1. 前言
随着重型机械的大型化和自重轻量化,对低合金高强钢的强度级别要求越来越高,以有效提高工程机械的综合能力和使用经济性。调质态交货使用的屈服强度890 MPa级的Q890D高强钢,广泛应用于工程机械、重型车辆以及矿山液压支架等关键钢结构件。是目前全面工程化应用的最重要的高强钢之一。
宝武集团鄂城钢铁公司(简称鄂钢,下同)基于130 t转炉冶炼–LF炉外精炼–RH脱气处理–单流板坯连铸(最大宽度2200 mm)–4300 mm轧机轧制–调质处理流程生产Q890D厚板,钢板厚度范围10~50 mm,宽度范围2.4~3.6 m,均大于铸坯最大宽度,需要3~4道展宽道次,规模化生产后,批量出现钢板边部线状裂纹缺陷,以至于钢板轧制时必须预留切边余量,发现成品有线状缺陷后进行切边处理交货,严重影响了钢板的生产效率和成材率。
本文通过取样检测分析,确定线状裂纹缺陷产生的根源和机理,并提出针对行的优化措施,以使裂纹的发生率得到有效控制。
2. 线状缺陷基本情况
Q890D作为4300轧制产线产品中强度最高的品种,厚度范围为10~50 mm,钢板表面的线状裂纹缺陷发生率也最高,典型的线状裂纹缺陷宏观形貌如图1所示。
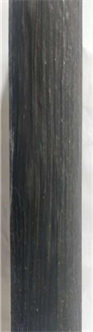
上表面Upper surface 下表面Bottom surface 侧面side
Figure 1. Edge linear defects and side morphology of Q890D plate
图1. Q890D钢板边部线状缺陷及侧面形貌
从图1看出,裂纹总体呈近直线型,分布于钢板两边,与钢板轧制方向平行,长度方向几乎贯穿钢板整个板面,裂纹基本未出现向两侧树枝状、龟裂状扩展的特征。实际中,轧制Q890D时,边部线状裂纹发生率达到40%以上,其中距离边部30 mm以上的发生率超过10%,距离边部10 mm以上的超过35%。
3. 取样检测及分析
从典型线状裂纹缺陷钢板的裂纹处取横向试样,镶嵌并打磨抛光后,通过QUANTA 400扫描电镜SEM结合EDAX能谱EDS进行微观形貌观察和典型区域和点位的成分分析,结果如图2~图5所示。
(a)
(b)
Figure 2. Linear crack morphology and oxidation dot on the upper surface of Q890D plate. (a) Overall morphology of crack on cross section; (b) Morphology of crack tail and oxidation dot on one side
图2. Q890D钢板上表面边部线状裂纹形貌与氧化圆点。(a) 裂纹横截面总体形貌;(b) 裂纹尾部形貌及一侧的氧化圆点
图2、图3中,上下表面的线状裂纹深度分别1.8 mm和0.8 mm。试样均从钢板宽度方向表面外侧向钢板中部的基体内延伸。裂纹尾端总体较圆钝,无明显的沿结晶扩张扩展,裂纹单侧有氧化圆点,但是氧化圆点分布基本无规律性。
(a)
(b)
Figure 3. Linear crack morphology and oxidation dot on the bottom surface of Q890D plate. (a) Overall morphology of crack on cross section; (b) Morphology of crack tail and oxidation dot on one side
图3. Q890D钢板下表面边部线状裂纹形貌与氧化圆点。(a) 裂纹横切面总体形貌;(b) 裂纹尾部形貌及一侧的氧化圆点

Figure 4. Oxidation and decarburization near the upper surface crack
图4. 上表面裂纹附近的氧化和脱碳特征
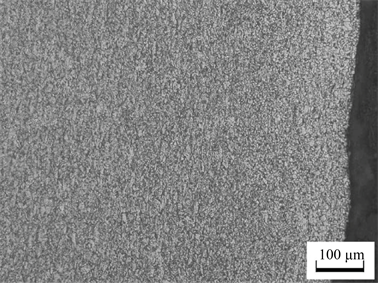
Figure 5. Microstructure characteristics near the bottom surface crack
图5. 下表面裂纹附近的组织特征
试样腐蚀后进行金相观察,图4所示的上表面裂纹附近氧化和脱碳特征较为明显,但图5中下表面裂纹处与钢基的组织基本一致,脱碳较为轻微。
4. 线状裂纹产生机理研究
4.1. 热模拟实验
