1. 引言
汽车行业发展迅速并已成为国民经济的支柱,随之也带来了能源短缺和环境保护等问题。汽车的生产制造在保证安全性的前提下采用轻量化的材料,可使总重降低,从而达到节能减排的目的[1] [2]。因此,汽车轻量化成为研究的主要方向。先进高强度双相钢(DP)是由硬相马氏体和软相铁素体两种相复合组成,其具有高的加工硬化率、低的屈强比以及强度与塑性的良好匹配等优异性能,已作为汽车轻量化材料广泛应用于汽车底盘、车顶内板和保险杠加强体等结构件中[3]。
冷轧双相钢的工艺控制比较稳定,是目前汽车用双相钢制品的主流,但冷轧需要增加退火、重卷等工序,也容易带来加工硬化等问题,使生产成本与生产周期增加,不利于国家的“双碳”政策的实施。控轧控冷技术(TMCP)的快速发展和控轧控冷设备的更新换代,为热轧双相钢的成功开发和应用提供了坚实基础。热轧双相钢的工艺流程短有利于降低碳排放,且其较好的综合力学性能有利于替代冷轧双相钢,从而受到用户和生产企业的青睐[4]。本文基于汽车轻量化进行低碳低合金的成分设计,通过控轧控冷工艺技术生产得到不同等温时间的试验钢,最后经组织性能的测试来研究工艺的影响因素,为高强度热轧双相钢的生产和获得优异性能提供参考。
2. 试验材料及方法
2.1. 试验材料
试验钢是通过真空冶炼炉冶炼得到的主要化学成分如表1所示,采用的是C-Si-Mn-Cr的成分设计,较低的C含量可有效降低碳当量和焊接裂纹敏感指数,从而提高钢的焊接性能和冷加工成形性能;少量的Si和适量的Cr可抑制渗碳体的形成促进铁素体的析出,也尽可能减少氧化铁皮的生成提高表面质量,少量的Al主要用于脱氧以净化钢质。
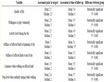
Table 1. Chemical composition of tested steel (mass fraction, %)
表1. 试验双相钢的化学成分(质量分数,%)
2.2. 试验过程
铸锭在浇注后经锻造得到40 mm的坯料,将坯料放入1200℃的加热炉中保温1 h,然后进行两阶段的控制轧制,具体的第一阶段为三个道次的再结晶区粗轧、第二个阶段为二个道次的未再结晶区精轧,开轧温度为1140℃,终轧温度为825℃,轧后厚度为4 mm,再经层流冷却至680℃分别等温7 s和9 s以析出先共析铁素体,最后水冷至300℃以下卷取发生马氏体相变,得到铁素体+马氏体的热轧双相钢。
2.3. 测试方法
对控轧控冷后得到的试验钢进行取样,根据GB/T 228.1-2021制取室温拉伸试样,力学性能和n值的测试在WAW-500C型万能材料试验机通过拉伸试验进行,拉伸的速度取2 mm/min,试样的宽度和标距分别取12.5 mm和50 mm。显微组织观察的试样通过线切割沿热轧板纵向切取,采用ZEISS金相显微镜进行金相组织观察(OM)和定量分析,采用Nova nano 400扫描电镜进行扫描组织的观察(SEM)及特征分析。
3. 试验结果与分析
3.1. 试验钢的显微组织
图1所示为试验钢在控制轧制后经7 s和9 s不同时间等温得到的金相显微组织,由铁素体和马氏体两相混合组成。图中显示铁素体呈白亮色,主要是多边形,也有较多晶粒非常细小的铁素体组织,这是由于铁素体是从过冷奥氏体中析出,包括形核和长大两个过程,应该有很多晶粒长大不完全,晶粒组织很细小[5]。通过IPP软件对得到的组织进行定量知,7 s和9 s等温试样的铁素体平均晶粒尺寸分别为4.8和5.3 μm,体积分数分别为83.5%和87.3%。从定量结果发现,试验钢中铁素体的平均晶粒尺寸较小约为5 μm,铁素体的体积分数较多约为85%,这是由于试验钢在第一阶段的再结晶区粗轧细化了原奥氏体晶粒,接着在第二阶段精轧使奥氏体中获得大量形变带,这些形变带为后续的铁素体相变提供了形核点,有利于组织的细化。另外,9 s等温的时间长,得到铁素体的尺寸和体积分数均增加,这说明在两相区的等温时间长,组织会不断长大并且更加均匀。
