1. 引言
烧结工序是钢铁联合企业的污染及耗能大户,目前国内烧结机都是抽风式烧结,采用负压抽风的方式从台车自上而下进行烧结。烧结风量分为有效风量和有害漏风,集中由主动力主抽风机负压抽取进行作业,其中通过料层的风量为有效风量,而从料层以外进入抽风系统的风量称之为有害风量。烧结机的有害风量的多少直接影响了烧结矿料的质量,并且决定烧结终点是否能在预定的区域内完结,减少矿料在烧结后出现烧结生料进而返回进行二次烧结的资源浪费问题。目前部分烧结机作业时,有害风量即烧结机实际漏风率高达60%,此问题已变为烧结领域的难题,进而严重影响烧结机生产水平的提高。烧结机漏风率升高造成烧结机机头主抽风机处理烟气量增大,配套脱硫脱硝系统运行负荷升高,大幅增加了生产成本,严重制约了钢铁企业的绿色发展。
2. 攻关技术方向
中厚板公司多次与周边钢铁企业多台烧结机进行对标分析,共同探讨研究烧结绿色发展之路,主要从两个技术方向进行技术攻关。
2.1. 烧结机实施漏风治理降低有害漏风
据分析烧结机有害风量主要有机械漏风及滑道润滑漏风两大主要方向,结合现场实际主要通过实施以下新技术治理,优化配比实现中厚板公司2台210 m2烧结机漏风率由58%降至35%。
2.1.1. 靶向定点定量完成系统整体机械密封
主要包括对210 m2烧结机实施机头、机尾整体密封;风箱的设备更换、修补;台车的封堵漏风治理、卸灰阀封堵、膨胀节漏风封堵等整体系统机械密封。
2.1.2. 新型的滑道自润滑密封系统有效应用
采用滑道自润滑密封系统,有效治理台车游板与滑道之间的漏风。
2.1.3. 通过监视测量方式试验最佳料层厚度及配比
在漏风治理完成后,通过监测方式优化配料结构配比,确定最佳提高料层度及配比,实现提产降耗。
2.2. 采用新技术控制烧结机烟气外排量
综合分析烧结机烟气特性,拟采用烧结机烟气循环技术实现减少烟气外排量。烧结机烟气循环是将烧结过程中排出的一部分载热气体返回烧结点火器以后的台车上再循环使用的一种烧结方法。通过热烟气的循环,减少了外排烟气量,降低了烟气净化设施的负荷,又回收了烧结烟气的余热,提高烧结的热利用率,降低燃料消耗。
通过以上技术地实施及改造,实现中厚板公司2台210 m2烧结机提产降耗减排创效多赢。
3. 技术方案和创新成果
烧结机降本增效的治理以“降成本,提产量”为主线,其治理工作主要分为两方面:1) 烧结机总体的设备改进、修补;2) 生产工艺影响的相关配料改进和设备改造。以“一线两面”为主导,对烧结生产设备、生产工艺进行多方位深度挖掘。为了降低烧结矿成本,烧结工序多次进行对标分析,查找自身存在问题,增产降耗主要攻关两个技术方向:一采取有效措施降低烧结机漏风率,降低有害漏风;二采用新技术控制烧结机烟气外排量,降低配套脱硫脱硝系统负荷。
3.1. 烧结机实施漏风治理降低有害漏风
据分析烧结机有害风量主要有机械漏风及滑道润滑漏风两大主要方向,结合现场实际主要通过实施以下新技术治理实现2台210 m2烧结机漏风率有58%降至35%。
3.1.1. 靶向定点定量完成系统整体机械密封
主要包括对210 m2烧结机实施机头、机尾整体密封;风箱的设备更换、修补;台车的封堵漏风治理、卸灰阀封堵、膨胀节漏风封堵等整体系统机械密封 [1]。
1) 机头机尾漏风治理
