1. 引言
机械连杆机构广泛应用于各种机械、仪表和机电等领域中。随着连杆机构设计方法的发展,相关设计及性能分析软件的开发,连杆机构的设计速度和使用性能有了较大的提高,同时利用有限元分析软件可得到连杆在特定工况下的应力分布及动力学特性,同时使用拓扑优化对连杆进行优化设计,使其性能要求保持不变的同时减轻质量并能降低成本。机械连杆是机械常见的组成部分之一,因为在机构中常见的连杆构件大多呈现杆的形状,所以称之为连杆。连杆除了一般的上下运动形式之外,还可以进行左右方向的摆动,或者做一些相对复杂的平面运动 [1]。连杆的特点为制造方便、便于安装且强度、刚度都有着不错的表现,因此得到了广泛的应用。
如果要对杆件的强度、刚度进行校核,采用传统的实验方法无疑会大大增加工作强度且会造成原材料的大量浪费,生产成本也会相应增加。而有限元仿真软件可以通过计算机的仿真计算来对构件进行模拟的数值分析,且计算结果与实验结果高度类似,这就使得有限元仿真软件在机械连杆的分析中显得十分必要。
国内很多的学者也对连杆进行了很多的研究,孙肾奎等人 [2] 在对连杆的研究时考虑了惯性力对其的影响,还有学者对连杆的动态响应方面进行了分析研究 [3] [4]。
文章中所研究的机械连杆常见的失效形式为受到剪应力和弯曲应力的作用,一旦剪应力或弯曲应力超过机械连杆的许用应力,机械连杆就会发生断裂破坏而造成失效 [5]。
2. 建模及有限元仿真分析
2.1. 机械连杆的建模
采用ProE有限元软件对机械连杆进行建模,ProE建模软件与ABAQUS有限元分析软件接口相同,且两软件的通用单位、坐标都可保持一致,因此在对机械连杆进行分析时所采用的有限元分析软件为ABAQUS。通过ProE建成的连杆模型直接导入到ABAQUS软件中进行后续的静力学模态仿真分析,使用ProE软件对机械连杆模型进行建模,模型如图1所示。本文分析的机械连杆由两个大小不相等且轴线相互垂直的大、小连接头通过两块筋板进行连接组成。机械连杆的材料选择35 CrMo调质钢,这种材料的力学性能良好,且有着不错的塑性和韧性,非常适合用作机械连杆的加工制造。35 CrMo材料相关的力学属性如表1所示。
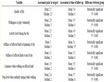
Table 1. Relevant mechanical properties of 35 CrMo materials
表1. 35 CrMo材料的相关力学性能
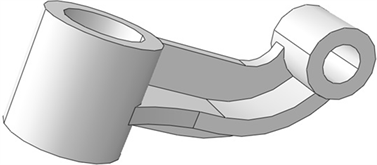
Figure 1. Schematic of a mechanical linkage model
图1. 机械连杆模型示意图
2.2. 有限元软件模型的导入设置及网格划分
根据2.1节的材料参数属性设置材料参数。ABAQUS软件的分析原理是对提交计算模型的单元节点进行相关计算并得出系统的离散域方程,最后对方程进行求解,求解得到的结果便是相关节点处的变量近似值。因此,为了更好地求解相关单元,需要对模型进行网格的划分,将模型变为具有节点的网格化有限元模型,这样就可以对复杂的构件进行相关的有限元分析。
因为此处研究的连杆存在很多的过渡圆弧,所以对机构的网格进行合理的划分在一定程度上会给计算机的运算减轻很多负担。本文对机械连杆的网格划分采用的是ABAQUS自带的自适应网格划分功能,在满足分析要求的基础上极大精简网格数量 [6]。机械连杆的网格划分如图2所示。在载荷施加上,本连杆采用大孔端固定,小孔端承载的方式进行分析,其中在小孔端进行耦合设置及载荷的施加,相关设置如图3所示。

Figure 2. Schematic diagram of the meshing of the mechanical linkage model
图2. 机械连杆模型网格划分示意图
(a) 载荷、固定设置
(b) 小头端耦合设置
Figure 3. Finite element setup diagram
图3. 有限元设置示意图
2.3. 有限元软件对模型的模态分析
模态分析在结构有限元仿真中经常使用,通过有限元分析软件对机械连杆结构固有频率的计算来进行应力及应变特性的相关研究分析。在此运用ABAQUS软件对机械连杆前10阶模态进行计算 [7],方便观看在此仅展示第1、3、5、7、10阶模态的结果示意图如图4所示,整合相关频率计算结果如表2所示。
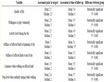
Table 2. Mechanical linkage correlation modal frequency
表2. 机械连杆相关模态频率
从图4中可以看出,连杆在第5阶振型附近发生部件中部的弯曲变形,并且小头端开始发生变形,从第7阶振型附近开始变形趋于剧烈并发生波浪形的摆动。这些现象都会导致机械连杆不能正常的配合,并且很有可能引起附加应力而产生失稳。