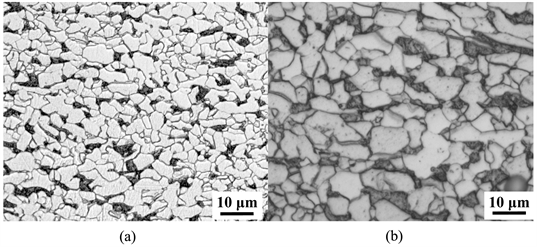
Figure 1. Microstructures of the tested steel with different isothermal time (a) 7 s;(b) 9 s
图1. 试验钢不同等温时间下的金相组织(a) 7 s;(b) 9 s
试验钢在两相区等温析出铁素体后水冷至300℃以下卷取发生马氏体相变,得到的马氏体弥散分布在铁素体周围,7 s和9 s等温试样的马氏体体积分数分别为16.5%和12.7%,其通过扫描电镜观察到的组织如图2所示。图2中显示马氏体具有浮凸效应,且以岛状和长条状为主,也观察到少量块状马氏体。9 s等温试样的等温时间长,得到的马氏体体积分数要少,是由于试验钢在两相区等温过程中还会发生碳原子向未转变的过冷奥氏体扩散,9 s等温试样的扩散时间长,未转变过冷奥氏体中的碳含量要多,降低了Ms点,后续相变得到的马氏体也要少。故而,等温时间对双相钢的组织形貌及含量有较大影响。
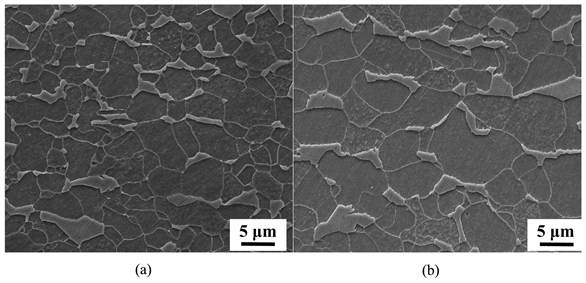
Figure 2. SEM micrographs of the tested steel with different isothermal time (a) 7 s;(b) 9 s
图2. 试验钢不同等温时间下的SEM组织(a) 7 s;(b) 9 s
3.2. 双相钢显微组织与力学性能关系
试验钢在室温下经拉伸测试后得到的力学性能结果如表2所示。由表2数据知,热轧双相钢具有高的伸长率在30%左右、高的加工硬化率n值在0.18~0.20,还具有较低的屈强比小于0.60。根据GB/T 20887.3-2010《汽车用高强度热连轧钢板及钢带:双相钢》知,经7 s和9 s等温的试验钢力学性能均DP580钢的性能要求,说明试验钢具有较好的强韧性匹配,而7 s等温的试验钢力学性能还达到了DP600的性能要求,因此,7 s等温的试验钢综合力学性能要优于9 s等温的试验钢。
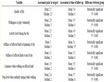
Table 2. Mechanical properties of the tested steel
表2. 试验钢的力学性能
两种试样的应力应变曲线如图3所示,得到的拉伸曲线比较平滑没有出现上下屈服点,而且具有较高的初始加工硬化率和较长的均匀塑性变形区。是由于马氏体相变膨胀挤压周围铁素体,使铁素体内产生较多的可动位错;同时,铁素体作为双相钢中的软相会首先发生塑性变形,而且铁素体的体积分数较大,也会产生大量的可动位错[6]。因此,双相钢在拉伸变形时表现为连续屈服。而且试验钢中有较多的条状马氏体,其板条边界不规则易发生扭折(如图4所示),是由于热轧后过冷奥氏体中保留了大量的形变带等高密度位错,破坏了原奥氏体中结构的均匀性,而马氏体是通过奥氏体发生相变得到,故观察到较多不规则的边界,而这些带有不规则边界的细化的条状马氏体较大的增加了马氏体与铁素体的有效接触面积,使得马氏体膨胀产生较多的可动位错,提高了钢的n值。另外,钢中屈强比较低,这些均有利于提高钢的深冲性能和冷加工成形性能。
