1. 引言
随着现代外科技术和治疗效果的提高,患者术后恢复情况和生活质量越来越受到重视。对于胃肠道疾病来说,消化道重建术是一种具有良好效果且能够提高患者生活质量的手术。消化道重建手术是一种将病变组织切除,再把剩余健康的组织重新缝合起来,以实现具有良好功能的消化道的手术 [1] [2] [3] 。目前,在临床上常用的缝合方式分为手工缝合和机械吻合,其中,机械吻合相比于手工缝合,具有操作简单,效率高且一致性好等特点,因此机械吻合也被更多地应用于微创手术。但在术中,由于人为因素、器械原因或者患者身体条件所导致的吻合口并发症等问题不容忽视 [4] 。
吻合器在胃肠道手术中的操作可以分为压榨、切割和吻合,其中压榨动作对于最终的吻合效果十分重要。陈丹和Morita等人分别通过直肠癌临床手术和猪小肠离体吻合实验,发现在对组织进行吻合前,对组织施加适当压力并保持一段时间,能够有效提高吻合质量,降低吻合口瘘的发生率 [5] [6] 。Cong等人将长海医院738例直肠癌患者病历进行了对比分析,发现专业的直肠外科医生和普通外科医生操作手术后并发症的发生概率分别为3.9%和11.3% [7] 。Bin Qiu等人对电动吻合器在中国开展了临床研究,通过评估电动血管吻合器在有电视辅助胸腔镜的肺叶切除术中的表现,最终96%的医生对设备比较满意 [8] 。Ali Akil等人和Wataru Shigeeda等人分别使用iDriveTM电动吻合器和SigniaTM电动吻合器进行临床试验,并与ENDO GIATM手动吻合器进行比较,发现电动吻合器效率更高、漏气概率更小且能够消除手动击发力,能够更精准地实现后方交会 [9] [10] 。在国内,孙宝峰等人发明了一款智能压榨电动腔镜吻合器,能够在吻合组织前,实现15秒预压榨 [11] 。因此,提高器械的电动化和智能化是非常有必要的。但目前电动吻合技术发展尚不完善,吻合过程中的相关参数仍比较模糊。
本文旨在探究一种新的压力检测方法,并完成检测部件的结构和电路设计,确保在吻合压榨过程中实现压力可控及可视化,实时判断组织状况,降低人为因素对手术质量的影响,帮助医生更加便捷、快速、有效地完成手术,进一步缩小吻合口并发症的发生概率 [12] 。
2. 材料与方法
2.1. 电动吻合器的系统框架设计
在微创消化道重建手术中,医生需要将吻合器深入病人已构成人工气腹的腹腔中,在辅助内窥镜的帮助下,通过调整器械的位置和角度,对病变组织进行抓取、切除、压榨、击发等动作,在完成重建手术后再将切除的病变组织和器械取出。为了满足手术的需求,电动吻合器应该具备压榨、击发、前端执行机构的转弯和自转等基本功能。由此,设计电动吻合器的系统结构框图如图1所示。整个系统主要包括电控模块和机械结构两大部分。机械结构中的压榨机构和击发机构可分别实现电动吻合器的压榨和击发动作;转弯机构能够保证前端执行机构的转弯和自转动作;传动机构将由电机提供的输出转矩转化为压榨和击发所需的水平动力 [13] 。电控模块中,电源电路模块为系统提供5 V直流电源;24位ADC采样电路通过高速采集压力检测模块和阻抗检测模块提供的信号,并传入主控模块进行计算分析,通过显示器模块实时显示组织压力和阻抗的变化;预设压力和阻抗阈值,通过主控模块调控电机驱动模块控制电机运动,并由压力检测模块和阻抗检测模块提供反馈控制参数。
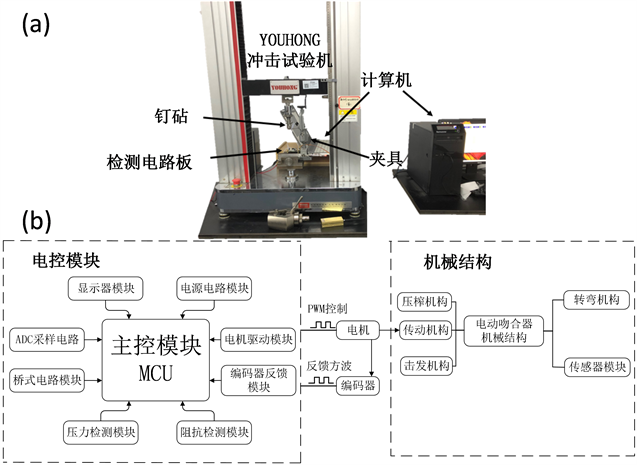
