1. 引言
车身耐撞性能的好坏严重影响到车内乘员的生命安全,目前对车身耐撞性能的研究一般集中在车身零部件的材料和结构上。在材料方面:Javad等人 [1] 研究发现改进后的钢铝/玻纤复合材料保险杠横梁能够减小扰度,缓冲冲击力和应力,同时实现了保险杠横梁的轻量化。毕思蕊 [2] 研究发现20%含量的长玻璃纤维增强聚丙烯复合材料注塑成型的保险杠相较于传统金属保险杠,吸收的能量会更多,强度也更高,同时,质量也更轻。在满足耐撞性的前提下进一步实现了轻量化。段书用 [3] 发现长玻璃纤维复合材料作制成的防撞梁耐撞性能优于铝合金防撞梁的同时质量还减轻了11%。Kim等人 [4] 设计了玻璃/碳复合材料混合的保险杠横梁,相比于常规保险杠横梁的重量轻了33%,并且抗冲击性能得到提升。
结构方面:一般通过改变保险杠横梁、吸能盒、纵梁等车身零部件的结构来提高前车身的耐撞性。程秀生等人 [5] 将某款轿车的保险杠横梁的矩形截面重新设计成“凹”型截面,此结构相比于原结构吸能特性有显著提高,且满足了轻量化的要求。刘利等人 [6] 开发出蜂窝状的保险杠横梁,在轻量化的基础上提高了保险杠横梁的耐撞性。宋家峰 [7] 根据竹子生长方向的厚度梯度和节间距离,设计了一种变厚度的保险杠横梁,此仿生结构的耐撞性能大大提高。王婷婷等人 [8] 通过研究多腔形结构吸能盒发现“田”字形的碰撞效能最好,且质量更加轻。徐平等人 [9] 将泡沫铝填充结构后保险杠进行碰撞仿真分析,较传统后保险杠,其变形量和峰值加速度都有所降低,且增大了最大吸收能量。
本文研究玻纤含量、玻纤取向、温度、应变率4种因素对PA6/SGF复合材料的影响。利用拉伸实验及插值法获得的PA6/SGF复合材料参数,建立B柱上接头CBS结构模型,并开展落锤试验进行验证。通过拓扑优化及精益化结构设计,在不提高质量的前提下大幅提高耐撞性能的目标。
2. PA6/SGF复合材料力学性能试验
2.1. 试样的制备
拉伸实验是材料力学性能实验中最普遍的方法之一 [10] ,实验前需要制备拉伸试样。不同玻纤取向的拉伸试样形状及尺寸参考GB/T 3354-2014《定向纤维增强聚合物基复合材料拉伸性能实验方法》,通过注塑成型大板材,然后根据玻纤取向分布的不同切割成不同尺寸要求的试样,如图1所示。表1为0˚、45˚和90˚玻纤取向的拉伸试样尺寸。
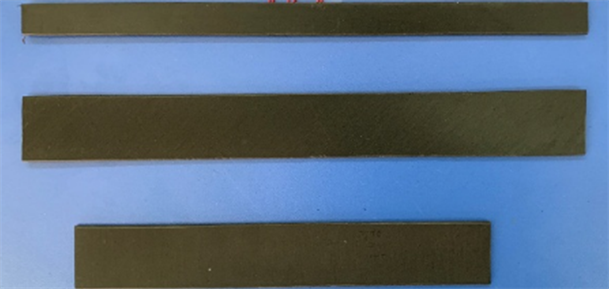
Figure 1. Stretch samples with different fiberglass orientations
图1. 不同玻纤取向的拉伸试样
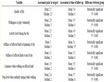
Table 1. Dimensions of tensile test samples
表1. 拉伸试验试样尺寸
2.2. 拉伸试验
2.2.1. 试验目标
表2为影响PA6/SGF复合材料力学性能的4种因素,其中玻纤含量在注塑工艺中控制玻纤和尼龙6的比例得到;玻纤取向在板材切割试样时控制切割角度得到;温度和拉伸应变率可以通过调整实验设备进行控制。为确保实验的准确性,对所有影响因素进行全矩阵实验,且所有实验的有效采样数为3个,总共保证405次有效实验。通过拉伸实验测得PA6/SGF复合材料在不同影响因素组合下的弹性模量、屈服强度、抗拉强度等材料力学参数,为后文B柱上接头CBS结构有限元建模赋予准确的材料参数,以便更加真实的分析出B柱上接头CBS结构的耐撞性能。
