1. 前言
激光束的强度具有高斯分布,光强在中轴处最大,并向外围递减,激光光束具有向轴线自动汇聚的特性,光束直径可达到5 × 10−6 m,对完成微小、复杂部件的精细化焊接具有相当重要的优势,因此激光焊接技术广泛应用于工业、军用等领域,研究非线性路径焊接激光焊接技术就变得尤为重要。
何林基 [1] 考虑激光深熔焊过程中存在对流、辐射、热传导等传热过程以及蒸汽反冲作用力,表面张力,热浮力等力学过程,采用移动旋转高斯体热源来简化焊接的热过程,使用VOF方法跟踪自由界面,通过焓孔隙法实现焊接过程的凝固熔化,同时采用连续表面张力模型将蒸汽反冲作用力转化为在一定厚度上连续的作用力,建立数学模型,获得了奥氏体不锈钢深熔焊接过程中动态熔池的温度场以及流场分布,得到了与试验结果一致的模型;夏胜全 [2] 考虑熔池蒸气反冲压力、表面张力、热浮力等力学因素和熔池内、外部的对流、辐射等热学过程,采用沿深度方向衰减的旋转高斯体热源简化熔池对激光的吸收,采用流体体积法追踪气/液界面,采用液相体积分数法和焓–孔隙度法分别处理熔化凝固潜热及液–固糊状区的动量损失,建立了激光深熔焊接熔池的三维瞬态模型,计算得到的熔池形状和焊缝横截面的试验结果基本吻合;史平安 [3] 采用Particle Level Set方法和有限差分模型的光线追踪法来描述小孔对激光能量的吸收作用,建立了描述激光深熔焊接过程中熔池动态行为和小孔瞬态演化行为的三维数值模型,研究了小孔动态演化的3个阶段。上述研究均未探讨非线性路径对激光焊接的影响,鉴于此,本文通过C语言编译UDF,建立以正弦函数为激光束移动路径的旋转高斯曲面体热源模型,实现了用Fluent软件进行非线性路径激光焊接温度场和熔池流动数值模拟,能够在节约大量人力、物力、财力的基础上,实现重复多次、高效率、高精度的实验,进一步掌握非线性路径激光焊接过程的原理和影响因素,发挥非线性路径激光焊接技术的优势。
2. 热源模型及边界条件
2.1. 正弦修正移动高斯曲面体热源模型
本文中为更好的模拟激光焊接熔池“钉头”形状,选择的热源是高斯曲面体热源模型,修正的热源模型沿几何模型的Z轴方向移动,同时热源以一定的幅度沿X轴方向正弦摆动,最终实现热源沿正弦曲线移动,如图1所示:
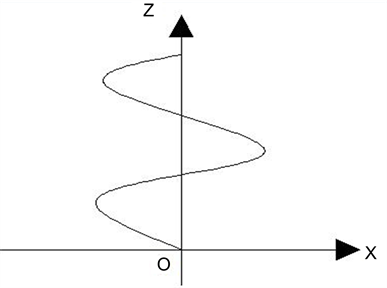
Figure 1. Schematic diagram of the moving trajectory of the heat source model of the sine-modified moving Gaussian surface body
图1. 正弦修正移动高斯曲面体热源模型移动轨迹示意图
本文中的正弦修正移动高斯曲面体热源模型 [4],是将正弦曲线的运动规律拟合在双椭球热源上,经C语言编译,通过user-defined functions接口实现热源在Fluent软件中移动,其数学表达式为:
其中a是有效系数;D是热源左右摆动的幅度值;e是热源左右摆动频率的1/2;t是热源移动的时间。上式可通过调整D、e的参数可以改变热源的正弦曲线运动轨迹,从而改变焊缝的形状。
正弦修正移动高斯曲面体热源模型中的参数是在多次模拟中得出的经验数值,本文中有效吸收系数a = 0.5,热源的摆动幅值D = 0.005 m,热源摆动频率的一半e = 0.5。
2.2. 边界条件
实现熔池流体流动模拟是在如下假设的前提下进行的:
1) 熔池内部液体为牛顿、不可压缩流体;
2) 熔池内部流体的流动为层流;
3) 熔池的表面是平坦的;
4) 工件的初始温度是300 K;
5) 浮力由材料密度变化来控制;
6) 焊接模型中保护气面,采用“mixture”边界条件,这种边界条件是氩气热对流和辐射的混合,速度边界条件设置为静止,氩气对流换热系数的数值已经算出为55.79 W/(m2·K),热辐射率0.56 [5];工件的left面、right面、铜板底面及侧面、不锈钢板焊缝底面都设置为空气面,同样设置为“mixture”,通常空气的对流系数为5~30 W/(m−2·K−1)。空气的换热系数取15 W/(m−2·K−1),辐射系数0.56 [5];工件的back面为恒温面,设置初始温度为300 K,速度为静止的边界条件。不锈钢板与铜板的接触面是耦合面,其边界条件设置为耦合的边界条件。
3. 数值模拟与分析
