1. 引言
钢中的硫元素和硫化物夹杂物会使钢的塑性降低,脆性增加,因此在通常情况下,硫元素是钢中的有害元素 [1],随着社会不断发展,各行各业对成品钢的要求逐渐提高,如轴承钢、管线钢及深冲钢要求钢中的含硫量要小于0.002%,油井管钢硫含量要小于0.005%,因此去除钢中的硫元素是十分必要的 [2]。
铁水预处理脱硫工艺是铁水进入炼钢炉前的脱硫预处理工艺 [3],又称为炉外脱硫,它能够有效降低铁水中的硫含量。KR (Kambara Reactor)铁水脱硫是目前广泛使用的一种铁水脱硫技术 [4],它是一种卷入型机械搅拌式脱硫法,是用一个外衬耐火材料的搅拌桨浸入铁水罐中,以一定速度旋转,搅动铁水,产生旋涡,将脱硫剂卷入铁水中,使两者充分反应,达到脱硫目的。尤其是近几年,KR法脱硫越来越受各大钢铁冶金企业的重视和关注。KR法在深脱硫和超深方面优势明显,同时在脱硫的稳定性方面也更具有优势,能够减少脱硫过程中的回硫现象 [5]。但在机械搅拌作用下,大部分脱硫剂进入铁水包后容易在中心强制涡流区发生团聚行为,导致脱硫剂利用率较低,成本较高 [6]。
已有大量学者针对桨叶的插入深度、转速等工艺参数展开研究 [7] [8] [9],曾彤等人 [7] 以武汉炼钢厂实际KR搅拌装置为原型,按比例设计出水模型实验装置,以聚氯乙烯塑料模拟脱硫剂,模拟不同搅拌器转速及插入深度对搅拌过程中脱硫剂卷入情况的影响。随着计算流体力学技术的快速发展,学者可以通过数值模拟技术对冶金容器内部的高温流体现象展开研究 [10] [11] [12] [13] [14],如悉超超等人 [10] 以宝钢现行搅拌器为原型,对其搅拌工艺优化进行模拟。李晶等人 [11] 利用k-ε模型以及多重参考系法对桨叶搅拌效果以及功率消耗进行了数值模拟,认为转速的提高只能在一定范围内提高搅拌的效率。张雪雯等人 [12] 基于PBM-MUSIG群体平衡模型,对局部含气率以及气泡尺寸的变化规律进行了阐述,并与实验进行了对比,结果的吻合性良好。
以上的研究成果有利于提高脱硫剂的使用效率,但大量脱硫剂在中心强制涡流区的团聚问题仍然存在。如果通过在高速旋转的桨叶底部和侧部喷吹氩气,将脱硫剂粉末送入铁水包内,有望减小脱硫剂在中心强制涡流区的团聚,从而提高脱硫剂的利用率。本文利用三维非稳态数值模型,研究了桨叶底部和侧部喷吹脱硫剂对铁水过程的影响,对铁水包内的氩气分布和脱硫剂运动进行分析,为工艺优化提供理论基础。
2. 数值模型
2.1. 几何模型
以宝钢KR搅拌装置及搅拌工艺方法为基础建立数值模型,其中铁水包结构如图1所示,所使用的搅拌桨型号如图2所示,其具体参数如表1所示。
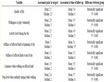
Table 1. Specific parameters of molten iron ladle
表1. 铁水包具体参数
2.2. 网格划分
