1. 引言
循环流化床燃烧技术是一种清洁燃煤技术,燃烧过程涉及气固流动、燃烧反应以及相间传热传质等 [1] [2],具有较高的燃烧效率和燃料适应性 [3]。
二次风系统是循环流化床锅炉中研究重点之一 [4] [5],其一方面能对密相区进行充分预混,有利于维持床温,另一方面让床料分布更加均匀,改善炉膛内壁磨损严重的情况 [6]。杨建华等 [7] 对循环流化床锅炉进行二次风射程试验时,发现通过增加喷口直径、二次风速、喷入点位置可以提升二次风穿透能力。程乐鸣等 [8] 对循环流化床锅炉二次风射流进行CFD数值模拟,研究其二次风风速等对炉膛物料浓度的分布和射流深度的影响。彭建升等 [9] 以新疆某热电厂320 t/h循环流化床锅炉为研究对象,并对二次风系统进行改造,最终使NOx排放值从400 mg/m3降至到50 mg/m3以下,同时床温、带负荷能力、减温水量等均有一定程度的改善。Zhang等 [10] 研究发现不同二次风配风方式会影响燃烧过程以及炉膛内的温度分布。Yan等 [11] 研究了二次风对烟气的影响,结果表明沿着炉子宽度,侧壁附近的氧气消耗几乎是中间部分氧气消耗的两倍。Zheng等 [12] 通过实验发现与一次风相比,二次风对床料的影响较小,但是随着二次风配比的增加会导致床料在密相区聚集。Xie等 [13] 对工业循环流化床锅炉进行了模拟,结果表明二次风配比增加可以有效降低NOx排放,但对SO2的降低没有显著影响。
综上所述,二次风对炉内燃烧产生了重要的影响,但随着对大型循环流化床的可靠性要求越来越高,对锅炉布置要求也越来越高。在目前常用的二次风布置中,将面临二次风穿透能力不足导致炉膛中心氧气供应不足 [14]、燃烧不充分 [15] 的问题。虽然通过加大二次风配比 [16] [17] 可以改善锅炉燃烧和流动不均匀性,但是会导致风机耗能加大,且会影响颗粒的向上流动。本文针对循环流化床锅炉存在的流动不均匀、炉膛中心氧气供应不足的问题,通过数值模拟的方法,研究不同二次风入射角度对炉膛内部流动和燃烧特性的影响的研究,提出改进方案,帮助循环流化床锅炉实现高效和安全运行。
2. 锅炉概述
本文以某240 t/h循环流化床锅炉为模拟研究对象按1:1的比例进行三维建模。考虑到模拟过程的复杂程度,对研究模型进行简化,仅保留炉膛部分,如图1所示。该锅炉将炉膛底部设置为一次风入口;在炉膛下部前墙设置六个进煤口,直径为800 mm;二次风口共有25个,前墙、后墙分别布置12、13个,直径均为240 mm;两个烟气出口设置在炉膛后墙顶部;返料口设置在炉膛后墙下部。
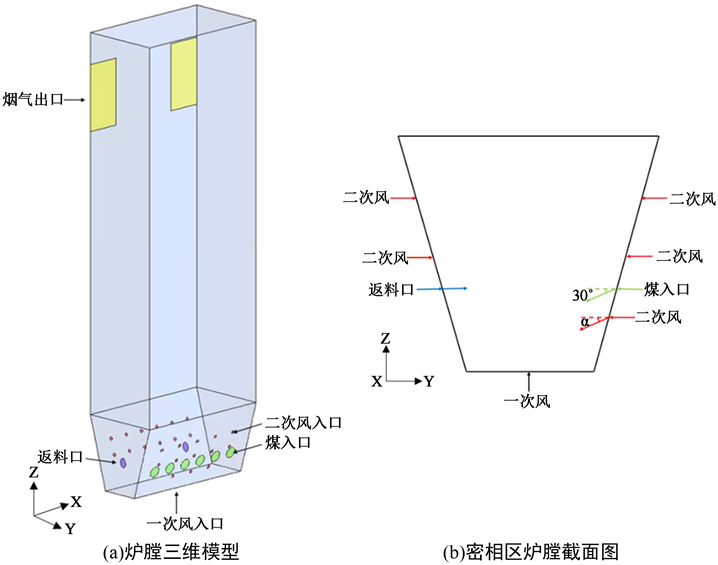
Figure 1. Furnace physical model diagram
图1. 炉膛物理模型图
3. 数学模型及参数设置
3.1. 数学模型
本文主要模拟循环流化床锅炉内部的燃烧及各组分的分布,因此选择欧拉方法中的欧拉模型,其中包括气相和固相的连续性方程、动量守恒方程和能量守恒方程。
1) 连续性方程
气相:
(1)
固相:
