1. 引言
随着国家工业化水平的发展和生产能力的不断提高,食品包装行业正向着机械化、自动化方向发展 [1]。商品零售超市如雨后春笋般的出现,市场上定量包装商品的种类和需求量越来越大,电脑组合秤需求也越来越大,而目前组合秤的核心技术依然掌握在少数几个发达国家手中,日本大和生产的ADW420系列产品,称重斗数为20,包装速度高达240包/min,定量精度一般在0.1~1 g,代表着组合秤的世界先进水平 [2]。在我国,各地的我国电脑组合秤正在蓬勃发展,但价位普遍较高,从而导致很多中小型企业没有经济能力去购买使用,他们想以相对便宜的价格购买组合秤来实现产品的自动化称量包装。目前,主要通过专用测量硬件的研发和控制方式的提高来进一步提高组合秤的称量精度和速度,然而只有对组合称量技术具有足够深入的了解,才能更优化控制系统进步来提高组合和的各方面性能 [3]。因此,为改变这一现状,本文设计一套使组合秤全自动运行的控制系统,首先利用数理统计的知识从理论层面分析如何使组合秤的称量精度高、速度快。只有透彻的了解组合计算方法和原理对产品合格率高低的影响,才能设计出响应快速且性能稳定的控制系统,以理论分析为依据根据设计需求对整个控制系统进行设计与实施,整个控制系统由硬件和软件两部分组成,通过软件程序的编写驱动硬件外设协同动作最终成功实现了组合秤的全自动运行。
2. 结构工作原理分析
2.1. 传统单体秤工作原理的分析
传统单体秤根据传感器内部的弹性体受力变形,内部应变片阻值发生变化,通过将电压信号解析、转换从而得到质量。但这需要物品必须稳定之后才能得到较精确的质量,在面对称量质量分布不均匀、形状不规则的物品时,有抗干扰能力差、称量速度较慢且精度不好把控等弊端,通常需要较长时间才能准确称出目标重量,因此效率较低 [4]。
2.2. 动态组合秤工作原理的分析
动态组合秤通过更加有效地控制振幅,实现均匀给料,通过多次组合从而适用于大重量称重。由上料盘进行上料,通过用控制主振机和线振机的振动,抖动料直至其下落到下面的存料装置,接着通过单片机控制存料斗打开,使料继续下落到称量斗里,使用称量装置下面附带的电阻应变式称重传感器,称出来每个斗的重量。通过组合算法,找到最接近设定的目标,并且满足误差要求的组合。同时释放称料斗,使料下落进行下一步包装。
因为这个传感器具有能良好的线性度以及抗偏载能力,对于形状较小且不规则的物品进行称量时,该系统保证了系统高精度高速度的分析,可以达到满足于企业应用的水平。标准组合秤的出现虽然弥补了传统定量设备的不足,提高了定量产品包装的速度和精度 [5]。但面对质量较小的物品时无法准确高效地给出其质量。
3. 组合算法的优化
3.1. TRIZ理论分析
当改善技术系统中某一特性或参数时,同时引起系统中另一特性或参数的恶化,这种矛盾就称为技术矛盾。工程中存在着大量的技术矛盾,利用TRIZ理论体系分析产品工作过程的不足之处,将实际问题转化为技术矛盾,之后就可以通过查矛盾矩阵表中的发明原理,归纳分析进而设计出一种有效的解决办法。
组合秤的精度和速度都是用户关心的主要参数,而根据实际生产中用户对于组合秤性能的要求,将组合计算分为高速度型和高精度型两种类型。工作速度快,测试精度较低;测试精度高,工作速度较慢。故组合秤的速度和精度构成了技术矛盾。由矛盾矩阵表1查到发明原理为:
(28) 机械系统替代原理——利用物理场或其他的形式、作用和状态来代替机械的相互作用;
(32) 颜色改变原理——通过改变颜色或一些其它的光学特性来改变对象的光学性质;
(1) 分割原理——以虚拟的方式或实物的方式将一个系统分成若干部分,以便分解或合并一种有益的或有害的系统属性;
