1. 引言
钻孔内撑式破岩是一种重要的非爆破破岩技术,其将液压劈裂机或静态化学膨胀剂等放入岩石内部预先打设的钻孔中,利用岩石抗拉强度远低于抗压强度的特性,从内部开始破碎岩石。其中液压劈裂法的主要设备为劈裂机,由上部的液压油缸和下部的劈裂器组成,破岩时将劈裂器插入钻孔内通过油缸的轴向移动对孔壁施加横向内撑力劈裂岩石从而达到破岩的目的。该方法因操作简单、可控性强和无环境污染等优势在石料开采、二次破碎和隧道开挖等当中得到广泛应用,特别是在破碎体附近有密集人口、建筑物或设备等不可采用爆破方法的工程中 [1] 。
在非爆破破岩的工程中,有时需要精准控制破裂面的延伸方向,以便实现对破裂面的定向控制。相关学者 [2] - [7] 就不同因素对劈裂破岩效果的影响进行了一定的研究工作,其中预切槽对破岩有较好的定向控制作用,且在爆破方面已有不少研究成果。如徐颖等 [8] 通过切槽炮孔和普通炮孔光面爆破的对比实验证明了切槽炮孔的优越性;S. H. Cho等 [9] 得出切口导向孔比圆形导向孔裂纹生成更早且断裂面更平滑;李清等 [10] [11] 和杨仁树等 [12] [13] 应用动焦散线测试系统对普通孔、双孔和含缺陷介质孔在切槽爆破中爆生裂纹的扩展规律进行了研究;王汉军等 [14] 采用数值计算、动光弹研究和断裂力学分析方法揭示了定向断裂爆破中裂纹起裂和扩展的机理。
上述研究表明,预切槽在爆破方面对定向引导裂纹扩展具有积极作用,为本文研究提供了良好的基础。但在采用液压劈裂法进行的非爆破钻孔内撑式破岩方面,预切槽对破岩效果的影响及裂纹扩展机理等还有待进一步研究。基于上述问题,本文在室内定向破岩试验获得预切槽的确对破裂面的定向控制具有显著作用的直观试验现象后,采用MIDAS GTS NX有限元分析软件建立与室内试验相匹配的数值模型,通过对加载过程当中孔口边缘与切槽端部主应力、矢量图及拉破坏区等的综合分析,探究预切槽对岩石破裂面定向引导控制的深层次机理。
2. 定向破岩试验
2.1. 试验试件
试验采用边长为15 cm的正方体花岗岩试件,且在试件上下表面形心连线方向上钻有直径为2 cm的圆孔。试验中共制作两块试件,其中一块不切槽,另一块在上表面切槽,二者互为对照。在预切槽试件上表面的孔口两侧进行人工切槽,切槽方向与试件上表面边界平行,两侧切槽长度均为2 cm,深度为1 cm。试验试件如图1所示,其中平面ABCD为试件破坏后的期望破裂面。

(a) 不切槽 (b) 切槽
Figure 1. Test specimen schematic diagram
图1. 试验试件示意图
2.2. 试验设备及过程
定向破岩试验设备主要由待加载试件(图2)、SDS500电液伺服动静万能试验机(图3)和劈裂器(图4)组成。待加载试件为劈裂部分,电液伺服动静万能试验机为加载部分,劈裂器则为核心部件,由橡胶圈、中间楔块和两块分裂翼片构成。
进行试验时,将劈裂器插入试件的钻孔内并放置于万能试验机的承压底座上,且劈裂器放置角度应尽可能使产生的横向劈裂力与期望破裂方向垂直。万能试验机的承压底座固定,加载顶板以2 mm/min的速度下降,提供竖向位移。当加载顶板与劈裂器中间楔块顶部接触时,劈裂器受力并对试件钻孔内部施加横向劈裂力,直至试件被劈裂形成贯通破裂面,则结束试验。
2.3. 试验结果分析
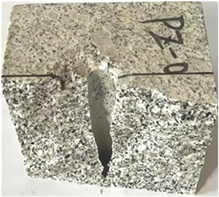
(a) 上表面裂缝 (b) 内部破裂面
Figure 5. Rock breaking effect of non-cutting specimen
图5. 不切槽试件的破岩效果
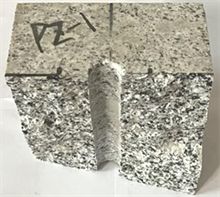
(a) 上表面裂缝 (b) 内部破裂面
Figure 6. Rock breaking effect of grooving specimens
图6. 切槽试件的破岩效果
