1. 序言
三羟甲基丙烷三甲基丙烯酸酯(TMPTMA)是丙烯酸酯系列交联剂中的一个重要产品 [1],因具有双键含量高、固化速度快、粘度低、高沸点、低挥发性等优点,被广泛用于聚烯烃、聚氯乙烯、聚酯、有机玻璃、离子交换树脂、特种橡胶、紫外线固化油墨、厌气性粘合剂中 [2] [3] [4] [5] [6],特别是在交联聚氯乙烯电缆中,其交联效率高于三烯丙基异氰脲酸酯(TAIC),成为在辐射固化领域中用途最广、用量最大的多官能丙烯酸酯活性交联稀释剂 [4] [5]。
酯化反应中,催化剂对具有促进反应、提高原料转化率、缩短反应时间等具有至关重要的作用。现有报道中,TMPTMA多是由三羟甲基丙烷(TMP)与甲基丙烯酸(MA)直接酯化反应合成得到,所采用的催化剂为浓硫酸或对甲苯磺酸 [7] - [12],尤以对甲苯磺酸居多,鲜有报道采用非管制化学品混二甲苯磺酸(对甲苯磺酸的制备原料甲苯为管制品)作为催化剂合成TMPTMA。本论文在前人研究的基础上,首次以工业生产二甲苯的精馏剩余物(主要成分为邻、间、对–二甲苯)为主要原料,以98%硫酸为磺化试剂,得到混二甲苯磺酸;重点研究了以此混二甲苯磺酸作为催化剂,氢醌作为阻聚剂,以二氯乙烷为共沸带水剂,催化TMP与MA经共沸酯化过程合成TMPTMA。通过气相色谱归一法(GC)监控反应转化率,采用气相色谱质谱联用法(GC-MS)对所得TMPTMA进行定性分析。
2. 实验部分
2.1. 主要试剂及仪器
主要试剂:三羟甲基丙烷(TMP)、甲基丙烯酸(MA)、氢醌、二氯乙烷、对甲苯磺酸、与98%硫酸均为分析纯,混二甲苯为工业品。
主要设备:三口烧瓶;分水器;球形冷凝管;搅拌器;恒温油浴装置;分液漏斗;减压蒸馏装置;G5气相色谱仪(北京普析通用仪器有限责任公司);GCMS-QP2010气质联用色谱仪(日本岛津公司)。
2.2. TMPTMA的合成及后处理 [8] [12] [13] [14]
在装有分水器、回流冷凝管、搅拌器及温度计的250 mL三口烧瓶中加入混二甲苯和98%硫酸,升温至既定温度,反应4小时,体系中游离硫酸含量 < 0.1%,视为反应结束,降温至室温,得到混二甲苯磺酸催化剂。
向上述250 mL三口烧瓶中二氯乙烷、TMP、MA、氢醌,升温搅拌至反应结束。蒸馏回收二氯乙烷。降温,体系中剩余物经饱和碳酸钠洗涤至中性,再用饱和食盐水洗一次,分去水层,得到浅黄色黏稠状液体产物。
3. 结果与讨论
3.1. 合成原理
由TMP与MA经共沸酯化法合成TMPTMA如图1所示。该反应副产物为水,利用二氯乙烷与水可形成低沸点共沸物的特点,采用二氯乙烷作为带水剂,及时将生成的水除去,使平衡向生成产物的方向移动。同时在体系中也加入了少量阻聚剂氢醌以避免MA及TMPTMA的自聚 [12]。因为它们都含有C=C键受热升温易产生热聚合而降低酯的产率。
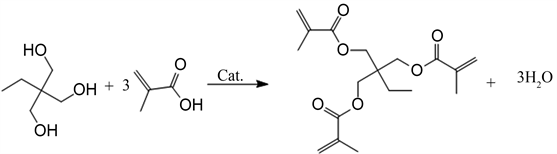
Figure 1. Process for synthesis of TMPTMA
图1. TMPTMA的合成图
3.2. 酯化条件对反应的影响
3.2.1. 催化剂用量对酯化反应的影响
以催化剂质量与TMP和MA的质量之和的比例为准,研究催化剂用量对图1所示酯化反应的影响(图2)。随着催化剂用量由0.1%增加到5%,TMP与MA的转化率均增加,同时,酯化反应酯化率也同样呈现明显上升趋势。但,当催化剂质量为TMP和MA的质量之和的5%之后,继续增加催化剂用量,MA的转化率基本保持不变,同时,TMP转化率以及酯化率均只呈现微弱的增长。因此,在本实验条件下,最适宜的催化剂用量为5%。
3.2.2. 外加温度对反应的影响
提高反应热源温度对促进和加快反应往往具有增强效应。然而,在本实验过程中发现,当外加温度超过一定温度范围后,反应液颜色加深且有明显黑色固体产生。通过分析反应过程中原料TMP与MA的转化率,以及反应酯化率数据(图3),在外加温度由90℃逐步升高至130℃时,原料TMP与MA的转化率,以及反应酯化率均呈现明显上升趋势,当外加温度为130℃时达到最大值,此时体系颜色仍可保持较为清澈、无固体不溶物。继续增加外加温度时,反应酯化率显示出明显的降低现象。尤其是当外加温度高于150℃时,体系呈现大量黑色固体颗粒。可能原因是温度超出一定范围后,阻聚剂对氢醌被迅速碳化,同时,带有双键结构的MA及TMPTMA发生或多或少的聚合等副反应 [12]。因此,在本实验条件下,最适宜的外加温度为130℃。