(2)
2) 动量守恒方程
气相:
(3)
固相:
(4)
3) 能量守恒方程
气相:
(5)
固相:
(6)
式中:αg、αs分别为气固相的体积分数;ρg、ρs分别为气固相的密度;
、
分别为气固相的速度;Ksg、Kgs分别为气固相间的曳力系数;pg、ps分别为气固相的压力;
、
分别为气固相应力应变张量;
、
分别为气固相间质量交换;hg、hs分别为气固相的焓值;Sg,q、Ss,q为包含化学反应热和其他体积热源的源项。
该模拟为三维非稳态气固两相流,采用半隐格式压力关联方程算法(SIMPLE)实现压力与速度耦合计算,湍流模型选择Realizable k-ε模型,气固相间曳力模型选择Gidaspow曳力模型,选择Syamlal模型作为颗粒相间曳力模型;使用UDF定义了燃煤反应中的挥发分析出反应以及焦炭燃烧反应,用有限速率/涡耗散模型实现可燃气体燃烧反应;根据循环流化床锅炉内部复杂的光学环境,选择了P1辐射模型作为辐射换热模型,并使用Gunn模型描述相间传热模型。模拟时间步长为0.003 s,模拟至炉内流动与燃烧较为稳定后进行数据分析。
使用ICEM软件对该模型进行网格划分,考虑到下炉膛部分有颗粒浓度较高,且相间作用较为剧烈,而上炉膛部分颗粒浓度较低,相间作用较弱,因此需要对下炉膛部分进行网格加密。上炉膛部分采用结构化六面体网格,并对下炉膛各进口进行加密,最终得到网格数为1,076,888。
3.2. 边界条件
该模拟参数如表1所示,将一次风、二次风入口设置为气相速度入口边界条件,给煤口设置为质量流量入口边界条件,将二次风的总风量和给煤口的总流量进行均匀分配;壁面温度为定温边界条件,上、下炉膛分别设置为800 K和1000 K。
3.3. 煤质参数
本文中使用的煤质参数如表2所示。
3.4. 数学模型验证
为保证本文数值模拟的准确性,使用文献 [18] 中的模拟参数,结合本文的数值模拟方法对文献的循环流化床燃烧实验装置进行了数值模拟,其模拟结果如图2所示。
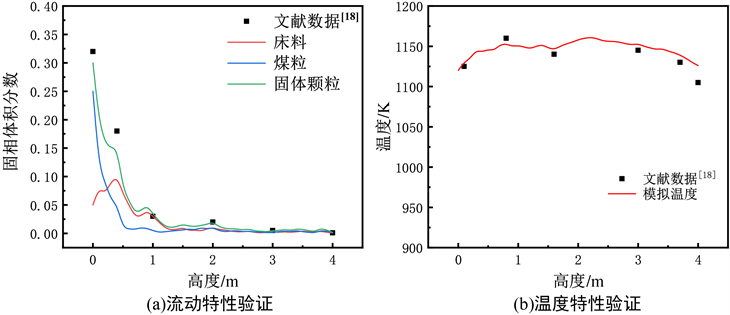
Figure 2. Numerical simulation method verification
图2. 数值模拟方法验证
其中图2(a)为流动特性的对比,红色曲线为床料体积分数,出现了先增大后减小的趋势,床料大部分聚集于密相区;蓝色曲线为煤粒体积分数,由于煤粉大量参与反应因此煤粒体积分数迅速下降;绿色为总固体颗粒的体积分数,其大致趋势以及数值均与文献中数据相近。图2(b)为温度值的对比,可以看到模拟的结果与文献中的实验结果较为接近,温差均在15 K以内。因此我们认为本文中的数值模拟方法与实验结果吻合良好,增加了该数值模拟方法的可信度。
4. 结果与讨论
二次风在炉膛内主要起到补充燃烧以及增强炉膛内的扰动的作用,工况一到五分别对应α为0˚,15˚,30˚,45˚以及60˚。
4.1. 流动特性分析