试验完成后有无预切槽试件的破岩效果分别如图5和图6所示。由图5可以看出:未切槽试件上表面的孔周有小块岩屑脱落与细小次裂纹生成,钻孔左侧裂缝大致沿预期方向扩展,但右侧裂缝与预期方向相差近30˚,两侧裂缝不在一条直线上,裂缝整体弯曲程度很大。其实际形成的内部破裂面也偏离预期破裂面较远,越靠近试件底部破裂面偏离预期位置越远,钻孔底部仍有少量岩石未被劈裂,且破裂面平直性差。
由图6可以看出:切槽试件上表面的孔周岩石完整且无明显次生裂纹,上表面只有一条清晰的主裂缝。裂缝从孔口切槽处起裂,在预切槽长度范围内,裂缝与切槽几乎完全重合,在预切槽长度范围之外,裂缝也沿预切槽方向扩展,直至上表面贯通,且裂缝整体近似直线,弯曲程度较小。其实际形成的内部破裂面与预期破裂十分吻合,钻孔自上而下被完全劈裂,且破裂面平直性非常好。
3. 预切槽对破裂面引导机制的数值模拟
3.1. 数值模型
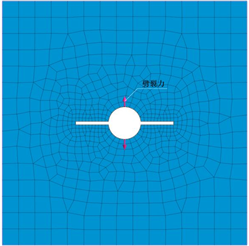
(a) 不切槽 (b) 切槽
Figure 7. Finite element calculation model diagram
图7. 有限元计算模型图
为了深入探究预切槽对裂缝与破裂面的定向引导机制,利用MIDAS GTS NX有限元分析软件建立两个平面应变模型。模型尺寸参照室内定向破岩试件,采用边长为15 cm × 15 cm的正方形且在其形心处有直径为2 cm的圆孔,其中切槽模型在孔口两侧有长度为2 cm,宽度为2 mm的长方形切槽。模型边界无约束,并在孔内竖直方向施加一对大小相等方向相反的劈裂力,加载过程中劈裂力逐级增大,单步增量为10 kN,直至在模型中部形成连通的拉破坏区。对模型的单元划分进行尺寸控制,在钻孔周围及切槽处进行加密细化。具体有限元计算模型如图7所示。
3.2. 模型参数
岩石材料选用广义霍克–布朗本构模型 [15] ,其为一种非线性强度近似准则,在连续性方程中不仅包含剪切强度,也包括了拉伸强度。为了确定该岩石材料的物理力学参数,根据《工程岩体试验方法标准GB/T50266-2013》的相关要求对同批花岗岩分别进行了单轴抗压强度实验和巴西劈裂实验,并结合霍克–布朗经验值范围来选取模型参数。具体物理力学参数取值如表1所示。
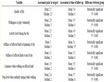
Table 1. The value of physical and mechanical parameters of the model
表1. 模型物理力学参数取值
3.3. 数值计算结果与分析
岩石破坏是岩石在受外部荷载作用后,其内部的应力状态满足岩石的破裂条件时的力学响应结果。对于钻孔内撑式破岩,由前述室内试验现象可知,岩样破裂具有典型的张拉型破坏特征。基于此,以下侧重对张拉型破岩起控制作用的最大主应力(拉应力)分布、主应力(拉应力)矢量与拉破坏区演化三个方面进行重点分析。
3.3.1. 最大主应力对比分析
通过数值模拟计算,得到在不同加载步下两种模型的最大主应力对比图,此处选取两个典型加载步予以分析。图8给出了第1加载步后的最大主应力,图9给出了第6加载步后的最大主应力。由图8可看出,两种模型的最大主应力分布特征有着很大差异。不切槽时,应力值较大的红色区域主要分布于圆形钻孔孔周,距离钻孔越远应力值越小;当有预切槽时,红色区域主要集中在两侧切槽的端部处,由端部向外逐渐减小,而钻孔孔周与切槽段的应力值却很小。从最大主应力数值上来看,两种模型的最小值均出现在劈裂力施加处,但最大值出现位置却不同,不切槽模型在孔壁两侧中间位置处达到最大值,而切槽模型则在两侧切槽端部处达到最大值,且应力数值较不切槽时更大。因此可以得出,预切槽的存在显著改变了原本孔口的应力分布状态,在预切槽端部处出现了明显的应力集中现象,端部的最大主应力数值最大且为拉应力。
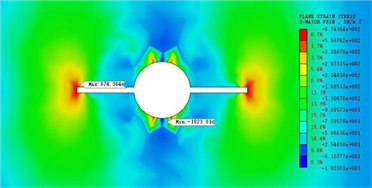
(a) 不切槽 (b) 切槽注:负值受压正值受拉。
Figure 8. Comparison of maximum principal stress after the first loading step
