1. 引言
KR法铁水预处理脱硫技术是指铁水兑入转炉之前对其进行脱除杂质元素或从铁水中回收有价值元素的一种铁水处理工艺,是冶炼纯净钢以及提高钢材产品质量的一种较为有效的方法。KR搅拌脱硫以其脱硫效率高、脱硫剂消耗低、作业时间短、金属损耗低等特点受到了钢铁冶金科技工作者的广泛关注。目前炼钢工序铁水全部进KR进行脱硫处理,由于原有粉状脱硫剂的粒度在200目左右,在实际使用中被除尘设备吸走较多,且此种脱硫剂比重小,易浮在铁水表面,造成脱硫剂利用率低,影响脱硫效果。另外,由于入厂铁水条件波动大,尤其是硅高炉次转炉操作时易产生喷溅,对转炉冶炼、生产组织、工序成本影响较大,针对目前的技术条件,开展自主科技创新活动,逐步形成了一套较完善的KR法铁水预处理工艺控制技术。
2. 现有工艺限制性环节
1) 采用鱼骨分析法,对影响脱硫效果的因素分析见图1。
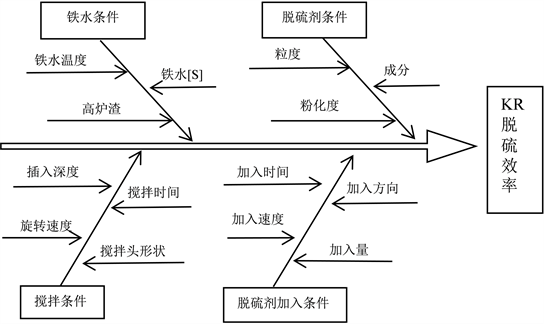
Figure 1. Analysis of influencing factors on KR desulfurization
图1. KR脱硫影响因素分析
从上图中看出,由于受铁水条件波动、脱硫剂质量波动、搅拌及加入参数不合理等原因,脱硫效果波动较大,脱硫效率偏低。
2) 受高炉炉况影响,入厂铁水硅含量在0.20%~1.8%,且无有效脱硅技术手段,硅高炉次转炉易产生喷溅。
3. 开发颗粒脱硫剂技术
3.1. KR法铁水脱硫机理研究
KR法铁水脱硫机理示意图见图2所示 [1]。
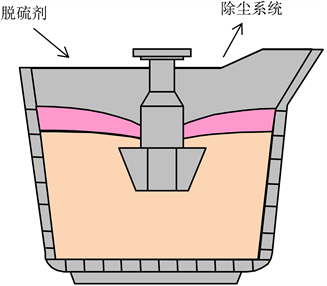
Figure 2. A sketch of KR desulfurization
图2. 铁水KR法搅拌脱硫示意图
在使用CaO基脱硫剂进行铁水脱硫过程中,一个突出的问题就是脱硫反应产物中有游离的氧产生,即有如下反应发生:
(1)
[O]离子与Si发生反应生成高熔点的2CaO·SiO2,在冶金石灰表面形成薄膜,阻止脱硫反应继续进行,降低CaO的脱硫效率及有效利用率。一般情况下认为铁水脱硫反应按如下公式反应。
(2)
在铁水中,可能也有C、Si参与脱氧反应,其脱氧反应方程式如下:
(3)
(4)
根据上述反应式标准自由能变化,不难发现在1500℃以下,碳不参加脱氧反应。另外现场铁水成分化验统计数据也表明,脱硫前后铁水碳含量基本不变。
一般情况下铁水中的
,而
,碳含量几乎比硅含量多一个数量级,且并没有明显的证据表明高硅铁水比低硅铁水脱硫更难,所以有人认为,铁水中发生的主要反应是下式。
(5)
仅就热力学角度看,各种不同元素有优先氧化还原顺序,但考虑到浓度差别、局部能量起伏及反应速度等综合因素,上述(2)、(5)两式能够同时发生。另外,CaO脱硫早已是个不争的事实,但CaO脱硫的限制性环节至今在业内尚未达成共识。有人认为,由于铁水脱硫是固–液反应,基于未反应核理论,S在CaO颗粒中扩散是脱硫反应的限制性环节;也有人认为,因CaO粉剂在铁水中停留时间短(喷吹法估测5~6 s)。根据双模理论,S通过液体边界层向CaO颗粒表面扩散是脱硫的限制性环节 [2]。
