1. 引言
节镍奥氏体不锈钢是在传统304奥氏体不锈钢的基础上,为节约成本,减少贵金属镍,增加锰、氮等形成室温下为单一奥氏体组织的经济型不锈钢。近年来,由于该类钢优异的力学性能、一定的耐蚀性能以及较低的成本,具有优异的机械性能、较高的强度、塑性和一定的耐蚀性,被广泛应用于建筑装饰、不锈钢焊管制作等 [1] [2] [3]。
目前某公司主要生产的J2钢种是节镍含氮经济型奥氏体不锈钢,但在热轧过程中钢带头尾在精轧时偶有出现分层现象,需对分层钢带进行剪切,影响了产品的质量和正常生产,严重时被判废或降级使用,给公司造成较大经济损失。其公司生产J2宽坯(1020、1240和1530 mm)在前期加工热轧轧制薄板时偶有分层现象,部分时段会批量出现,在钢坯轧制中厚板(16 mm)时也有分层现象,赵喜伟 [4] 在低合金中厚板Q345E在做拉伸实验过程中常出现分层脆性断裂缺陷,出现分层缺陷的主要原因是钢板厚度1/2处出现带状组织,夹杂物较多。通过优化炼钢工艺,提高连铸机设备精度,改进连铸工艺等措施,降低了钢中的夹杂物含量,减轻了连铸坯的中心带状组织偏析,使钢板出现分层缺陷的情况得到了明显改善;申鹏 [5] 对0Cr18Ni9不锈钢热轧卷的分层原因进行了分析,主要原因是由于连铸过程中产生的氧化物夹杂物引起的。为避免分层的产生,应加强连铸中间包保护渣操作的管理,以避免夹杂物的产生。
为查找镍型钢种钢板“分层”原因,提高成材率,特对“分层”钢板进行了低倍分析、显微组织检验和电镜-X射线能谱分析等检测手段和工艺排查寻找分层原因。
2. 试验材料与方法
2.1. 试验材料
试验J2钢带化学成分见表1,试样取自编号210725072,分层钢板的宽度为1530 mm,厚度为16 mm。分层裂纹沿轧制方向扩展,分层部位距板卷边部约520 mm,分层部位长度约200 mm。将分层部位用火焰切割枪割下,宏观形貌见图1。
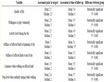
Table 1. Chemical composition of J2 steel strip (%)
表1. J2钢带化学成分(%)
2.2. 检测方法
本报告采用的检测方法见表2。
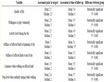
Table 2. Analysis content and detection methods
表2. 分析内容及检测方法
3. 实验过程及结果
J2热轧时头尾分层情况有时非常严重,大多数分层缺陷出现在钢板厚度方向1/2处(端面中部),有时在精轧过程中还会听到钢板“放炮”的声音。对铸坯厚度方向1/2处进行取样分析,如图2所示。
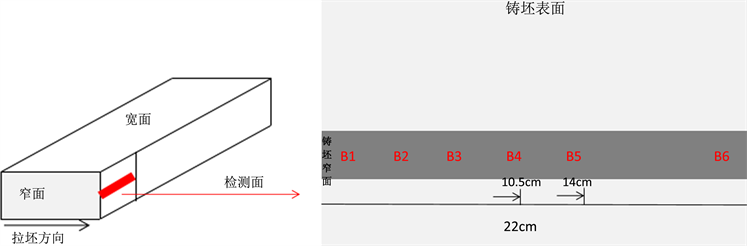
Figure 2. Sampling locations of continuous casting slab
图2. 连铸坯取样位置

Figure 3. Inclusions and looseness at hot-rolled layers
图3. 热轧分层处的夹杂物和疏松
在图2中B4、B5处缩孔价位严重,经检测发现缩孔处氧含量较高,如图3所示,存在很多非金属夹杂物,夹杂物的成分如表3所示。
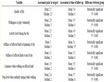
Table 3. Content of Fe, Cr, Mn and O at hot-rolled layers (%)