(24) 借助中介物原理——使用中介物传递或完成所需动作;
(13) 反向作用原理——尝试以一种相反的方式来制造或执行。
3.2. 优化算法的实现
3.2.1. 高速度型组合算法
高速度型指的是按照允许的误差区间开始执行程序后,按照顺序进行组合运算。一旦出现允许误差范围内的组合,则停止本次组合,对合格组合进行输出并开始下一次的组合。高速度型算法计算量比较小,可以节省大量的运算时间,极大地提高了组合秤的组合速度。程序流程图如图1所示。
3.2.2. 高精度型组合算法
高精度型指的是按照允许的误差区间开始执行程序后,依次进行组合计算,直到把所有的组合种类全部计算一遍,然后将满足要求的组合相互之间进行比较,选择其中与目标重量偏差最小的组合进行输出。高精度型算法最终选取的组合重量相较于高速度型算法更接近于目标重量,但相对来说消耗时间较长,适合用于对精度要求很高的产品。程序流程图如图2所示。
3.2.3. 优化的组合算法
经过上两小节的组合算法比较,我们采用发明原理(1)分割原理和发明原理(13)反向作用原理来解决这一矛盾。首先,利用发明原理(1)分割原理通过递归函数来完成组合程序算法的实现。再利用发明
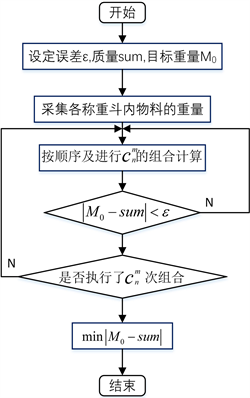
Figure 2. High-precision combinatorial process
图2. 高精确度型组合流程
原理(13)反向作用原理,使组合秤的速度、精度都得到了保证。为了能够更加直观的反映组合程序的设计过程,以
的组合计算为例进行介绍。总共有16个称重斗,取其中4个参与组合。组合称量的目标重量为M,允许称量误差为±ε,从16个称重斗中选取4个进行组合,令这4个料斗对应的组合编号分别为a、b、c、d,对应的重量分别为i、j、x、y。用m表示组合得到的重量,组合计算的程序流程如图3。
由流程图可以看出组合算法程序的实现可以通过递归函数来完成。下面介绍算法的程序实现。下面程序中,浮点型数组a [n]为重量数组,负责存放每个称重斗得出的重量;n表示称重斗总数;数组b [M]为组合数组,用来存储参与组合的称重斗元素,这里存储的是称重斗的下标。m表示满足要求的组合中称重斗的数量,M = m。
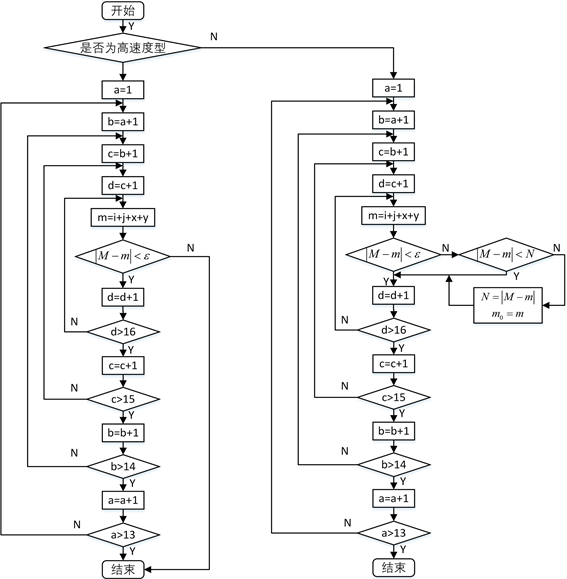
Figure 3. Combined computer program flowchart
图3. 组合计算机程序流程图
4. 硬件部分的设计
4.1. 控制系统硬件总体设计
本文采用模块化的设计理念,将整个控制系统划分为若干个不同功能的子模块,其中包括称重传感器、AD数据采集模块、中央控制器模块、步进电机及驱动器模块、直流电源模块等。组合秤的称重流程为:首先开机进行初始化,清空料斗中的物料;然后进行物料检测,若物料低于光电检测开关的位置,通知物料传送装置加料;然后主振机和线振机振动给存料斗加料,加料的速度由主振机和线振机的振幅决定;然后主控制器驱动存料斗电机运转,将物料加入称重斗;称重传感器将称重斗物料重量转换为模拟信号输出,经过放大、滤波后由AD模拟数字转换器将模拟信号转换为数字信号,由副控制器CUP通过RS485传送给主控制器;主控制器对采集的多路重量值进行组合运算,选择出满足要求的组合,主控制器驱动满足组合要求的称重斗电机运转放料,完成一次组合称重。系统总框图如图4所示。
4.2. 主控模块的设计
在进行控制系统的设计时,CPU的选择显得至关重要。CPU的性能直接决定了系统运行速度的快慢、功能的强大与否以及系统是否稳定。在进行CPU的选择时主要参考芯片的运算速度和精度、所含硬件资源、价格和货源、功耗、配套的开发工具和封装方式等其他信息。由于组合秤通常是由多个称重斗组成,
