1. 工艺流程简介
湛江钢铁石灰产线由2座1000 t/天,回转窑和2座650 t/天双膛竖窑以及配套的原料成品和加工系统组成,主要煅烧石灰石与白云石,成品主要有块石灰、粉石灰、轻烧白云石和轻烧压球。整套系统采用以西门子S-400PLC为核心的现场总线控制系统和基于WINCC的人机交互界面,集成了远程控制、信号反馈、数据采集和预警等功能 [1]。本次改进主要是针对石灰破碎系统的控制原理进行优化,旨在提高破碎效率,降低操作人员工作强度。
石灰破碎系统是将烧制好的成品块石灰经过破碎与筛分,得到满足粒度要求的粉石灰,主要用户为炼钢和烧结。其工艺流程为回转窑和双膛窑的成品块石灰以及除尘粉通过块石灰运输系统到破碎中间仓储存起来,通过仓底的振动给料机运输至复式破碎机加工成粉石灰,再通过筛分系统将细粒与粗料分离,合格的物料进入粉仓,不合格的物料返回到破碎机继续加工,物料走向如图1所示。
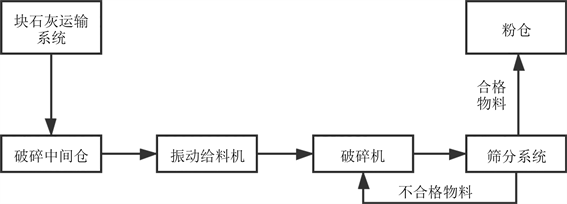
Figure 1. Process flow chart of lime crushing system
图1. 石灰破碎系统工艺流程图
2. 现状分析
破碎系统的关键设备是振动给料机和破碎机,它们的运行状况直接影响到破碎效率,其理想状态是给料机连续运转、破碎机电流稳定、出料流量适中,以斗提机料斗2/3为最佳,太少效率不高,太多容易引起斗提机过载。出于对破碎机的保护考虑,当破碎机出现高电流时需停止振动给料机下料,防止破碎机超负荷运行发生过载现象。由于破碎的原料来源广泛,各类物料的粒度和硬度大不相同,要做到给料机连续运转并不容易。对破碎原料进行分析可得出以下结论:
1) 回转窑块料:回转窑块料为回转窑未经过筛分的成品物料,其粒度适中、质地脆,能被破碎机轻易磨成粉,如图2(a)图所示。加工此种物料给料机可连续运行,是理想的破碎物料。
2) 回转窑筛下料:回转窑筛下料为回转窑块料经过筛分后不合格的细料,其粒度小且含有较多粉料,如图2(b)图所示。由于粉料的破碎时间短,破碎机的电流很低,当出现高电流时往往已经超过破碎机的负荷,从而造成破碎机过载,极大的影响破碎效率。
3) 双膛窑物料:双膛窑物料为双膛窑成品经过鳄式破碎机初破之后的物料,粒度和硬度较回转窑物料要大得多,如图2(c)图所示。加工此种物料极易造成破碎机出现高电流使给料机停机,操作人员需要频繁启动给料机,有时人手不足或未注意到振动给料机停了,没能及时开启给料机造成破碎机空转,大大降低了破碎效率。
4) 除尘粉:除尘粉为KR脱硫加石灰时的除尘粉以及成品区域的除尘粉,此物料全部为粉料,如图2(d)图所示。此物料进入破碎机后极易造成破碎机过载,若大量除尘粉堆积在料仓底部,还会造成破碎机冲料(出料口溢料)和下游斗提机过载,需要人工将溢料清理。处理时间较长,即增加了员工劳动强度,又降低了破碎效率。
综上所述,破碎物料的差异是制约破碎效率的客观因素,而较低的自动化程度又让我们不得不投入大量的人力去抵消这种因素,例如频繁启动给料机、人工测仓位、冲料后人工挖料等。因此,本次研究的目的便是通过对控制原理进行优化改进,提高系统的自动化程度,从而最大限度的消除物料差异所带来的影响,同时减轻操作人员的劳动强度。
(a) 回转窑物料
(b) 回转窑晒下料
(c) 双膛窑物料
(d) 除尘粉
Figure 2. Contrast diagram of broken raw materials
图2. 破碎原料对比图
3. 控制原理优化
图3所示波形为破碎机电流趋势,横坐标为时间,纵坐标为电流,波峰为电流到达预设峰值,此时给料机停机,波谷为电流达到最小值,此时给料机开启,波谷和波峰之间为给料机连续运转的时间。为了对比明显,破碎机a加工回转窑物料,其波形如图3黑色曲线所示,破碎机b加工双膛窑物料,其波形如图3红色曲线所示。
由图可知,加工回转窑物料时波形相对稳定,其波峰到波谷有时可达数小时之久,此时破碎效率最大,加工双膛窑物料波动较大,给料机运行时间仅有几分钟,破碎效率较低。因此,要提高破碎效率,关键在于延长给料机的运行时间,即:
1) 根据物料的品种设置合适的波谷电流(即“高电流”)和波峰电流(即“低电流”),在破碎机负荷内最大限度延长给料机运行时间。
2) 减少破碎机的空转时间,即当到达波谷电流时立即启动给料机。
3.1. 电机电流自主化
“高电流停机”中高电流的实际值是在程序后台设定的,一经设定不会改变,而不同的物料引起的电流波动不一样。适用于回转窑块料的电流限值对于筛下料来说就偏大导致破碎机过载,对于双膛窑块料就偏小使得给料机频繁停机。因此,将电流限值由后台设定改为HMI设定,由操作人员根据实际情况对电流的限值进行自主修改,既可避免物料变化导致破碎机过载,又能最大限度延长给料机的运行时间,从而减少破碎机空转,提高破碎效率。
