1. 引言
过去的几十年间,随着社会发展的加快,严峻的能源问题以及其引起的环境问题引起了各国的重视,太阳能、风能、水能等可再生的新能源的使用比例在快速上升。目前,全球能量来源依旧是以化石燃料为主,化石燃料在能源结构中占比均在83.1%以上 [1]。太阳能、风能、水能源等新能源受时间和空间的限制发展缓慢,假如将它们通过驱动水分解产生更易储存运输的氢能,可以很好的解决太阳能、风能等存在的间歇性、难储存的问题 [2]。
氢能具有能量密度高、可再生且燃烧产物清洁的优点,被认为是未来最具潜力的替代能源 [3]。目前,世界范围内每年生产的氢气中,96%的氢气都是由化石燃料制成的,这种制氢的方法会产生大量的CO2温室气体,污染环境 [4] [5]。电水解制氢相比于化石能源制氢,原料水丰富且可再生,并且水分解过程中无有害气体生成、效率高、产物氢气纯度高,因此电解水制氢成为了新能源研究的热点。
电解水制氢工艺主要在碱性和酸性介质中进行。酸性溶液作为电解质具有更加优异的能量效率,制氢速率更高。然而,酸性介质会腐蚀电解池和电反应设备,在酸性环境的制氢成本更高。虽然贵金属基材料在酸性介质有较好的活性,但是大多数过渡金属催化剂在强酸环境中是不稳定的。相比之下,过渡金属材料在碱性电解槽中有较好的催化活性,并且在相应的商业化技术得到了很好的发展。因此,促进碱性电解槽的发展对大规模制氢起着至关重要的作用。图1是碱性电解水工艺示意图,整个水分解的反应可以分为两个半反应,即析氧反应(OER)和析氢反应(HER),分别发生在电解池的阳极和阴极 [6]。析氢反应只需要转移两个电子–质子,析氧反应通过水的电化学氧化产生氧气,整个过程涉及四个质子和四个电子,通过多步质子耦合电子转移进行。析氧反应在动力学上很缓慢,不仅增加了电解水的能耗,更需要施加更大的电压驱动反应,降低了制氢的效率,大大限制了电解水在工业领域的应用 [7]。所以,需要有效的电催化剂来加速反应,减少过电位,从而提高能量转换效率。
目前已经成功开发出许多优良的碱性电解水析氧催化剂,但是它们大多数只适用于小电流的环境,在工业生产所需要的大电流密度下,其催化性能往往呈现快速下降的趋势,仍然无法满足商业化的要求:在1.8~2.4 V的电压下,电流密度达到200~400 mA/m2。所以,开发出能在500 mA/m2以上的高电流密度下,仍然能够保持稳定、高效的电催化剂,对于提高大规模电解水工作的效率有着非常重要的意义。
电解水制氢在能量储存与能量转换中具有重要意义,发展大电流析氧催化剂是提高工业制氢的重要方向。因此,有必要总结近几年的大电流析氧催化剂的发展情况,以推动该领域从实验基础研究走向工业应用。本文从电解水的原理出发,简要介绍在碱性环境条件下析氧催化剂的催化机理。总结了碱性大电流析氧催化剂的分类,并分别对近几年的贵金属基催化剂和非贵金属大电流析氧催化剂的研究情况做了分析和总结。最后,对当前大电流析氧催化剂面临挑战做了简要分析,并对未来的发展进行展望。
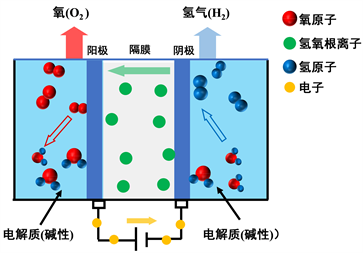
Figure 1. Schematic diagram of alkaline electrolyzed water process
图1. 碱性电解水工艺示意图
2. 析氧催化剂的催化机理
析氧催化剂主要是负载在阳极上,在电解池工作过程中可以加快阳极OER的速率和降低驱动OER的能量。析氧催化剂的原理包括降低阳极反应的能垒,促进中间产物的吸附,提高电子传递的效率等。
电解池在工作时,反应产生的氧气从阳极表面逸出。