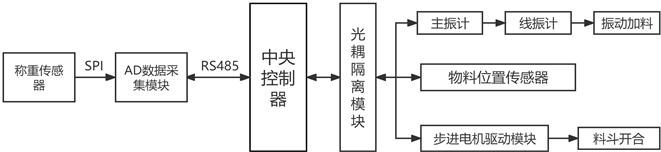
Figure 4. Block diagram of the overall system hardware design
图4. 系统硬件整体设计框图
一般为8~16个称重料斗,因此控制器的输入输出IO口数量较多。本课题采用16个称重斗,则需控制32个引脚控制步进电机,16个引脚控制线阵机,1个引脚控制主振机,此外还有其他的一些输入输出例如指示灯需要占用引脚,故输入输出口以及芯片资源需要很多。综合考虑下,拟采用ARM级STM32F103ZET6微处理器设计控制主板,该芯片拥有高达144个引脚可供使用,且时钟高达72 MHz,运行速度非常快。
在通信方面,选择RS485总线实现主控与副控之间的通信。RS485通信速率快、带负载能力强,能够有效抑制共模干扰,且各负载之间相互独立工作,大大降低了副控单元的故障影响率。基于RS485总线的需要,选用RS485芯片作为通信芯片,该芯片在通信的距离和速度上有很好的表现,接收输入具有真正的失效保护功能,能够有效提高通信模块的安全性和稳定性。
4.3. 电源模块的设计
组合秤控制系统的电源模块繁多,为简化电路设计,直流电源模块均设计在主控板上,由主控板统一供电,各电源模块之间相互独立,但电路设计的基本原理相同。以给主控单元供电的图5,12 V电源为例,供给给通信模块的工作电压是4.5~5.5 V,供给给微处理器STM32F103ZET6的工作电压是2.0~3.6 V。使用外部直流电源给AD8253供±15 V电压,+15 V电压经过LM7805稳压器降为+5电压,+5 V电压供模拟数字转换器AD7609使用,+5 V电压再通过AMS1117转化为+3.3 V电压。+3.3 V电压供副控制器主CPU及外围电路使用。
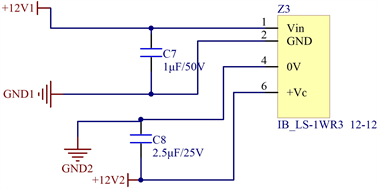
Figure 5. Schematic diagram of 12V power supply circuit
图5. 12V电源电路原理图
4.4. AD采样电路的选用及理由
称重传感器输出的电压信号经过AD8253仪表放大器进行放大滤波,此过程称重传感器输出的微弱的电压小信号放大驱动ADC模数转换器。ADC模数转换器将连续的模拟信号转换为数字信号 [6] [7],经副控制器CPU通过RS485传输给主控制器进行处理和运算。本课题拟采用转换器AD7609。
AD760是ADI公司生产的一款18位,8通道的电荷再分配逐次逼近型模数转换器(ADC)的数据采集系统,模拟输入阻抗为1 MΩ,8个差分模拟输入通道可以进行同步采样,每一路输入通道均具有200 KSPS的吞吐速率,采用5 V单电源供电,使用RANGE引脚可以选择±10 V或±5 V的输入范围,可以采用并行或者串行的方式与CPU通讯,芯片每一通道都具有一个采样保持器,因此可进行多通道信号的同时采集 [8]。
如图6所示,AD7609采用5 V模拟电源供电,电源引脚AVCC接去耦电容至AGND,REGCAP引脚通过1 µF电容去耦至AGND,V1至V8引脚通过1 µF电容去耦至AGND,REFCAPA与REFCAPB引脚连接在一起通过低ESR10 µF陶瓷电容去耦至AGND,REFGND引脚直接连接至AGND,REFIN/REFOUT引脚与REFGND引脚附近的地之间加10 µF的去耦电容。去耦电容的使用为芯片提供了稳定的电源 [9] [10] [11]。
