1. 芬顿技术简介
在1894年,由法国科学家H.J.H. Fenton发现了Fe2+/H2O2的混合试剂具有降解多种有机污染物的能力,并将其命名为Fenton (芬顿)试剂 [1] [2] [3]。芬顿反应是指二价铁离子与双氧水反应生成具有强氧化能力的
,
与大分子有机物(R)反应使其分解为小分子,
与小分子有机物(r)进一步反应矿化成CO2和H2O,从而高效去除有机污染物。近年来,科学家们踊跃探索芬顿反应的机理,得出了典型的结论,我们将其反应主要的机理结论归纳为如下公式:
(1-1)
由公式1-1可知,Fe(II)可以和H2O2相互反应生成羟基自由基用来降解有机污染物。
(1-2)
(1-3)
其中Fe2+可再生,其再生公式如1-2所示:
(1-4)
由上述可知,传统的均相芬顿技术催化效率非常高,操作也简单,因此在实际废水处理中被广泛使用,但是在这个过程中,由于公式1-4的反应使得体系中的H2O2被消耗而未能生成具有强氧化能力的
,导致H2O2的有效利用率降低 [4]。且大量铁盐的投加会导致后续铁盐的回收非常困难,反应后生成的大量含铁污泥会严重污染环境 [5]。而固体催化剂相对于可溶性的铁离子,具有稳定性高和可回收等特点,从而有效避免了铁离子的溶出和二次污染,这些技术被称为非均相芬顿技术,正成为业界热点。
2. 复合非均相芬顿技术
非均相芬顿技术在芬顿技术的基础上解决了铁离子溶出导致的二次污染问题,但在实际应用中还存在一些缺点,尤其Fe3+向Fe2+的转化效率比较低。由公式1-1和1-4可知,Fe(II)向Fe(III)的转化速率高达76 M/s,但是由Fe(III)生成Fe(II)的速率却只有0.001~0.1 M/s,这导致亚铁离子的利用率十分有限,在一定程度上限制了非均相芬顿技术的应用。为了加快反应中Fe(III)向Fe(II)的转化,研究者们希望通过外加的能量能够促使Fe(II)与Fe(III)的循环。为此有学者提出了复合芬顿技术:将光催化剂与芬顿催化剂复合,通过复合芬顿技术合成的复合非均相光芬顿催化剂能够协同光催化反应和芬顿反应,能够显著提高催化剂对太阳光或者可见光的利用效率,从而提高催化活性。
Zhu [6] 等人制备了新型的非均相光芬顿催化剂Ag/AgBr/水铁矿,这种催化剂是将半导体等离子体光催化剂的光生成电子引入异质芬顿催化剂中,显著提高了降解污染物的效率,在最优条件下,1 h内可实现对双酚A (BPA)的100%降解,且在中性pH下也表现出相对较高的光芬顿反应活性,催化剂Ag/AgBr/水铁矿光芬顿降解BPA机理如图1。
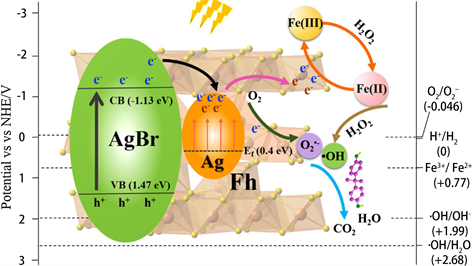
Figure 1. Possible photo-Fenton catalytic mechanism
图1. 可能的光芬顿催化机理
Miao [7] 等人合成了一系列掺杂铁的g-C3N4化合物(Fe-g-C3N4),并通过控制温度将Fe-g-C3N4热解分裂为均匀分散的多层结构,由于铁的掺杂、独特的层状结构和中孔特性,催化剂在非均相光芬顿反应体系中的催化活性得到了显著提高,对罗丹明B (RhB)的去除效率达到100%,且矿化率得到提高,Fe-g-C3N4光芬顿降解RhB的机理如图2。
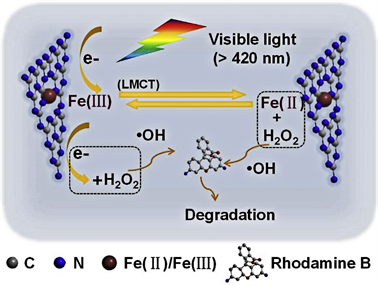
