1. 引言
小负载液压缸多数为液压缸水平施力,推动某机构,其负载仅为机构的摩擦力。工程应用上会出现液压缸完全回收后,活塞杆在一段时间内自动伸出现象,即产生活塞杆漂移故障。本文针对活塞杆漂移故障,对液压系统及液压缸的内泄漏特性开展研究。液压缸活塞杆完全伸出后,其内泄漏特性对机构影响较小;液压缸活塞杆完全回收后,其内泄漏特性会导致活塞杆漂移故障,使得装备机构意外活动导致运动副干涉,甚至对设备或人员安全造成较大影响。液压缸的内泄漏特性是液压缸固有特性,其产生的主要原因有:活塞杆、活塞、缸筒之间的同轴度等加工精度差异 [1] [2];活塞表面的圆柱度不满足要求或磨损不均衡时产生偏磨问题 [3];密封圈实际接触应力大于设计应力 [4];密封损伤、油液污染、油温过高、元件老化、使用时间及次数等因素的影响 [5],其内泄漏量因个体差异而存在差距。液压缸的内泄漏特性,可使得执行元件的动力变低、活塞的运行速度变小 [6],甚至在无任何指令控制下,意外动作,导致设备故障或损坏。本文利用AMESim软件对不同的液压系统建立了小负载液压缸仿真模型,根据实际产品参数对液压缸模型进行配置。本文针对某型液压缸从内泄漏量、工作压力、系统背压、静摩擦力4个方面对内泄漏特性的影响开展了研究,并提出了防止液压系统或者液压缸内泄漏导致液压缸活塞杆漂移的措施,为故障分析提供了理论指导。
2. 基本数学模型
小负载液压缸在完全回收后,油缸进回油管路完全截止,假设液压系统元件无泄漏,则液压缸活塞杆存在漂移的主要原因在于液压缸内部的内泄漏导致,液压缸内部泄漏示意图如图1所示。
当活塞杆停止运动后,由于液压缸有/无杆腔压差及内泄漏现象的存在,液压缸两腔的压力最终相等,其液压缸的受力达到平衡,其基本数学模型的受力计算如式(1)所示:
(1)
P有杆腔——液压缸有杆腔的压力;
P无杆腔——液压缸无杆腔的压力;
S活塞——活塞的面积;
S活塞杆——活塞杆的面积;
F负载——负载的力;
f摩擦力——密封圈的静摩擦力。
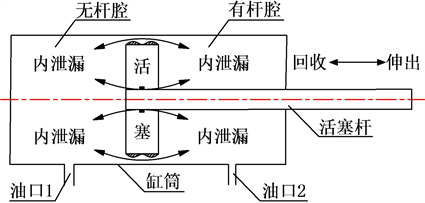
Figure 1. Internal leakage diagram of hydraulic cylinder
图1. 液压缸内部泄漏示意图
3. 仿真模型
本文利用AMESim软件进行了小负载液压缸仿真模型的建立,对不同的液压系统进行仿真模型,如图2所示。根据实际产品参数对液压缸模型进行配置,仿真模型的参数如表1所示,对换向阀控制液压缸的伸出和回收时间进行设置,如图3所示,最终液压缸活塞杆处于完全回收状态。
在建模过程中进行以下几点简化:
1) 忽略油温对油液粘度及泄漏的影响;
2) 忽略液压油内气体对泄漏的影响;
3) 忽略换向阀和液压锁的内泄漏;
4) 模型初始时,假设系统背压为0 bar。
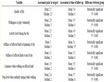
Table 1. Simulation model parameters
表1. 仿真模型参数
本文通过仿真模型研究了活塞杆完全回收、换向阀回到中位后,由于内泄漏的原因导致活塞杆自动伸出现象。从图4可以看出,Y型阀、Y型阀 + 液压锁、O型阀三种液压系统,当活塞杆完全回收后,Y型阀的系统液压缸未出现自动伸出,而其他两个系统都存在活塞杆自动伸出的现象,最大伸出4 mm,

Figure 2. Simulation model of small load hydraulic cylinder system
