1. 引言
产品碳足迹是指产品在其整个生命周期中所释放的温室气体总量,由于二氧化碳为主要温室气体,通常用二氧化碳当量(tCO2)量化碳足迹,用以衡量产品绿色低碳水平 [1] [2]。当前国家鼓励企业强化节能减排能力,建设产品碳足迹相关机制,围绕碳足迹核算方法及应用范围等方面开展重点研究 [3] [4],促进绿色产品转型升级。电工装备企业作为电网建设物资的供应商,承接产业链绿色转型的重大任务,这需要企业自身持续推动产品生命周期绿色低碳化,识别业务经营过程存在的碳排放源,精准核算其各环节碳排量值,并以碳标签形式告知产业链上下游产品碳足迹用量信息 [5],进而助力企业制定高效的绿色转型策略,形成规模化绿色经济效益,推动上下游产业链绿色发展。
2. 设计碳足迹模型的重要意义
电工装备企业践行绿色发展理念,推广应用碳足迹跟踪模型,组织评估重点物资品类,掌握产品生命周期碳排放情况,跟踪原材料、生产过程、物流运输等环节的能耗量值,形成可溯源的碳足迹报告,促进企业生产经营绿色转型,引领产业链绿色升级,为电网公司开展绿色产品采购管理提供坚实依据。具体如下:
精准掌握企业产品生命周期能耗分布。通过调研当前生产经营情况,明确碳足迹跟踪规则的适用范围,识别产品原料到成品运输过程的能耗点分布,结合对应的能耗类型,采集产品碳足迹能耗量值,运用排放因子法,将能耗量值转换成二氧化碳碳排放量,形成产品碳足迹量化的借鉴案例。
推进电工装备企业产品绿色转型策略。通过产品生命周期碳足迹方法,确定污染能耗较大的分布点,从而树立产品绿色转型治理的目标,协调企业内外部资源,制定产品绿色转型升级策略,针对能耗大、减碳难等问题,提出有助于落实的绿色减碳建议,形成产品碳足迹绿色应用的示范案例。
3. 目前碳足迹面临的痛点及挑战
当前电网公司推行绿色产品采购,提高产品绿色低碳水平,为配合电网公司绿色管理要求,电工装备企业强化产品生命周期的碳减排能力,结合现场调研情况,探索出产品生命周期开展碳足迹设计过程中存在的痛点(见图1):
1) 产品碳足迹边界有待确定
经企业内部决定,试点产品选取电网重点物资变压器,为便于梳理核算变压器生命周期的碳足迹,制定适合的减碳策略及举措,这需要明确变压器生命周期系统边界,从原材料到成品运输的各阶段,划定重点业务排查环节,对后续碳足迹分析建议具备强化指向作用。
2) 产品碳排放源确认有待商榷
在重点业务排查环节中,碳足迹的碳排放源务必需要精准识别,现阶段重点业务包括原材料、生产过程、物流运输,可根据SOP操作手册和技术文件确认碳排放源,对碳排放源涉及的能耗类型、计量单位等信息,需要结合企业实况进行设计,准确设置碳足迹相关信息,为碳排放测算奠定基础。
3) 产品碳足迹分析结果待指向
随着电网公司绿色采购趋势的紧迫性,绿色产品的转型指向亟待解决,根据碳足迹评价结果,制定相适配的绿色产品转型策略尤为重要,既要切实贴近企业产品线现况,还要符合电网公司产品技术要求,通过建设中长期绿色战略,完善绿色产品管理要求,改进提升绿色技术,显现碳足迹减碳的成效。
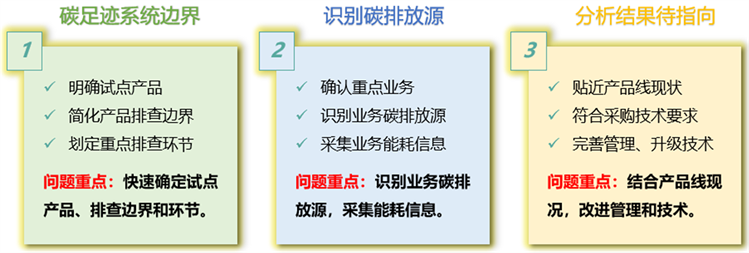
Figure 1. Pain points in establishing product carbon footprint
图1. 建立产品碳足迹面临的痛点
4. 针对碳足迹痛点的举措以及工作方向
产品碳足迹以制造企业产品线为主线,根据ISO14040标准和现场调研情况,对产品生命周期碳足迹过程划分为边界确认、排放核算、分析建议三个阶段,通过识别重点排查环节的碳排放源,采集产品线各环节能耗数据转换成碳排量,提出改进建议,设计应用场景。主要举措包括(见图2):
1) 产品碳足迹系统边界确认
针对产品碳足迹边界问题,企业主供电网物资为特高压变压器,以400 kV互换流变压器产品生命周期为碳足迹基准流,主要包括原料加工、生产制造和物流运输,产品使用阶段(维修及养护等)和废弃阶段(包括回收再利用或废弃处置)未包括在边界内。
2) 采集能耗数据、量化碳排放
针对业务碳排放源能耗排查问题,识别原料加工、生产制造、物流运输为关键点,经调研技术文件,确认产品模块环节包含的碳排放源,明确碳排放源消耗的能源类型,从而编制产品生命周期清单,根据每种能源类型的不同,依据GHGP标准查找相应的排放因子,运用IPCC排放因子法计算得出碳排放数据。
3) 分析碳排放数据、提出改进建议
针对碳足迹分析结果指向问题,根据获得的碳排放数据,分析产品线环节碳排放数据的占比,利用物联网监测手段,编制企业产品碳地图,对关键业务节点设置碳标签,实时跟踪碳标签数据,通过建立健全绿色减碳管理制度,设计业务场景管控力度,促进业务各环节持续减排。

Figure 2. Whole process of product carbon footprint
图2. 产品碳足迹全流程