烧结机机头机尾由于烧结机使用年限过长磨损比较严重漏风较大,烧结机使用四连杆横向接触式头尾密封结构,该密封装置密封板由7块500 mm宽密封板平铺构成,每块密封板由中间支撑板和滚轮、支撑板和支座铰接连接,密封板靠重锤复位。当台车运行到密封板时,台车地面与密封板表面接触导致密封板上下活动时,若活动密封板由于进入物料不能及时复位,密封板间将会在垂直方向上错位,台车地面与外界连通,漏风加剧,密封效果差。为减少机头机尾漏风,更换为柔性涡流机械金属密封,此设备主要由上下两密封箱体组成,上下两箱体之间由不锈钢波纹补偿器密封,靠安装在箱体内部的弹簧复位,上箱体表面安装横向交错耐磨衬板,当台车行进至密封板时,密封板与台车底面形成涡流,有效的避免漏风。
2) 台车相关漏风治理
烧结机台车本体及栏板使用中无损坏,但是仍存在四点漏风问题:台车体两侧长期运转磨损严重,造成台车与台车之间有缝隙,发生漏风;台车体与栏板接触位置为平面设计,存在密封不严,发生漏风;台车两块栏板间接触面为平面设计,存在密封不严,发生漏风;台车压轴销销杆为等直径圆柱设计,销杆与台车销孔间隙较大,存在密封不严,发生漏风。为减少以上三类漏风,烧结工序为此返修全部台车,台车恢复原尺寸,台车体两侧加装耐磨板,使其台车与台车之间紧密结合;改变台车体与栏板之间接触结构,台车端头增加凸起,栏板处增加凹槽,使之交错结合,两栏板之间同样采取交错结构,采取类似迷宫密封;换用新式压轴销,安装时易将圆台状的一端插入烧结机台车销子孔中,而圆柱段的圆柱面与烧结机台车上的箅条销子孔的配合间隙较小,减小了销孔处的漏风。
3) 风箱的设备更换、修补
a) 梯形箱体、锥斗的修补、涂抹
梯形箱体位于台车下方,主抽风机工作时该位置负压较大,同时存在连续高温环境,又受长时间粒度料冲刷,涂抹部分有掉落,箱体、锥斗、横梁、纵梁存在多处破损,纵梁全部更换,用以支撑滑道,箱体重新用锰钢板制作焊接,表面涂抹陶瓷耐磨料。
b) 烧结机16米风箱补偿器、直管更换、修补
设备长时间运转加之粒度料长期冲刷,风箱补偿器、直管出现破损,为此更换新式补偿器并补焊加厚直管部分。
4) 主机烟道、灰斗、双层卸灰阀漏风治理
对主机烟道内部修补,内村涂抹耐磨料,烟道灰斗连接处和灰斗进行修补处理。双层卸灰阀密封不严处进行修补,严重位置进行卸灰阀更换。同时对设备法兰连接进行更换紧固处理。
3.1.2. 新型的滑道自润滑密封系统有效应用
浮动密封板与台车滑道之间接触不好,很容易造成系统漏风。浮动游板和游板槽之间的3毫米的间隙和游板弹簧使用过程中失效是导致原有结构漏风的重要因素。
在不改变烧结机的主体结构,目前烧结台车基础上去掉原有的游板,在该位置安装水平动合金板;取消滑道并且降低滑道支撑梁的高度,在该位置安装滑道自润滑密封系统。滑道自润滑密封系统由自润滑密封板(减少运行阻力、提高使用寿命)、侧密封、限位装置、弹性支撑机构、基础支持等部分组成。使动、静密封装置依靠弹性压力可以紧密贴合在一起,该金属静密封装置在限位装置与弹性支撑的作用下可以稳定的与台车下动密封始终贴合,保持良好的密封效果,阻止粉尘通过。同时在侧面装有不锈钢密封板,阻止粉尘进入系统内。由于是全金属自润滑密封装置 [2],解决了耐高温和润滑油脂消耗难题,设备免于维护,并能确保密封性能始终处在良好的状态下运行。同时减少因现场漏风量大出现的噪音。
3.1.3. 通过监视测量方式试验最佳料层厚度及配比
1) 优化配料结构
