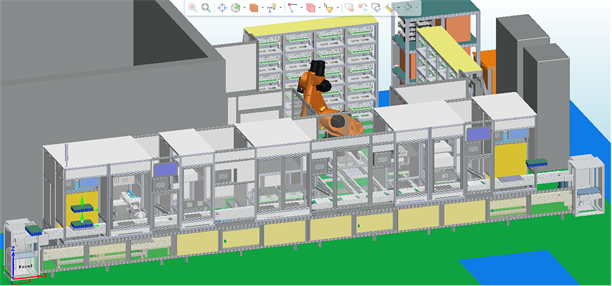
Figure 3. Module detection line in PS
图3. PS中的模组检测线
3.3. 构建虚拟调试环境
3.3.1. 建立运动学关系
分析整线的工作流程,利用Kinematics Editor,根据运动机构的运动规律创建相应的运动学链。如图4所示,以OP30下压检测机构为例,下压检测机构被分为3个元素,即基座、检测治具1和检测治具2,因此在Kinematics Editor中创建了3个链接,橙色链接代表基座,绿色和黄色链接分别代表检测治具1和2,检测治具相对于基座的运动由蓝色箭头表示。最后在Pose Editor中根据工艺设定机构的3种姿态,即原始位、检测治具1下降位、检测治具2下降位。
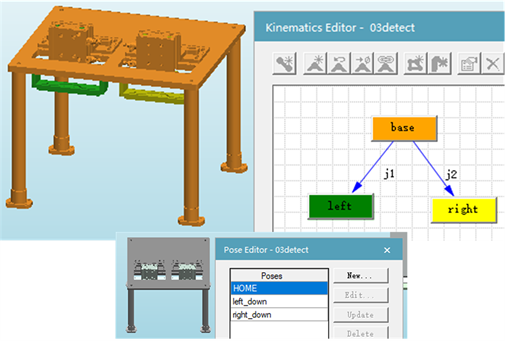
Figure 4. An example of establishing kinematic relationships
图4. 建立运动学关系示例
3.3.2. 创建内部逻辑块
PLC的控制需要通过智能组件的内部逻辑来控制,用于描述运动机构将执行的动作。在PS中,通过将输入输出信号地址与PLC程序中的I/O信号地址对应,设定信号逻辑运算公式等来创建逻辑块(LB)。逻辑块接收PLC输出的控制信号,经由运算公式计算后,控制设备执行相应的动作,并将动作到位的信号反馈给PLC。以OP30下压检测机构逻辑块的创建为例,如图5所示。
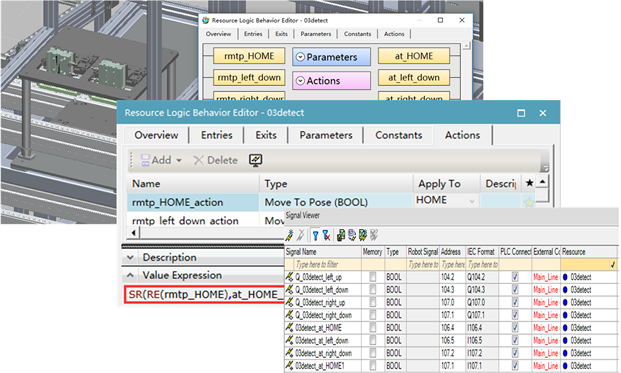
Figure 5. Creation of logic block of push down detection mechanism
图5. 下压检测机构逻辑块的创建
3.3.3. 创建传感器信号
根据模组检测线的控制方案以及传感器的布置情况,在虚拟模型中创建三维传感器模型,并赋予传感器检测对象、检测范围等参数。诸如光电开关、接近开关、磁性开关等传感器返回给PLC的都是布尔信号,因此在PS中将除磁性开关以外的传感器都设置为光电开关,并在Signal Viewer中将传感器信号的地址设置为PLC程序中对应的原传感器的信号地址。对于磁性开关的反馈,使用智能组件的位置信号,并在Signal Viewer中将智能组件中输出信号的地址设置成PLC中对应的磁性开关的信号地址。
3.3.4. 创建传送带及物料流
采用多段传送带拼接的方式,实现工件流转,包括12条传送带:主线段上倍速链、主线段下倍速链、进OP10提升机的传送带、出OP10提升机的传送带、进OP80提升机的传送带、出OP80提升机的传送带、去OP50的上料段、出OP50的下料段、出OP60的下料段、从主线段去OP50的倍速链、从OP50返回主线段的倍速链、从OP60返回主线段的倍速链。在PS中,可使用Conveyor来构建传送带。
物料流表示生产过程中物料的运动变化过程。根据超级电容生产工艺和仿真需要,一共建立了5种工件,包括托盘(trays)、电池(battery)、托盘+电池整体(parts)、托盘(trays_end)、电池(battery_end)。由于从OP10上料直至OP80下料,托盘和电池始终一起运动,故合并为一个工件(parts);下层传送带运送托盘(trays);单独的电池会出现在OP10上料位和OP80下料位,故建立了battery和battery_end;同样地,单独的托盘也会出现在OP10和OP80工位,故建立了trays和trays_end。分别定义5种工件的物料操作,操作之间建立链接(Link)得到完整的动作流程,再将动作都包含进一个复合操作内;将所有物料操作导入物料流窗口(Material Flow Viewer)中,并生成物料流,如图6所示。在仿真运行期间,物料的产生和消失由物料操作实现,物料操作的触发条件由PLC程序或仿真逻辑控制。
3.3.5. 创建机器人程序
