1. 引言
随着科学技术的不断进步,对塑料制品质量的要求也越来越高。汽车内饰的设计工作量占汽车总设计量的一半以上,因此其为汽车车身的重要组成部分之一。伴随着汽车行业的迅猛发展以及私人用车市场的崛起,人们对汽车内饰的需求逐步提高。信息技术的发展促进了计算机辅助工程CAE在模具设计领域的广泛应用,并且Moldflow作为注塑成型最佳的CAE软件,为塑件的设计提供了强有力的保障 [1] 。注塑成型工艺也同样具有一定的缺陷,比如翘曲、缩坑、流痕、熔接痕、气孔、放射纹、龟裂、变色、飞边等质量缺陷,需要提供一套行之有效的解决方案。但是采用CAE技术,可以提前给出预防这些缺陷产生的模具设计方案,降低生产成本,缩短生产周期,提高生产效率,保证塑件的质量 [2] 。本实验以汽车导航仪外框固定架为研究对象,运用正交试验法和Moldflow模流分析软件设计探究影响翘曲变形的工艺参数对注塑件的影响程度,得到的最优工艺组合,使得注塑件的翘曲变形量最小。
2. Moldflow模流分析
2.1. 网格划分
将汽车导航仪外框固定架作为研究对象,首先使用UG软件绘制出产品模型图,如图1所示,然后将模型导出为光固化立体造型术文件格式,之后导入到Moldflow软件中。
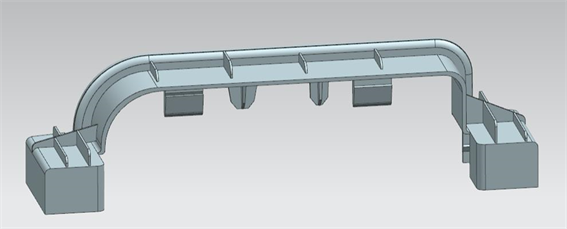
Figure 1. The model of the outer frame of the car navigator
图1. 汽车导航仪外框固定架模型
对汽车导航仪外框固定架三维模型进行网格划分,为了之后分析结果的精确性,根据零件尺寸大小,定义全局网格边长为3 mm,网格统计如图2所示。根据图2可以得出,最大纵横比是19.0,最小纵横比是1.16,对于本产品双层面,其中没有自由边、多重边、没有定向的单元,没有单元交叉,且连通区域为1;纵横比在20以内,单元匹配率达到95.2%,满足对模型进行翘曲变形模拟分析的条件 [3] 。
2.2. 浇注系统设计
首先确定最佳浇口位置,如图3所示,最佳浇口位置在节点N23755处,上图中蓝色为最佳浇口位置,红色为最差位置,绿色介于两者之间,因此该汽车内饰件的最佳浇口位置应选择正中位置。
由于塑件的尺寸较小,且需要大批量生产,为了节省成本和提高生产效率,确定产品为一模两腔。本次设计采用侧浇口,采用单浇口和双浇口两个方案进行对比,浇口尺寸为4 cm,冷流道尺寸为5 cm,冷主流道始端直径为3 cm,冷主流道末尾尺寸为5 cm。在结果中选择充填时间、气穴、熔接痕进行比较,分析结果分别如图4~9所示。
虽然双浇口的充填时间比单浇口短,但采用单浇口的气穴数目和熔接痕更少,经过综合比较,采用单浇口的浇注系统。
2.3. 冷却系统设计
有效的冷却系统在注塑生产过程中起到了重要的作用,降低冷却时间,提高生产效率,降低残余应力,提升产品质量 [4] [5] 。本次设计两个方案进行对比,一个为普通冷却管道,一个为阶梯冷却管道,对比结果如下表1。
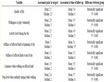
Table 1. Part temperatures for different pipe types
表1. 不同管道类型下的零件温度
通过比较零件的温度,得出阶梯管道的冷却效果更好,因此采用阶梯管道进行冷却系统的设计,如图10所示。
3. 工艺参数优化正交试验设计
正交试验设计的分析过程包括五个基本步骤,确定试验因素的数量和每个因素的水平,设计适当的正交表,列出试验方案和试验结果,对正交试验设计的结果进行范围分析和回归分析,确定最佳或更好的因素组合 [6] 。利用正交实验设计法对大量组合进行简化,大大减少试验次数,提高测试效率,以此得出最优的注塑工艺条件 [7] 。
