1. 引言
目前国内常用选择性催化剂还原法(SCR)去除燃煤电厂尾气中的氮氧化物(NOx)。SCR法就是在温度控制在290~400℃的条件下,还原剂NH3选择性地把NOx还原成N2 [1] [2] [3]。通过尿素制NH3,可以克服液氨易爆炸、氨含量低和体积大等缺陷,近年来备受关注。尿素制氨通常有尿素水解制氨 [4] 和尿素热解制氨两种方案 [5]。本文总结了尿素制氨的各类工艺特点,并预测尿素制氨工艺的未来发展方向。
2. 尿素热解制氨
当前,国内使用的尿素热解制氨系统大部分使用美国FUEL TECH公司产品 [6]。主要流程为:首先通过输料机将尿素固体颗粒输送到尿素溶解罐内,在尿素溶解罐里完成对尿素固体颗粒的溶解,配置成浓度为50%左右的尿素溶液,然后通过输送装置到达热解室并蒸发热解制氨。热解制氨实质上是尿素溶液不断浓缩结晶,达到饱和状态在350℃以上发生蒸发热解产氨。为了使尿素充分热解,需要提供足量的热量,另外还要控制产物温度,以减少可逆反应。尿素热解制氨具有效率高、系统简单、可靠性高等优势,同时存在高能耗及高故障率的问题。这些问题目前主要有以下解决方案。
2.1. 尿素溶液直喷制氨技术
尿素溶液直喷制氨 [7],包括利用锅炉高温烟气将尿素直接热解成氨气和CO2的炉内尿素直喷技术和借用高温烟气热量将尿素溶液分解为氨气的锅炉高温烟气旁路直喷等两种技术。尿素直喷制氨取消了传统热解系统内的电加热器、热解炉、一(二)次热风管道系统等电加热和天然气加热获取热解热源的辅助设备,从而减少高质量能源(如电能、天然气、一次风等)的消耗,使得运行成本大大下降 [8],减少了投资成本,提高了运行稳定性。尿素直喷制氨的工艺在烟道的入口处安装喷射器,保证尿素溶液的喷射位置最佳,如此一来,尿素的使用率和脱硝的效率就得到了提升。和传统尿素热解制氨相比,尿素直喷制氨技术NH3与烟气混合程度较差,为了改善这一弊端,提高烟气与氨气的混合程度,确保氨气与烟气的充分混匀,需要在SCR反应器的入口处加设涡流混合器。尿素热解不充分亦或是温度降低,都会使得尿素溶液析出结晶,进而导致管道堵塞,而这一操作可以消除以上原因造成的管道堵塞的风险。
2.2. 尿素电加热热解制氨技术
电加热尿素热解制氨工艺 [9] [10] 使用电加热的方式提供尿素热解所需热源,通过电加热器将300℃左右的热一次风加热到650℃左右,经过加热后的热一次风进入热解炉,在热解炉中,加热后的热一次风为尿素热解提供热量,尿素溶液即发生高温热解反应,生成NH3和CO2。
电加热制氨方案(图1),虽然降低了故障率,但使用的电加热器的功率比较大,能耗较高,电加热器的制造成本和使用成本都比较高,影响电厂经济性 [11]。
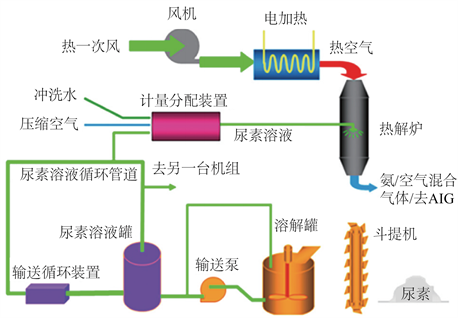
Figure 1. Ammonia production by electric heating urea pyrolysis [10]
图1. 电加热尿素热解制氨工艺 [10]
2.3. 烟气加热尿素热解
烟气加热尿素热解工艺中,烟气换热器的分布位置可以有所不同,如此也就衍生出两种方案:炉外热风加热和炉内热风加热,两种方案的工作原理相同,只是烟气换热器的设置位置不同,所以这两种方案的主要工艺一致。
(1) 炉外气气换热尿素热解技术
