1. 引言
弱刚度工件广泛应用于航天、造船、汽车和模具等领域中,但由于其刚度低、形状不规则、难以加工等一直是研究难点。为此,许多学者对弱刚度工件的加工过程进行精细优化,使工件的刚度增大、振动减小,提高加工精度,其中大多是对机床控制系统进行的改造。汪征宇 [1] 改造了机械臂加工控制系统,完成了对薄壁工件的加工,但其加工效率低、灵活性差,成本也较高。张宝荣等 [2] 研究变壁厚弱刚度零件加工变形,通过对切削刀具的设计及其参数优化得到最佳加工参数,最终解决了变壁厚弱刚度工件加工中的问题。此外在提高弱刚度工件刚度的问题上,张智森和戴延丰 [3] 利用有限元仿真软件对工件变形机制进行分析,设计了相应的夹具装置,该夹具安装方便、操作简单,明显提高了弱刚度零件的加工精度。杨中宝等 [4] 设计的薄壁件内撑自平衡柔性夹具,在一定范围内可适用于不同内径、不同长度的产品,并具有可自动平衡两端内撑力的功能。毋健雄 [5] 利用磁流变励磁固化特性对薄壁件加工进行振动抑制,设计了基于磁流变液的柔性夹具,该夹具对铣削过程中产生的振动明显具有抑制作用。张永亮等 [6] 设计了一种用于加工复杂薄壁零件的辅助支撑装置,并进行了力学性能测试。马佳伟等人 [7] 设计了半自动磁流变弹性体减振器,经实验表明,该减震器利用合适的控制方法,在不同的激励形式下起到很好的减振作用。李清云 [8] 利用MRE设计了舰船推进轴系纵振吸振器,经实验表明MRE不仅拥有良好的剪切特性,而且具备橡胶的特性优点,克服了磁流变液(MRF)易沉降、易活跃等缺点;FU Jie等 [9] 对基于磁流变的柔性夹具进行了结构仿真及各性能测试,研究了线圈匝数、电流对磁场强度的影响,并对固化后的MRF在挤压前后所产生的剪切应力进行了分析。
对于弱刚度工件的加工,本文通过在弱刚度区域增加磁流变弹性体辅助支撑的方式增加系统的刚度并抑制工件的加工变形,要增加系统的刚度,装置的磁场强度是研究关键 [10] 。为了得到足够的磁感应强度,需要合理的结构设计及选择合适的材料,来使工件与辅助支撑部件之间产生足够的支撑力。本文将利用Comsol软件对MRE柔性辅助支撑装置内的磁场分布进行仿真分析及试验测试,为确定该装置的最佳结构参数奠定基础。
2. MRE辅助支撑装置设计及工作原理
本文设计的弱刚度工件加工辅助支撑装置利用了特殊的智能材料–磁流变弹性体,将磁流变弹性体均匀分为四块放置于工件内壁并与楔形块相接触,用以固定支撑套筒。另外,楔形块、楔形柱、螺母、螺柱用于胀紧弹性体,使其贴于工件表面。磁场的大小可通过更换不同类型的电池进行调节。线圈中有电流时,产生的磁场使外部的MRE刚度增大从而为弱刚度工件提供支撑力,抑制工件振动幅值,提高工件加工质量。
图1为磁流变弹性体辅助支撑装配结构图。
1-工件;2-芯轴;3-线圈;4-楔形块;5-楔形柱;6-螺柱;7-螺母;8-磁流变弹性体;9-电池;10-绝缘垫片。
Figure 1. Structure diagram of MR elastomer auxiliary support assembly
图1. 磁流变弹性体辅助支撑装配结构图
3. 不同参数下磁流变辅助支撑装置的磁场分析
3.1. 建立仿真模型
本文通过Pro/Engineer软件对磁流变弹性体辅助支撑进行三维建模,将其导入Comsol中进行磁场仿真。下面是网格划分情况:网格类型采用自由四面体,其中网格大小最大单元尺寸为31.8 mm,最小单元尺寸为5.72 mm,最大单元增长率为1.5,曲率因子0.6,狭窄区域分辨率为0.5,求解自由度数17,108,如图2所示。
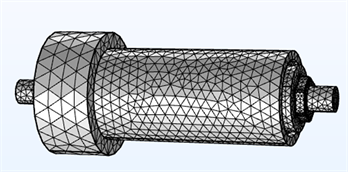
