1. 引言
钢铁行业作为能源消耗和碳排放大户,占全国碳排放总量的15%~18%。因此,为实现碳达峰碳中和的目标,推动钢铁行业的制度改革与科技创新迫在眉睫。目前,国内以长流程为主,占90%左右,本文将基于数字仿真模型优化钢铁长流程碳排放。在满足当代钢铁行业生产需求的基础上,以钢铁行业长流程的几个主要工序为基础进行改进,实现低碳减排任务。曲余玲、张琦等分别为钢铁行业的低碳减排提出了宝贵的意见 [1] [2]。当下,钢铁行业内部主要工序的能源利用效率低是钢铁行业低碳减排的主要问题,由于钢铁行业内缺乏低碳技术,成熟的低碳生产工艺未得到广泛应用,增加了碳排放。
本文将从以下三个方面研究:分工艺流程构建长流程碳排放数字化仿真模型,通过计算机程序求解模型满意解,改善各工序原料配比,实现碳减排;构建长流程资源循环利用体系,以桑基图为基础,用物质流表示内部资源的关系,改善长流程内部工序联系,实现碳减排;结合长流程成本约束限制、工序条件限制,同时运用新型低碳科技,改进钢铁行业的工艺,以降低碳排放量。
2. 碳排放计算方法分析
根据中国统计局公布的数据,2020年内,中国粗钢产量达到10.53亿吨,同比增长5.2%,钢铁行业能耗约占全国能耗的8.9%。作为主要的碳排放行业,其在生产过程中存在高能耗、高污染、高排放等问题,需要对其内部工序进行工艺优化,提高能源利用率,推动钢铁行业高质量发展。而目前钢铁行业主流生产方式分为高炉–转炉(BF-BOF)路线(图1)与电弧炉(EAF)路线(图2),本文将以长流程生产方式为例进行分析,对现钢铁行业长流程生产方案提出改良优化方案。如图1所示,将钢铁行业内部工序分为焦化、烧结/球团、高炉、转炉、连铸、轧钢六大工序。通过对各工序碳排放的优化分析,利用图论提出整体的长流程生产工艺优化方案,助力钢铁行业减碳提质。
2.1. 钢铁行业长流程工序碳排放边界分析
如图3所示,各工序物质的流向已用箭头标出。据此,工序模型碳素流主要影响因子便可确定,进而根据主要影响因子成分的不同,确定各工序模型的变量。
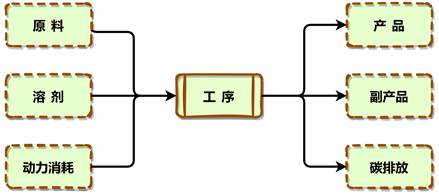
Figure 3. Process model boundary determination
图3. 工序模型边界确定
2.2. 确定碳排放因子
碳排放因子是碳排放计算公式的关键,其计算方法取决于物质的含碳种类 [3] [4] [5]。根据物质含碳种类的不同,本文将碳排放因子分为三类:直接碳排放因子、间接碳排放因子与抵扣碳排放因子。
直接碳排放因子计算公式如下:
式中,下标j表示第j种原料;
为原料购入量;
是基于热值的排放因子;
是热值;
为氧化率;
为原料直接碳排放因子。
间接碳排放因子计算公式如下:
式中,
为
生产时动力时消耗原料燃烧产生碳排放量;
为动力终端所消耗利用效率。
抵扣碳排放因子计算公式如下:
式中,
为原料所含碳元素比例;
为碳元素转为二氧化碳的分子质量转化系数。
2.3. 碳排放计算公式的优化
根据2.2节中碳排放因子的分类,优化现有各工序碳排放计算公式如下:
式中,
表示为某种原料,
表示某种原料含碳部分的碳排放量,单位tCO2,此
为直接碳排放因子;
表示非含碳能源的碳排放量,单位tCO2,此
为间接碳排放因子;
表示产品、副产品等的碳排放量,单位tCO2,此
为抵扣碳排放因子 [3]。
得到各工序对应的优化碳排放计算公式后,需要根据钢铁行业的碳素流图确定与碳排放因子相关的物质。所谓“碳素流图”,即桑基图的一种表现形式,通过观察此图,可得到含碳物质在各个工序间的流向,从而划分出碳输入物质和碳输出物质,再根据物质的类型判断物质的碳排放因子所属的种类。