炉外气气换热是把锅炉烟道内排放的烟气中的一部分高温烟气引入设置在锅炉外的换热器内,借助高温烟气的热量对一次风进行加热,将经高温烟气加热后的高温空气输送至热解炉内,高温空气提供的温度可以达到尿素的热解温度,尿素即发生热解,生成氨气和二氧化碳,完成换热的原锅炉高温烟气再输送到SCR反应器,对这部分烟气进行脱硝 [12]。
炉外气换热热解技术引用烟道高温烟气作为热源加热一次风,相比于电加热和天然气加热,该工艺降低了能源的消耗,减少了运行成本。但该技术也存在一定的缺点:a) 运行设备体积大,从而导致占地面积大;b) 在锅炉钢结构内安装换热器难度大,装置安装成本较高;c) 该工艺需要引用锅炉烟道内高温烟气,由于烟气温度较高,烟气管道就需要选用耐高温、高质量的材料,如此成本就增加了;d) 该工艺在使用过程中,为调节烟道主路和支路的烟气份额,需要设计调节板;e) 该工艺运行过程中锅炉烟气温度和调节挡板开度都会影响其使用效果。
(2) 炉内气气换热尿素热解技术
炉内气气换热尿素热解技术 [13] 需要设置一组蛇形换热管束,将蛇形换热管束布置在锅炉烟道内,此处锅炉烟气温度在550℃~800℃,在蛇形管束内通入干净的空气,并使得高温烟气从蛇形管束外部通过。蛇形管束内引入的洁净空气可以是直接从大气中抽取,也可以利用锅炉的冷一次风的压头获得,从蛇形换热管束外部通过的高温烟气可以对其内部的洁净空气进行加热,然后将蛇形换热管内已经被加热的空气通至热解炉内,在热解炉内利用加热后洁净空气所提供的热量进行尿素的热解反应,反应最终生成NH3。
正常使用条件下,这种技术不需要通过电来加热,而是要在开机并网之前很短的一段时间里才需要使用。此外,采用一次冷风作为稀释风,冷一次风的含尘量低,从而有效地防止了热解炉和格栅的阻塞。
相比于炉外气换热尿素热解技术,炉内气气换热尿素热解技术具有以下优点:a) 降低能耗,减少能耗成本;b) 管道及设备没有被堵塞的风险;c) 设备体积小,占地面积校小,改造难度低;d) 不需要另设烟道,投资成本低。
2.4. 尿素水解制氨工艺
尿素水解 [14] 法是用吊斗或人工将固体尿素加到尿素溶解罐中,在溶解罐内,将其溶出,以50%的比例配置成尿素溶液,然后将混合后的尿素溶液送入尿素储罐,接着经计量分配器分配后将尿素溶液送入尿素水解器,尿素水解需要在水解器内达到一定的温度,然后进行尿素水解,产生NH3、CO2,该反应为可逆反应,反应方程式为:
CO(NH2)2 + H2O = NH2COONH4 (8)
NH2COONH4 = 2NH3 + CO2 (9)
尿素水解反应是先生成氨基甲酸铵(NH2COONH4),当温度稍微降低气态的氨基甲酸铵就容易析出结晶,从而致使产品气管道堵塞 [14]。
反应温度、反应停留时间和尿素溶液浓度都是影响尿素水解速率的变量。
1) 温度对尿素水解速率的影响
尿素水解反应是吸热反应,其反应速率随温度的变化而变化,温度升高,尿素水解速率也随之加快。因此,尿素的水解率可以通过调整水解器的温度而得到控制,在一定的压力和温度下,用阿伦尼乌斯方程求解尿素的水解率 [15] 表示:
(10)
在水解过程中,尿素溶液浓度、反应温度对NH3产率有重要影响。在115℃以下,水解速率相对缓慢;在128℃以上,水解率有显著提高;在145℃以上,尿素的产率显著增加 [16]。温度与尿素水解反应速率关系如图2。