Figure 2. Reaction mechanisms of Fe-g-C3N4 catalyzed Fenton-like and photo-Fenton-like reactions
图2. Fe-g-C3N4催化芬顿反应和光芬顿反应的机理
Xie [8] 等人通过真空过滤法将光芬顿催化剂M88A插入石墨烯纳米片中,不仅可以调节石墨烯纳米通道的结构,也赋予其光芬顿催化活性,成功制备GO/M88A膜,该膜被直接用作非均相光芬顿催化剂降解污染物时具有相对高的降解效率MB (98.81%)和BPA (97.27%)。
3. 非均相芬顿技术及其催化剂的选择
复合非均相芬顿技术中,外加光源构成的非均相光芬顿技术因其操作简单,对环境污染小等优点而被研究者广泛关注。因为光能在自然界中是比较普遍存在的,并且目前大部分研究都倾向于利用可见光作为光源,因为在到达地球的太阳辐射光中,可见光的比例占到了43%左右。因此为了能够使催化剂有效吸收可见光以及加速Fe2+与Fe3+的相互转化,我们需从材料的改进及研究新材料方面进行考虑。
在非均相光芬顿体系中,催化剂的孔径尺寸和表面特性对有机物降解的矿化率、脱色率以及反应的动力学速度都有重要影响 [9]。由此可见,催化剂载体的选择十分重要,总的来说,非均相光芬顿催化剂载体的选择应该从以下几点出发考虑:一,载体的加入能否提高催化剂的稳定性;二,载体的加入能否实现催化剂的循环使用;三,载体的加入能否增加催化剂与目标污染物之间的接触面积。
4. 纳米磁性颗粒及其改性应用
磁性纳米颗粒是一种兼具纳米材料与磁性材料特性特质的颗粒,主要是由金属元素如Fe,Co,Ni,Mn等所组成的氧化物及其复合结构 [10]。磁性纳米颗粒种类繁多,其中纳米四氧化三铁(Fe3O4)因具有饱和磁化强度高、表面可修饰性、生物相容性等优点在催化领域被广泛使用 [11] [12] [13]。
磁性纳米Fe3O4作为非均相芬顿催化剂已经广泛应用于难生化降解的废水处理中。磁性纳米Fe3O4不仅可催化降解废水中的有机物,而且在磁性环境中还可以回收重复利用。计宏益等 [14] 采用前驱体法以钛白副产品为原料制备了Fe3O4 (Fe3O4-PR),并将其作为催化剂催化H2O2降解活性艳红X-3B。实验结果表明Fe3O4-PR具有良好的催化活性和稳定性。
但是Fe3O4颗粒暴露在空气中极容易被氧化而失去磁性;此外,Fe3O4在使用过程中容易发生团聚从而降低活性,这些缺点在一定程度上限制了Fe3O4的应用。
为了减少其团聚或者氧化等缺陷所带来的损失,研究者们尝试对其进行改善来增加颗粒的稳定性。例如采用不同的方法对纳米Fe3O4颗粒的表面进行修饰,包括高分子聚合物修饰,有机小分子修饰和无机纳米材料修饰等,以得到功能修饰性的纳米Fe3O4颗粒 [15],这些改性颗粒同时具备的良好纳米磁性以及功能特异性使其拥有了极大的应用价值。在以往的研究中,纳米Fe3O4颗粒在无机合成反应中的应用是催化领域研究的热点之一 [16]。研究表明,在纳米Fe3O4颗粒表面包裹介孔二氧化硅、多孔碳、二氧化钛、石墨烯等无机材料能够有效减少其团聚并实现功能化。
例如,Nasrollahzadeh等 [17] 将Cu(II)-5-苯基-四氮唑络合物固定在Fe3O4@SiO2表面,并在室温下对该催化剂去除水中亚甲基蓝的反应进行了研究,研究结果证明该催化体系具有反应时间短、催化活性高、催化剂易回收等特点。