图2. 小负载液压缸系统仿真模型
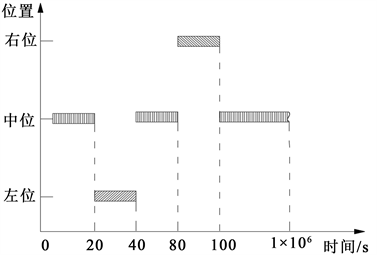
Figure 3. Control time of reversing valve
图3. 换向阀控制时间
这是因为单独Y型阀的系统,液压缸活塞杆完全回收、换向阀回到中位后,有/无杆腔的压力及时泄放至油箱,使得无内泄漏产生。而Y型阀 + 液压锁、O型阀两个系统,活塞杆完全回收、换向阀回到中位后,液压缸两腔的压力被液压锁或O型阀截止,两腔的压力维持换向阀回到中位前的压力,有杆腔的压力大于无杆腔,导致内泄漏现象发生,有杆腔高压的液压油泄漏至无杆腔,当两腔压力相等时,无杆腔的力大于有杆腔,使得活塞杆自动伸出,直至两腔的力达到平衡,最终液压缸两腔的压力稳定在8.6 bar,在活塞杆自动伸出的过程中,液压缸两腔的压差逐渐降低,其内泄漏量也逐渐减小。
4. 内泄漏特性研究
小负载液压缸的活塞杆完全回收后,由于液压缸的内泄漏特性,导致活塞杆在一定的时间内出现自动伸出的现象,本文针对某型液压缸从内泄漏量、工作压力、系统背压、静摩擦力4个方面对内泄漏特性的影响开展了研究。
4.1. 内泄漏量影响
液压缸的泄漏量受活塞与缸体之间或活塞与活塞杆之间的加工精度及配合精度影响,同时随着液压缸的使用时间和次数的影响,每个液压缸的个体内泄漏量存在差异。
(a) 活塞杆行程
(b) 活塞泄漏处流量
(c) Y型阀 + 液压锁系统液压缸压力变化
Figure 4. Internal leakage characteristics
图4. 内泄漏特性
(a) 不同泄漏量活塞杆自动伸出的行程
(b) 不同泄漏量液压缸两腔最终稳定的压力
(c) 不同泄漏量活塞杆不再伸出的时间
Figure 5. Influence of internal leakage on internal leakage characteristics
图5. 内泄漏量对内泄漏特性影响
由图5可知,液压缸内泄漏量从8 × 10−7 L/min/bar增加到8 × 10−3 L/min/bar,Y型阀 + 液压锁、O型阀两个系统内泄漏特性变化趋势一致。随泄漏量的增加,液压缸活塞杆自动伸出的行程变化不大,最大约为4.6 mm,液压缸达到力平衡后有/无杆腔压力最终稳定在8.6~9 bar之间,达到稳定状态所需要的时间越短。这是因为内泄漏量在一定范围内时,泄漏量大小只是增加了两腔油液流动速度,液压缸自动伸出量取决于负载和缸内摩擦力大小,当这个两个参数不变时,由公式(1)可知液压缸的两腔最终平衡压力一致。
4.2. 工作压力影响
单独Y型阀系统当换向阀回到中位后,液压缸两腔的压力相同并及时释放至油箱,若油箱背压很小,则液压缸的静摩擦力可以抵抗住由于液压缸两腔面积不同带来的推力,其工作压力对泄漏无影响。
当系统背压较小时,Y型阀 + 液压锁和O型阀都能够及时关闭液压缸两腔的通道,实现保压功能,工作压力不同,当换向阀回到中位后,液压缸两腔的压差不同,对泄漏有一定的影响。
本文以Y型阀 + 液压锁的换向系统为例,内泄漏量为8 × 10−5 ml/min/bar,研究了不同的工作压力对内泄漏特性的影响。
由图6可知,随工作压力的增加活塞杆自动伸出的行程增大,当工作压力为160 bar时,活塞杆自动伸出约8 mm;工作压力越大,液压缸两腔的压力到达稳定状态所需要的时间越长,但不同的工作压力下,液压缸两腔的压力最终压力值一致,均为9.2 bar。