优化前的碳素流图绘制如图4所示。
随着钢铁行业不断发展,促进钢铁行业碳达峰、碳中和的低碳科技也在不断提高,通过搜集国家发布的节能低碳技术目录及其他相关人员研究 [2],以及对模型的试算,本文将在图4基础上,根据下面表1中的技术,对相应工序模型进行优化,使低碳科技应用到钢铁长流程生产数字仿真模型中。
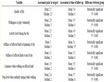
Table 1. Examples of various processes of low-carbon technology
表1. 低碳技术各工序采用举例
3. 钢铁行业碳减排规划模型
3.1. 模型理论与求解
以钢铁行业长流程工艺的能源结构、内部关系、低碳科技应用条件等方面为约束对钢铁行业进行优化,旨在求得工序相应最低碳排放量。根据此最优解特性,选择使用规划模型构建工序模型。根据工序产品构建的碳素流网络,选取合适产品生产线路,求得最佳碳排放路径。
钢铁行业因工序产品多样,由工序总碳排放量每新加一道工序,使得该钢铁行业模型碳排放量在现加工序中仍保持最小碳排放量。将未在总模型内的工序不断加入到总模型内,进而选取出关于碳排放量的最小生成树,得到碳排放量最小、总体产量满意的钢铁行业长流程生产模型。
3.2. 数字仿真模型建立
根据钢铁长流程生产的客观规律,并注意到部分流程副产品可循环利用的特性,本文考虑从以下方面完成各工序模型的约束条件建立:
1) 成本上下限约束;
2) 原料供应量约束;
3) 元素守恒约束;
4) 反应元素供应量约束;
5) 物料守恒约束;
6) 工序产量约束;
7) 工序副产品产量约束(焦炉煤气、高炉煤气等);
8) 可循环利用副产品的守恒约束(焦炉煤气、高炉煤气等)。
下面以高炉工序模型建立为例:(其他流程数字仿真模型的约束条件,均来源于上面提到的八个方面,这里不再赘述)。
高炉工序规划模型
根据钢铁行业各个工序能耗的比较分析,高炉炼铁工序能耗约占到总体系统能耗70%左右,高炉炼铁是钢铁行业减碳的重点 [5]。
高炉工序变量确定:
根据高炉的原料数据、工艺和产品质量参数限制决定出对高炉碳排放具有影响的变量 [6],见表2。假定高炉生产出铁水量为1吨为结果进行建模。
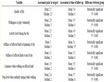
Table 2. Variables of blast furnace process model
表2. 高炉工序模型变量
高炉工序目标函数确定:
为达成钢铁行业碳减排目标,将高炉工序模型用CO2排放量作为目标函数,通过规划模型求得最小CO2排放量。根据上述条件,列出高炉工序的目标函数:
式中,
为高炉工序的CO2排放量;
表示为
变量的碳排放因子。
高炉工序约束条件确定 [7]:
1) 根据高炉炉渣的碱度,要求生铁的二元碱度在一定范围内,符合生铁的生产工艺:
式中,
表示二元碱度的下限;
表示二元碱度的上限;
为Si元素转化SiO2成分转化系数。
2) 高炉炉渣中对MgO含量也具有含量要求:
式中,
表示MgO含量上限;
表示MgO含量上限。
3) 高炉铁水对各个元素含量要求:
式中,
对铁水中Si含量要求下限,
对铁水中Si含量要求上限;
对铁水中P含量要求上限;
对铁水中S含量要求上限。
4) 高炉原料对矿石分量要求要求:
式中,
对矿石原料中烧结矿含量要求下限,
对矿石原料中烧结矿含量要求上限;
对矿石原料中球团矿含量要求下限,
对矿石原料中球团矿含量要求上限;
对矿石原料中铁矿含量要求下限,