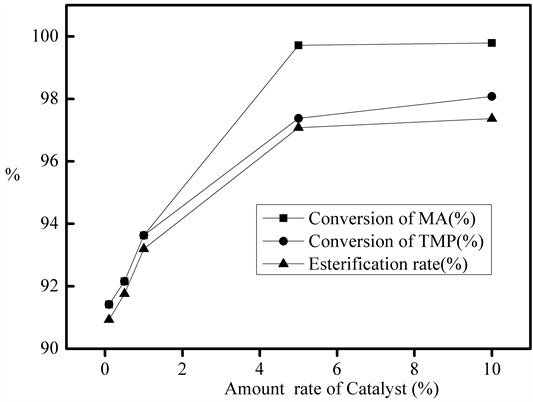
Figure 2. Influence of the dosage of catalyst on the reaction
图2. 催化剂用量对反应的影响

Figure 3. Influence of the temperature on the reaction
图3. 外加温度对反应的影响
3.2.3. 酯化反应时间对反应的影响
由实验数据可知(图4),当反应时间由2小时延长到8小时,原料TMP与MA的转化率,以及反应酯化率均展示出上升现象;继续延长反应时间为10小时,原料TMP与MA的转化率仍能给出继续增大的趋势,但反应酯化率出现明显降低现象。可能原因是,反应时间的延长引起TMPTMA的产生和自聚反应同步进行。因此,在本实验条件下,反应时间为8小时为最适宜反应时间 [8]。
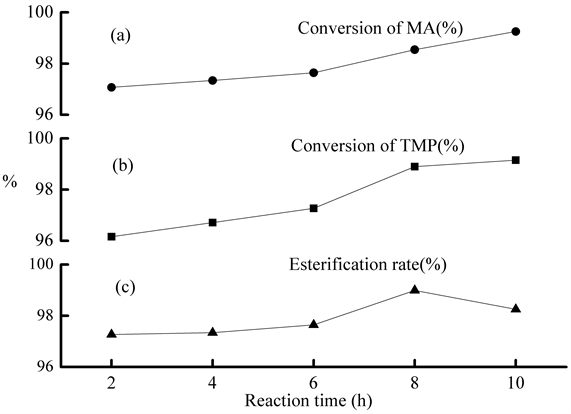
Figure 4. Influence of the estrification time on the reaction
图4. 酯化反应时间对反应的影响
3.2.4. 催化剂种类对反应的影响
为进一步衡量自制混二甲苯磺酸催化剂的催化性能,选择98%硫酸和工业对甲苯磺酸作为对比,在同样条件下,考察了三种催化剂对图1所示酯化过程的影响。表1数据表明,所对比三种催化剂在相同的条件先对原料TMP与MA的转化率的促进性能十分相近。反应酯化率数据明显展示了三种催化剂对应的反应酯化率分别为87.8%、98.6%和99.1%。说明文自制催化剂体现出几乎与工业对甲苯磺酸相同的催化性能,而98%最不适宜于本反应,其可能原因是其强大的脱水能力,在130℃条件下,造成了反应原料及产物发生脱水碳化等副反应。
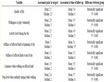
Table 1. Influence of different catalysts on the reaction
表1. 不同催化剂对反应的影响数据一览表
综上所述,本文自制催化剂体现出几乎与工业对甲苯磺酸相同的催化性能,既为制备TMPTMA开发了一款新型磺酸类催化剂,又为解决工业生产二甲苯的精馏剩余物(主要成分为邻、间、对–二甲苯)提供了一种资源化利用途径。
3.3. 产品检测
通过气相色谱质谱连用仪(GCMS)对如图1所示的反应过程,在上述最优化条件下,得到的TMPTMA产品进行检测。
其分子结构式为 [12]: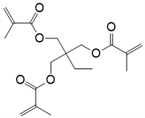
GCMS(EI):338[M],310,253,183,154,109,98,81,69,41。结果与文献 [12] 相符。
4. 结论
本论文以TMP与MA为反应原料,采用共沸酯化法合成了TMPTMA。
1) 以工业生产二甲苯的精馏剩余物(主要成分为邻、间、对–二甲苯)和98%硫酸反应制备得到混二甲苯磺酸作为催化剂;研究了催化剂用量、外加热源温度、反应时间对酯化过程的影响,结果表明最适于本反应的条件为催化剂质量为TMP与MA质量之和的5%、外加热源温度为130℃、反应时间为8小时,在此条件下原料TMP与MA的转化率、反应酯化率均在98%以上;
2) 通过与现有技术中常用的98%硫酸、工业对甲苯磺酸两种催化剂进行对比,发现自制混二甲苯磺酸催化效果明显优于98%硫酸、与工业对甲苯磺酸具有几乎相同的催化性能;
3) 分别采用GC和GC-MS对产品进行了纯度检测和定性分析。
基金项目
滁州学院2021~2022学年开放实验项目(kfsy2101);滁州学院校级科研启动基金(2020qd07);滁州市指导计划项目(2021ZD026)。
NOTES
*通讯作者。