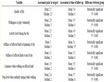
Table 2. Full matrix of tensile test influencing factors
表2. 拉伸试验影响因素全矩阵
2.2.2. 影响因素分析
玻纤取向的影响:从表3可以分析得出:随着玻纤取向角度的增加,PA6/SGF复合材料各项材料力学参数(弹性模量、屈服强度、抗拉强度)都会减小且呈现出减幅降低的趋势。这说明了复合材料纤维取向和施载方向所成的角度对其性能参数有着直接的影响,当纤维方向与施载方向一致(即0˚)时,复合材料整体所能承受的应力值达到最大;当纤维方向和施载方向垂直(即90˚)时,复合材料整体所能承受的应力值达到最小。
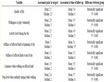
Table 3. Analyzing the stress and strain curves of each glass fiber orientation
表3. 分析玻纤取向的各应力应变曲线
玻纤含量的影响:从表4可以分析得出:随着玻纤含量的增加,PA6/SGF复合材料各项材料力学参数呈现出先增大后减小的趋势。这说明了在复合材料中,纤维的含量并不是越多越好,而是要和基体满足一定的体积比,才能最大化的发挥两种材料的作用。在这里对于纤维增强塑料来说,存在一个合理的经济效果,即当基体所受到的应力达到自身极限的同时,纤维受到的应力也达到了自身的极限,两者同时失效,就是最合理的经济效果,此时的基体纤维体积之比被称作临界体积比。
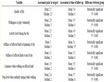
Table 4. Analyzing the stress and strain curves of glass fiber content
表4. 分析玻纤含量的各应力应变曲线
温度的影响:从表5可以分析得出:无论是多少玻纤含量还是何种玻纤取向,随着温度的升高,PA6/SGF复合材料各项材料力学参数都会逐渐减小。这说明了温度升高使得GFRP材料性能降低。究其原因,在GFRP材料的构成组分中,温度对基体(尼龙)力学性能的影响更加明显,随着温度的升高,高分子链变得柔软,使得材料整体性能下降。
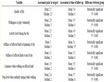
Table 5. Analyzing the stress and strain curves of temperature
表5. 分析温度的各应力应变曲线
应变率的影响:从表3、表4、表5可以分析得出:随着应变率的增加,PA6/SGF复合材料的各项材料力学参数都会有所增大。
3. B柱上接头CBS结构建模与落锤验证
3.1. B柱上接头CBS结构建模
首先在Hypermesh中导入B柱上接头CBS结构模型,在划分网格前要进行几何清理,对模型的一些细节信息进行简化,并抽取中面。对B柱上接头CBS结构中面进行网格划分后的单元总数为16,432个,节点数为16,173个,平均单元尺寸为2.5 mm,如图2所示。
车辆大多时候是置于常温环境中,因此本文模型的材料参数取自于常温(20℃)。根据工程经验及拉伸实验数据分析可知:35%玻纤含量的PA6/SGF复合材料具有良好的材料力学性能。综上,建模的材料参数选择常温(20℃)状态下,35%短玻纤含量条件下不同玻纤取向和不同应变率的材料参数。因为单轴拉伸实验只测得了0˚、45˚、90˚玻纤取向的PA6/SGF复合材料力学性能参数,所以采用TREND函数插值求得30˚和60˚玻纤取向的PA6/SGF复合材料力学性能参数(见表6),根据模流分析的结果,分别将不同角度的材料参数赋予CBS结构。