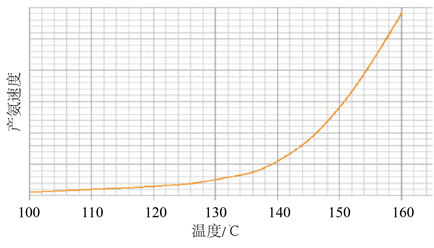
Figure 2. Relationship between temperature and urea hydrolysis reaction rat [16]
图2. 温度与尿素水解反应速率的关系 [16]
尿素的水解反应,反应器中温度低于130℃时,中间产物NH2COONH4会由气相转变为固相,在水解器的表面结晶,NH2COONH4对于水解器的不锈钢材料表面的氧化膜有严重的腐蚀作用,会加速水解器的腐蚀。因此,尿素水解器及管道选用316 L不锈钢,同时还要保证水解反应器内的温度保持在128~150℃ [16],这样可以有效减缓水解器及管材的腐蚀速度,水解反应器可以使用较长一段时间。
2) 尿素溶液浓度对水解速率的影响
尿素溶液浓度低,尿素固体可以比较溶解,水解速率大,但水解产物含量低,氨气浓度低;尿素溶液浓度高,尿素固体颗粒溶解难度增大,水解速率小,但水解产物含量高,氨气浓度高。高浓度的氨气。考虑到尿素溶液的配制及水解反应的安全,应控制尿素溶液的质量分数为50%,相应的密度为1135~1140 g/cm3,通过在线密度计在尿素溶解工艺中进行尿素溶液浓度的控制 [17]。
2.4.1. 尿素普通水解制氨工艺
普通尿素水解 [16] 工艺流程如图3所示。尿素溶液储罐里的尿素溶液通过输送泵输送至水解反应器内,蒸汽减温减压后进入反应器内的盘管,利用蒸汽的温度对反应器中的尿素溶液加热,达到尿素水解温度时,尿素溶液即发生普通水解反应,反应生成的NH3通过管道输送至SCR反应器。蒸汽传递热量之后冷凝为冷凝水,再将冷凝水输送至疏水箱。
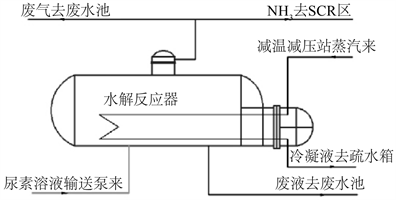
Figure 3. Common hydrolysis process of urea
图3. 尿素普通水解工艺
目前,普通水解的反应温度为150℃~160℃,压力为0.5~0.7 MPa。
尿素普通水解制氨技术优点主要有:可采用公用制布置,多台机组共用水解反应器,以便于集中控制管理,且投资费用相对较低;水解反应器采用撬装模块,可与尿素溶液制备区集中布置,节约占地空间,节约土地成本;尿素水解反应耐符负荷,可以比较稳定的制氨。但尿素普通水解反应也存在一定的缺点:普通水解反应器水解反应所需的温度相对较高,在水解过程中会产生一定的缩二脲和异氰酸副产物,抑制尿素水解,导致水解速率降低;当温度降低时,尿素溶液和氨气会发生结晶,析出固体,致使管道堵塞、阀门卡死等,更甚会导致水解反应器以及脱硝反应部分暂停。
2.4.2. 尿素催化水解制氨工艺
尿素催化水解制氨技术主要由三个部分组成:尿素颗粒储存系统、溶解输送系统和尿素水解系统 [17],如图4所示。
通过运输车将尿素固体颗粒输送到尿素溶液制备区,储存在尿素存储车间,配制尿素溶液需要使用抬升机将尿素固体颗粒提升到一定的高度后送入尿素溶解罐。在尿素溶解罐中,用去离子水将其配置成浓度为50%左右的尿素溶液。布置蒸汽盘管,利用蒸汽为尿素溶解提供热量,同时可启用尿素溶液混合泵对尿素溶液搅拌,以加速尿素的溶解。将配置好的尿素溶液输送至尿素溶液储存罐。在尿素溶液储存罐处也设置蒸汽加热盘管,以避免尿素溶液因温度下降而结晶析出,通过加热盘管,使得尿素溶液的温度维持在50℃~70℃。