由图3可知,随着α的增大,二次风入口区域风速逐渐减小,这是因为α增大二次风进入时的纵向速度不断增大,而这个速度与一次风速度方向相反,故出现了入口区域的气相速度较小。此外,随着α的增大,逐渐出现了炉膛中心处气相速度较小而近壁面处速度较大的情况,这是因为α的增大使得二次风的横向穿透深度逐渐减小。
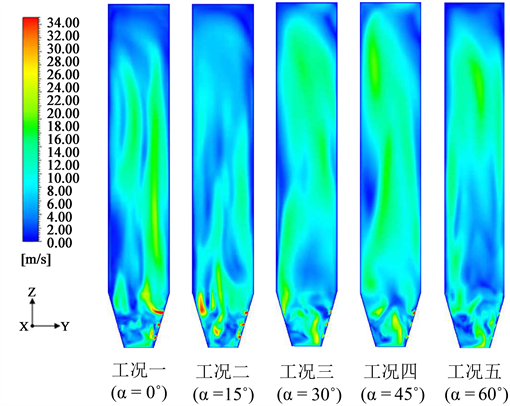
Figure 3. Vapor velocity distribution of X = 0 section under different conditions
图3. 不同工况下X = 0截面气相速度分布
从图4中可以看出,随着α的增大,床料在炉膛内受到的影响越大,其原因为二次风的角度增大使得二次风对床料的作用更靠下,影响了更多的床料,增强了扰动。工况一的二次风入口为水平方向,因此对床料的作用极小,不利于炉膛内部的流动与传热;工况二类似于工况一,最底部的床料分布几乎没有改变,工况三、四拥有较好的床料分布,工况五存在部分床料堆积在底部炉膛近壁面处的现象。
图5为不同二次风入口角度下的Z = 1 m床料体积分数分布云图。由图可知,工况一图下方出现了高浓度床料堆积,这是因为α为0˚的情况下,二次风直接将一部分床料吹至炉膛壁面处;工况二、工况三和工况四中炉膛中心有较多的床料分布,整个平面上的分布较为平均;工况五中的床料分布整体体积分数较低。
结合图4与图5可知工况一、二受到二次风的影响小,不利于密相区的气固混合,工况三、四表现较为相似,床料分布均匀,工况五出现了部分床料堆积的现象。从流动特性分析可知,工况三(α = 30˚)、工况四(α = 45˚)都表现了良好的流动特性。
4.2. 温度场分布
图6为不同二次风入口角度下的x方向中心截面处温度分布云图。由图可见,工况一中下炉膛温度低,其原因为该工况下二次风对没有作用到密相区底部的床料,进入的煤颗粒不能较好的完成破碎、燃烧的过程,同时没有为底部的燃烧提供充足的氧气,导致低温区域较多;工况二在炉膛中部出现高温区域,但该工况下二次风对床料的作用较为有限,因此高温区的温度较低;工况三在较低高度处就出现高温区域,高温区域温度较高,整体温度分布平均;工况四在炉膛上部出现了较大面积的高温区域;工况五的下炉膛同样出现较大的低温区域,而近壁面处高温区域较多,不利用炉内高效燃烧,其原因为该工况下二次风的横向穿透深度较小,在运行过程中不能为炉膛中心提供充足的氧气。
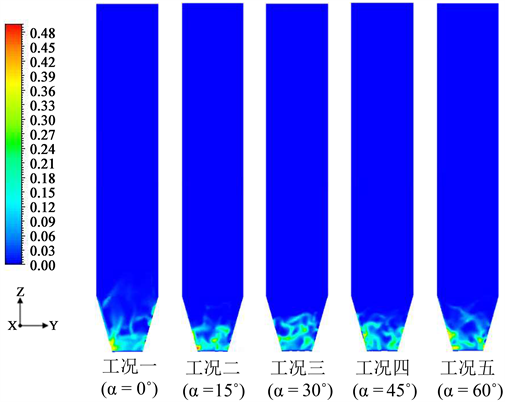
Figure 4. Distribution of bed material volume fraction of X = 0 section under different conditions
图4. 不同工况下X = 0截面床料体积分数分布
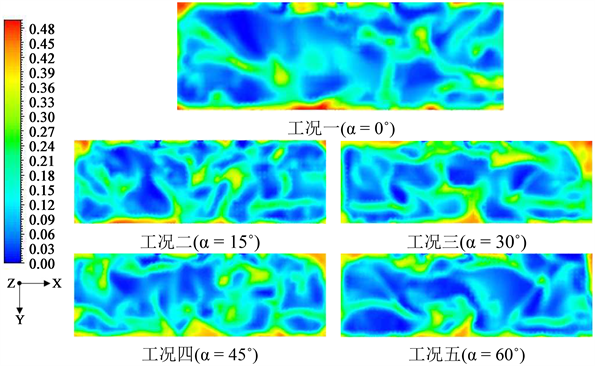
Figure 5. Distribution of bed material volume fraction of Z = 1 m section under different conditions
