1. 引言
传统生产线故障诊断方法,主要依靠维修人员的经验、控制原理和设计图纸等,通过逐个排查可能的故障点来进行诊断,维修效率低,对维修人员的技能要求较高 [1] 。随着科技的发展,由于生产线上的设备集成度变高、设备之间的关系更加复杂、设计原理图存在保密需求等原因,依赖经验和设计图纸的传统诊断方法已经不适用于现代生产线,专家学者开始向人工智能和数据挖掘方向探索故障诊断新方法 [2] 。王彦昆等 [3] 将物联网与卷积神经网络结合,运用到轴承的故障诊断中,提高了诊断的抗干扰能力。王兴等 [4] 提出一种基于信号特征的多头注意力诊断方法,显著提高故障特征识别效率。李腾飞等 [5] 通过多元信息融合和卷积神经网络构建智能诊断模型进行故障分类,具有高精确性和有效性。然而,这些诊断方法主要针对某单一模块或设备,如何高效完成整条生产线这类复杂系统的故障诊断,是亟待解决的热点问题。
在复杂系统诊断领域,何彦等 [6] 结合故障树和灰色关联度理论进行船用发动机组的故障诊断与分析;安慧等 [7] 将模糊集理论引入故障树分析法中,解决了所求失效概率不精确问题;Cheng Xiaoyu等 [8] 将模糊故障树分析和置信规则库结合生成一种新的FFBRB模型,提高故障诊断的准确性。
也有学者将贝叶斯网络与故障树结合起来应用在故障诊断领域。陈洪转等 [9] 将故障树引入模糊贝叶斯网络,所建立的模型不仅能诊断故障,还能实现潜在风险识别。白旭等 [10] 结合故障树与贝叶斯网络,实现了不同故障状态下,薄弱环节的可靠度计算。
本文以动力锂电池模组生产线为研究对象,整合专家系统和人工智能技术,设计出基于故障树的动力锂电池模组生产线故障诊断专家系统,实现时间与空间的拓展,使得维修人员能快速完成故障排查任务,保障生产线的正常运行,降低生产线维护成本。
2. 故障树构建与分析
2.1. 故障树构建
故障树是进行复杂系统故障诊断的有效工具,该方法通过从上而下梳理系统故障产生的原因,用逻辑关系将这些原因联系起来,以此为基础建立故障树,这是故障诊断系统的基础和关键。
动力锂电池模组生产线由8个工位组成,包括自动上料工位、电芯配组工位、激光清洁工位、涂胶工位、电芯堆叠工位、电池盒组装工位、模组上盖拧紧工位和模组下线工位,工位之间相对独立,对于整条生产线的故障诊断而言,需要诊断每个工位的故障,再将结果汇总得出完整生产线的故障情况。下面以激光清洁工位为主要研究对象,论述该系统故障诊断的可行性。
基于激光清洁工位的结构原理,通过分析得出故障树,如图1所示,模型对应的事件表,如表1所示。
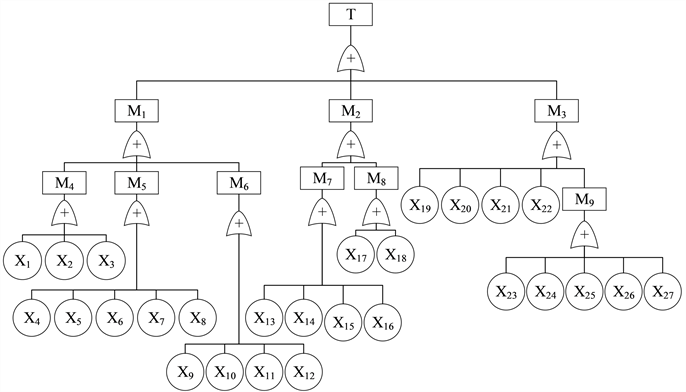
Figure 1. Fault tree of laser cleaning station
图1. 激光清洁工位故障树
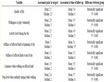
Table 1. Fault tree model event table of laser cleaning station
表1. 激光清洁工位故障树模型事件表
2.2. 故障树定性分析
最小割集是引起一个特定故障事件的最小集合,当这个集合中所有事件同时发生时,就会导致这个故障事件发生。采用布尔代数的逻辑计算方法来求取故障树的最小割集,如下面(1)式。
(1)
2.3. 故障树定量分析
根据故障树模型和贝叶斯网络模型的转化关系,利用Netica将故障树转化为贝叶斯网络模型如图2所示。其中单故障样本数与总故障样本数的比值为相对故障率 [11] ,即:
(2)
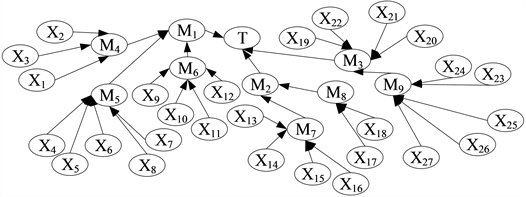
Figure 2. Bayesian network model diagram
图2. 贝叶斯网络模型图
将相对故障率作为贝叶斯网络模型的先验概率,输入模型中更新后,获得后验概率,为了方便比较分析,将先验概率和后验概率对比放置在表2中。