从表2软件中提取得到的频率数据可以看出,在400 Hz以下的频率有四阶,频率都略低,而机械连杆一般都在发动机附近工作,发动机在低频段的激励比较大,极其容易发生动态响应。因此在设计中应该考虑通过对结构进行优化处理或者改进材料来降低共振的影响。
2.4. 有限元软件对模型的应力应变分析
使用有限元仿真分析软件机械连杆进行静力学分析 [8],对已经划分好网格的机械连杆模型的小头端耦合点施加2000 N的力。在机械连杆大头端固定、小头端受力的情况下进行静力学分析,最后得到的相关分析结果如图5及图6所示。从图5的结果中可以看出,机械连杆的最大应力出现位置在靠近大头端与筋板的连接处,大小为6.798 MPa,远远小于材料的许用应力值大小,仿真结果也符合材料力学的最大应力点分布规律,此位置所受的弯曲应力最大。从图6中可以看出最大位移位置在小头上远离较宽筋板的位置,大小为6.991 × 10−9 mm,位移量可以忽略不记。此规律也与材料力学相关部件受力后产生位移的规律相符合。从ABAQUS的静力学结果来看,应力、应变规律均符合正常材料力学规律。
3. Abauqs软件的拓扑优化
3.1. 拓扑优化概述
拓扑优化是在特定工况及参数限制条件下对构件进行结构优化,根据材料的分布来选择优化对象,对均匀分布的材料在空间方面寻找最优的布置方案。在很多领域上大量使用,运用ABAQUS有限元分析软件对构件进行相关部位的针对性优化,在相同工况保证功能要求及使用寿命的前提下对构件进行轻量化设计 [9],通过节省材料来达到降低生产成本。
对机械连杆优化的过程中主要包含目标函数、设计变量、约束条件三个要素,使用变密度法表达为:
(5)
(6)
(7)
其中,
为设计变量;
、
分别为总刚度矩阵和连杆位移向量;
为连杆所受的外力向量;V为连杆体积;
为连杆拓扑优化后的体积峰值。
ABAQUS仿真软件拓扑优化的相关流程如图7所示。
根据2.3节的分析结果,对机械连杆的筋板部位进行拓扑优化,设置优化目标区域优化后的体积为优化前的70%,最大应力需不超过材料的许用应力值835 MPa。
3.2. ABAQUS软件的拓扑优化结果
使用Abauqs软件对机械连杆构件进行拓扑优化后,优化区域较为明显的迭代结果如图8所示,依次为第2、3、4、5次迭代结果,根据迭代结果结合2.4节的结果可知:轻量化设计可优先考虑削减面积较小的筋板上靠近小头端位置的材料。对于机械连杆中选择优化的位置在空间方面寻找最优的布置方案,从图9的迭代、体积变化曲线可以看出:模型进行5次的迭代运算以后变收敛且此时应变能达到最小,在对制定优化区域进行70%体积的轻量化设计之后,模型体积下降部分接近机械连杆选中优化位置未进行优化前体积的30%左右 [10]。

Figure 8. ABAQUS topology optimization region iteration results
图8. ABAQUS拓扑优化区域迭代结果
(a) 模型迭代次数曲线
(b) 模型整体体积变化曲线
Figure 9. Model optimization iteration and volume change curve
图9. 模型优化迭代、体积变化曲线
提取优化后机械连杆的应力、应变结果如图10所示,优化后的最大应力值为7.716 MPa,远小于许用应力值,最大应变量为1.07 × 108 mm,两次的应变量都很小。优化前后的变化数值对比结果如表3所示。
4. 结论
本文的研究对象机械连杆并通过ProE软件进行建模,并用ABAQUS软件进行模态分析、静力学分析以及拓扑优化设计,通过分析机械连杆的前10阶振型的表现形式探究可能对构件产生的影响;通过静力学
(a) 应力云图
(b) 应变云图
Figure 10. Stress and strain result graph before and after optimization
图10. 优化后的应力、应变结果图
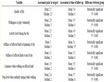
Table 3. Results before and after optimization
表3. 优化前后结果
仿真分析找到连杆部件极其容易发生动态响应位置,并通过对结构进行优化处理或者改进材料来降低共振的影响,在此基础上进行拓扑优化设计,根据材料的分布来选择优化对象,对均匀分布的材料在空间方面寻找最优的布置方案。从最终结果可以看出,杆身设计区域去除质量较多,且满足实际机械加工工艺要求,对降低连杆自身质量和成本有较大意义,为连杆优化提供了一种可行的优化方法。对机械连杆的仿真分析得出了此型号的连杆在工况下的应力分布及构件性能安全,并对连杆设计机构进行优化设计,分析不仅得出了连杆模态静力学分析结果,也验证了ABAQUS软件在仿真分析领域的实用能力,对提高企业核心竞争力有着很大的作用。