图5. 不同工况下Z = 1 m截面床料体积分数分布
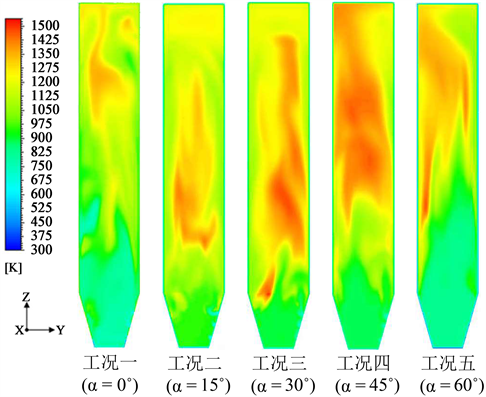
Figure 6. Temperature distribution of Y-Z section under different conditions
图6. 不同工况下Y-Z截面温度分布
图7为不同二次风入口角度下的z方向平均温度变化曲线。从图中可以看出α = 0˚时,整体温度很低,最高温度仅有1250 K;α = 30˚时最早出现高温区域,在8 m处就出现了约1300 K的高温区域;α = 45˚时出现最高温度,最高温度约为1450 K;α = 60˚时最晚出现高温区域,12 m处才出现1200 K的温度。所以根据温度场分析,可知工况3燃烧效果最好,温度分布最均匀。
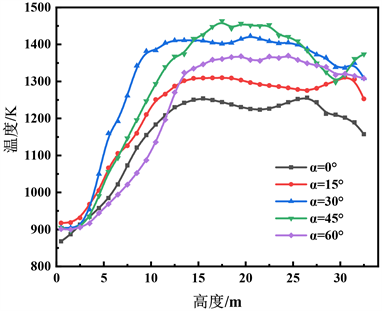
Figure 7. Average temperature change curve in z direction under different working conditions
图7. 不同工况下z方向平均温度变化曲线
4.3. NOx质量浓度分析
图8为不同工况下NOx质量浓度曲线。由图可见,随着α的增大炉膛下部的NOx质量浓度逐渐增加,但随着高度的增加,NOx的质量浓度相差逐渐变小。其原因是α较大时,炉膛下部氧气浓度较高,形成了富氧燃烧区域。
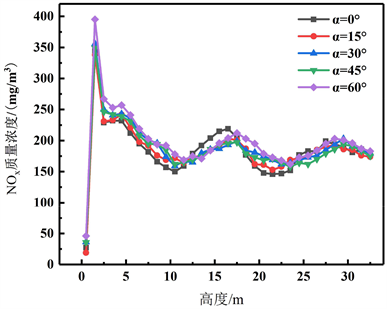
Figure 8. Variation curve of average mass concentration of NOx in z direction under different conditions
图8. 不同工况下Z方向NOx质量浓度变化曲线
综合流动特性、温度场分布以及NOx排放的特点可知,工况一、二的二次风纵向穿透深度小,对床料作用小,不利于密相区的气固混合;工况五的二次风横向穿透深度过小,不能及时补充炉膛中心燃烧需要的氧气,致使炉膛下部温度过低;工况三、四床料分布都较为均匀,工况四最高温度略高于工况三,但工况三温度分布更加均匀。综上所述,工况三(α = 30˚)为最佳二次风角度。
5. 结论
本文利用数值模拟的方法探究了不同二次风入射角度对炉膛内部流动和燃烧特性的影响,其结论如下:
1) 随着α的增大,二次风入口区域风速逐渐减小,且出现中间速度低而近壁面处速度高的现象。
2) 随着α的增大,纵向分速度增大,纵向穿透深度增大;初始时大量的床料位于炉膛底部,纵向穿透深度大会对更多的床料产生作用,有利于气固混合效果。
3) 当α过小时,其纵向穿透深度小,影响煤颗粒的破碎和燃烧过程;当α过大时,其横向穿透深度小,不能及时的辅助炉膛中心部分的燃烧,易造成较大的气体不完全燃烧损失。
综合考虑流动与燃烧的结果,工况三(α = 30˚)的角度设置最为适宜。
基金项目
国家重点研发计划项目(2021YFF0600605)。
NOTES
*通讯作者。