4.5. 光耦隔离模块的设计
为抑制噪声、消除接地回路的干扰,提高响应速度,采用光电隔离电路,隔离外部设备和电路控制单元。如图7,该电路采用两个光耦构成的线性电路,两个光耦输入端串联组成差分负反馈电路来补偿光电耦合器的非线性电流传输特性 [12]。
然后采用Multisim进行仿真分析,从图8中可以看出,两个光耦输入端串联组成差分负反馈电路可以很好的补偿光电耦合器的非线性电流传输特性,图像可以看出,电压基本成线性输出,在4~5 V之间存在较小波动。由此该电路符合设计要求,能够补偿非线性特性。
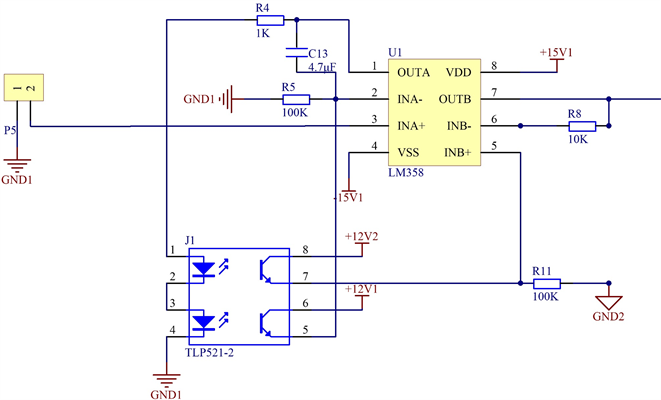
Figure 7. Schematic of a 0~5 V isolation circuit
图7. 0~5 V隔离电路原理图
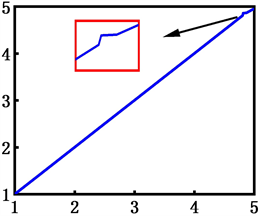
Figure 8. Linearity analysis of photoelectric isolation circuit
图8. 光电隔离电路线性分析
4.6. 滤波电路模块的设计
由于传感器在测量构成中常常参杂许多噪声信号,因此会影响测量系统的精度。因此常常需要消除噪声信号的干扰。本文测量的电流信号频率低于100 Hz,因此设计一个二阶低通滤波器,滤去频率超过100 Hz的高频干扰。该电路具有原件少、增益稳定、频率范围宽等优点。电路中C11、C12构成反馈网络。具体电路设计如图9。
应用Multisim对二阶低通滤波电路进行仿真分析,结果如图10,从图中可以看出,对于频率高于100 Hz的电压信号逐渐降低,最终变为0。仿真结果表明该电路能够有效的消除高于100 Hz的信号。
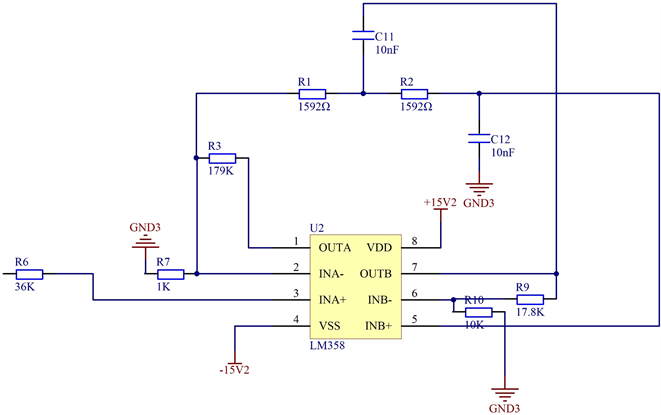
Figure 9. Schematic of a second-order filter circuit
图9. 二阶滤波电路原理图
5. 实验过程与结果
在工业现场本文以定量包装常用的花生为原料,用量程为2500 g、分度值为0.001 g的电子天平对下料的组合进行称重后备用,标注其重量值,用于对比组合称重误差。目标重量分别设置为100 g、200 g,偏差值为5 g,对组合结果做了数据统计,实验数据如表2所示。由于本文对系统的组合算法进行了优化,减少了其他不必要的组合工作,可以将组合时间控制在20 ms之内。根据每个环节所需时间推算出组合一次的时间大约为928 ms,即组合速度大65包/min。
综上所述,由实验结果可知,当组合速度达到65包/min时,目标重量为0~200g时组合平均误差在±0.5 g范围内,可以满足企业生产要求。
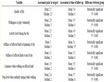
Table 2. Table of field experiment measurement results
表2. 现场实验测量结果表
6. 结论
本文设计的基于STM32的组合秤控制系统通过对现有问题的分析归纳,不仅全面的了解了传统系统的不足之处,而且能针对性的进行流程算法的改进,弥补了传统的固定每次参与组合的称重斗的数量而过分依赖加料稳定性方式的不足。在硬件设计方面,将整体控制系统模块化,进而逐个进一步设计仿真,调整元件参数至实现称重不同物料之间的自动切换,这样相对于传统的设备在配置不同物料参数之前的大量的测试工作,本文系统大大减少了工作量,提高了设备的精确性和运行的速度。通过现场的测试,系统的速度和精度都能达到预期要求,能够有效提高中小型包装生产效率。
NOTES
*通讯作者。