Figure 1. (a) Physical diagram of pressure calibration test platform. (b) Structural block diagram of electric stapler system
图1. (a) 压力校准实验平台实物图;(b) 电动吻合器系统结构框图
2.2. 电动吻合器的机械设计
2.2.1. 电动吻合器结构设计
不论机械吻合器或目前的大多数电动吻合器在使用过程中都缺少关键的反馈参数,其主要原因是受制于吻合器的体积及其传动机构。伊桑·柯林斯将压力传感器至于吻合器的传动机构中,通过电机带动传动杆,对传感器进行挤压,间接检测吻合器执行端的输出压力 [14] 。本研究基于系统设计框架,参考传统吻合器结构,进行电动吻合器结构设计,并对吻合器钉砧结构进行创新性设计,以实现输出压力的直接检测并将压力传感器和阻抗传感器的内置于钉砧内部 [15] ,其整体结构如图2(a)所示。并将压力传感器和阻抗传感器模块化处理,如图2(b)所示,在压榨过程和击发过程中,都能够实现对于压力和阻抗的检测。
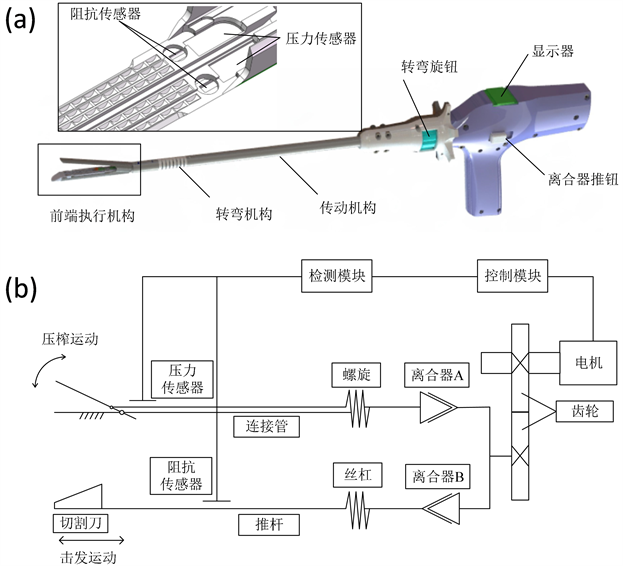
Figure 2. Schematic diagram of structure design of electric stapler. (a) Overall structure; (b) Schematic diagram of sensor layout and clutch function
图2. 电动吻合器结构设计简图。(a) 整体结构;(b) 传感器布置和离合器功能示意图
2.2.2. 钉砧的有限元分析
胃肠器官主要由粘膜、粘膜下层、外肌层和浆膜四层组织构成,因其分层和复杂的结构而表现出各向异性和强非线性的力学特性。在被施加的过程中,组织内会出现重新排列现象,研究对粘膜、粘膜下层和外肌层(标号为1、2、3),建立超弹性本构模型,如式1所示。
(1)
其中,
代表基层组织应变能,C代表右柯西–格林应变张量,
代表第i层纤维应变能,
代表第i层与第j层纤维之间的相互作用应变能。
由于生物组织是一种超弹性材料 [16] ,在其受到压力时会发生较大形变,但由于其几乎不可压缩性,体积几乎不会发生变化,因此将组织的应变能分为体积应变能和等体积应变能两项。
(2)
(3)
(4)
其中,
为组织应变能,
为体积应变能,
为等体积应变能,r为基底矩阵特征值,J为可变雅克比矩阵,c1和α1表示组织的剪切特性,
是右柯西–格林应变张量等容部分的第一个不变量 [17] 。取Kv = 88.754 MPa,r = 71.594,C1 = 0.028 MPa,α1 = 0.814代入,结合Baker R S等人对组织在不同压榨强度下愈合情况的研究 [18] ,最终确定压榨力的范围为19.6 × 10−3 MPa至156.8 × 10−3 MPa。
本研究设计了一种应变式压力传感器,为使传感器内置于器械中,需要对钉砧结构进行重新设计,在保证应变程度有效性的同时确保结构的刚度满足要求。通过有限元分析辅助结构设计,选择恰当的位置放置传感器,参考传统吻合器执行端尺寸,选用120-1AA应变片(阻值为120 ± 2 Ω,基底尺寸为3.0 mm × 2.0 mm,丝栅尺寸为1.0 mm × 1.0 mm)搭建。因此在钉砧钉槽面开设2个(5.0 ± 0.5) mm × (3.0 ± 0.5) mm的槽口,在背面开设一个(10 ± 0.5) mm × (5 ± 0.5) mm的槽口,用于放置应变片。