首先应该明确实验指标,通过对塑件形状,及材料的分析,翘曲是对塑件影响较大的指标。所以实验指标为翘曲。通过成型窗口分析的结果来确定因素的水平。成型窗口分析结果如下图11所示。
根据成型窗口的分析结果确定出各因素及水平,如下表2。
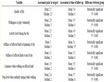
Table 2. Orthogonal test factors and levels
表2. 正交试验因素及水平
以翘曲量作为正交试验的评判指标,确定了因素和水平后,根据表2的数据,列出正交试验表3。
4. 结果分析
4.1. 设置极差分析表
对实验结果进行统计分析,分析方法一般包括两种,极差分析法和方差分析法,本实验采用极差分析法。极差是各参数在不同的水平下实验结果均值的最大值和最小值的差值。极差分析可以帮助我们清楚地看出各因素对实验目标(翘曲量)的影响程度,列出极差分析表,如下表4所示。
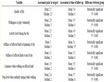
Table 4. Range analysis of factor levels
表4. 因素各水平的极差分析
注意:Li表示第i个因子水平下的均值,R为因子水平的极差。Ri越大,表示所对应的工艺参数对翘曲变形量的影响越大 [8] 。根据极差大小排序,可以得出各参数对翘曲的影响大小为保压时间 > 注塑时间 > 保压压力 > 熔胶温度 > 模具温度 > 注射压力。
4.2. 均值折线图
根据极差计算结果,将试验因素水平作为横坐标,以翘曲变形量作为纵坐标,运用origin软件绘制折线图,如图12所示。
通过该折线图所示,我们可以发现当翘曲量取最小值时各因子的最佳优化组合为A5B1C1D2E2F2。将其代入Moldflow软件中,即当模具温度为70℃、保压压力为50 MPa、保压时间为3 s、注塑时间为2.5 s、注射压力为75 MPa、熔融温度为245℃时,可以得到最小的翘曲变形量为1.814 mm,与未进行优化前的翘曲变形量2.303 mm相比,有了很好的改进,如图13和图14所示。
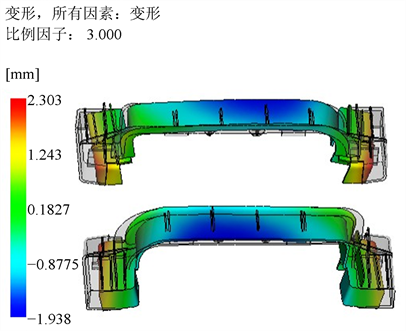
Figure 13. Warpage deformation before optimization
图13. 未优化前的翘曲变形量
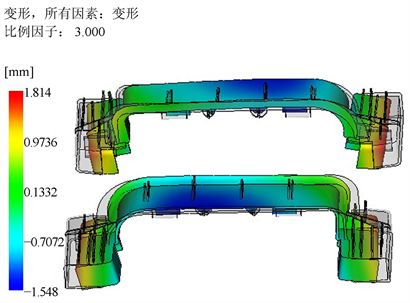
Figure 14. A5 B1 C1 D2 E2 F2 combined optimized warpage deformation
图14. A5 B1 C1 D2 E2 F2组合优化后的翘曲变形量
5. 结束语
本文以汽车导航仪外框固定架为研究对象,过正交试验法和Moldflow模流分析软件,找到了模具设计和工艺参数组合的最佳方案,改善了产品质量、缩短了生产周期并且降低了生产成本,对提高生产效率起到了巨大的作用。
该塑件采用单浇口的浇注系统,采用一模两腔的结构,使用阶梯管道进行冷却系统的设计。通过正交试验和极差分析可得出各主要工艺参数对翘曲变形量的影响程度大小为保压时间 > 注塑时间 > 保压压力 > 熔胶温度 > 模具温度 > 注射压力。最优的工艺参数组合为A5B1C1D2E2F2,即当模具温度为70℃、保压压力为50 MPa、保压时间为3 s、注塑时间为2.5 s、注射压力为75 MPa、熔融温度为245℃时,此时塑件的翘曲变形量最小为1.814 mm,与未优化前相比,降低了21.2%的翘曲变形量。