为了降低烧结矿成本,烧结工序发挥临港优势,根据物料性价比和生产经营条件的变化优化配矿结构,主要烧结用铁矿粉成分详见表1,目前已开始逐渐降低地方精粉配比至全部停用,主要只配加5%左右的南非PMC调整烧结矿中钛含量,配料精粉率由16%降至7%左右;提高外矿低品粉的比例,减少中品粉比例,低品粉主要品种是一钢粉、火箭超特粉、麦克粉、阿特拉斯粉和FMG混合粉,中品粉主要品种是金布巴粉、PB粉和BRBF粉。选择性价优的一钢粉替代部分BRBF粉,麦克替代部分PB粉,在品位允许的前提下,可以适当配加部分火箭超特粉和阿特拉斯粉等低品粉,整体优化配料结构。主要低品位矿粉重点成分对比详见图1。
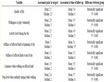
Table 1. Main compositions of iron ore fines for sintering
表1. 主要烧结用铁矿粉成分

Figure 1. Comparison of key components of main low-grade ore fines
图1. 主要低品位矿粉重点成分对比
实施变料前后,我们根据对各种物料的冶金性能分析比对,冶金性能包括单品种物料的熔点、液相流动性等指标,可以理论比对变料前后对烧结过程中的影响,调整生产控制参数,减少变料后生产影响。提高低品粉比例,降低高品粉比例,因低品粉含结晶水高,为保证烧结矿转鼓强度,提高燃料比,固体燃耗相应的升高,对各配料结构烧结矿指标对比,对比结果详见图2。
1#、2#烧结有计划的减少地方精粉配比以提高烧结透气性;低品粉由2020年的15.91%逐步增加配比至24.98%以上,高品粉由18年的38.71%逐步降低配比至30.08%。9月份一、二号烧结机漏风治理完成后,优化配比,料层厚布,利用厚料层自动蓄热作用可以降低固体燃耗,在保障烧结矿品质质量的基础上实现提产。
2) 提高混合料初始料温
混合料温度对烧结生产的影响较大,将混合料温度提高到露点温度以上有利于改善过湿现象,提高料层透气性,从而提高烧结矿产质量。同时混合料温度的提高,还可降低烧结固体燃耗的消耗,降低工序能耗。1#、2#烧结机改善提高措施为泥浆池通入蒸汽,对提高一混混合料料温有一定作用。
在一混或二混滚筒中通入蒸汽提温后要经过数条皮带,在皮带运输过程会造成热量损失,最终确定在混合料槽“方段”位置安装蒸汽补偿设备,利用环冷余热过饱和蒸汽通入混合料槽对混合料进行热交换,提高混合料温度。混合料槽蒸汽投入后,24小时现场指导岗位提前控制混合料水分,防止混合料水分过大造成混合料槽悬仓;指导岗位控制混合料槽仓位在15~25吨之间,可使蒸汽能够充分利用;要求倒班作业区每班清槽一次,克服了因混合料槽通蒸汽造成粘仓影响烧结布料。。经核算1#、2#烧结机混合料槽通入蒸汽后,每台烧结机每天产量提高200吨。
3) 提高烧结料布料厚度
烧结机受设备影响,1#、2#烧结机布料厚度设计为750 mm,从工艺角度考虑,厚料层布料有利于强化烧结自动蓄热作用,提高烧结矿产质量,因此对设备进行改造,在九辊疏料器后面增加梯形布料装置,聚拢台车边缘混合料,同时提高布料厚度,装置加装后,混合料布料厚度提高至800 mm,烧结矿质量得以保证。
4) 提高混合料水分
