1. 引言
汽车车身通常是由复杂的曲面形状薄壁类零件焊装而成,焊装质量直接影响着整车的质量 [1]。因此,汽车车身焊装夹具在汽车车身焊装线上占有举足轻重的地位,其设计制造对汽车的生产规模、生产效率和质量都有着至关重要的影响,它的快速高效设计与制造是汽车制造业快速响应市场需求的重要条件之一 [2]。一般的焊装夹具设计方法基本上都是通过设计人员依据自己的设计经验进行设计的,这种方式不仅耗时耗力,而且对设计人员也有很高的要求。目前,国内针对于车身焊装夹具研究较为广泛的方向是建立参数化零件库,并取得了一定成绩,如四川大学、新疆大学、江苏科技大学的科研工作们均研究了零件库的设计 [3]。但在后续焊装夹具装配布置等方面仍存在很多困难。我国在车身焊装夹具辅助设计系统方面起步较晚,技术落后,在车身焊接夹具辅助设计系统上大多没有进行深层次的焊接夹具二次开发。作为计算机辅助设计中最受欢迎的应用技术之一,参数化设计是通过改变图形中某一部分或某几部分的约束尺寸,从而实现尺寸对图形的驱动,从而自动完成对图形中相关部分尺寸的改变,是一种基于约束的产品描述方法。本文主要根据白车身夹具设计过程中的工艺特点和设计要求,运用基于实例推理技术和基于参数化的实例求解技术来实现夹具的智能化推理设计。
2. 车身焊装夹具方案规划研究
进行夹具设计前应首先做出焊装夹具方案的前期规划,包括分析工件的几何形状特征和夹具设计工艺要求分析等内容。一般的方案规划是由夹具设计人员首先分析工艺文件,依据工件的定位点信息手动创建特征,之后确定具体方案,但这种方式操作繁琐,效率较低。本系统的车身夹具方案规划将采用基于CATIA二次开发技术的定位点自动解析创建和基于实例推理的车身夹具方案的自动设计。
2.1. 定位点信息解析
本夹具中研究对象为RPS系统中的定位点。RPS (Reference Point System)即汽车设计、制造过程中贯穿前后的基准点系统 [4]。
工艺文件中的RPS点信息主要包括RPS点名,定位点的坐标以及定位点的坐标公差。其中RPS点名中包含了定位点的序号,定位方式及定位方向等信息。传统RPS点的创建方式是由设计人员手动的进行绘制,在本系统中通过程序读取工艺文件信息来进行自动创建。
传统创建RPS系统定位点的方法是由工程师根据工艺文件中RPS Table中RPS点的名称、坐标及公差信息等参数,手动添加至车身当中。本系统中使用了基于CATIA的二次开发技术来实现RPS点参数的自动提取保存。
2.2. 定位点特征的自动创建
在提取RPS点的信息之后,一般的开发方式是通过手动创建RPS点,这种方式较为繁琐,效率较低,不利于开发周期的缩短,因此本系统开发了RPS定位点特征的自动创建功能,可以帮助开发人员实现“一键式完成”,同时加入了计算机技术中“多线程”技术手段来实现多个RPS点的并发创建,提高了工作效率,极大的缩短了产品的开发周期。
程序首先根据前面获取到的DataTable中的定位点的坐标信息,创建每个定位点的HybridShapePointCoord对象,并对每个定位点添加对应的属性值。对于部分面形状定位的RPS点,还需要再定位点的基础上创建大小为20 mm × 20 mm的网格面特征。网格面特征的创建首先在定位点的基础上创建定位点与工件表面的法向线,然后以创建的法向线为Z轴,结合定位点坐标创建笛卡尔坐标系,然后获取笛卡尔坐标系的X轴和Y轴来创建对应的特征线,便于后续的装配操作。然后以坐标系的原点为参考点,创建大小为20 mm × 20 mm的正方形,在每条边上创建七个点,将各个点依次相连即可得到网格面,由于每个网格面都是相对较密,因此每个网格面去依次创建的话会花费很多时间,不利于提高效率,因此采用多线程来解决该问题。图1展示了整个定位点特征和网格面创建的流程。
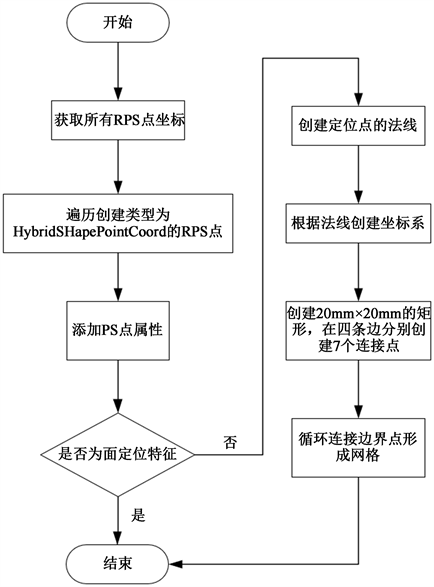
Figure 1. Flow chart of positioning point creation and mesh face creation
图1. 定位点创建及网格面创建流程图
3. 基于实例的夹具推理设计