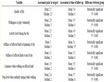
Table 2. Summary and comparison table of a priori probability and a posteriori probability of failure events
表2. 故障事件的先验概后验概率汇总对比表
3. 生产线故障诊断专家系统设计
3.1. 诊断系统的框架设计
基于故障树的锂电池模组生产线故障诊断专家系统,主要用于生产线发生故障时,快速定位故障点并分析原因,给出处理意见,其框架结构分为用户层、表现层、业务层和数据库。
为保证所开发的系统便于操作,本文采用网页模式、C#开发语言和MySQL数据库实现系统功能。专家系统诊断时通过模拟人类思考模式进行推理解决问题,属于人工智能的诊断方法 [12] ,主要包括知识库、推理机、交互界面和数据库等,其核心部分是知识库和推理机。
3.2. 故障诊断系统知识库构建
3.2.1. 知识获取及表示
根据上文故障树的建立和分析,对故障树进行知识提取,将其转化为可被计算机识别的表现形式,为系统的知识存储和推理奠定基础。在数据库中存放专家系统的知识规则,供推理机调用。因此,知识的表达水平决定了推理机效率。本文采用产生式规则法来表现系统中的知识,即根据上文建立的故障树事件之间的逻辑关系,以“IF-条件,THEN-结论事件”的形式表示故障知识 [13] 。以激光清洁工位的控制子系统搭建的故障树如图3所示。
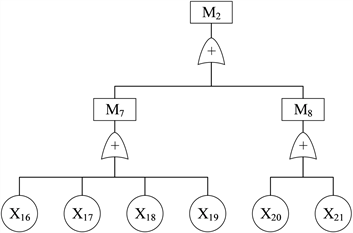
Figure 3. Fault tree of control subsystem
图3. 控制子系统故障树
故障树对应的事件表前文已经介绍,根据IF-THEN规则对控制子系统故障树进行规则提取,共获得8条规则,结果如表3所示。
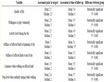
Table 3. Rule table of control subsystem fault event
表3. 控制子系统故障事件规则表
3.2.2. 知识存储
激光清洁工位故障树的结构较为复杂,存在某几种故障原因均可能导致同一故障出现的情况,因此本文利用数据表来表示诊断知识,采用故障分类表和故障原因表两个子表来搭建专家系统知识库,两表之间通过主键进行联系 [14] ,对应关系如图4所示。

Figure 4. Sub-table correspondence diagram
图4. 子表对应关系图
1) 故障分类表如表4所示。本表用于故障树中顶事件和中间事件的存放,其中子ID对应规则的下级事件,父ID对应规则中的上级事件,该表是故障诊断推理的基础。
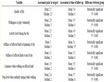
Table 4. Table of fault classification
表4. 故障分类表
2) 故障原因表如表5所示。本表用于记录生产线故障树的故障类别、故障原因、措施和故障发生次数,是生产线故障诊断系统中结论推断的基础。
3.3. 故障诊断系统推理机设计
3.3.1. 诊断系统推理方式
推理机包括正向推理、反向推理和混合推理三种推理方法,其中正向推理是指从现有故障征兆出发,逐级向下推理其对应规则的前提条件。本文采用正向推理,具体诊断思路为:以故障现象为分析起点,通过持续排查每个节点,找出故障原因。
3.3.2. 诊断系统冲突消解策略
当有多个原因导致同一结果产生时即为冲突,选出最可能导致结果原因的过程即为冲突消解。本文以概率高低作为冲突消解的准则,根据故障树事件概率分析,当遇到冲突时,以故障概率优先为准则,率先匹配故障概率高的知识,从而提高推理效率。
3.3.3. 推理机设计方案
基于3.3.1的推理方式和3.3.2的冲突消解策略,所设计的推理机推理过程如图5所示,其步骤为:
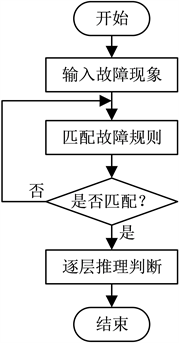