工业生产中,为了降低能耗,通常以强酸或强碱溶液作为电解质。无论在何种介质中,发生一次析氧反应都需要转移四个电子和四个质子。碱性电解质下,催化位点可以两个吸附的O直接结合产生O2,也可以在催化位点形成OOH中间体。在OER过程中存在多个中间体(如O*、OH*和OOH*),导致难以确定速率控制步骤 [8]。
阴极:
(1)
阳极:
(2)
催化机理:
(3)
(4)
(5)
(6)
OER在标准条件下,即25℃和标准大气压下,析氧反应的热力学电位值都是1.23 V。然而,实际上电解池在工作过程中,总是需要施加更大的电位才能驱动阳极的析氧反应。超出部分(称过电位或超电势,η)主要是克服析氧反应固有的势垒以及溶液电阻(ηa和ηc)、接触电阻(ηother)等其他电阻 [9]。所以,要降低过电位,提高制氢效率,就是要降低ηa和ηc和ηother。其中,电阻可以通过设计电解池的结构来降低,而降低固有能垒的方法主要是负载高活性的析氧催化剂。所以需要开发出能够有效降低析氧反应能垒的阳极电催化剂。
3. 碱性大电流电解水析氧催化剂
大电流析氧催化剂通常可以分为贵金属基与非贵金属基(图2)。其中,虽然贵金属有多种,但其中作为析氧催化剂的主要是Ir基、Ru基和Pt基催化剂。而非贵金属基析氧催化剂分类方式一般是两种。按非贵金属的种类可以分为Co基、Ni基、Fe基、Mn基等析氧催化剂,按非金属元素的种类可以分为非贵金属氧化物、氢氧化物、硫化物、磷化物等析氧催化剂。

Figure 2. Classification diagram of high current oxygen evolution catalys
图2. 大电流析氧催化剂分类示意图
贵金属的氧化物在作为析氧催化剂时,具有最好的催化活性。但是,贵金属在地壳中的含量少,价格昂贵,且在长时间的电解过程中缺乏稳定性等,阻碍了电解水制氢技术工业化的进程。贵金属在所有pH条件下都表现出很好的OER性能,而非贵金属析氧催化剂则在碱性条件下更有研究的价值,所以碱性电解水催化剂受到人们的瞩目。
3.1. 贵金属基催化剂
贵金属催化剂的高成本影响了其在电解水制氢领域的应用,但由于其优异的性能,仍然广泛应用于制备电解水的阳极催化剂。对于大电流的贵金属基电催化剂的研究主要是通过掺杂、负载等方法,降低贵金属的用量,提高其利用率,并提高催化剂在高电流密度下的活性和稳定性。
3.1.1. Ru基催化剂
金属Ru在研究中表现出较好的析氢性能,但在析氧反应的过程中稳定性差。因此很少将Ru金属单独作为析氧催化剂使用。而RuO2则在驱动OER方面有独特的优势,在所有贵金属基析氧催化剂中,具有最高的OER活性。但是RuO2无论在酸性还是碱性条件下,RuO2的稳定性都很差。尤其在高电流密度下,RuO2会很快进一步氧化而使催化活性快速下降,不适用于在工业的长期大电流条件下工作。
在过去的几年中,Ru单质、Ru与其他一种或多种金属组成的合金、Ru的氧化物及其化合物在大电流析氧催化剂领域得到了广泛的研究。目前RuO2在大电流析氧催化剂方面的使用,主要是对RuO2纳米颗粒的尺寸、纳米结构、结晶度、晶型等进行调控,并负载在其他析氧催化剂上,提高催化剂的OER性能。Wu Dulan等 [10] 以在将Ru加入到钴基氧化物中,构建了掺入Ru的无定形钴基氧化物(Ru-CoOx/NF),合成了一种OER/HER双功能的非晶态电催化剂。它在1 M的KOH碱性介质中,只需要370 mV和252 mV的过电位就可以进行驱动OER和HER达到1000 mA/cm2的电流密度。而且,在组装好电解槽后,该电解池只需2.2 V的超低电压,就可以达到1000 mA/cm2的电流密度。