尿素催化水解制氨系统是将浓度约为50%、温度为50℃~70℃的尿素溶液通过高压泵从尿素储存罐打入尿素水解反应器中,在压力0.4~0.9 MPa、温度135℃~160℃的条件下和催化剂的作用下进行水解反应,反应生成NH3、CO2、水蒸气混合气。混合气经由减压、流量控制调节与稀释风在氨、空混合器中混合,将氨气浓度稀释至5%以下,由氨喷射装置喷入SCR反应器内与烟气中的NOX反应。
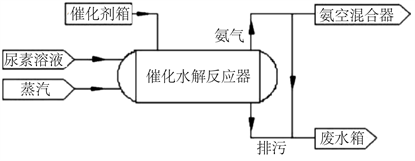
Figure 4. Ammonia production process by catalytic hydrolysis of urea
图4. 尿素催化水解制氨工艺
尿素催化水解制氨系统中使用的催化剂是按一定比例配置的磷酸盐,系统开始启动时,将催化剂磷酸盐加入,在水解反应器内,该催化剂可循环使用。催化的主要作用是改变反应路径以加快反应速率,降低水解反应的响应时间。
尿素催化水解反应速度比较快,相比于尿素普通水解技术,尿素催化水解技术反应速度提高了约10倍以上,响应时间大大缩短,可达到在1 min以内 [17]。
尿素催化水解技术具有以下优势 [18]:运行成本低。尿素水解温度低,可以利用蒸汽提供热量,降低运行成本;与普通的尿素水解反应相比,尿素催化水解加入了催化剂,水解反应速度极大提高;设备布置更为灵活。
2.5. 尿素制氨技术对比分析
2.5.1. 各种工艺技术比较
对于反应时间、布置安装方式、主要设备材质、系统适应性及成熟等方面,尿素水解和尿素热解各有不同,不同的工艺也有不同的优缺点。
1) 系统响应性。对于NH3的需求信号响应时间,尿素热解系统通常为5~10 s,尿素普通水解技术一般为3~5 min。在尿素水解器的上部装有缓冲罐,可以改善水解反应响应时间长的情况,尿素催化水解的响应时间可达到1 min以内。
2) 设备布置、安装与检修。相比于尿素热解,尿素水解系统的布置方式比较灵活,可以采用单元制布置,也可以采用公用制布置。对于检修,尿素水解系统可以设置备用水解器,这样就使得检修时间更加灵活,不影响机组的正常使用。
3) 主要设备及材质。尿素水解的中间产物NH2COONH4会腐蚀水解反应器和管道,所以水解反应器采用耐腐蚀的316不锈钢;尿素热解反应过程中不会生成强腐蚀性的物质,通常选用304不锈钢 [19]。
4) 系统可靠性。炉内烟气换热技术在锅炉烟气中设置换热器,烟道内的大量灰尘则附着在换热器表面,从而导致换热效率降低、热量回收困难,且在使用过程中电耗增多,使用成本增加,影响锅炉运行的经济性 [20]。尿素水解技术容易出现管道堵塞,用低浓度的尿素溶液,并在过程中及时冲洗管道,在管道外面做好保温工作,一般可以有效地避免管路堵塞的问题 [20]。尿素水解反应器可设置备用设备,可靠性较高,而尿素热解炉只能单炉布置,没有备用装置,可靠性较低。在尿素催化水解工艺中,由于催化剂的存在,系统中的pH值大幅度的下降,从而加快了对水解反应器的腐蚀。催化剂的添加,改变了水解反应的途径,使得反应的活化能降低,因而加速了水解的速度,但是,由于催化剂的存在,也会降低反应的指前因子,进而使尿素的水解速度对温度的敏感性降低,因此,当机组负载改变时,尿素催化水解效果就会比普通尿素水解更差。目前,尿素普通水解工艺的应用比尿素催化水解工艺要多得多。