如图4所示,在画面上组态文本框,将“Field Type”属性设置为“I/Ofield”,将“Output value”与模拟量/工程量转换程序实际值的高限值变量相关联 [2],即可实现在HMI上设定高电流的限值。
3.2. 下料控制自动化
无论是哪种物料,高电流停机的现象无可避免,双膛窑块料更是明显。针对此问题,通过对给料机的启动程序进行优化,使其高电流自动停机,低电流自动启动,并在画面上组态手/自动切换按钮,实现给料机自动下料。通过这种方式,操作人员只需设置好电机的高/低电流,振动给料机就能根据破碎机的电流自动启停。即无需时时盯着画面,又避免了因未及时开启给料机所造成的破碎机空转现象。
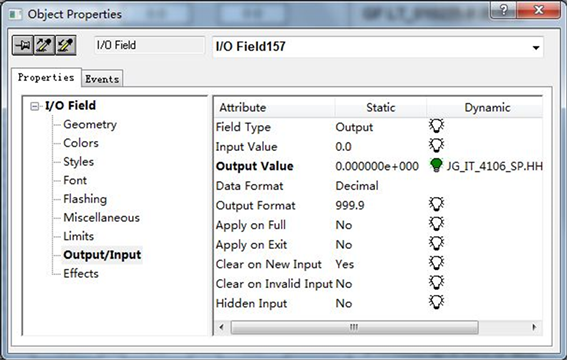

Figure 4. Current Settings screen configuration and properties
图4. 电流设定画面组态和属性
如图5所示,在画面上组态一个按钮并对按钮进行编程,使其按下为“1”同时显示“自动”,再按为“0”同时显示“手动” [2]。如图6所示,通过电流的模拟量/工程量转换程序输出一个“低电流”和
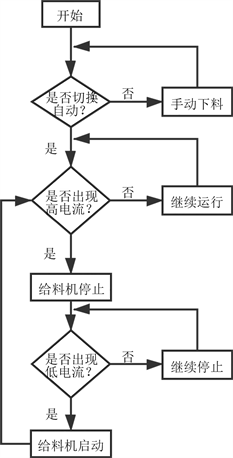
Figure 5. Screen configuration and control logic flow chart
图5. 画面组态与控制逻辑流程图
“高电流”的开关量,将按钮所关联的变量与“低电流”的变量串联,再接入一个通电延时定时器,消除因电流的波动所造成的误启动,最后将编好的程序嵌入到给料机的启动程序中 [3],以此来实现低电流自动启动。将“高电流”开关量串联到电机的“运行条件”程序段中,当出现高电流时即表明运行条件不满足给料机停机,以此来实现高电流自动停止,从而实现破碎系统自动下料功能。
3.3. 料仓料位连续化
除尘粉冲料主要是因为大量粉料堆积在仓底,若要避免这种情况,需采用“半仓下料”的进料模式,即当破碎中间仓的块石灰料位达到50%以上时才允许除尘粉进仓。由于除尘粉体积较小,在给料机运行过程中随着料流向下与块石灰均匀混合,避免大量除尘粉积压在仓底造成冲料。
要实现“半仓下料”,关键是要知道仓内的实时料位,料仓的料位为重锤料位计,输入数据为开关量,仅当料位到达高料位触碰到重锤时画面才显示“高料位”,无法得知料仓的实际料位,需要人工去现场实际测量。经过改进,将重锤料位计改为雷达料位计,输入数据为模拟量,通过PLC转换成工程量之后再组态到中央操作画面,以百分比的形式显示料仓的连续料位 [4] [5],程序及画面组态如图7所示。通过这种方式,操作人员无需去现场测量,并且可以根据实际料位合理的安排除尘粉进仓,避免冲料的同时减轻操作工的劳动强度。
4. 结论
电机电流自主化实现了破碎机的“高电流”限值由后台到HMI的转变,操作人员可根据物料的品种以及破碎机锤头的磨损情况对“高电流”数值进行更改,最大限度的延长振动给料机的运行时间,在破碎机的额定负载内得到最好的运行效果。
下料控制自动化实现了振动给料机“高电流”自动停机,低电流自动启动,同时具备手动/自动切换
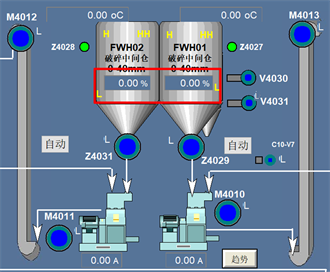
Figure 7. Analog quantity/engineering quantity conversion program and screen configuration
图7. 模拟量/工程量转换程序及画面组态
功能。在自动状态下,操作人员设定好破碎机的高/低电流限值,当破碎机电流到达低电流时,默认为破碎机空载,此时给料机自动开启向破碎机进料,当破碎机电流到达高电流时,默认为破碎机满载,此时给料机自动停止,待再次出现低电流时开启,如此往复。自动下料的应用大大减轻了操作人员的劳动强度,更因此避免了未及时开启破碎机所造成的空转,从而提高了破碎效率。
料仓料位连续化将原来料仓的高/低料位改为现在的连续料位并在HMI上显示,实现了料仓料位的实时监控。操作人员可根据料位合理的安排除尘粉进仓,避免了除尘粉堆积在底部造成的“冲料”现象。
经过本次改进,石灰破碎系统的自动化程度明显提高,有效的提高了破碎效率,降低了操作人员的劳动强度。但石灰破碎系统仍有进步空间,例如目前振动给料机为电动式,通过调整偏心块的角度来调振幅,需停机调整且时间过长,若改为电磁式可实现在线调振幅,搭配电流自主化和下料自动化可进一步提高破碎效率。