图3为铁水包的三维网格图,其中旋转区域(黄色部分)包含桨叶。基于旋转坐标系进行求解,而外部区域则基于静止坐标系进行求解,这样的处理方式提高了整个系统的求解精度,优化了网格划分方式。由于静止区域结构化网格 + 旋转区域四面体网格的划分方式,在旋转区的网格质量往往并不会很好,而为了得到较优的结果需要大量的网格数量,而多面体网格相较于四面体网格数量只需要原来的1/3,计算时间也约为1/3,因此改为通过多面体网格进行网格划分。网格划分如图3所示,网格总数量在30万左右。
2.3. 数学模型建立
2.3.1. 模型假设条件
根据铁水包内钢液物性特征及其流动特点,做如下假设:
1) 铁水流动呈湍流流动,流体为不可压缩的粘性流体;
2) 设脱硫剂对流场无影响,其形状简化为球形;
3) 铁水流动对夹杂物的运动产生影响;
4) 脱硫剂的运动采用随机运动模型进行描述;
5) 脱硫剂初始速度与喷气速度一致;
2.3.2. 控制方程
连续性方程:
(1)
(2)
式中
为气相速度,
为液相速度。采用标准k-ε方程描述气液两相流动的湍流特性
动量方程:
(3)
(4)
(5)
式中,
为混合相的速度,m/s;p为压力,Pa;
为力的源项,N/m3;
为体积分数;
为密度,kg/m3;
为黏度,kg/(m∙s);
为重力加速度,m/s2;下标ℓ、g分别表示液相和气相。
采用标准k-ε模型模拟,湍动能k方程为:
(6)
湍动能耗散率
方程如下:
(7)
(8)
(9)
式中:
为湍流粘度,k-ε模型中常数
,
,
,
,
。
利用DPM模型追踪脱硫剂的运动过程,在每次迭代计算中,首先计算连续相的流场,然后结合流场结果求解每一个离散脱硫剂的受力情况,得到脱硫剂的加速度、速度,从而追踪每一个脱硫剂的运动情况,脱硫剂在流场中运动受力包括曳力、重力、浮力、虚拟质量力、压力梯度以及提升力,其控制方程主要有:
(10)
式中
为拖曳力,
为重力,
为浮力,
为虚拟质量力,
为压力梯度力,
为提升力。
2.3.3. 求解参数及边界条件
求解迭代压力–速度耦合使用SIMPLE算法,差分格式为一阶迎风格式,同时选用标准k-ε湍流模型。使用滑移网格模型求解KR机械搅拌器的旋转运动问题。滑移网格模型需要定义旋转区域和相邻静止区域的交界面,数据通过网格交界面进行传递。
通过速度入口模拟氩气喷吹,脱硫剂入口速度与喷气速度相同,其脱硫剂的粒径范围为0.05~0.5 mm。设壁面为无滑移壁面,脱硫剂碰撞壁面进行反弹,出口为压力出口,时间步长为0.005 s。搅拌桨转速为80 rpm。桨叶喷吹位置如图4所示,以桨叶底部半径为单位,桨叶底吹位置距离桨叶中心0.9 R (603 mm),侧吹喷嘴在桨叶高度一半的位置(500 mm),箭头表示喷吹方向。
3. 结果与讨论
本研究所使用的数学模型已在该课题组前期的研究工作中进行了详细的实验对比,验证了该模型的准确性 [15]。
图5为未喷入气体,搅拌稳定的流场情况。如图所示,桨叶搅拌使铁水从距离桨叶顶部1/3处流向壁面,部分铁水向上流动,部分铁水向下流动,形成明显的两个一上一下的涡流。可以看到整个铁水包流场在距离桨叶顶部1/3处存在明显的两个一上一下的涡流。
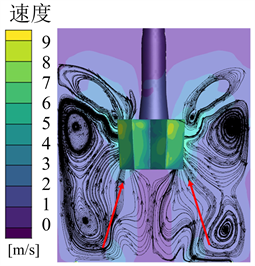
Figure 5. Velocity distribution of molten iron