根据OP50老化试验的工艺流程,机器人的运动路径主要包括:从OP50上料位抓取托盘存入老化柜、从老化柜中取出托盘放至OP50下料位或OP60抽检位。机器人具体执行存还是取操作,由PLC发出的信号(INT型)决定。老化站共有40个检测位,作用于哪个检测位,也是由PLC内部逻辑计算,并发送相应信号(INT型)决定。按照生产工艺,进一步对机器人路径进行分段,可分为40条抓路径、40条取路径以及若干条公共路径,如图7所示。
在此基础上,创建机器人程序、编辑机器人信号、利用逻辑块(LB)设定机器人逻辑、给机器人程序添加离线编程(OLP)命令、测试程序等,最终完成机器人与其他工装、设备之间的交互。
3.4. 构建虚拟PLC
虚拟调试在于验证PLC程序的可靠性,需要对PLC程序进行预处理,如屏蔽OP10工位处由人工操作获取的扫码数据信号以及双拍开关信号、增加创建托盘和电池的信号等。在Portal中分别打开主线段和OP50老化站的PLC程序,并将它们下载至PLCSIM Advanced,从而建立虚拟PLC。然后,在PS中为仿真模型定义两个外部连接,分别表示与PLCSIM中主线段和OP50段PLC程序的连接。在Signal Viewer中,将PLC Connection与External Connection通过地址进行内外部连接。
4. 调试与优化
如图8所示,在虚拟调试仿真过程中,可以针对传统实体设备调试问题进行数字化诊断。以仿真过程中发现的机器人经常运行至某个位置卡住问题为例,选中卡住的机器人操作,打开机器人程序查看器,查看程序执行至哪一步。发现程序在执行机器人存操作时,机器人经常在放下托盘之后不会回到原位;程序在执行机器人取操作时,机器人经常在将托盘放至下料位之后也不会回到原位。在机器人程序查看器里可以看到,程序是卡在某个Wait信号处,存的过程是卡在等待一个PLC信号(Store Release Done),取的过程是卡在等待一个PLC信号(Release Done)。在Simulation Panel中监控这两个信号,观察到在仿真过程中这两个信号确实有被传递至PS,只是在变为True之后立刻又变回False。等到机器人程序执行Wait命令时,信号已经从True变回False了,所以机器人会卡住。
解决办法如下:如图9所示,在机器人信号窗口中添加两个新的输出信号,在逻辑块中添加两个输入、两个输出,输出表达式写为SR(RE(),),将信号保持到机器人程序执行End。将OLP中相应的Wait信号改为Store Release Done _Hold和Release Done _Hold,仿真发现机器人可以正常工作了。
在PS环境中依据路径分段和规划实现覆盖40个库位的所有机器人路径定义和仿真建模,如图10所示。
由于对超级电容模组检测线的控制程序进行了修正与优化,最终仿真结果显示,模组检测线运行平稳流畅,机器人搬运准确无干涉,生产节拍合适,达到了现场安装的要求。
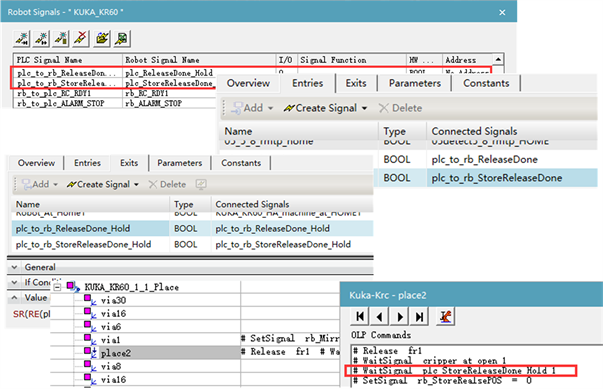
Figure 9. Robot commissioning and optimization process
图9. 机器人调试与优化过程
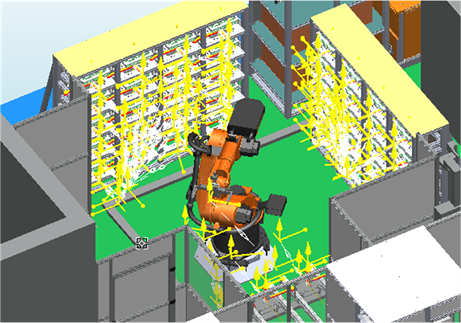
Figure 10. Simulation of robot path planning in PS
图10. PS中机器人路径规划仿真
5. 结语
本文通过Process Simulate建立了超级电容模组检测线虚拟调试模型,实现了设备安装前PLC程序与机器人控制的测试与修正,从而减少了现场调试的时间,节约了调试成本。对于多工位多控制器的自动化生产线的虚拟调试有一定的参考价值,未来将在更大规模的智能制造产线数字化设计中充分发挥虚拟调试的优势。
基金项目
上海市科委科研计划项目“超级电容智能制造关键技术研究及应用”(19511104701)。
NOTES
*通讯作者。