对矿石原料中铁矿含量要求上限;
对矿石原料中焦炭含量要求下限,
对焦炭原料中铁矿含量要求上限。
5) 高炉炉渣生成约束,高炉炉渣主要由原料中矿石生成,根据炉渣的主要成分,通过原料矿石计算得出:
式中,
为铁水转化炉渣S元素系数;
为铁水转化炉渣Mn元素系数;
为铁水转化炉渣SiO2元素系数。
6) 高炉煤气生产平衡约束:
式中,
为C元素转化高炉煤气成分系数;
为H2转化高炉煤气成分系数;
为N2转化高炉煤气成分系数。
7) 高炉成本约束:
式中,
为
原料的价格转化系数;
为高炉工序成本上限。
3.3. 系统模型简述
钢铁行业作为高能耗、高污染的碳排放大户。其行业生产流程又分为高炉–转炉长流程与电炉短流程生产方式,两者碳排放量之间相差巨大,新兴短流程较之长流程能耗低,碳排放量少,但其生产方式在国内较为少见。因此,优化现有钢铁行业长流程生产模型是很有必要的。
钢铁行业长流程生产总体优化模型总目标函数如下:
式中,
为系统模型碳排放量;
为工序模型碳排放量;
为钢铁碳排放转化系数。
总模型以六大基本工序为基础,由各个工序规划模型结合得到,完成对长流程工艺的优化。
在满足各工序模型工艺要求、成本要求、产品产量等约束的条件下,以各工序原有生产技术为基础,根据最优化路径算法,适当选用符合生产实际的新型低碳科技,使钢铁长流程生产碳减排更进一步。
4. 实例分析
以国内某钢铁厂长流程生产数据为模型输入,利用Python编程语言的相关科学计算库,实现模型并求出模型满意解。最后将优化结果与该厂实际生产情况进行对比,以验证模型的优化效果;并对满意解进行数据可视化分析,为该厂的长流程工艺提供改进意见。
4.1. 焦化工序碳排放模型优化结果
结合某焦化厂生产工艺条件,将相关工艺参数代入焦化工序碳减排模型。根据焦化厂生产情况得出焦化工序优化结果,由表3表示。
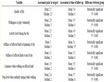
Table 3. Carbon flow result of each unit product in coking process
表3. 焦化工序各单位产品碳流结果
经过上述模型优化结果计算得知焦化工序碳排放量为:487.04 kg CO2。相比与一般生产工序吨工序碳排放结果,减少碳排放量93.86 kg CO2。
优化结果与该厂实际生产相比:
1) 肥煤用量减少约50%;
2) 新增转炉煤气用量278.94 kg。
综上所述,焦化工序碳排放主要源头在于用煤种类选择上。
因此,对于焦化工序碳减排方案重点应在煤炭等化石燃料的合理搭配利用,同时综合使用煤气回收技术。
4.2. 烧结/球团工序碳排放模型优化结果
根据现烧结厂相关技术要求,结合烧结模型,解出烧结/球团模型优化结果,具体情况如表4所示。
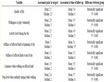
Table 4. Carbon flow result of each unit product in Sintering/pelletizing process
表4. 烧结/球团工序各单位产品碳流结果
由上述情况计算求得现烧结碳减排优化结果为:152.67 kg CO2。相比与传统烧结厂,模型优化结果减少碳排放量27.27 kg CO2。
根据上述结果表示,烧结工序能源消耗主要在于原矿配料选择情况上。
因此该厂可以通过选择合适原矿、寻找合适的原料配比解决烧结工序碳排放较多的问题。
4.3. 转炉工序碳排放模型优化结果
将转炉相关工艺参数,带入转炉工序优化模型,求得物质用料情况如表5。