钢板裂纹的来源主要为铸坯原生裂纹和轧制裂纹 [1],如果Q890D板坯已经出现边部裂纹缺陷,经加热后,裂纹将会出现扩展,在轧制过程中可能形成不同特征的裂纹,正常情况下,如果板坯进入加热炉前表面已经存在裂纹,在1200℃超过4小时的加热过程中,裂纹两边将产生非常严重的氧化圆点,图2和图3中裂纹单侧出现氧化圆点,且分布规律性不足,无法做出有效判断,因此,开展了热模拟实验,取典型边部线状裂纹试样,分切为尺寸均为30 × 50 × 50 mm的矩形块,放入无保护气体的型号为Thermo-T的厢式电阻加热炉内,加入至800℃、1000℃和1250℃分别保温30 min后取出,在空气中降至室温后制样,打磨抛光后,通过LEICA DM6000M金相显微镜进行金相分析,结果如图6所示。
(a) 800˚C
(b) 100˚C
(c) 1250˚C
Figure 6. Oxidation characteristics around cracks at different heating temperatures
图6. 不同加热温度条件下裂纹周围的氧化特征
在图6中,试样800℃及以上保温30 min后,裂纹两侧即出现密布的氧化圆点,且越靠近裂纹,氧化圆点越密集,粒径越大,裂纹内部镶嵌有大量的氧化物。对比图2和图3,很显然,虽然裂纹周围也有氧化圆点存在,但是均为单侧分布,且不具规律性,严重程度远不及图6(a)中的状态,加之裂纹从表面向钢基内部延伸具有明显的方向性,基本可以断定,线状裂纹的缺陷不是起源于铸坯的表面裂纹。
4.2. 机理分析
在基本排除线状裂纹起源于铸坯的表面裂纹之后,则转而分析其在轧制过程中的形成机理。相关文献中,将上述裂纹定义为黑线、边直裂等类型的裂纹缺陷 [2] [3] [4],总结起来其产生的原因可能包括以下几点:
1) 铸坯边角部温降太快,边角部金属变形能力严重低于中部区域,轧制过程中,特别是展宽轧制时,铸坯角部向表面的侧翻所形成折叠线。
2) 铸坯处加热炉高压水除鳞和轧制过程中除鳞导致边部温降过大,轧制时产生应力性裂纹;
3) 展宽轧制过程出现扣头问题。
而以上集中情况中,可连续稳定出现的,只能是第1)中情况,即铸坯边角部侧翻至钢板表面形成折叠线,其机理如图7所示。
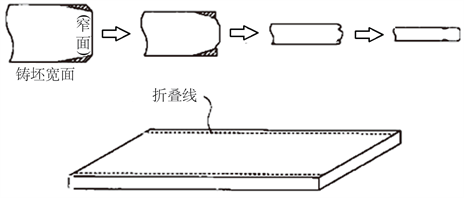
Figure 7. Schematic diagram of forming mechanism of edge folding line of plate
图7. 钢板边部折叠线形成机理示意图
而结合图2图3中裂纹向钢基延伸的方向特征,与图7中形成折叠线状裂纹的机理完全一致,即宽展轧制过程中,铸坯心部随轧制先部分凸出,二维散热、变形能力差的边角部后被推向钢板边部,边角线被压入钢基后形成线状裂纹,边角部倒向钢板边部,线状裂纹从表面向钢基扩展的方向,也是从钢板边部斜向板面中部,与原边角部向外倒的方向一致。
而由于线状裂纹两侧在形成前分别是铸坯窄面和初始钢板表面,二者温度明显不同,因此,二者被压至紧密接触时,裂纹两侧的氧化圆点分布情况不一致,与图2和图3的检验结果相照应。
总之,从本节的分析可以得出结论,Q890D钢板的边部线状缺陷来源于轧制环节,主要由铸坯边角部的折叠压入所致。
5. 优化措施及实施
基于前述分析,从铸坯组织均匀性、加热制度、轧制工艺等方面提出了控制边部线状裂纹的系列措施,主要包括:
1) 优化连铸二次冷却工艺,在保证冷却强度总体稳定的情况下,在铸坯矫直区,减小边部喷嘴的喷水量,从四组喷嘴喷水量平均分布降至边部与中部水量比30%~40%,增加铸坯不同区域的温度均匀性以及在冷却过程中的组织均匀性 [5]。
2) 优化板坯加热工艺,均热段温度由1200℃提高到1230℃,减小出炉板坯上下面温差,有效降低轧件上下面的变形抗力差别,从而缩小轧件上下面变形程度的差别,减小轧件边部的不均匀变形。
3) 通过增加坯料宽度,减小钢板宽展比,同时结合展宽比,同等条件下增加1~2展宽轧制道次,减小单道次的压下量,避免铸坯角部压入。
4) 使用倒角结晶器是解决钢板边部线装裂纹缺陷的根本途径,可在后续铸机改造升级过程中实施。
通过以上1~3条措施的实施,Q890D钢板边部线状缺陷的发生率降低至3%以下,且均分布于距离边部10 mm以内的范围,优化效果十分明显。
6. 结论
1) Q890D边部线状两侧无严重的、规律性分布的氧化圆点,结合裂纹从表面向钢基延伸的特征,可以确认该类裂纹起源于轧制过程的展宽环节。
2) 展宽过程中,温度较低、变性能力较差的铸坯边角部压入,是形成边部线状缺陷的直接原因。
3) 通过优化连铸二次冷却工艺、适当提高加热炉均热段温度并增加1~2个展宽道次,钢板边部线状缺陷可以得到有效控制。