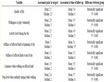
Table 6. Simulation material parameters for each fiberglass orientation
表6. 各玻纤取向的仿真材料参数
3.2. CBS结构落锤试验仿真
对CBS的仿真过程模拟的是落锤冲击试验,采用图3所示的方案。图中A区域为锤头自由落体冲击区域,通过提升锤头下落高度H1 = 0.95 m和H2 = 1.15m以控制锤头在仿真中定向冲击CBS结构的初速度4.32 m/s和4.75 m/s。仿真所用锤头与试验保持一致,质量为14.22 kg。Ls-dyna中材料卡片为MATL20,在仿真中锤头材料参数值如表7所示。B和C区域为试验时夹具夹持位置,在仿真中将采用全约束形式。
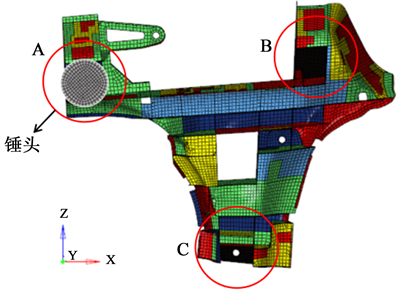
Figure 3. Directional impact simulation scheme
图3. 定向冲击仿真方案
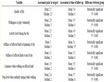
Table 7. Material parameters of hammer head simulation
表7. 锤头仿真材料参数
将设置好的CBS有限元模型导出K文件,在MANAGER中递交求解。在CBS有限元碰撞仿真过程中,总能量应该保持守恒。在仿真刚开始,系统的总能量等于锤头的动能,随着时间的增加,动能逐渐转变成内能,但在这个过程中,总能量是基本保持不变的。图4为仿真结果中的各能量曲线,可以看出各曲线变化符合规律,其中沙漏能的最大值占总能量的0.83%,并没有超过5%,可以说明本次仿真的有效性。
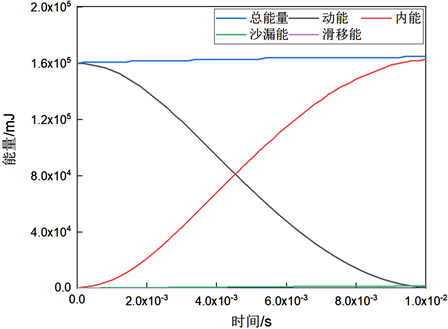
Figure 4. CBS collision simulation energy curve
图4. CBS碰撞仿真能量曲线
3.3. 对比分析验证
表8为锤头高度H = 1.15 m,锤头初速度V = 4.75 m/s条件下,在CBS结构第一次发生回弹前高速摄像机记录的碰撞过程与仿真碰撞过程的时序图对比。为了更加清晰地看清楚B柱上接头CBS结构在各时刻的变形,在仿真图中将锤头隐藏。从时序对比图中可看出,B柱上接头CBS结构在定向冲击试验过程中与仿真计算过程中的变形基本保持一致。
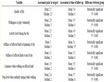
Table 8. Comparison diagram of test and simulation timing
表8. 试验与仿真时序对比图
从图5初速度为4.32 m/s的加速度对比图可以得到:定向冲击试验所测得的加速度曲线峰值为627.7 m/s2,仿真计算所测得的加速度曲线峰值为609.8 m/s2,试验较仿真计算高出约2.9%,为了保证验证的可信度,再次设置锤头高度H = 1.15 m,以较高的4.75 m/s初速度对B柱上接头CBS结构进行定向冲击。从图6对比可以得到:定向冲击试验所测得的加速度曲线峰值为803.7 m/s2,仿真计算所测得的加速度曲线峰值为841.2 m/s2,试验较仿真计算高出约4.5%,两者吻合度较高。通过定向冲击试验与仿真计算的加速度对比,验证了基于玻纤取向的B柱上接头CBS结构有限元模型的有效性,为下文B柱上接头CBS结构优化奠定了基础。