Figure 2. Meshing model of magnetorheological elastomer auxiliary support device
图2. 磁流变弹性体辅助支撑装置的网格划分模型
为了得到足够的磁感应强度,需要设计合理的结构并选择合适的材料使工件与辅助支撑部件之间产生足够的支撑力。为此,本文对不同参数下装置内的磁感应强度进行了三维仿真分析,并分析了各参数对磁感应强度的影响规律。
3.2. 不同参数下对磁感应强度的仿真与分析
3.2.1. 芯轴磁导率的影响
芯轴是磁流变弹性体辅助支撑装置的关键零件之一,它对线圈产生磁场起着重要的作用。本文就不同芯轴材料对磁流变弹性体辅助支撑工作间隙处的磁感应强度的影响进行磁场仿真,不同芯轴材料的磁导率如表1所示。
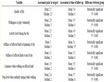
Table 1. The permeability of different mandrel materials
表1. 不同芯轴材料的磁导率
不同磁导率的芯轴,工作间隙处的磁感应强度曲线如图3所示。
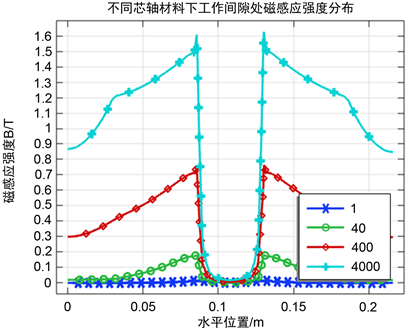
Figure 3. Magnetic induction intensity distribution curve at working gap of different mandrel materials
图3. 不同芯轴材料工作间隙处磁感应强度分布曲线
由图3可知,磁导率为4000时芯轴与工件之间工作间隙处的磁感应强度约是磁导率为400时的2.19倍,是磁导率为40时的7.94倍,是磁导率为1时的97.33倍。从总体来看,磁流变弹性体辅助支撑装置工作间隙处的磁感应强度随芯轴磁导率的增大而增大,所以芯轴材料的选择对工作间隙处的磁感应强度的影响具有关键作用。因此,本文选择磁导率最大的电工纯铁作为芯轴材料。
3.2.2. 工件磁导率的影响
本文对磁流变弹性体辅助支撑装置在不同磁导率工件情况下进行磁场仿真,并对磁流变弹性体工作间隙处的磁感应强度进行分析,不同工件材料的磁导率如表2所示。
不同磁导率工件,工作间隙处的磁感应强度分布情况如图4所示。
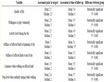
Table 2. Permeability of different workpiece materials
表2. 不同工件材料磁导率
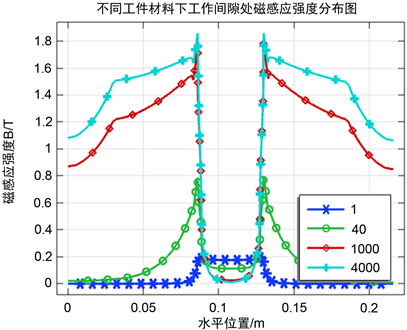
Figure 4. Magnetic induction intensity distribution at different workpieces’ working gaps
图4. 不同工件工作间隙处磁感应强度分布情况
由图4可知,工件为电工纯铁时,磁流变弹性体辅助支撑装置工作间隙处的最大磁感应强度是工件为铝时的2.01倍,是工件为铁镍钼合金的2.13倍,是工件为45#钢的1.18倍。以上分析表明,磁流变弹性体工作间隙处的磁感应强度主要随工件磁导率的增大而增大,当达到一定的磁导率时,磁感应强度将处于饱和状态。由于45#钢容易获得、成本较低,并根据磁感应强度分布值可得,选用磁导率为1000的45#钢作为工件材料比较合适。
3.2.3. 工件厚度的影响
在加工不同厚度的工件时,其工作间隙处的磁感应强度也会不同。本文对不同工件厚度的情况下磁流变弹性体辅助支撑装置进行磁场仿真,并绘制其工作间隙处的磁感应强度曲线图。不同的工件厚度如表3所示。
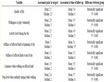
Table 3. Different workpiece thickness values