图8. 第1加载步后最大主应力对比图
由图9可知,随着劈裂力的不断增大,红色区域的应力值与范围也逐渐变大。不切槽时,应力值较大的红色区域主要从孔壁两侧横向向外扩展;当有预切槽时,则是在两侧切槽端部处产生范围更大更强的应力集中效应。根据最大拉应力理论(第一强度理论),应力集中后的最大主应力为拉应力且该拉应力超过岩石的抗拉强度时,岩石就会沿最大拉应力的作用面发生破坏,故可认为,在预切槽端部处最先产生张拉裂缝,这也就解释了为什么室内试验中切槽试件上表面的裂缝优先从孔口切槽处起裂。张拉裂缝形成后,裂缝的尖端也会出现与上述预切槽端部相同的应力集中特征,从而产生更长的张拉裂缝,使得裂缝进一步扩展。
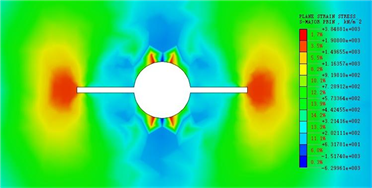
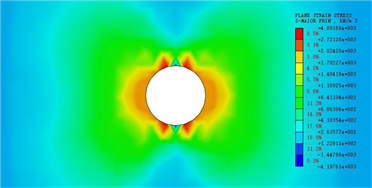
(a) 不切槽(b) 切槽
注:负值受压正值受拉。
Figuer 9. The maximum principal stress comparison diagram after the sixth loading step
图9. 第6加载步后最大主应力对比图
为了更具体地反映有无预切槽对最大主应力的影响,提取两种模型应力集中显著区域(不切槽模型为孔壁两侧中间位置,而切槽模型为两侧切槽端部处)不同加载步下的最大应力数据,绘制变化折线如图10所示。由折线图可知:随着加载步数的递增,二者的共同特征是最大主应力数值均不断增大并最终趋于稳定。二者不同点表现在,应力增长过程中切槽端部处的最大主应力数值增长迅速,曲线较陡;而不切槽时,孔壁两侧中间位置处的应力数值则增长较缓慢,需要多个加载步才能趋于最大值,且不同加载步下切槽端部处的应力数值均远大于不切槽孔壁两侧的中间位置。这些变化特征进一步说明了预切槽的设置不仅使切槽端部处最大主应力值数值显著增大,出现明显的应力集中效应,且加载过程中应力值增长速度也更快,更易达到岩石开裂条件而产生裂缝。
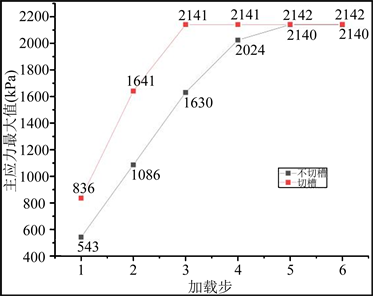
Figure 10. The comparison diagram of the change trend of the maximum principal stress under different loading steps
图10. 不同加载步下主应力最大值变化趋势对比图
从应力分布的角度来讲,预切槽的设置对定向破岩能产生积极影响的原因为:预切槽的存在改变了孔口的应力分布特征,强化了切槽端部处的应力集中程度,同样也使加载过程中切槽端部处应力值增长速度加快,使其端部最先产生张拉裂缝,裂缝长度增加尖端变窄,又将进一步加剧应力集中的程度。
3.3.2. 最大主应力矢量对比分析
为了探究裂缝沿预切槽方向扩展的原因,对两种模型的最大主应力矢量进行对比分析,图11给出了第1加载步后的最大主应力矢量,图12给出了第6加载步后的最大主应力矢量。其线段长度表示主应力的大小,箭头的方向表示主应力的方向。
从图11可以看出,两种模型的最大主应力矢量图差异明显。从矢量长度上来看,不切槽时,线段长度较大的矢量主要分布在钻孔孔周;当有预切槽时,线段长度较大的矢量则分布在切槽端部,说明切槽端部处的主应力较大,这也与上节分析的切槽端部处应力集中相一致。从矢量方向上来看,不切槽时,钻孔周围长度较大的矢量均与钻孔相切;当有预切槽时,切槽端部处的最大主应力矢量与预切槽方向相垂直,即该处最大拉应力方向与切槽方向垂直。
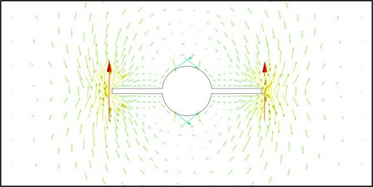
(a) 不切槽 (b) 切槽
Figure 11. The maximum principal stress vector comparison diagram after the first loading step
图11. 第1加载步后最大主应力矢量对比图