Figure 5. Reasoning flow chart of inference engine
图5. 推理机推理流程图
1) 进入诊断界面,输入故障现象,系统从数据知识库中匹配出某条规则;
2) 搜索该条规则的条件事件与数据库中的内容进行对比;
3) 若匹配成功,则根据现有的数据内容从上而下进行推理,得到诊断结果;
4) 若匹配不成功,则重新选择规则进行匹配,直至成功。
4. 生产线故障诊断专家系统设计与应用
4.1. 故障诊断专家系统功能设计
4.1.1. 主界面功能设计
基于HTML和CSS进行系统前端界面设计,实现用户登录、工位管理、故障诊断、知识维护和历史记录查询等功能。用户登录界面为不同分级用户设置权限,其中管理员具有最高权限,可对系统进行所有操作;工位管理界面可录入生产线全部工位信息。
4.1.2. 故障诊断界面功能设计
故障诊断作为故障诊断专家系统核心部分,首先在工位管理界面中选择需要被诊断的工位,其次在故障诊断界面输入故障现象,进行推理诊断,然后在人机交互界面显示可能的故障原因,检修人员根据提示进行故障排查,最后根据排查结果更新显示界面。
4.1.3. 知识维护界面功能设计
知识维护界面功能主要包括两个部分:一是向管理员展现现有的故障知识,能够实现对现有知识数据的添删改查;二是向管理员展现现有的故障类型,在添删改查故障类型时,实现逻辑关系的更新。
4.2. 故障诊断专家系统测试
下面以某智能制造公司锂电池生产线上激光清洁工位(如图6所示)故障为例,验证诊断发现工位故障原因是工业相机故障的准确性。
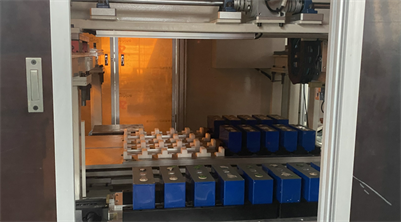
Figure 6. Laser cleaning station diagram
图6. 激光清洁工位图
假设激光清洁工位发生故障后不能正常清洁,且故障原因不明,检修人员通过故障诊断专家系统对激光清洁工位进行故障诊断与分析。
检修人员确定故障工位后,登录故障诊断系统,在工位管理界面选择激光清洁工位,在故障诊断界面输入故障现象,系统开始逐层推理。
第一次推理完成后,界面显示故障为继电器故障,检修人员排查后确认继电器故障不是导致激光清洁工位故障产生的原因,在“检测结果”栏选择“否”,系统更新故障状态;
第二次推理完成后,界面显示故障为工业控制计算机故障,检修人员排查后发现工业控制计算机故障并不是导致激光清洁工位故障产生的原因,在“检测结果”栏选择“否”,系统重新更新故障状态;
第三次推理完成后,界面显示故障为减速机故障,检修人员对减速机进行检测,未发现减速机存在异常问题,在“检测结果”栏选择“否”,系统再次更新故障状态;
第四次推理完成后,界面显示故障为工业相机故障,检修人员对工业相机进行检测,发现工业相机发生了故障,在“检测结果”栏选择“是”,故障诊断界面显示诊断结果和维修建议。至此,故障诊断结束,经维修后生产线恢复运行。
该测试通过四次诊断实现故障排除,验证本文所构建的锂电池模组生产线故障诊断专家系统可以实现人机交互、系统更新、故障诊断等功能,故障诊断结果准确。
5. 结论
本文通过将故障树与专家系统相结合,分析了锂电池模组生产线结构原理和故障特点,并建立了该产线故障树,构建了故障诊断专家系统,实现了生产线故障智能诊断目标,提高了故障检测效率,降低了生产线维修维护成本。同时,基于知识库的维护更新功能,扩大了系统的应用范围和应用场景。
本文验证了故障树和专家系统这两种故障诊断技术融合的可行性和准确性,解决了专家系统知识获取困难、推理机设计依据不充分等问题,为锂电池模组生产线故障诊断提供了一种有效的诊断方法,对复杂装备故障诊断具有重要参考价值。下一步研究可将数据驱动技术融入诊断系统,建立动态知识库,进一步提高诊断准确率。
基金项目
江苏省重点研发计划(BE2019317);常州市5G+工业互联网融合应用重点实验室(CM20223015);江苏理工学院研究生实践创新计划(XSJCX21_29)。
NOTES
*通讯作者。