5. 碳足迹量化及应用场景设计方案
1) 明确业务环节碳排放源
选择400 kV互换流变压器生产过程为边界范围,通过现场调研和查阅文件,统计原材料、生产过程、物流运输环节的碳排放源数量。同时,统计碳排放源对应使用能源类型,可知一次能源为汽(柴)油,二次能源为电力。将上述信息进行汇总编制成能耗采集清单(见表1),以便后续测算碳排放量并加以分析。
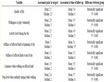
Table 1. Product carbon footprint data collection list
表1. 产品碳足迹数据采集清单
2) 测算碳足迹排放量
在确定碳足迹的能耗数据后,依据GHGP标准查询能源相对应的排放因子,即汽(柴)油、电力的碳排放因子,运用IPCC排放因子法(见公式1),利用能耗量乘以碳排放因子得出碳排放量,即:
(1)
其中:E为总碳排放量值,n为所有数据条数目,Qi为某种能源消耗量,Ti为Qi对应的碳排放因子(见表2)。
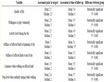
Table 2. Carbone mission factor parameters of various energy sources
表2. 各类能源碳排放因子参数
3) 汇总碳足迹排放量
经收集碳足迹排放量的相关数据,运用IPCC排放因子法,计算得出各能耗类型的排放量,通过汇总累加得出产品碳足迹走过排放量。将上述数据信息整合,清晰辨别出碳足迹在业务环节的能耗类型及排放量,精准把握减碳措施的实施重点,为后续碳足迹全景地图奠定基础。
4) 精准分析形成碳足迹策略
根据获取的碳足迹排放量数据,结合电工装备企业现况,开展精准分析碳排放数据,对碳排放总量及各业务环节排放量,提出碳足迹减碳建议,切实改善业务环节碳排放量显著的现象。优化建议具体如下。
一是提升原材料工艺水平,例如硅钢片裁剪环节,通常采用设备仪器将硅钢片冲塑成统一规制,每日大量柴油消耗供能的同时,衍生出一定量的边角料,经过工艺改进和产品改良,可以避免边角料等废弃物的耗能处理,降低生产成本带来的压力,为产品生命周期整体减碳做出贡献。
二是生产过程结构调整,面对生产碳排放源多、排放量大的问题,需协同研发部、制造车间、计划库存等部门开展专项分析会,为降低生产空置时间进行结构调整。生产空置时间是指某工序资源(设备等)等待上步工序移交产品任务的时间,不仅消耗能源用于设备暖机,使交付周期拖长,因此需多部门联合调整产线,逐步降低生产控制时间,进而实现生产过程减碳。
三是采购清洁型能源车,物流运输的排放量同样值得重视,对厂区内短距离运输,推荐采购清洁型能源车用于搬运货物,对厂区外长距离运输,推荐优化计划交付时间,鼓励对具有订单散多特征的单一客户,实行计划集中供货,减少多次运输能耗排放量,在交付装载阶段进一步降低生产运输成本。
综合上述优化建议,势必需要技术升级加以支撑。基于物联网感知技术,排放源监测方面,使用碳标签技术,采集该环节能耗类型、排放上限等数据;排放量监测方面,汇聚碳标签数据到信息平台,展示碳全景地图,监督各环节排放量变化趋势,进而形成完善的碳足迹追踪服务机制。
6. 碳足迹量化及应用场景的预期成效
1) 碳足迹量化与碳标签联动应用
通过对每个排放源设置碳标签,实时显示排放源投入的能耗类型、使用量等数据信息,一旦出现排放量即将触及排放上限,现场立刻提醒并运用物联网网络层通知企业责任部门,避免各排放源出现排放量短暂峰值的突发情况,保持碳排放量处于稳定递减的过程,有利于下游电网企业实行绿色采购策略。
2) 碳足迹追踪与碳地图联动应用
通过对各排放源碳标签的追踪,并实时汇总数据到碳地图信息平台,强化企业高层统筹管控产品线碳变化趋势,及时调配产品线设备、人员等资源,更新制度、流程等管理保障体系,积累数据经验制定符合企业绿色发展的各层次策略,有助于联动电网企业绿色采购策略共同绿色转型。
3) 碳足迹量化、追踪与电网企业联动应用
产业链上下游是互相影响、互相联动的利益共同体,电工装备企业产品碳足迹减碳举措关系到电网企业绿色采购策略的制定,因此,两者应达成碳数据贯通,电网企业掌握上游企业的碳变化趋势,电工装备企业及时了解电网企业需求,在保障供应链稳定的基础上,达到绿色发展双赢的目的。
7. 结论
本文围绕电工装备企业碳足迹量化与追踪服务,以构建电网绿色低碳产业链为目的,探索建立一套产品碳足迹排放量计算方法、标准,并协同物联网新技术例如碳标签、碳地图等追踪排放源相关数据,集成到数据平台进行统筹管控,及时调配产品线资源应对碳排放量超出变化趋势的现象,保障供应链减碳措施的顺利推行,通过制定碳相关的制度、流程等管理措施,联动电网企业的绿色采购策略的制定生成,从而形成可持续的产业链上下游减碳“长鞭效应”,带动整个产业链供应链绿色转型发展,为实现“双碳”目标做出贡献。