从图12可以看出,随着加载步数的增加,应力矢量发生了一定的改变。不切槽时,孔周长度较大的矢量数量有所增加,分布范围也相应有所扩大,矢量方向基本仍与钻孔孔壁相切;当有预切槽时,切槽端部处长度较大的矢量数量也有所增加,并沿预切槽方向向外平行分布,且矢量方向均与预切槽方向垂直。由岩石的破裂理论可知,当岩石在拉应力的作用下发生张拉型破坏时,岩石内部产生的张拉型破裂面与拉应力相垂直,故这也就解释了室内试验中有预切槽试件的裂缝延伸方向为什么与预切槽方向基本一致。
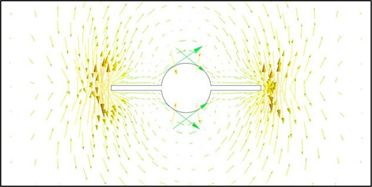
(a) 不切槽 (b) 切槽
Figure 12. The maximum principal stress vector comparison diagram after the sixth loading step
图12. 第6加载步后最大主应力矢量对比图
从主应力矢量的角度来讲,预切槽的设置对定向破岩能产生积极影响的原因为:预切槽的存在使得加载过程中切槽端部处的最大拉应力始终与预切槽方向垂直,故其所产生地张拉裂缝与预切槽方向相一致,并一直沿预切槽方向扩展,从而有效实现了对裂缝扩展方向的定向引导。
3.3.3. 拉破坏区对比分析
由室内试验可知,钻孔内撑式破岩属典型的受拉破坏,图13给出了数值模拟中不同加载步时的拉破坏区分布情况。从图13可以看出,不同加载步下两种模型的拉破坏区分布存在明显差异。一方面,从拉破坏区最先产生位置来看,不切槽时,受竖向劈裂力影响拉破坏区最先出现在钻孔左侧,但数量较少;当有预切槽时,拉破坏区最先出现在两侧切槽的端部处,且数量较多。由于拉破坏区最先出现的位置不同,从而使得二者起裂位置不同,有预切槽的试件优先在切槽端部处起裂。
另一方面,从拉破坏区扩展来看,不切槽时,拉破坏区扩展方向具有随机性,在孔周多方向均出现拉破坏区,分布较散乱,且拉破坏区扩展不连续,形态较弯曲。这表明裂缝具有多个可能扩展的方向,实际拉裂缝不一定沿预期方向扩展,且裂缝弯曲程度较大,这同样也解释了试验中不切槽试件孔周有细小次生裂纹产生的原因;当有预切槽时,拉破坏区扩展具有明显的规律性,分布非常集中,均分布于两侧切槽的端部,其延伸扩展方向也均沿着预切槽方向,整体近似呈直线,且拉破坏区扩展连续。这表明预切槽的存在使拉破坏区的范围更集中,连续性更好,从而使得实际主裂缝清晰,并沿预切槽方向直线扩展。
从拉破坏区产生与扩展的角度来讲,预切槽的设置对定向破岩能产生积极影响的原因为:预切槽的存在使拉破坏区最先在切槽端部处产生,分布范围更小更集中,且扩展方向与预切槽方向完全一致,扩展也更为连续。
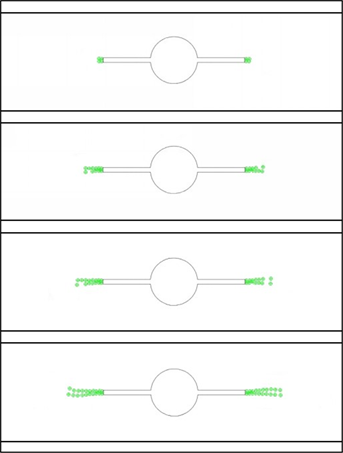
(a) 不切槽 (b) 切槽
Figure 13. Comparison diagram of tensile failure zone under different loading steps
图13. 不同加载步下的拉破坏区对比图
4. 结论
本文对花岗岩试件进行了室内定向破岩试验,观察了预切槽设置与否对定向破岩的影响,并通过数值模拟计算,对有无预切槽情况下的最大主应力分布、矢量图和拉破坏区进行了对比分析,获得下述关于预切槽对破裂面定向引导机制的认识:
(1) 预切槽的设置能有效控制裂缝起裂位置、抑制次生裂纹生成,并引导裂缝向着切槽方向扩展,使岩石在预期破裂面处产生裂缝,从而实现对岩石破裂面的定向控制。
(2) 预切槽的存在显著改变了孔口的应力分布状态,在预切槽端部出现了明显的应力集中现象,加载过程中应力值增长速度也加快。张拉裂缝形成后,裂缝尖端也将出现与预切槽端部类似的应力集中特征,进一步促使裂缝扩展。
(3) 劈裂加载过程中切槽端部处的最大拉应力方向始终与预切槽方向相垂直,从而使得产生的张拉裂缝方向与预切槽方向相一致,并始终沿切槽方向扩展。
(4) 预切槽的存在同样使得拉破坏区在切槽端部更为集中且扩展更为连续,其扩展方向与预切槽方向相一致,更有利于实现对破裂面的定向引导。
参考文献
NOTES
*通讯作者。