图5. 铁水的速度分布
图6为流场稳定后,喷入氩气的运动轨迹,如图所示,气体从喷嘴喷出后,由于氩气密度远小于铁水密度,气体逐渐沿着搅拌轴上浮,如图6(b)与图6(c)所示,当气体上浮到了桨叶顶部位置时,受流场中拖曳力影响,气体开始向四周运动,最终如图6(d)所示,气泡在桨叶顶部形成气柱,包裹住桨叶顶部,随后上浮到液面。

Figure 6. Gas movement process. (a) Blowing argon 0.25 s; (b) Blowing argon 0.4 s; (c) Blowing argon 0.6 s; (d) Blowing argon 0.8 s
图6. 气体运动过程。(a) 喷吹氩气0.25 s;(b) 喷吹氩气0.4 s;(c) 喷吹氩气0.6 s;(d) 喷吹氩气0.8 s
3.1. 喷吹模式对流场的影响
图7为在不同喷吹模式下铁水包内的气体运动轨迹,当喷嘴布置在桨叶底部时,气体喷入铁水包后克服阻力做功,其动能快速消耗,气体向下运动距离较短,随后受中心负压区的压力影响,大部分气体沿着搅拌轴上浮。图8给出了不同喷吹条件下铁水的速度分布,如图所示,喷嘴位于桨叶底部时(图8(a)),当气体上浮到桨叶中间时,受拖曳力影响,气体在水平方向上向外运动,并逐渐螺旋上升直至液面。而喷嘴分布在桨叶侧面时,由于喷嘴面向铁水包壁面,氩气喷入铁水包后本身具有水平方向上的动能,因此桨叶侧吹相较于底吹,气体分布范围更广。
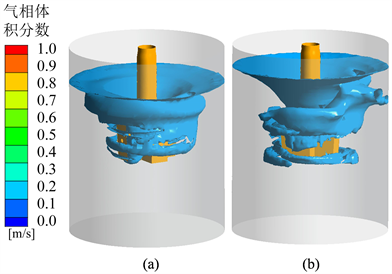
Figure 7. Gas trajectory. (a) Blade bottom blowing; (b) Blade side blowing
图7. 气体运动轨迹。(a) 桨叶底吹;(b) 桨叶侧吹
当喷嘴分布在桨叶底部时,由于气体是垂直向下喷射,气体在水平方向上并不具备动能,因此气体能够在水平上运动,主要是受流场中拖曳力的影响,气体通过与铁水交换能量,使气体能够向四周扩散,由于铁水与气体交换了能量,使得从桨叶流向壁面的铁水动能不足,无法在铁水包两侧形成较大的自由涡流区,因此在图8(a)中,铁水受气羽推动,在圈所示位置,铁水向上流动,破坏了两侧自由涡流区的结构,使得铁水拖曳脱硫剂进入铁水包底部的能力减弱,其底部弱流区约占铁水包1/3的区域。
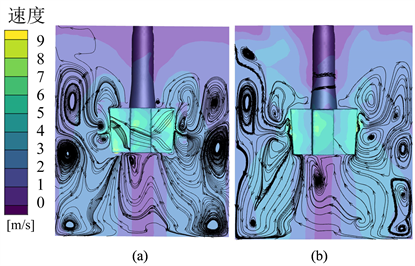
Figure 8. Velocity distribution of molten iron. (a) Blade bottom blowing; (b) Blade side blowing
图8. 铁水的速度分布。(a)桨叶底吹;(b)桨叶侧吹
当喷嘴分布在桨叶侧面时(图8(b)),喷嘴位置刚好是铁水从桨叶流向铁水包壁面的位置,从此处喷吹氩气,气羽能够进一步推动铁水向壁面流动,从而增大自由涡流区,减小底部弱流区,有利于提高脱硫效率。对比图8(a)与图8(b),喷嘴分布在桨叶侧面比在底面更有利于加大自由涡流区强度。