因此,尿素普通水解技术的可靠性优于尿素热解制氨技术及尿素催化水解技术。技术成熟度及业绩。尿素热解(电加热)制氨技术在之前应用广泛,技术相对较为成熟,但由于其能耗高,电厂使用成本较高,而且目前国家趋势为节能降耗,该方案不再盛行。尿素普通水解制氨技术和尿素热解制氨技术(烟气换热方式)比较成熟,已在国内很多机组中成功应用。在适应性方面,尿素催化水解比尿素普通水解低,所以目前在国内的使用率较低。
2.5.2. 各种工艺运行费用比较
按照常规2 × 660 MW超超临界机组,单台机组需氨量500 kg/h,年运行时间按5000 h计算时,尿素水解和尿素热解运行费用见表1所示。
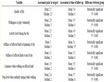
Table 1. Comparison of operation cost of urea ammonia production process
表1. 尿素制氨工艺运行费用比较
注:1) 运行费用中电费按厂用电费0.36元/kW,尿素2000元/t,辅助蒸汽60元/t,标煤800元/t,除盐水5元/t,压缩空气1元/m2。表中基础数据是参照常规2 × 600 MW级超超临界机组额定工况下运行数据 [13]。2) 表中各工艺的尿素耗量均按照100%的转化率进行计。
由表2可知:尿素水解制氨比尿素热解制氨运行费用低,其中,尿素普通水解制氨工艺运行费用最低。
2.5.3. 投资成本比较
按照常规2 × 660 MW超超临界机组,单台机组需氨量500 kg/h,年运行时间按5000 h计算时,尿素水解和尿素热解投资成本见表2所示。
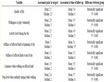
Table 2. Comparison of investment cost of urea ammonia production process
表2. 尿素制氨工艺投资成本对比
注:1) 单位:万元。2) 各费用参照近年来2 × 600 MW级超超临界机组液氨改尿素项目采购价。
尿素普通水解工艺和尿素催化水解工艺设备费用和建设成本较低,其中尿素热解制氨工艺中的烟气换热工艺最高。烟气加热尿素热解的气气换热器和反应热解炉价格较高,因此投资成本比较高。目前水解反应器通常采用一体化撬装模块化,安装费用较低;热解系统需要在SCR区进行改造,现场施工费用较高。
3. 结论
尿素直喷技术在我国脱硝工程中已有部分应用,但在实际运行中发现普遍存在尿素利用率低、副作用大等缺点;尿素催化水解由于加入催化剂的原因,系统中的pH值大幅度地下降,加速了对水解反应器的腐蚀,且使得尿素水解反应速率对温度的敏感度下降,从而致使尿素催化水解对于机组负荷变化的适应能力下降;尿素热解制氨中电加热方案存在电热器能耗高、运行成本高的缺点;尿素热解炉外气气换热方案存在运行设备体积大、占地面积大、在锅炉钢结构内布置换热器难度大,改造成本较高等缺点,也正因为此工艺系统缺点较多,应用极少 [21]。综合工艺特点、运行成本等因素,尿素普通水解制氨和尿素热解制氨中的炉内气气换热方案在国内的脱硝处理中运行情况良好,运行案例相对较多,具有较好发展前景。
NOTES
*通讯作者。