但从动力学角度来看,因为KR法脱硫过程是固态石灰与铁水中硫之间的多相反应,有研究人员提出混合限制性环节联合控制概念,其中包括复杂的传质过程和界面反应,大致有5个环节组成,即:[S]通过脱硫剂颗粒表面和铁液边界层向反应界面扩散,[S]与[O]的界面反应,[O]离开反应界面通过铁液边界层向铁液内部扩散,[S]穿过CaS产物层向脱粒机颗粒内部扩散,石灰内部[O]穿过CaS层向反应界面扩散,其反应模型 [3] [4] 如图3所示。
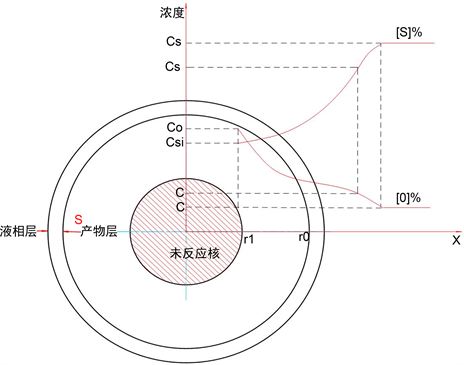
Figure 3. Reaction model of KR desulfurization
图3. KR法脱硫反应模型
在1400℃的铁水温度下,界面之间化学反应速度很快,不是脱硫过程的限制性环节。基本可以确定:在反应初期,第一、第三步外扩散制约反应的进行,其中氧比硫在铁液中的扩散系数高1个数量级,因此第一步是过程的制约因素,反应中期为内扩散和外扩散的混合制约阶段,反应后期第五步固相扩散是限制性环节。
3.2. 颗粒脱硫剂开发
需要着重指出的是,不论限制性环节在哪里,增加颗粒的表面积、延长颗粒在铁水中的停留时间及加快固–液表面更新速度都是提高脱硫效果的努力方向。因此通过统计研究,依据现有铁水实际条件,开发钙基颗粒脱硫剂,并在生产中推广使用。钙基颗粒脱硫剂理化指标见表1。
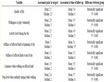
Table 1. Physicochemical parameters of pellet desulfurizer
表1. 颗粒脱硫剂理化指标
1) 设备选型
根据工艺技术需求,选用石灰筛分设备、颚式破碎机、运输皮带、滚筒式包膜机、链条提升机等主要设备。
2) 颗粒石灰包膜工艺
颗粒脱硫剂使用的活性石灰在正常生产后若不采取有效措施,极易在加工、运输环境中受潮,吸收空气水分产生粉化变质,为此研制开发了一套颗粒脱硫剂包膜钝化技术,其中根据颗粒脱硫剂特性采用硅胶粉作为主要钝化剂。
为了使石灰颗粒充分达到防水钝化和不损害石灰颗粒粒径,经过选用不同混料设备,对比产品成型效果,最终确定采用圆形滚桶包膜机。它的特点是可以使硅胶粉和石灰颗粒充分在无外重力情况下吸附硅胶粉,使颗粒表均匀的形成防水膜。
4. 开发搅拌深度自动测量技术
KR脱硫用搅拌桨作为搅拌脱硫动力学条件改善的动力源泉,搅拌桨的转速、插入深度、搅拌桨形式对脱硫效率均会造成极大的影响,尤其是搅拌桨插入深度,对于铁包内的流场起到决定性作用,但对于搅拌桨插入深度,虽然没有一个通用明确的区间,但均表明了其对脱硫率具有决定性作用。
通过数值模拟及现场工业试验表明,当搅拌桨插人深度与铁水液面深度之比为0.287时,也即插入深度为900 mm时(搅拌桨插入铁水液面以下距离),其上下环流循环分界面约为z = 1/2 H,此时,上下两环流区域大小大致相同,搅拌效果均匀。而且通过试验发现,当搅拌桨插入深度为900 mm时脱硫效果最好,与上述研究结果一致。但现实中存在插入深度计算不准确问题,原有工艺主要靠目测铁水罐净空值,然后根据经验值设定插入深度,无法实现准确设定插入深度,造成搅拌效果波动大,为此开发铁水插入深度自动测量计算技术。此技术原理为通过采用液位计对到位后的铁水罐进行净空自动测量,数据传至电脑后根据模型计算出插入深度。现场操作见图4、图5。