表3. 不同工件厚度值
不同工件厚度,工作间隙处的磁感应强度分布情况如图5所示。
由图5可知,在其它条件不变的情况下,工件厚度为8毫米时在芯轴及胀紧零件处工作间隙的磁感应强度是工件厚度为4毫米时的1.33倍,是工件厚度为2毫米时的2.30倍,是工件厚度为0.5时的18.40倍。总体上来说,工件厚度越大磁感应强度越大,工件厚度太小将会影响工作间隙处的磁感应强度。因此本文选择的工件厚度应大于2毫米。
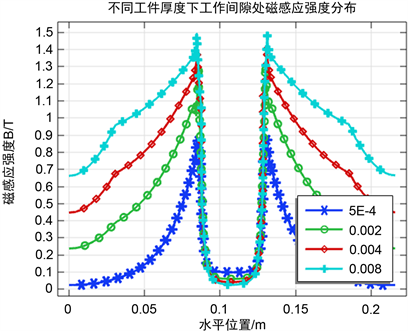
Figure 5. Magnetic induction intensity distribution at working gaps with different workpiece thicknesses
图5. 不同工件厚度下工作间隙处磁感应强度分布情况
3.2.4. 工作间隙大小的影响
工作间隙的大小对工作间隙处磁感应强度的大小也有着一定影响,本文在不同大小的工作间隙下对磁流变弹性体辅助支撑装置进行磁场仿真。不同工作间隙大小值如表4所示。
不同工作间隙大小,工作间隙处的磁感应强度分布情况如图6所示。
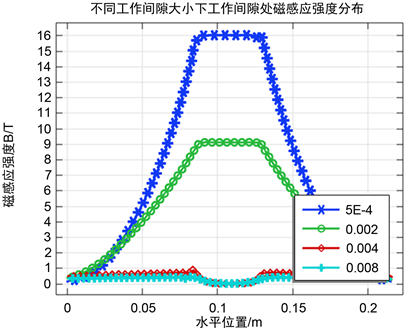
Figure 6. Magnetic induction intensity distribution at working gap under different working gap sizes
图6. 不同工作间隙大小下工作间隙处磁感应强度分布情况
由图6可知,在其它条件不变的情况下,工作间隙为0.5毫米时工作间隙处的磁感应强度是工作间隙为2毫米时的1.77倍,是工作间隙为4毫米和8毫米时的32倍。
经上述仿真结果及分析表明:工作间隙越大时工作间隙处的磁感应强度越小,当大于3毫米时工作间隙处的磁感应强度基本一致,都很小;当小于3毫米时,工作间隙越小工作间隙处的磁感应强度变大越明显;当小于3毫米时,工作间隙处的磁感应强度值最大部分位于线圈外围处,向两端处的磁感应强度逐渐降低。虽然工作间隙越小工作间隙处的磁感应强度越大,但由于磁流变弹性体位于工作间隙处,太薄的磁流变弹性体制备比较困难,因此本文选择制备2毫米左右的磁流变弹性体,工作间隙大小选择2毫米。
3.2.5. 电流大小的影响
本文设计的磁源方式是在磁导率较大的芯轴上缠绕线圈,使其产生较大的磁场来满足实验要求,线圈中的电流大小是影响磁场强度大小的重要因素之一。因此需要对不同电流大小下的磁流变弹性体辅助支撑装置进行磁场仿真,研究工作间隙处的磁场分布情况。不同的电流值如表5所示。
不同大小的电流,工作间隙处的磁感应强度分布情况如图7所示。
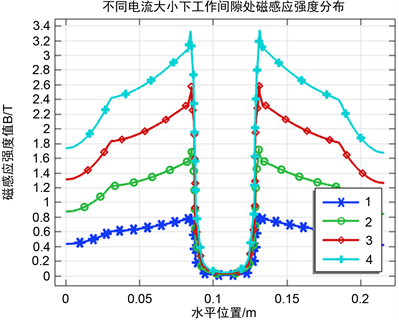
Figure 7. Magnetic induction intensity distribution at working gap under different current sizes
图7. 不同电流大小下工作间隙处磁感应强度分布情况
由图7可知,线圈中电流大小为4 A时的磁感应强度是电流为3 A时的1.33倍,是电流为2 A时的1.98倍,是电流为1 A时的4.00倍。上述仿真结果及分析表明,工作间隙处的磁感应强度随电流增大而增大,此外电流的选择还应综合考虑能耗等客观条件,以达到最佳技术效果。
4. 参数优化后装置的磁场仿真
根据各参数仿真结果,通过对比后选出最合适的参数作为最终确定参数,如表6所示。通过仿真软件设置相应的参数进行磁场仿真,得到磁流变弹性体辅助支撑装置工作间隙处截面磁感应强度分布云图,如图8所示,并绘制该轴向截面工作间隙处的磁感应强度分布曲线图,如图9所示。由图9可知,芯轴及胀紧零件外围的工作间隙处的磁感应强度最小可达0.83 T,最大可达1.62 T,满足车削弱刚度套筒工件提供辅助支撑要求。