在Solidworks 2018中将钉砧结构分为三段,分别为前端、载荷加载区和网格细化区。使用ANSYS19.2进行结构静力学分析,连接方式选择No Separation (未分离),过程中先使用0.7 mm正四面体网格进行划分,比较实验结果后,为验证电路设计的可行性,对网格细化区的网格精细化为0.5 mm,并对钉砧结构进行多次修改,最终确定最优结构。
2.3. 电动吻合器的检测模块设计
吻合器电动化控制可以减少手术风险、提高操作的一致化率,从而降低手术后病发症的概率。为实现压榨和吻合时的智能控制,需要获取组织参数作为反馈控制依据,本研究研制并使用隔离电源模块输出+24 V电压,经WRA2405S-3WR2电源模块转换输出5 V电压供检测模块使用。通过两块线性稳压芯片输出+3.3 V和−3.3 V电压,供后续检测电路使用。
为实现传感器装置的内置,通过自研制压力传感器,以完成压榨和吻合过程中,对组织状态的实时检测。同时为克服手术过程中体内热能对压力传感器的影响,通过构建惠斯通四可变电阻电桥消除温度的影响。在未进行压榨时,使用可变电阻对检测电路进行调零,消除机械结构塑性形变造成的检测误差。针对仿真结果中的钉砧受载应变量级,使用ADS1256对电压信号进行高精度采集,将信号传递到单片机中,使能串口接收发送数据,实现对组织参数的实时检测。
3. 结果与讨论
3.1. 多参数检测钉砧的有限元分析
根据吻合器实际使用过程中钉砧的运动情况,将钉砧与传动结构的连接处施加固定约束,使用0.7 mm正四面体网格进行划分,共计划分126,689个节点和74,515四面体网格。钉砧材料选择316医用不锈钢,在载荷加载区施加逐渐递增的连续载荷(从0 MPa至19.6 × 10−3 MPa,再由19.6 × 10−3 MPa至156.8 × 10−3 MPa两个阶段),观察发生应变区域如图3所示,结果表明钉砧刚度和强度能够满足实验载荷,其只发生塑性形变,最大应力集中和最大应变处皆位于两翼连接处,最大应力为68.805 Mpa,网格细化区的应变为1.0695 × 10−5 mm/mm至1.0618 × 10−4 mm/mm,故在此布置压力传感器。
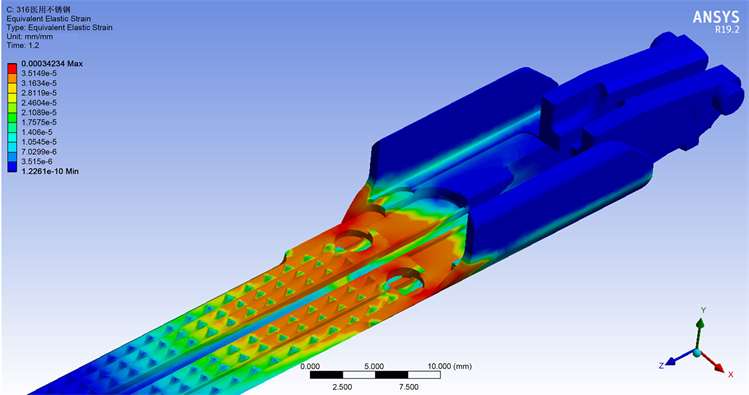
Figure 3. Stress strain nephogram of the nailing anvil (electronic version is color picture)
图3. 钉砧受力应变云图(电子版为彩色图片)
由于应变片为Cu-Ni系合金箔应变片,K值取2.1,同时为方便计算,应变范围取1.1 × 10−5 mm/mm至1.1 × 10−4 mm/mm,则应变片电阻的变化范围为(2.1 × 1.1 × 10‒5 × 120) Ω至(2.1 × 1.1 × 10‒4 × 120) Ω,即0.0028 Ω至0.028 Ω,应变片两端的电压变化量级为10−7 V。
3.2. 压力传感器的测试与校准
由于使用内置传感器,因此需要根据测量构件材料的不同对传感器进行调试和校准,故搭建如图1(a)所示的测试平台。本研究使用YOUHONG冲击试验机(型号:UH6503;最大负荷:5000 N;精度等级:0.5级;额定功率:750 W;输入电压:220 V)进行试验,将钉砧夹于夹具上,并固定于压力试验机上,将压力试验机的下降速度设置为2 mm/min,并以8 mm/min速度使构件卸载,通过电路板与计算机收集数据,整理计算完成压力传感器的数值校准。