基于实例推理(Case Based Reasoning, CBR)是一种基于过去经验的问题解决方法,现已被广泛应用于多种智能领域 [5]。基于实例推理的设计思想就是将设计经验按某种方式存储在实例库中,然后利用系统所建立的搜索机制来进行实例的搜索以获取待求的解,对于不满足条件的实例进行重新修改来适应当前问题,从而得到新得知识实例。根据Aamodt & Plaza所提出的4R模型,整个推理过程被分为四个阶段:检索(Retrieval)、重用(Reuse)、修正(Revise)和更新(Retain) [6]。
3.1. 基于实例推理的相似度计算
基于实例的推理技术的检索机制本质是将用户输入的特征集
与实例库中特征集
对比,找到相似的特征就可以使用该实例
来作为用户求解实例的方案解
,即
。该式成立的前提条件是问题和实例库实例的特征集的相似度能够大于一定的阈值,因此就要先对
与
的相似度值进行计算。合理的相似度计算的检索算法应基于两个方面来实现:一是能够进行快速高效的进行检索,二是能够最大程度的解决当前的问题,提供最优的解决方案。
进行相似度计算首先要构建合理的相似因子集,本系统根据夹具设计过程中的关键信息来进行构建,主要相似因素包含以下五层:工件层C1,单元类型层C2,气缸信息层C3,工序类型层C4,客户类型层C5,进行相似度评价计算时就在这五个大类层次上进行评价。各相似因子又可进行具体分类:
工件类型因子C1:用于描述车身夹具所应用的工件类型,典型的类型包括以下:侧围、翼子板、车门内板、行李箱外板、机舱、地板、总拼等。
单元类型因子C2:用来指定夹具单元模型的或需求方案的单元类型包括支撑、压紧、空压、定位、平推等。
气缸信息因子C3:包括气缸的类型、气缸的行程角度等信息。
工序类型因子C4:描述加工时的工序信息,常见的典型工序类型因子包括:侧边冲压、车门支撑、侧围焊接等。
客户类型因子C5:客户类型决定了焊装夹具单元的选用标准,常见的客户类型有上汽大众、长城、东风日产、奔驰、特斯拉等。
3.2. 基于层次分析法的夹具实例特征项权重计算
在夹具的实例单元模型中,不同属性特征对夹具设计方案的影响程度不尽相同,所以影响因子的大小也不同,因此在进行相似度计算时各个特征的权重值也不同,要对各个特征项的设置不同的权重值来确定各个特征项对夹具整体设计方案的影响程度大小 [7]。本系统采用层次分析法来计算夹具实例特征项的权重值。最终确定目标层为选择出合适的夹具实例模型,准则层为上述确定的相似因子,方案层为实例库中所有的实例单元,图2对层次模型进行了构建。
本系统中针对权重值的计算仅需计算出准则层,即上述构建的相似因子的权值即可。根据相关车身夹具设计专家的意见并参考大量相关文献最终得出判断矩阵为表1所示。
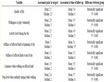
Table 1. Judgment matrix of body fixture features
表1. 车身夹具特征项的判断矩阵
求解O-C的特征值,可解得
,特征值法求出的权重向量
。
得到特征值后要对判断矩阵进行一致性检验,计算出一致性指标及一致性比例,计算一致性指标CI的公式为:
(1)
由公式得到CI = 0.0251,计算一致性比例CR的公式为:
(2)
查表得RI = 1.12由公式得CR = 0.0224,因为CR < 0.10,因此该判断矩阵的一致性符合要求。
3.3. 夹具实例相似度值计算数学模型建立
输入的求解问题的信息与实例库夹具单元的相似度计算应该通过相似因子值的相似度来构建相似度矩阵。假设
为待求解问题的相似因子所对应的属性值,
为实例库中夹具单元对应的相似因子属性值,那么两种方案之间对应的相似度矩阵即为:
(3)
在相似度矩阵中只有对角线元素表示相同的相似因子比较后得到相似度值,其他元素为非相同相似因子之间的比较不具备可比较性,由此得到相似度计算数学模型为:
(4)
其中,相对于其他相似因子来说,工件类型和单元类型更为重要,这两个相似因子需要模型两方进行完全匹配。因此新的相似度计算模型为:
(5)
式中,
为工件类型相似因子的相似度值,输入实例特征的相似因子与实例库实例的相似因子值相同则
,反之
。
为单元类型相似因子的相似度值,比较相同则
,反之
。
为其余相似因子的相似度值,
为各个相似因子的权重值。
根据相似度计算公式来计算用户输入与实例库模型之间的相似度值,进而得到产品的相似度,最后获取到最相似的夹具单元案例,为基于实例推理的夹具单元设计奠定了基础。