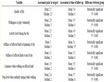
Table 5. Carbon flow result of each unit product in converter process
表5. 转炉工序各单位产品碳流结果
在转炉工序优化模型求得优化结果为:191.67 kg CO2。与一般转炉工序碳排放量结果相比,碳排放量减少36.32 kg CO2。
优化结果与该厂实际生产结果相比:
1) 新增高炉煤气输入量53.57 m3;
2) 新增焦炉煤气输入量9.37 m3。
综上所述,转炉工序的碳减排方案主要还是在原有技术的基础上,适当引进煤气回收技术、余热回收技术等的融合方案。
新型融合方案的实施会给转炉工序的节能减排方面带来较明显的成效。
4.4. 该钢铁厂总体碳排放模型优化结果
根据上述仿真模型求得,该厂最优吨钢碳排放量为1583.40 kg,并绘制各工序碳排放量百分比对比图,如图5所示。
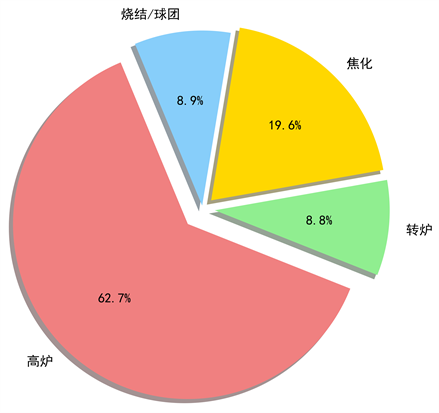
Figure 5. Comparison chart of carbon emission percentage of each process
图5. 各工序碳排放量百分比对比图
以碳素流图为渠道,对钢铁长流程原有方案和本文提出的基于数字仿真优化方案进行对比,如下:
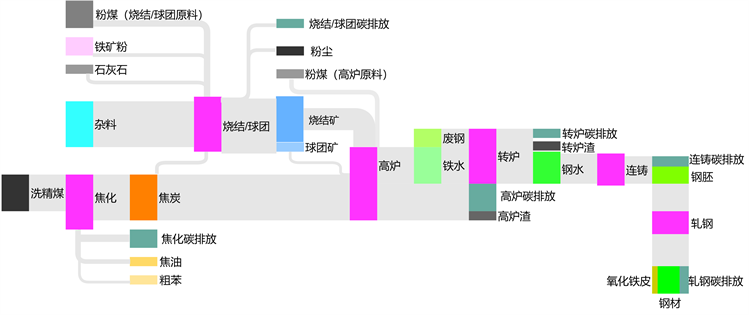
Figure 6. Carbon flow diagram of original scheme
图6. 原有方案碳素流图
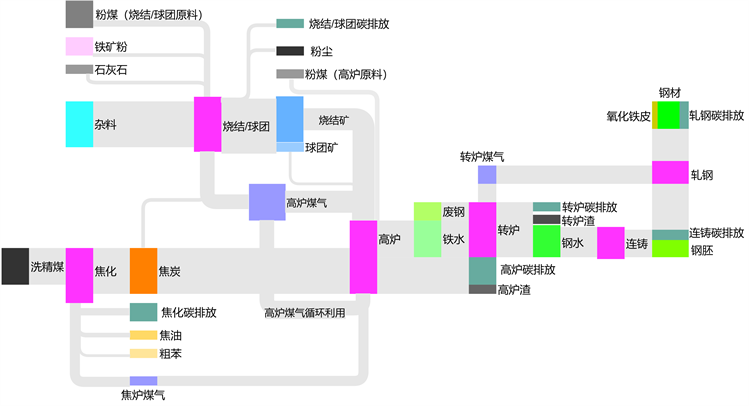
Figure 7. Optimization results of digital simulation model
图7. 数字仿真模型优化结果
由图5、图6、图7结合4.1~4.3节的结果分析得到:由于钢铁行业长流程工艺中高炉工艺的碳排放量占比最大,钢铁行业应将低碳减排的重心放在高炉工序上,多引入成熟的新型低碳科技,同时优化生产过程中的能源供给结构。另外,各工序的具体碳减排方案可参考4.1~4.3节。
5. 总结
本文基于数字仿真模型,将钢铁行业长流程生产工艺数字化,利用运筹学中图模型的最小生成树理论进行建模,再考虑引进钢铁行业较成熟的低碳技术优化原有模型,最后基于最小生成树算法Prim算法的Python编程实现,辅以国内某钢铁企业的生产数据,求得该钢铁企业各个工序碳排放数字化仿真模型的满意解。
本文对满意解进行了不同形式的数据可视化,以便进行结果分析。
分析可得,该钢铁企业减少碳排放量的方法概括如下:在图模型满意解的指导下,减少原料消耗量、增加物料重复利用(如:钢铁行业系统中煤气回收利用),使用新型低碳科技减少碳排放。
根据优化结果,对该钢铁企业提出以下几点建议:
1) 增加废钢使用量,将废钢利用到转炉炼钢当中,减少相应铁矿石的能源消耗。重复利用废料,仿照电炉短流程生产工艺,增加废钢使用比重,会有效减少钢铁行业长流程工艺的能源消耗与碳排放量。
2) 优化钢铁工业结构,改进钢铁长流程生产结构,需要从各个工序原料使用量及配比、新兴低碳科技使用等方面进行优化,进而为钢铁长流程生产的各个工序提供优化方案。
备注:
本文提出的模型主要基于一般性钢铁长流程生产理论建立,实际应用时还需根据实际情况,做适当修改。
致谢
本文是在华北电力大学(保定)数理系刘明浩老师精心指导和大力支持下完成的。他渊博的知识、开阔的视野和敏锐的思维给了我深深的启迪。
最后,再次对关心、帮助我的老师和同学表示衷心的感谢。