3.1.2. Ir基催化剂
虽然IrO2与RuO2相比稳定很多,但在长期大电流的刺激下,仍然存在组分与物质结构的变化,造成性能的衰减。Ir基电催化剂在析氧反应过程中一开始的是Ir(OH)3,经过一步去质子化的过程后,变为IrO(OH)2,然后IrO(OH)3会进一步氧化为IrO3,此时Ir为正六价。在之后的反应中,IrO3分为两个部分。一部分会还原成+3价的Ir离子,这就回到了最初的状态,并且会释放出氧气;另一部分的IrO3会再次发生氧化,以
的形式存在于电解质中,导致催化剂脱落。这部分的反应是人们不期望发生的,因为这会降低催化剂的活性和稳定性。
Ir基大电流析氧催化剂的研发思路和Ru基催化剂接近,研究者同样是针对单原子Ir、Ir的氧化物以及Ir各种结构的合金,包括纳米颗粒、纳米线、纳米棒等进行研究。或者是将Ir在其他材料(如非贵金属材料)上负载。Jiang Peng等 [11] 采用Ir改性金属有机框架(MOFs)前驱体的策略,将IrFe纳米合金支撑在掺杂N元素的碳片上,通过Fe原子的加入,改变了催化剂的电子结构。IrFe/NC催化剂只需850 mV的过电位就能提供1000 mA/cm2的电流密度,超过了最先进的商业贵金属催化剂Pt/C。
3.1.3. Pt基催化剂
Pt基电催化剂在碱性条件下的能量转化效率较高,是优异的析氢反应(HER)和氧还原反应(ORR)催化剂。无论是在酸性还是碱性条件下,Pt都被认为是最优异的析氢催化剂,暂时没有其他金属可以很好的代替Pt作为电解水的阴极材料。当Pt作为阳极时,发生的是氧还原反应。然而,Pt的氧化物属于惰性物质,且Pt基析氧催化剂的活性较低,一般不单独作为析氧催化剂。
基于上述原因,研究者们通常将ORR活性Pt基材料与OER活性材料(如优异的Ir基、非贵金属基析氧催化剂等)结合,实现双功能电催化剂的构筑。双功能电催化剂对两个半反应都具有催化活性,可以简化设备的结构,降低生产成本,在工业生产的大电流大规模条件下,显得尤为重要。Wu Jin等 [12] 用简单的自发氧化还原方法将Pt负载到CoFe(II)LDH催化剂上,利用催化剂的三维多孔结构和Pt纳米团簇与Co、Fe的协同作用,共同提高Pt-CoFe(II)LDH的催化活性和稳定性。在1 M的KOH电解液中,Pt-CoFe(II)LDH在500 mA/cm2的高电流密度下可稳定催化40 h以上。
3.2. 非贵金属基催化剂
贵金属及其氧化物,因为实际电流密度下的OER超电势低,所以他们在酸性和碱性环境下都表现出很好的OER催化性能。但是由于他们储量少且成本高的特点,使得他们商业应用上受到限制。因此,若可以用储量丰富、成本较低且耐腐蚀的非贵金属来完全代替贵金属在这方面的应用,则能使电解水制氢展现出巨大的可能性。
近年来,非贵金属(如Ni、Fe、Co等)基化合物,在催化OER方面,表现出优异的性能,不断向贵金属催化剂靠近。然而,要获得能够组装成工业电解槽的OER或HER电催化剂,使其能够在高电流密度(≥500 mA/cm2)下稳定工作,仍然具有挑战性。因为在高电流密度下,阳极上会形成大量的O2气泡。在这种情况下,气泡会在电催化剂和电解质界面上大量堆积,严重阻碍液体的传质过程,减缓了电子转移速率,也会减少催化剂上活性位点的暴露,最终导致催化剂活性和稳定性的下降。另外,在连续的大电流催化过程中,电极附近的离子和电子会大量消耗,若此时电子转移太慢导致反应的电子供应不足或电极附近离子浓度太低,会使电流密度下降 [13]。因此,除降低OER势垒以外,大电流析氧催化剂的设计还必须考虑电导率和对催化剂表面进行调控。