研究通过实验测量,获得构件受力与施力时间的曲线及函数,以及在这个过程中电压与施力时间的曲线与函数,经过反解受力时间获得构件受力与电压的曲线与函数,完成压力传感器的测试与校准,写入单片机中完成吻合器在手术过程中压力的实时检测。通过实验仪器获得压力与时间的曲线,以秒为步进单位,求和平均一秒内的压力值,利用GraphPad Prism进行重新绘制,得到压力随时间变化的函数曲线如图4(b)所示。
本研究使用PCB电路板采集电压信号,通过Python编写程序读取串口信号,选用系统时钟作为计时方式,设置ADC采样率为50 SPS,共采样3312组数据,以秒为单位,求和平均一秒内的电压值,并绘制电压随时间变化的函数曲线,如图4(c)所示。
将压力和电压分别与时间进行多项式拟合,得到其通用方程为
,其中a、b、c、d、e为拟合常数,其值如表1所示。为得到电压随压力变化的函数关系式,将压力与电压作为自变量与因变量进行多项式拟合,得到两者的关系式如下:其R2 = 0.9936:
(4)
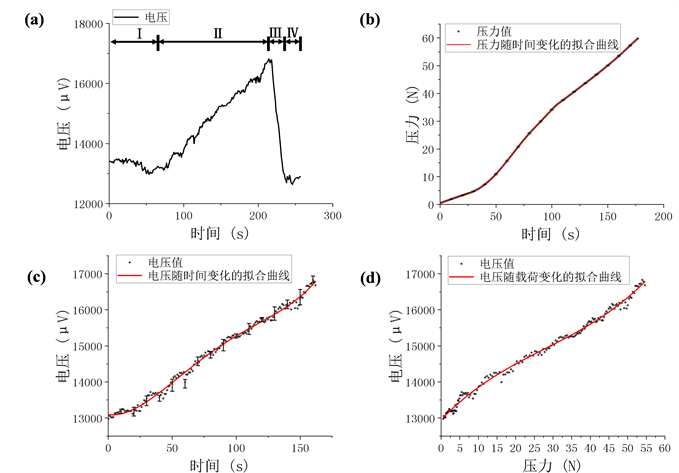
Figure 4. (a) Serial port reading pressure change curve with time I: No-load stage II: Loading stage III: Unloading stage IV: No-load stage; (b) Forward load change with time; (c) Voltage change with time under forward load; (d) Voltage change with load after inverse fitting
图4. (a) 串口读取压力值随时间的变化曲线I:空载阶段II:加载阶段III:卸载阶段IV空载阶段;(b) 正向载荷随时间的变化;(c) 受正向载荷时电压随时间的变化;(d) 反解拟合后电压随载荷的变化
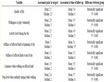
Table 1. Polynomial fitting table of each experimental parameter
表1. 各实验参数多项式拟合表
将函数关系式和实测值进行比较,函数关系式计算所得值的误差约为1.5%,因此使用公式(4)作为工程函数,其拟合后的函数图像如图4(d)所示。
将公式(4)输入单片机,在由LED显示模块输出计算完成的压力值,至此完成了对压力传感器的校准。根据图4(a)所示钉砧在受正向载荷及卸载过程中的电压值的变化,可知钉砧在受载及卸载过程中处于弹性形变区。选取两个处于平稳阶段的值(651, 12974.07692)和(3225, 12903.57143),计算得两者的误差为0.543%,误差极小,属于受电路噪声影响的正常范围。
4. 结论
本文为电动吻合器力反馈设计提供了一种新思路,借助有限元仿真,设计了吻合器前端的多参数检测钉砧的结构和检测电路,通过搭建实验平台,验证了设计的可行性并完成了传感器的矫正。
后续研究将对设计进行进一步优化,结合吻合器手柄开展离体实验,验证设计的有效性,并与传统吻合器进行对比实验。
基金项目
国家自然科学基金项目(51735003);2019年科技部数字诊疗装备研发计划(2019YFC0120402)。
参考文献
NOTES
*第一作者。
#通讯作者。