文中对利用正弦修正移动高斯曲面体热源模型模拟激光焊接过程,焊件尺寸40 × 20 × 10 mm,网格类型采用规则的六面体网格,尺寸为0.3 × 0.3 × 0.5 mm,焊接速度为1 mm/s,T表示正弦曲线周期,分析一个正弦周期内温度场变化规律。
3.1. 温度场
当激光束接触到工件时,熔池温度迅速升高,金属开始熔化,熔池开始形成,当焊接时间达到0.5 s时,峰值温度迅速升高至2220 K,同时熔池内部熔融金属开始转动,形成两个流动方向相反的涡流,此时涡流峰值流速达到0.0118 m/s,这是由于热源中心,熔池温度最高,使得中心区域的金属熔化,金属等离子蒸汽产生的反冲作用力和表面张力的作用使得金属液体由小孔内向外流动,同时将热量沿厚度方向传递;随焊接路径正弦变化,熔池温度逐渐升高至2390 K,峰值流速升高至0.0199 m/s,如图2所示。说明:熔池在形成初期,其内部流体流速增加,流动加剧,流速和温度同时达到峰值,最高和最低流速差值为0.0081 m/s,激光焊接路径变化对流速的影响处于mm/s的数量级。
(a)
(b)
(c)
Figure 2. Eddy current flow state of molten pool at t = 0.5 s and changes of molten pool temperature and flow rate during the whole welding process
图2. t = 0.5 s时熔池涡流流动状态及整个焊接过程熔池温度和流速变化
激光焊接过程随焊接路径的正弦变化,熔池峰值温度和峰值速度变化也表现出了类似“正弦曲线”的形状,如图2所示,峰值流速表现出与峰值温度“同增同减”的变化趋势;焊接过程经历到2 s~2.5 s时,熔池峰值温度进入“平台期”,此时峰值温度不再变化,峰值流速的差值也仅为0.0006 m/s,说明:激光焊接路径变化时,焊接过程存在准稳态的过程,但准稳态焊接过程很容易受焊接路径的变化发生改变。
3.2. 温度场和流速周期性
随着正弦焊接路径激光焊接过程的进行,在0.5 s~1.0 s~1.5 s时间范围内,熔池的峰值温度变化2220~2350~2390 K,峰值流速变化0.0118~0.0185~0.0199 m/s;在2.5 s~3.0 s~3.5 s时间范围内,熔池的峰值温度变化2210~2350~2390 K,熔池峰值流速变化0.0119~0.0179~0.0198 m/s,如图2所示,两个时间段,熔池峰值温度和流速近似表现出了周期性,这是由于随着激光焊接进行时,焊接路径变化,熔池内产生的等离子体(或金属蒸气)对激光的屏蔽和散射作用减弱,熔池吸热增加,温度上升,由于焊接路径的周期性变化,致使峰值温度和流速也表面出周期性。表明:激光焊接过程中,当焊接路径存在周期性变化时,熔池峰值流速和峰值温度也会表现出周期性。
3.3. 熔池形状和静压力
非线性焊接路径激光焊接过程熔池形状近似为“钉头形状”,熔池顶面,内部压力高于外部,最高达到4.64 Pa,熔池底面,压力数值为“-”,负号说明熔池外部压力高于内部,最高到49.2 Pa,随焊接过程的进行,熔池顶面压力逐渐减小,顶面压力逐渐增加,但总体熔池底面压力高于表面压力,如图3所示,这是由于在焊接开始阶段,金属开始熔化、蒸发产生等离子体,由此形成的向下的蒸汽反冲力直接作用于熔化的金属上,流动的金属液体将热能带到了熔池的底部,使得熔池在深度方向进一步拓展,已达到反冲力、表面张力等作用力下的熔池动态平衡过程。
(a)
(b)
(c)
Figure 3. The shape of the molten pool at t = 0.5 s and the changes of the static pressure on the top and bottom surfaces of the molten pool during the whole welding process
图3. t = 0.5 s时熔池形状及整个焊接过程熔池顶面和底面静压力变化
4. 结论
1) 激光焊接路径变化对流速的影响处于mm/s的数量级;
2) 激光焊接路径变化时,焊接过程存在准稳态的过程,但准稳态焊接过程很容易受焊接路径的变化发生改变;
3) 当激光焊接路径存在周期性变化时,熔池峰值流速和峰值温度也会表现出周期性;
4) 非线性焊接路径激光焊接过程熔池形状近似为“钉头形状”,熔池底面压力高于表面压力。