3.2.1. Co基催化剂
Co元素是一种储量丰富的三维金属元素,其氧化物、磷酸盐、硫酸盐等已被广泛用于大电流OER催化剂的制备,表现出良好的活性与稳定性。磷酸盐暴露在空气中易氧化,在实际应用的大电流情况下,表面总是覆盖氧化物层。将非贵金属氧化物和磷化物组合形成的多组分催化剂可以改善这种情况,并表现出更高的催化活性,更加符合大电流的使用条件。Zhang Xiaoyan等 [14] 设计了一种Co3O4/Fe0.33Co0.66P纳米界面,不仅增强了界面的催化活性,而且降低了水氧化过程中每一步反应的能垒,在大电流下,表现出惊人的稳定性。Co3O4/Fe0.33Co0.66P催化剂在800 mA/cm2的电流密度下,过电位为291 mV。并且,在240 mV的过电位下,进行了150 h的极化测试后,其电流密度损失可以忽略不计,晶体结构和形态保持良好,已经超过了许多贵金属催化剂的性能
3.2.2. Ni基催化剂
镍基催化剂是一种经济高效的水电解替代催化剂,因其具有低成本、固有的催化活性和储量丰富,被研究者认为是有潜力OER催化剂。同时镍的高导电性、热稳定性和良好的电学性能使它成为一种很好的电催化剂材料。通常,Ni在溶液以二价阳离子形式存在,但它的化合价可以在+1到+4间变化,使它可以实现多种电子跃迁。催化剂在电水解过程中的性能与其晶体结构、尺寸分布、化学组分、表面化学和电导率等有关,所以提高镍基催化剂的电催化活性的关键是调整其化学环境、结构和形貌 [15]。
目前开发的许多优异的大电流析氧催化剂很多都用到了镍元素,包括使用泡沫镍基底或是负载镍元素等。尤其可以考虑将Ni和Fe结合制备催化剂,这类催化剂比镍氧化物/氢氧化物具有更高的OER电催化活性,其在高电流密度下的应用受到广泛关注。Gao等 [16] 用一步电化学沉积法,在Ni丝复合电极上制备了S掺杂的非晶态NiFe2O4/Ni3Fe复合电极,具有出色的OER电催化活性。该电极达到500 mA/cm2的大电流密度,只需要提供285 mV的低过电位,且在500 mA/cm2电流中的催化性能可以稳定保持20 h。Zhu Weijie等 [17] 设计了NiFe/NiFe-OH双金属合金和氢氧化物核壳层电催化剂。由NiCo/NiCo-OH和NiFe/NiFe-OH组装而成的电解槽在碱性条件下只需要1.74 V的电压就能实现500 mA/cm2的水解电流,且该电解槽可在1000 mA/cm2下稳定催化300 h以上,远远优于目前商用的Pt/C和RuO2组成的电解槽。
3.2.3. Fe基催化剂
与Ni基、Co基电催化剂相比,Fe基OER催化剂的研究相对较少,一方面是由于还没有理论计算和实验结果可以明确Fe基电催化剂的催化机理,另一方面FeOOH的活性与电导率也并不高 [18]。Fe及其化合物很少单独作为电解水的催化剂使用,而是作为掺杂物加入到其他催化剂中。Fe掺杂到Ni基、Co基电催化剂中能有效的增强催化剂的导电性能、改变Ni和Co(氧)氢氧化物的结构,对增强OER催化剂有重要的作用 [19]。各项研究表明,Fe元素或多或少的掺入都可以有效提高催化剂的OER性能 [20]。