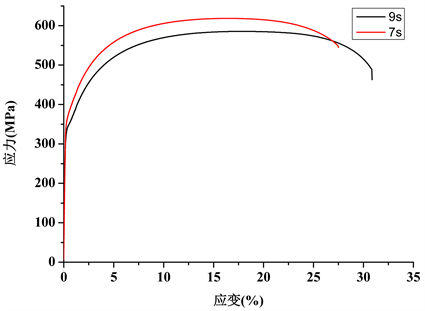
Figure 3. Stress strain curve of the tested steel
图3. 试验钢的应力应变曲线图
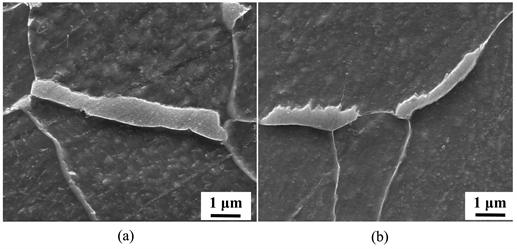
Figure 4. Microstructure characteristics of lath marten site in test steel (a) 7 s;(b) 9 s
图4. 试验钢的条状马氏体组织特征(a) 7 s;(b) 9 s
试验钢的力学性能差异与显微组织有较大关系。7 s等温试样的两相区等温时间短,得到的铁素体体积分数少,而铁素体作为软相在塑性变形过程中起主要作用,得到的伸长率相对较低为27.5%;又由于铁素体的平均晶粒尺寸要小为4.8 μm,根据霍尔佩奇公式,7 s等温试样得到的屈服强度要高为366 MPa;钢中马氏体的体积分数较多为16.5%,而马氏体作为硬相在塑性变形后期起强化作用,得到的抗拉强度较高为618 MPa,即达到了DP600的力学性能要求[7] [8]。而9 s等温试样的两相区等温时间长,钢中马氏体的体积分数较少为12.7%,得到的抗拉强度较低为586 MPa,达不到DP600的力学性能要求。同时考虑到产线上长时间的等温会降低生产效率,故试验钢合适的等温时间为7 s左右。
3.3. 双相钢的节能减排效果
与常规的高强钢相比,双相钢因较低的屈强比和较高的n值具有较好的冲压成形性能、扩孔性能和耐疲劳性能,可实现对具有复杂形状的轮辐和底盘等汽车零部件采用高强钢进行冲压,从而可有效减小材料的厚度。当钢板厚度减小0.10 mm时,车身可减重12%,燃油消耗则下降10%,碳排放下降8%。国际汽车用钢协会针对电动汽车车体发布了未来钢质汽车项目FSV (Future Steel Vehmle),其汽车使用的高强钢和先进高强钢高达97%,可实现车身减重39%为188 kg,并具有5星的安全评级。
日本科学家对钢板的抗拉强度与钢板厚度之间的关系进行研究发现:厚度为0.80 mm对应抗拉强度为590 MPa的钢板与厚度为0.83 mm对应抗拉强度为540 MPa的钢板,其承载力与厚度为1 mm对应抗拉强度为370 MPa的钢板相同,因此,采用DP590或者DP540替代常规的Q235B高强钢来制作汽车零部件,可使相应的汽车部件减重约20%与17% [9]。所以,对于本试验钢,7 s等温试样的抗拉强度较高为616 MPa,用其替换Q235B高强钢,可使相应的汽车部件减重约21.5%,燃油消耗则下降18%,碳排放下降14%,具有较好的节能减排效果。
4. 结论
1) 采用低碳低合金的成分设计,通过控轧控冷工艺技术得到性能良好的DP580和DP600双相钢,其显微组织均为铁素体+马氏体。
2) 试验钢的屈服强度为338~366 MPa、抗拉强度为586 MPa~616 MPa,伸长率为27.5%~31.0%,屈强比较低为0.58~0.59,n值较高为0.18~0.20,表现出较好的强韧性。
3) 试验钢的力学性能达到DP580与DP600双相钢的要求,可满足车辆零部件的减重要求,具有较好的节能减排效果。
NOTES
*通讯作者。