表3. 热轧分层处Fe、Cr、Mn、O元素含量(%)
由图3出现的现象和表3中的数据推断,在板坯切割的短时间内,缩孔处表面已氧化,其周围也存在渗氧现象。说明分层发生在连铸坯凝固的末端,由于此时Cr、Mn、O等元素的偏析,形成了一层与基体成分完全不一样的特殊层,该层的特点如下:
1) Cr、Mn、O等元素明显偏析,有大量的夹杂物;
2) 该层的密度明显低于基体,切割后在加热炉内容易氧化,进一步形成夹杂物,导致分层更加恶化。
研究者都把分层的主要原因归结为Mn在凝固过程中出现较大的偏析,这也可以从图4中明显看出。
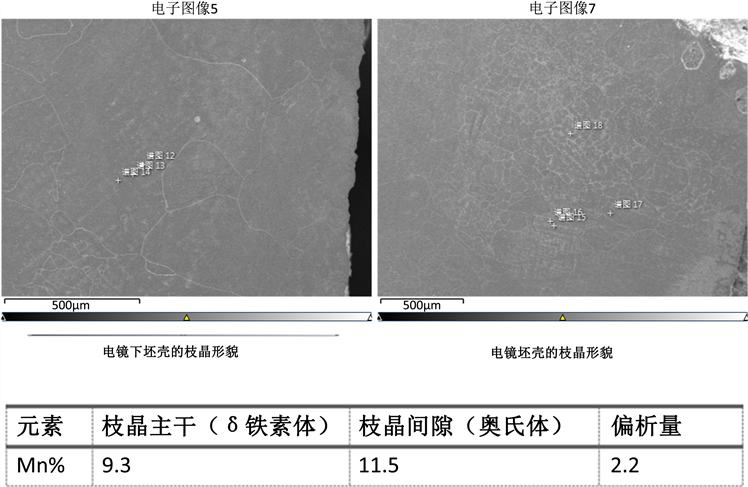
Figure 4. Mn segregation during the condensation process
图4. Mn在冷凝过程的偏析
图4中J2铸坯组织由网状或者树枝状铁素体以及亮块状奥氏体组成。具体的凝固过程为:
首先J2钢水液相中先析出δ铁素体,由于铸坯壳层的过冷度较大,铁素体以发达的树枝晶向液相中生长。凝固过程中发生了溶质再分配,铁素体生长过程中消耗大量的铁素体形成元素Cr、Si等,而使奥氏体形成元素如Ni、Mn、Cu等排挤到液相中,浓度不断增加。到凝固终了阶段,剩余液相中的铁素体形成元素贫乏,而奥氏体形成元素富集,导致铁素体生长受到抑制,剩余液相直接冷却得到奥氏体 [2]。实际检测到此时的Mn平均偏差达到20%。也就是说J2钢种在高锰的条件下,凝固末端更加恶化了锰的偏析,也是造成分层的主要原因。
根据相关文献 [6] [7] 报道,他们针对中厚板的分层问题,采用提高扇形段5~7段的水量,加快凝固末端的冷却,铸坯的表面温度明显降低,说明凝固末端冷却加快,可以减缓敏感元素Mn的偏析同时减少或消除了铸坯缺陷,从而改善了中厚板的分层问题。连铸环节在现有工艺基础上降低钢水浇注时的过热度(建议值1460℃~1470℃),中间包过热度控制在35℃以下;中厚板拉速控制在0.9~1.0 m/min;配水方案采用西重所推荐方案,加大凝固末端配水,如表4所示。
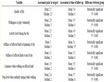
Table 4. Continuous casting water distribution used in the conditions of Xizhong
表4. 西重所推荐采用的连铸配水方案
前段将目标温度适度下调,以保证铸坯快速冷却,减小鼓肚的产生。在矫直段的目标温度适度提高,也可以避免产生过大的拉坯阻力,使铸坯在避开脆性区后尽量保持一定的温度直到出坯,使温度梯度平稳下降,减少热应力的产生。后续热轧中厚板未反馈有明显分层的现象。
4. 具体改进措施和工艺实施方案
根据以上对中厚板分层的机理分析,制订如下几点工艺的改进措施:
1) 连铸环节在现有工艺基础上降低钢水浇注时的过热度(建议值1460℃~1470℃),中间包过热度控制在35℃以下;中厚板拉速控制在0.9~1.0 m/min;配水方案应加大凝固末端配水。
2) 优化当前喷嘴,减少喷嘴喷水异常率(≤3%),使连铸机的二次冷却更加高效、稳定,避免出现造成中厚板分层的缺陷,如三角区裂纹、中间裂纹、中心裂纹、成分偏析、柱状晶发达等一系列内部缺陷时不能用作中厚板。
3) 水质(浊度 ≤ 10),减少喷嘴喷水异常率;水量总体增大,特别是扇形段5~7段进行强冷,弥补液芯的偏析。
4) 提高连铸设备精度,包括加垫片、调辊缝。