3.4. 基于参数化驱动的车身夹具实例的调整
在进行相似度计算之后,得到相似度最高的单元实例并调用,但调用后的实例单元可能与实际的工况条件产生冲突,此时就需要对实例单元进行修改调整,完成自适应的夹具设计 [8]。其中产生干涉的主要影响因素包括两大方面:实例单元立柱和Base板的距离问题,实例单元和焊枪之间的干涉问题。要想对上述两个问题进行解决就需要对夹具单元整体进参数化设计,通过尺寸驱动实例单元的整体进行变形设计,实现对Base板的接触距离的调整及规避对焊枪的干涉。
3.4.1. 夹具单元实例的参数化模型建立
因为本系统设计的夹具单元都是完整的单元装配体,如果仅针对零件进行参数化设计无法满足本系统要求,因此本系统在装配体模式下进行结构尺寸参数化定义,采用变量驱动的参数化来作为单元调整求解的手段。
在夹具单元实例库中实例模板的三维模型上定义的单元的参数变量。以图3左图中给定的单点压紧单元中定义的尺寸变量为例来定义三维模型中的参数变量结果如图3中的右图所示。
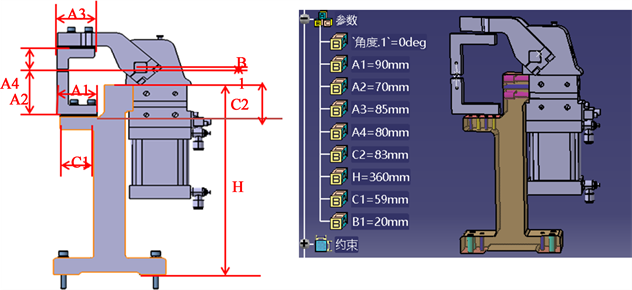
Figure 3. Create a dimension parameter variable
图3. 创建尺寸参数变量
对于参数变量的获取、修改,通过获取Product对象的Parameters的子项来获取相应的Parameter对象,然后对Parameter对象的Value属性进行赋值即可完成对相应尺寸的修改。
3.4.2. 支撑板的参数化设计
支撑板即BASE板是汽车焊装夹具的重要组成部分。其为整个工件的尺寸精度检测提供基准,同时为整个夹具单元的支撑,调整提供支撑 [9]。本系统将BASE用作实例库中的标准实例,对其进行参数化设计来适应不同的工作情况,避免重新设计的麻烦,提高产品设计效率。
为了实现程序的自动处理,首先将参数化设计规则进行归纳,规则如表2所示,图4展示了两个底座的样式。
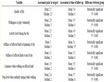
Table 2. Parametric design requirements of BASE board
表2. BASE板参数化设计要求
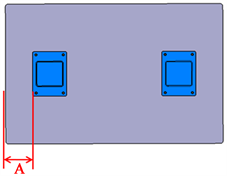
Figure 4. Style for installing two bases
图4. 安装两个底座的样式
程序交互式的获取用户需求的BASE的长度和宽度要求,然后根据上述底座定位点的位置要求规则安装特定个数和位置的底座。
4. 系统实现与测试
本系统基于CATIA V5和Microsoft Visual Studio 2017平台,利用CATIA Automation接口,使用C#进行了该系统的开发
系统首先导入车身模型,打开工艺文件,进行导入工艺文件,生成RPS点。如图5所示。
导入支撑版模块,根据车身大小,自动匹配不同支撑板样式,如图6所示。
根据实例推理模块提示框输入特征条件,系统开始计算输入条件与数据库内夹具单元相似度,匹配相似度最高的单元。点击即可插入夹具,插入后夹具单元会根据支撑板高度及干涉情况自动调整参数。对于匹配的实例也可进行手动参数修改。结果如图7所示。
由装配结果可以看出,在匹配到夹具单元后,根据单元高度与BASE板的距离对单元支撑腿进行了自动参数调整,同时对与车身及焊枪产生干涉的单元进行了位置调整,按照设定规则进行了角度旋转,最终结果满足设计需要。
5. 结论
本文研究了车身焊装夹具设计方法,设计开发了基于实例推理技术的车身夹具智能辅助设计系统并完成系统测试,取得以下成果。
1) 对车身夹具进行了方案规划,开发了系统工艺文件导入模块,实现了RPS信息的智能化导入。
2) 将基于实例的推理技术应用于车身夹具开发中,并利用层次分析法对单元特征权重进行计算,完成了车身夹具智能辅助设计系统的搭建。
3) 对车身焊装夹具及支撑板进行参数化设计,使其可以根据系统需要智能匹配相应参数,也可适应推理设计夹具的参数修改。
由工程中实际焊装夹具设计测试表明,利用本设计系统辅助汽车焊装夹具设计可显著提高设计效率,缩短设计开发周期,有效降低设计工作难度,对夹具设计过程的简化及新车型上市速度的提高都可起到一定的推动作用。