这是因为在负载和摩擦力相同时,由公式(1)可知,无论工作压力多大,最终液压缸两腔的压力都会稳定至一个固定值才能实现力平衡,而随工作压力的增大,则有杆腔内向无杆腔内渗漏的油越多,从而你导致活塞杆伸出越长。
(a) 不同工作压力下活塞杆自动伸出的行程
(b) 不同工作压力液压缸两腔的压力
Figure 6. Effect of working pressure on internal leakage characteristics
图6. 工作压力对内泄漏特性影响
4.3. 系统背压影响
本文研究的系统背压为换向阀T口有主动的油压,在仿真模型内设置为10 bar,从换向阀T口至油箱之间回油管路产生的被动背压较小,此处忽略。
由图7可知,活塞杆完全回收、换向阀回到中位后:O型阀系统由于内泄漏现象,自动伸出约6 mm;单独Y型阀系统活塞杆在很短的时间内完全伸出;Y型阀 + 液压锁系统在较长的时间内完全伸出,这是因为系统背压过大,导致液压锁频繁开启,使得液压缸无杆腔内不断补充油压的原因。由图7(d)可以看出,随着液压锁开启压力的增大,活塞杆完全伸出的时间增大,当开启压力大于5 bar时,系统背压无法开启液压锁,其自动伸出的行程为内泄漏导致,与O型阀系统活塞杆自动伸出的行程相近,约为6 mm。
(a) 不同系统背压下活塞杆自动伸出行程
(b) 不同系统背压下泄漏处流量
(c) 不同系统背压下两腔压力变化
(d) Y型阀 + 液压锁系统不同液压锁开启压力下活塞杆行程
Figure 7. Influence of system back pressure on internal leakage characteristics
图7. 系统背压对内泄漏特性影响
4.4. 静摩擦力影响
小负载液压缸在使用过程中,液压缸内密封圈的静摩擦力不可忽略,也是液压缸活塞杆自动伸出的阻力。由图8可知,随着静摩擦力的增加,活塞杆自动伸出的行程降低,液压缸两腔达到平衡的压力增大。这是因为当活塞杆完全回收、换向阀回到中位后,由于内泄漏的原因,两腔的压力最终泄漏至相等,此时液压缸两腔压力作用面积不同导致力的差值与密封圈静摩擦力以及负载的力之和相等时,活塞杆不在自动伸出,当密封圈摩擦力增加时,液压缸两腔稳定的油压在较高压力下可达到平衡,活塞杆也无需再次伸出来降低两腔的压力。
5. 结语
本文利用AMESim软件进行了小负载液压缸仿真模型的建立,对不同的液压系统进行仿真模型,根据实际产品参数对液压缸模型进行配置。
当活塞杆完全回收、换向阀回到中位后,由于液压缸的内泄漏特性,导致活塞杆在一定的时间内出现自动伸出的现象,本文针对某型液压缸从内泄漏量、工作压力、系统背压、静摩擦力4个方面对内泄漏特性的影响开展了研究。
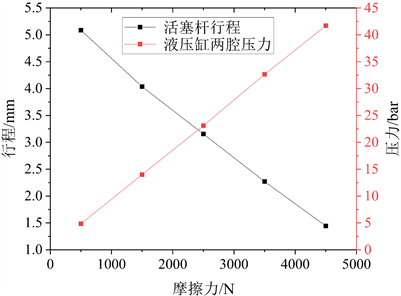
Figure 8. Effect of static friction on internal leakage characteristics
图8. 静摩擦力对内泄漏特性影响
结果表明:活塞杆自动伸出的行程取决于伸出时的负载和密封圈静摩擦力的大小,完全伸出所需要的时间取决于内泄漏量的大小。
针对小负载液压缸内泄漏特性,液压缸活塞杆漂移现象,本文对液压系统提出以下几项措施:
1) 采用Y型换向阀时,在液压系统中增加液压锁;当系统背压较大时,适当增加液压锁的开启压力或在换向阀T口增加单向阀;
2) 采用密封性能好的O型换向阀,并在换向阀T口增加单向阀;
3) 适当增加活塞杆伸出时的负载或者静摩擦力;
4) 液压缸完全回收后,及时泄放液压缸有杆腔的压力。