烧结料中水分含有结晶水和物理水,前者主要来源于矿粉自身,后者来源于物料的外来添加水。混合料加水主要是有助于混合料成球、制粒,改善料层透气性;其次是在烧结过程中,水分有吸热、传热功能,能有效改善或增加料层的热交换条件。如混合料水分较小时,混合料成球效果不好,经烧结台面负压抽风后造成台车料面压实,风向负压相对升高但透气性变差,降低烧结矿产量。因此在进行漏风治理后烧结漏风率减小的情况下,适当加大混合料水分,提高混合料成球效果,将混合料水分由7.0提高至7.3。当混合料槽使用蒸汽余热装置来提高料温时,因蒸汽中含有的水分对混合料水分产生一定的影响,在生产过程中我们一般都是在保证烧结料水分稳定的前提下尽量加大蒸汽量来提高料温 [3]。通过数据可以看出,当混合料温度提高至60℃以上时,混合料水分要提至7.5%,过湿层的含水量是下降的,从而提高烧结料层的透气性,提高产量。
3.2. 采用新技术控制烧结机烟气外排量
综合分析烧结机烟气特性,拟采用烧结机烟气循环技术实现减少烟气外排量。烧结机烟气循环 [4] 是将烧结过程中排出的一部分载热气体返回烧结点火器以后的台车上再循环使用的一种烧结方法。通过热烟气的循环,减少了外排烟气量,降低了烟气净化设施的负荷,又回收了烧结烟气的余热,提高烧结的热利用率,降低燃料消耗。一是可回收烧结烟气的余热,提高烧结工序的热利用效率,降低固体燃料消耗。二是这部分废气中的有害成分将在烧结层中被热分解或转化,二噁英和NOx会被部分消除,抑制NOx的生成,粉尘和SOx会被烧结层捕获,减少了粉尘、SOx的排放量,烟气中的CO作为燃料使用,可降低固体燃耗。
另外,通过烟气循环利用减少了烟囱处排放的烟气量,减小了终端处理负荷,可提高烧结脱硫装置的脱硫效率,降低脱硫装置的规格,减少脱硫脱硝装置的投资。脱硫脱硝不用改造就可以提高排放标准 [5]。
采用烟气循环工艺的节能作用主要体现在节省固体燃料和节电两个方面。结合中厚板公司2台210 m2烧结机现场实际状况,综合比较内循环和外循环两种工艺的技术及适用性,2台210 m2烧结机采用烟气循环采用外循环 + 内循环模式。
主要实施方案是将主抽风机排出的大约30%以上的烟气引回到烧结机上的热风罩内,剩余约60%~70%的烟气外排。热风罩将烧结机大部分罩起来,在烧结过程中为调整循环烟气的氧含量,鼓入少量新鲜空气与循环废气混合。这样,仅须对外排的约70%的烧结烟气进行处理,灰尘等污染物可相对减少,使其达到环保排放要求。采用烧结机主排烟气部分外循环方式,使部分含有氮氧化合物和硫化物的烟气经过燃烧层继续燃烧,总烟气量中始终有一部分烟气在系统内部循环,不外排放,降低脱硫脱硝系统的运行负荷,减少外排污染物总量及脱硫废物的产生量。
4. 实施效果
2021年中厚板公司从管理上对标找差距,探讨研究烧结绿色发展之路。主要攻关降低烧结有害漏风及采用新技术控制烧结机烟气外排量,通过漏风全面治理与采用烧结机烟气循环技术的实施,对生产数据、治理数据、等相关数据进行列统分析,实现了烧结机生产连续稳定,利用系数提高,日产量由6000 t提升至7000 t,吨烧结矿固定费用及电耗显著降低,通过技术漏风治理改造及采用烟气循环等技术手段来提高烧结矿产量,从而带来的年经济效益为1943.256万元。在保障脱硫脱硝出口外排污染物稳定达标排放的基础上,保障区域环境质量的前提下,实现了减少脱硫脱硝系统的运行负荷,降低脱硫脱硝系统的运行成本,减少脱硫脱硝系统副产物产生量,固体废弃物处置安全可控;同时减少了设备的维护及人工成本,实现了经济效益、社会效益与环境效益的多赢局面。