通过对搅拌桨插入深度准确计算,进一步稳定了铁水搅拌效果,从而有效提高了脱硫终点命中率。
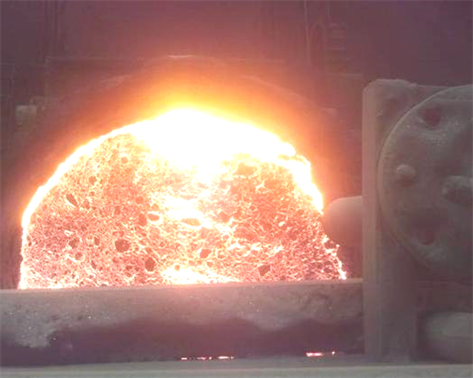
Figure 4. Auto clearance survey by radar
图4. 雷达液位自动净空测量
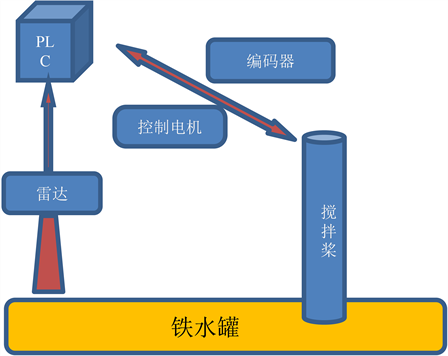
Figure 5. The calculation sketch of impeller insertion depth
图5. 搅拌桨插入深度计算示意图
5. 开发脱硫高效扒渣技术
铁水预处理前扒渣是为了去除铁水自带的高硫炉渣,从而降低脱硫剂消耗,预处理后扒渣是为了去除脱硫形成的炉渣,避免铁水回硫现象,因此铁水扒渣对于脱硫处理效果稳定至关重要。在生产实践中发现,扒渣板作为铁水扒渣机重要组成部分对于提高扒渣效率是主要限制因素,为此,特开发一种新型扒渣板,通过增大扒渣板与炉渣接触面,改变扒渣角度,从而提高扒渣效率。另外由于增加了与炉渣的接触面积,降低了扒渣板对铁水的搅动,间接的降低了扒渣带来的铁损。新型扒渣板见图6。
说明1:扒渣板上端窄面部分;2:扒渣板下端宽面部分;3:扒渣板与扒渣机连接孔;4:扒渣板上端窄面部分;5:扒渣板下端宽面部分;6:铁水包渣面;α = 110˚;β = 160˚。
Figure 6. The front, side sketch of new slaging-off board
图6. 新型扒渣板正面、侧面示意图
从新型扒渣板使用效果来看,脱硫扒渣时间平均缩短1 min左右,进一步提高了扒渣效率。
6. 吹气赶渣技术的运用,实现铁水与脱硫渣快速分离
铁水脱硫后的炉渣成颗粒状,且流动性良好,在铁水包内的炉渣几乎分布在整个铁水面上,因此不仅扒渣面积大,而且存在扒渣“死角”,铁水扒渣时间长,扒渣过程中铁水损失较大。
针对上述问题,自主改造开发吹气赶渣技术,通过吹渣枪将氮气以一定的压力和流量送入到铁水包液面后部,即扒渣“死角”区域一定深度的铁水中,利用喷入氮气的喷吹动能和氮气在铁水中被加热、膨胀和上浮产生的动能将铁水翻动,部分动能通过铁水包包壁折射,推动铁水表面的渣向铁水包扒渣口方向流动,将铁水表面的渣“赶到”铁水包口区域(赶渣作用),再采用扒渣板进行扒渣去除。
通过对气体压力与流量的控制,气体将比重较轻的脱硫渣与铁水分离,提高扒渣效率,进而减少铁损,产生较大的经济效益。此技术示意图见图7。
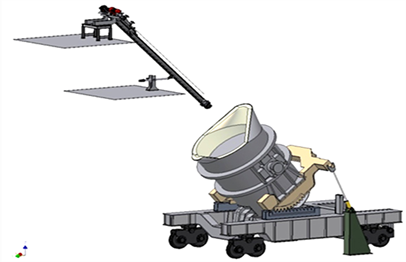
Figure 7. Hot metal slaging-off by blowing
图7. 铁水吹气赶渣
7. 开发铁水高效脱硅技术
7.1. 高效脱硅剂研究与开发