Li等 [18] 成功制备了一种用TiO2包裹柠檬酸钠来修饰的磁性催化剂,并探究了该催化剂在紫外光条件下降解罗丹明B的反应,包裹TiO2后的纳米Fe3O4具有介孔结构,这种结构有利于提高催化剂对罗丹明B的降解效率,且在经过5次循环实验之后对罗丹明B的降解率仍然高达90%以上,同时具有良好的可回收性。
Wang等 [19] 采用模板法制备了一种碳包裹纳米Fe3O4的磁性材料Fe3O4@C,经研究发现,碳材料与纳米Fe3O4之间具有较大的接触面积,能够有效地增加催化剂的催化活性位点,提高材料的电子导电率,从而加快反应速率。
Gong等 [20] 设计制备了磁性光芬顿催化剂Fe3O4@GO@MIL-100(Fe),并用其在可见光条件下对2,4-二氯酚进行降解。研究表明,将石墨烯包裹在纳米Fe3O4颗粒表面之后,能够有效地实现其功能化,增加了体系中电子传递的速率,且石墨烯的引入能够有效地分散纳米Fe3O4颗粒,防止其团聚并高效降解污染物。相比传统的磁性纳米Fe3O4颗粒催化剂而言,改性后的Fe3O4材料表现出更高的催化活性、更大的比表面积以及更容易回收利用等优点,使其在催化领域中具有更高的实际利用价值。
Huang等 [21] 制备了磁性核壳结构的催化剂Fe3O4@GO-CoPc,该催化剂是以Fe3O4 (四氧化三铁)为核,GO (氧化石墨烯)为夹层,CoPc (酞菁钴)为壳的非均相光芬顿催化剂。Fe3O4的存在使得材料具有良好的磁性,反应后可以简单快速地回收,GO的引入则加速了Fe2+与Fe3+之间的循环以及提高了H2O2的有效利用率(即H2O2转化为
的效率)。由图3可知,将GO引入催化剂Fe3O4-CoPc中,通过加速光生电子从CoPc到Fe3O4的转移抑制了CoPc中光生电子和空穴的复合,而且提高了催化剂中Fe(III)到Fe(II)的转换速率,增强了Fe3O4-CoPc对H2O2的有效利用率,提高了体系光生载流子的转移能力,增强了催化剂的光芬顿催化活性。
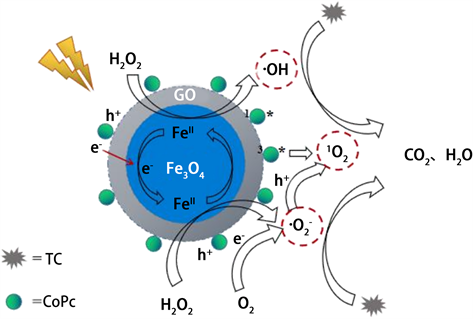
Figure 3. Simplified degradation mechanism of TC in the photo-Fenton system with Fe3O4@GO-CoPc
图3. Fe3O4@GO-CoPc光芬顿降解四环素(TC)的简化机理
5. 展望
近些年来,随着民众环保意识的增强以及政府环保执法力度的加大,对环保技术的发展也提出了避免二次污染、提高能源利用率、催化剂可回收等新要求。非均相复合催化剂广泛应用于废水、废气的处理技术之中,越来越多研究者们成功制备出复合非均相光芬顿催化剂,从开发新型绿色的具有强太阳光响应能力、高载流子分离效率以及良好光催化稳定性的半导体光催化材料的研究目的出发,通过掺杂、负载、包裹等方法对传统催化剂进行改性。在今后的研究中,可以结合密度泛函理论、分子动力学模拟等原理与方法,继续研究催化剂结构参数与催化活性之间的关系。深入了解不同单催化剂之间的复合方式,根据实际要求设计不同构型的复合催化剂,以提高在实际应用中的催化活性和反应速率。
基金项目
国家十三五重点研发计划(2017YFB0310700);湖南省重点研发计划(2018GK2062);湖南省战略新兴产业科技攻关与重大科技成果转化项目(20196GK4044)。