Zhou Haiqing等 [21] 报道了一种由Fe(PO3)2/Ni2P组成的镍泡沫电催化剂,在过电位仅265 mV和300 mV时,其电流密度分别为500 mA/cm2和1705 mA/cm2,具有优异的耐久性,可以用于大规模的商业化。Ren Jintao等 [22] 在泡沫镍上合成Ni(OH)2纳米片,然后将该电极置于含Fe3+的溶液中,得到具有特殊纳米结构的Ni(OH)2-Fe/NF电极。Fe的掺入引起了部分电荷转移,从而极大地改变了Ni(OH)2的电子结构,促进了电极对OER和HER的电催化活性。该电极在330mV的过电位下,电流密度为1000 mA/cm2,并且可以在1100 mA/cm2的电流和1 M的KOH电解液中,稳定工作至少10 h。Ye Qinglan [23] 用简单的水热法合成NiFe片阵列作为电催化剂。NiFeLDH纳米阵列在255mV和284 mV的过电位下,电流密度分别为500 mA/cm2和1000 mA/cm2,并且1 M的KOH电解液和750 mA/cm2的电流下能够稳定工作超过40 h。
3.2.4. Mn基催化剂
Mn基电催化剂也是人们广泛研究的对象。构建纳米结构和提高亲水特性,可以加速气体的逸出和增加活性位点的数量,这在大电流密度条件下显得尤为重要。Tang等 [24] 在泡沫镍上构建了形态、成分可控的碳酸钴锰(CoMnCH)纳米片阵列,且可作为双功能电催化剂。Mn掺杂同时调节纳米片的形态和Co中心的电子结构,从而显著增加了催化剂电化学活性。CoMnCH/NF电极也具有有利于传质过程的纳米结构,其在1000 mA/cm2电流密度下的过电位为462 mV。Liu Hao等 [25] 合成了一种柔性自支撑纳米多孔NiMnFeMo合金(np-NiMnFeMo),其在高电流密度下表现出优异的HER和OER性能,尤其是HER活性(达到1000 mA/cm2的电流密度时,HER的过电位为290 mV,OER的过电位为570 mV)。密度泛函理论计算表明,np-NiMnFeMo如此优异的HER活性是由于固溶体元素的协同作用。在反应过程中,Ni原子充当水的离解中心,而其它金属元素(Mn、Fe、Mo)起到了调节电子结构和促进氢的吸附的作用。Qin Chunlin等 [26] 将Ni、Mn、Ce分别掺杂到Co基氧化物纳米阵列中,通过水热合成法在碳纤维纸(CFP)上生长CoxM1-xO4 (M = Ni、Fe、Ce)。结果表明,CoNiO-NWs/CFP电极表现出最佳的OER性能,可以在1000 mA/cm2的大电流下持续工作约130 h,而Mn和Ce的掺杂反而降低了原本Co3O4纳米线的OER活性。他们的研究充分说明,在高电流密度下,纳米阵列电极的失活机制不同于传统的金属氧化物电极。
3.2.5. Cu基催化剂
铜元素有丰富的价态,Cu2+可以氧化为Cu3+和Cu4+,也可以还原为Cu1+和Cu单质,且在地球上储量充足,所以近年来,Cu基材料在大电流析氧催化剂方面的应用也受到研究者大量的关注。各种非金属元素的掺入可以改变晶体结构和对原子的吸附能力,从而促进催化剂表面的反应,在大电流析氧催化剂的开发中有重要应用。如,硫的掺入可以促进对氧原子的吸附能力。Zhang Xian等 [27] 通过简单的两步法,在负载了CuNi合金的泡沫镍(CuNi/NF)上原位生长CuS-Ni3S2。通过该方法得到的阳极,只需在该电极上施加444 mV和510 mV的过电位就可以使电流密度达到500 mA/cm2和1000 mA/cm2。
3.2.6. 双金属基催化剂