日本和国内少数钢铁厂采用的高炉前铁水沟上置法、顶喷法脱硅以及鱼雷罐,虽然能达到一定的脱硅效果,但起泡问题严重,渣中残余FeO含量较高。北京科技大学耿敬涛,杨世山等人研究对比了上置法、吹气搅拌法、喷吹法和机械搅拌法的脱硅能力、炉渣起泡高度、脱硅氧效率。结果表明机械搅拌能明显地缩短脱硅反应时间,提高脱硅速率,脱硅能力提高 [5] [6]。
一般情况下,脱硅剂主要由氧化剂和造渣剂组成,常用的氧化剂包括氧化铁皮、铁精粉、转炉灰等。由于硅与氧的结合能力远远强于磷与氧的结合能力,所以铁水加入脱硅剂后硅比磷优先氧化,从促进反应的角度分析,由于硅反应生成酸性的物质,为了降低产物的活度,在脱硅剂中加入适当的活性物质CaO、Al2O3,便于提高脱硅效率。反应式如下:
(6)
为此,通过研究开发Fe2O3-Al2O3系高效脱硅剂,具体理化指标及与其他脱硅用材料对比见表2。
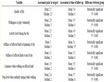
Table 2. Physicochemical parameters of new desiliconization agents and contrast with the others
表2. 新型高效脱硅剂理化指标及与其他脱硅剂成分对比
从成分对比来看,新型高效脱硅剂具有以下优点:
1) 全氧含量相比氧化铁皮较低,脱硅反应过程平缓可控,避免了脱硅急剧反应造成的炉渣快速溢出铁水罐而造成的安全和设备事故,也就是说放宽了对铁水罐的净空要求,从而可以提高脱硅处理的铁水罐次比例。
2) 提高氧化铝含量,增加了炉渣的表面张力,降低了炉渣黏度,有利于缓解脱硅炉渣的起泡问题。
3) 含有一定量的氧化钠,能够降低炉渣中P2O5的活度,而且也能够降低硅酸根离子的聚合,从而降低炉渣黏度。
7.2. 高效脱硅剂工业应用
通过应用新型高效脱硅剂后,铁水预处理工序可以根据初始硅含量最大限度地调整脱硅后硅含量,应用效果良好。
1) 脱硅氧效率
由于不同类型脱硅剂成分不同,初始硅含量不同,加入脱硅剂量波动也较大,因此采用脱硅氧效率(ηsi)作为衡量脱硅剂效率的指标比较合适。
ηsi = 与硅反应的氧/脱硅剂中的全氧 × 100%
新型脱硅剂脱硅氧效率平均72.6%,能够满足铁水脱硅需求。
2) 脱硅剂脱硅稳定性
统计工业试验罐次脱硅0.1%时,脱硅剂消耗量同均值的偏差对比情况见图8。
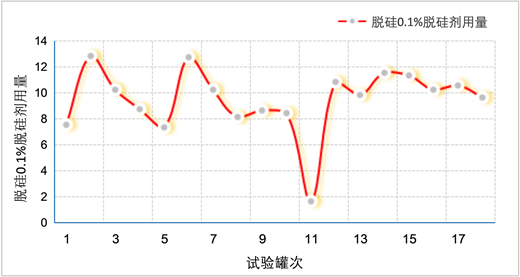
Figure 8. The dosage with 0.1% desiliconization mean divagation
图8. 脱硅0.1%时,脱硅剂用量同均值偏差
可以看出,在均值9.93 ± 2 kg/t的范围内,囊括了12罐次,充分说明了新型脱硅剂的脱硅性能比较稳定。
8. 结语
1) 通过开发应用颗粒脱硫剂技术,铁水脱硫剂消耗降低了30%。
2) 开发并应用铁水自动测量技术、高效扒渣技术,脱硫搅拌时间控制在10 min以内,脱硫命中率稳定在90%以上。
3) 开发Fe2O3-Al2O3系高效脱硅剂,动态调整铁水硅含量,达到降本增效目的,效益显著。
4) 自主开发高效低耗铁水预处理技术,在实践中积累宝贵经验,对其他钢铁企业具有积极借鉴意义。