为了进一步对比两种喷吹模式对铁水包内流场的影响,模拟从液面添加示踪剂,所测混匀时间如表2所示,喷嘴分布在桨叶侧面相较于桨叶底面更有利于加强铁水包内铁水流动,其铁水混匀所需时间相较于桨叶底吹减少了13%。
3.2. 喷吹模式对脱硫剂运动的影响
图9为脱硫剂在铁水包内的运动轨迹,脱硫剂从桨叶底部喷入铁水包的运动轨迹如图9(a)所示,当喷嘴位于桨叶底部时,脱硫剂从桨叶底部喷入铁水包后,由于脱硫剂具有向下的动能,脱硫剂先向包底运动,但受浮力与铁水阻力的影响,脱硫剂运动距离并不长,随后开始做螺旋上升运动,并逐渐远离桨叶,在螺旋过程中,脱硫剂运动轨迹较为复杂,时浮时沉,碰撞较为激烈,团聚程度较为高。当脱硫剂运动到自由涡流区时,受拖曳力影响,脱硫剂逐渐向下运动,当脱硫剂运动到底部弱流区时,铁水向下的拖曳力不足,脱硫剂无法继续下沉。
脱硫剂从桨叶侧面喷入铁水包的运动轨迹如图9(b)所示,当喷嘴位于桨叶侧面时,脱硫剂喷入铁水包后立刻沿着液面做螺旋上升运动,并且运动范围逐渐扩大,随后被卷入自由涡流区,受拖曳力影响,脱硫剂看是螺旋下降,并逐步运动到底部弱流区。
对比图9(a)和图9(b),从桨叶底部喷吹脱硫剂虽然能使得脱硫剂先向下运动,但由于铁水与脱硫剂密度相差较大,脱硫剂向下运动的距离并不长,且由于底吹使得铁水包两侧自由涡流区结构被破坏,使得其大量脱硫剂无法运动到底部弱流区,从而聚集在铁水包顶部,脱硫剂运动轨迹较为复杂,碰撞凝并的概率较大。
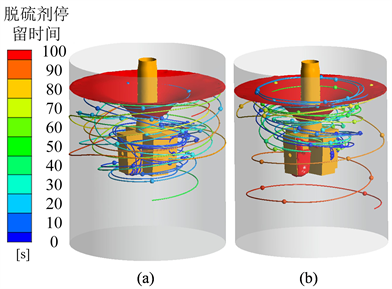
Figure 9. Movement trajectory of desulfurizer. (a) Blade bottom blowing; (b) Blade side blowing
图9. 脱硫剂运动轨迹。(a) 桨叶底吹;(b) 桨叶侧吹
图10为两种喷吹位置的脱硫剂分布,从底部喷吹脱硫剂使得大量脱硫剂聚集在铁水包上部,故在桨叶顶部脱硫剂粒径较大,而从桨叶侧面喷入脱硫剂使得脱硫剂运动范围更广,碰撞较少,从而减小了脱硫剂凝并程度。
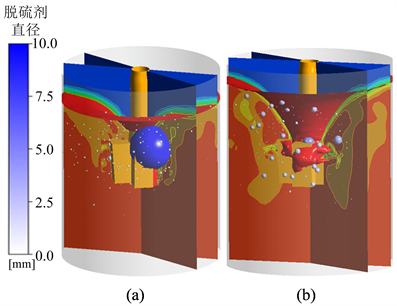
Figure 10. Distribution of desulfurizer. (a) Blade bottom blowing; (b) Blade side blowing
图10. 脱硫剂分布。(a) 桨叶底吹;(b) 桨叶侧吹
4. 结论
KR搅拌法在深脱硫和超深脱硫方面具有较大的优势,但在中心强制涡流区,脱硫剂团聚程度较高,导致脱硫剂使用成本增加,为了避免脱硫剂聚集在中心强制涡流区,本研究对桨叶喷吹氩气送入脱硫剂展开研究,对比了从桨叶底部及侧面喷吹两种模式,现得到以下结论:
1) 桨叶喷吹氩气,气体上浮会推动铁水向上流动,从而对铁水包两侧的自由涡流区造成影响。
2) 桨叶侧吹相较于底吹,其气羽能够推动铁水向壁面流动,从而增大其自由涡流区强度,减小底部弱流区,其铁水混匀时间减少了13%。
3) 桨叶侧吹增大自由涡流区强度有利于更多脱硫剂进入底部弱流区,扩大脱硫剂的运动范围,降低其凝并程度。