(a) 轴向截面磁感应强度分布云图
(b) 径向截面磁感应强度分布云图
Figure 8. Cloud map of magnetic induction distribution
图8. 磁感应强度分布云图
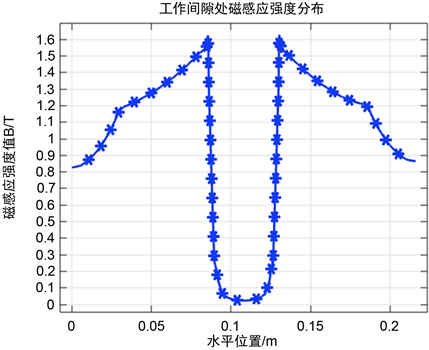
Figure 9. Distribution curve of magnetic induction intensity at working gap
图9. 工作间隙处磁感应强度分布曲线图
5. 磁感应强度试验验证
对通电后的磁流变弹性体辅助支撑装置中的磁感应强度进行测量。采用型号为HT201的数字特斯拉计,磁流变弹性体是由704RTV硅橡胶、羰基铁粉和二甲基硅油制备得到的。测试现场如图10所示。给励磁线圈加电流2 A后,沿工件内表面从上至下等距测得间隙处磁感应强度的实验数据,记录并绘出磁场强度分布图。
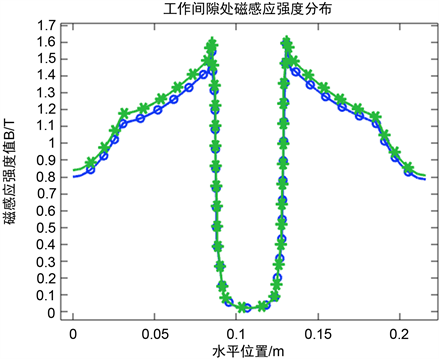
Figure 11. Experimental and simulation magnetic induction intensity distribution curve
图11. 实验与仿真磁感应强度分布曲线图
用之前优化后的参数进行磁感应强度测试实验,将实验测试的磁感应强度与参数优化后的仿真结果对比,绘制磁感应强度分布曲线图,如图11所示。其中绿色星号曲线为参数优化后的仿真曲线,蓝色圆号曲线为实验测得的磁感应强度曲线。通过磁感应强度测量实验可知,实验与理论数值误差范围在1%~10%,误差合理,实验验证了有限元仿真结果的正确性。
6. 电流与磁感应强度的拟合关系
由上面的磁场仿真及磁感应强度实验可得,在不同电流大小下的磁感应强度不同,根据磁场仿真来计算出在不同电流作用下的平均磁感应强度,并用matlab绘制出拟合出曲线图。
其中得到:
因此取
,
,
,
最终可得拟合函数为
。其x与y的关系图如图12所示。为了评估拟合程度,本文运用了计算拟合的均方根误差(RMSE)来评估。当函数为一次时,其均方根误差(RMSE)等于0.033263816399828,当函数为二次时,其方根误差(RMSE)等于0.033250257225766,当函数为三次时,其方根误差(RMSE)等于0.031690517839814,因此选择三次函数匹配电流与磁感应强度之间的关系较为合适。
若把x换成电流I,y换成磁感应强度B则可得到电流与磁感应强度的关系式为:
(1)
把公式(1)带到磁流变弹性体的特性公式中可得到电流与弹性模量的关系及电流与磁流变弹性体的耗损因子之间的关系式,再带入到公式磁流变弹性体的等效刚度和等效阻尼公式 [11] 中可得到刚度和阻尼分别与电流之间的关系式。
7. 结论
本文设计了基于磁流变弹性体的辅助支撑装置,并研究装置磁路中部分零件材料、间隙、厚度等不同参数对磁流变弹性体柔性辅助支撑的工作间隙处磁感应强度的影响规律,得到了在芯轴材料为电工纯铁、工件材料为45#钢、工件厚度为8 mm、工作间隙为2 mm的情况下通2 A电流时工作间隙处的磁感应强度最小可达0.83 T,最大可达1.62 T,满足车削弱刚度套筒工件提供辅助支撑要求。通过实验得到,误差范围为1%~10%,误差合理,实验验证了有限元仿真结果的正确性。最后利用MATLAB对电流与磁感应强度之间的数据关系进行拟合,得到关系式:
,为进一步研究磁流变弹性体辅助支撑车削建模奠定了理论基础。
NOTES
*第一作者。