双金属基析氧催化剂一般由两种金属的化合物为主要组成,并通过掺杂其他元素、调控结构等手段进一步提高催化剂的性能。由于金属间的协同效应,双金属基催化剂一般具有优异的OER性能。双金属基催化剂通常选择两种非贵金属或者一种贵金属加一种非贵金属。大量研究表明,Fe和Ni之间的耦合效应是最强的,在所有非贵金属基析氧催化剂中,镍铁基析氧催化剂(包括NiFe氧化物、氢氧化物、层状双金属氧化物以及NiFe合金等)表现出最佳的综合性能。即使是纯Ni或Fe基的电催化剂,其催化性能也明显低于镍铁基电催化剂。这是由于结构相似的Ni、Fe原子间存在相互作用,可以调剂活性位点附近的电子结构,并改善析氧反应的动力学过程。Liu Peng等 [28] 借助NixFe1−x合金纳米锥阵列(存在2 nm左右的NiO/NiFe(OH)2表面层)来改善反应物的转运。利用优化后的合金制备的电极显示出优异的OER性能,只需施加255 mV的过电位就可以达到500 mA/cm2的大电流。
掺杂非金属元素的方法广泛被研究者用来提高催化剂性能,常见的掺杂元素有P、S、N等。另外,也有一些报道的析氧催化剂掺杂了B、Se、Te等非金属元素,并且表现出优异的催化性能。非金属元素通常具有丰富的价态,可以改变催化剂的电子排列结构和导电性,并影响催化剂的微观形貌和组成成分。在电解水过程中,阳极材料处于强氧化性的氛围中,非金属元素会被氧化为酸根离子,促进电荷的转移和反应中间产物的形成。Zou Xu等 [29] 通过简单的两步法合成了Ni-Fe-OH@Ni3S2/NF电催化剂。它由非晶镍铁双金属氢氧化物薄膜涂层和泡沫镍泡沫支撑的Ni3S2纳米片阵列组成,在1 M和30 wt%的KOH溶液中都表现出非常优异的析氧催化性能。在30 wt%的KOH溶液中,Ni-Fe-OH@Ni3S2/NF只需要370 mV、469 mV和565 mV的过电位就可以驱动电流密度分别达到500 mA/cm2、1000 mA/cm2和1500 mA/cm2。Cheng Xiaodi [30] 将Fe2O与通过热磷化反应生长Ni泡沫上,制备一种新的三维三元杂化电催化Fe2O3@Ni2P/Ni(PO3)2/NF。由于Fe2O3@Ni2P/Ni(PO3)2/NF之间的协同效应和它们的强耦合效应,3D Fe2O3@Ni2P/Ni(PO3)2/NF杂化物在碱性电解液中在超高电流密度下实现了优异的电催化OER性能。催化剂在1.0 M KOH,1.57 V和1.60 V的极低电位达到500和1000 mA/cm2的超高电流密度。
3.2.7. 三金属基催化剂
除表面工程外,多金属的集成是改善催化剂性能的常用方法。引入多种金属可以调节催化剂的电子结构。Yan Gang等 [31] 报道了一种尖晶石型三元多金属混合氧化物(NiO-Fe3O4@NiCo2O4),由于在泡沫镍上生长,它还具有多孔的层次结构。通过尖晶石型结构促进电子转移过程,分级多孔结构促进传质过程,再加上多金属的协同作用,这种材料表现出令人讶异的电催化活性和长期使用的稳定性,只需要250 mV的超小过电位就可以达到1000 mA/cm2的大电流密度,在1500 mA/cm2的大电流下能够保持100 h以上。
4. 总结与展望
电解水制氢技术作为一种高效的获得清洁可再生氢能的手段,被期望能改变目前利用天然气重整、煤气化或甲醇制氢等传统技术来获得氢能的现状。近几年研究者对电解水的基础理论和高效催化剂做了更深入的研究。综上所述,贵金属材料是OER最有效的催化剂,但稀缺性和高成本很难在工业上大规模使用。在碱性的生产环境中,非金属析氧催化剂更具优势,使用范围更加广泛。在提高OER催化活性方面,主要围绕增加催化剂的固有活性点和增加暴露的活性点数量。催化剂的内在活性可以通过相位工程、缺陷工程和多金属工程来提高。而通过制备特殊结构,如纳米结构、核壳结构,以及在三维的基底上生长来处理催化剂可以暴露更多的活性位点,提高制氢效率。近年来,OER催化剂的研究和设计已经取得了很大的进展。但是大多数析氧催化剂仍然局限于100 mA/cm2以下的低电流密度,对于大电流析氧催化剂的研究还处在起步阶段。目前,大电流析氧催化剂的研究中存在的问题与挑战主要是以下几个方面:
1) 在高电流密度的电解水过程中,质量传递成为反应速率的决定步骤,需要快速供应电解液和逸出气体。连续的大电流催化过程中,电极附近的反应离子大量消耗,此时电子转移太慢导致反应的电子供应不足,使电流密度下降。另外高电流下阳极产生的大量气泡粘附在催化剂表面,堵塞活性位点,同样导致电流密度下降。在这些方面,一些大电流电催化剂的传质性能没有得到充分的重视,尤其是以粉末形式存在的催化剂。
2) 电解水的反应是涉及气相(反应产物)、液相(电解液)、固相(电极、催化剂等)三相的过程。超疏氧或超亲水三维多孔结构在促进气体的快速逸出方面很有前景,但如何设计和调控阵列微观结构以获得优异的超疏氧/超亲水性能,还有待进一步研究。
3) 要设计出最佳的组成与结构形貌的析氧催化剂,必须更清楚的了解每种成分的作用与其原理,明白整个催化过程中起决定作用的因素。而目前包括Fe在内,一些元素掺杂的机理以及很多析氧催化剂在使用时的中间产物吸附机理还没有得到具体明确的解释。
4) 稳定性是限制碱性电解水工业化发展的关键因素。在长时间的大电流析氧反应过程中,催化剂容易转化为其他的活性物质并溶解在电解质中,逐渐从电极表面脱落,或者由于气体不断快速逸出使阳极表面活性物质脱落,造成性能的下降。而且在实际的工业生产中,溶液的pH、催化剂表面的氧化等可能并不能像在实验室中那样精确控制,而使催化剂不能如预期的那样稳定。因此,如何提高析氧催化剂在大电流下的稳定性仍然需要不断的研究。所以,优异的大电流析氧催化剂的开发对于电解水制氢技术在大规模工业产氢中的应用有重要的意义。
目前商用的贵金属基析氧催化剂由于昂贵的价格和工业电解条件下的不稳定性,正在逐渐被一些优异非贵金属基析氧催化剂取代。非贵金属基析氧催化剂的研发思路已经从原先的金属领域,到非金属领域,甚至到了聚合物领域,通过中间产物吸附效应、晶格氧介导效应、多金属的协同效应等,已经有非贵金属基催化剂表现出比单金属铂族催化剂更优异的催化活性和稳定性。然而,虽然目前在析氧催化剂的研究方面已经取得一定的进展,新的优异催化剂的相关报道也不断出现,但大电流析氧催化剂的研发还存在瓶颈,距离真正实现工业化的使用还有较长的距离。当前对于大电流析氧催化剂的设计没有考虑固体电极和液体电解质之间的浸润性,且催化剂的活性面积还有待提高。
针对这些方面和上述提到的大电流析氧催化剂研究中存在的问题,未来对于大电流析氧催化剂的研究工作包括以下几个方向:1) 利用惰性的聚合物基底,改善目前析氧催化剂普遍存在的稳定性问题。另外,聚合物基团的多样性可以赋予整个析氧阳极更加优异的性能,比如,亲水基团对实现阳极材料的超浸润性有重要作用。2) 增大催化活性面积,不仅仅是从负载催化剂粒子的尺寸、均匀性方面,还有通过3D打印等相关技术,从基底载体到催化剂整体设计,构筑整个阳极的结构。3) 模拟工业生产中的条件(如大电流、高温、高浓度电解液等),组装电解池,使析氧催化剂的性能测试结果更加接近实际应用中的表现。4) 结合理论计算和各种先进的表征手段,分析各种组分、结构对催化剂的影响的机理,进而归纳出对催化剂性能提高最有力的一些因素和条件,为未来新型先进的析氧催化剂的制备和优化提供理论和实验依据。总而言之,高效、稳定的大电流析氧催化剂的研发是实现电化学技术在能源领域取得突破的关键,也将会在其他多个领域发挥重要作用。
NOTES
*通讯作者。