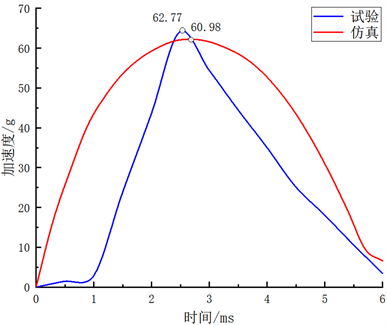
Figure 5. 4.32 m/s acceleration comparison
图5. 4.32 m/s加速度对比
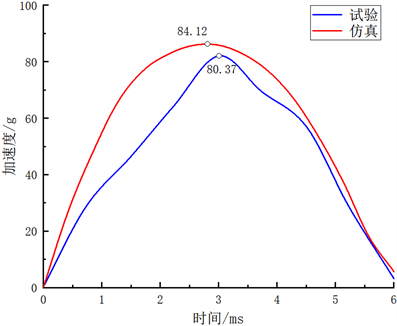
Figure 6. 4.75 m/s acceleration comparison
图6. 4.75 m/s加速度对比
4. 基于耐撞性的结构拓扑优化
4.1. B柱上接头CBS结构耐撞性分析
汽车翻滚碰撞中车身压溃入侵会使乘员的头部空间受到极大地压缩,威胁到乘员的生命安全。所以要减少B柱上接头CBS结构的入侵量 [11] 。另外,B柱上接头CBS结构受到的碰撞力峰值越大,安全性越低。下面以B柱上接头CBS结构在碰撞时的最大入侵量和碰撞力峰值作为评价指标。为便于观察分析,将网格透明化,黄色区域为B柱上接头CBS结构三个角上螺栓孔6个自由度为0的约束,如图7所示。
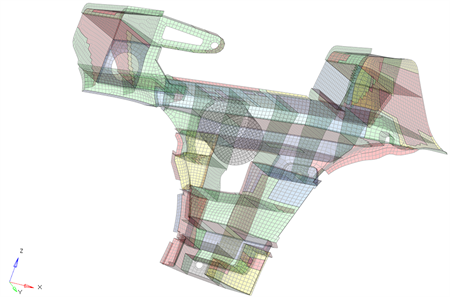
Figure 7. Settings of constraints and drop hammers
图7. 约束及落锤的设置
本文采用锤头对CBS结构中部区域进行Y轴正向定向冲击来模拟车身发生翻滚碰撞时B柱上接头CBS结构受到的定向冲击工况。设置锤头定向冲击初速度为13,411 mm/s。
通过提交Ls-dyna计算得到最大入侵量与碰撞力峰值。图8为CBS结构入侵量变化曲线,最大入侵量为61.11 mm。图9为CBS结构碰撞力变化曲线,碰撞力峰值为10468.5 N。
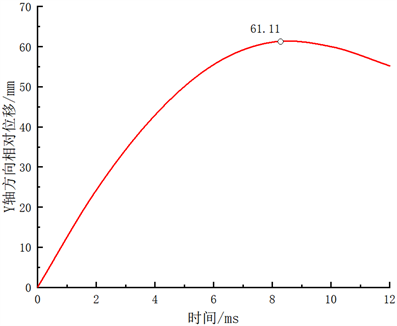
Figure 8. Change curve of invasion volume
图8. 入侵量变化曲线
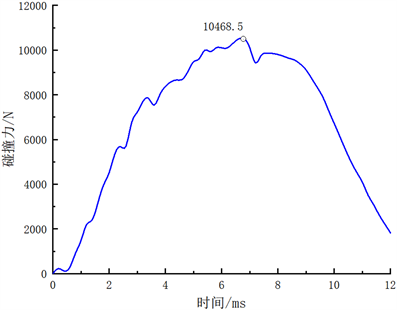
Figure 9. Change curve of collision force
图9. 碰撞力变化曲线
4.2. 结构拓扑优化方法
拓扑优化是众多优化中使用较多的一种。通过设定响应和目标,可以根据载荷的大小,结合自身的尺寸形状,将结构主要承力部分保留,生成较为原始的模型。它的灵活之处是,在保持结构性能基本不变的情况下,通过调整保留材料的百分比,实现不同程度的轻量化。拓扑优化中的三要素为:设计变量、约束条件及优化目标 [12] 。连续体拓扑优化的方法一般有三种,分别是均匀化法、变密度法和渐进结构优化法,其中变密度法最为常用。
变密度法的基本思想是将分析的结构离散化,假设每个离散单元的材料密度在0到1之间变化,以整个离散结构变化的材料密度为变量,对结构进行工况设置,求解分析 [13] 。
4.3. 结构拓扑优化模型
网格划分:通过连接原B柱上接头CBS结构外廓线(图10)得到了体积增大的T型概念结构(图11)。这样的结构增加了优化空间以及拓扑优化的自由度。对T型概念结构采用四面体单元(tetramesh)进行网格的划分,网格尺寸为3 mm,共有96,361个节点,489,665个单元。
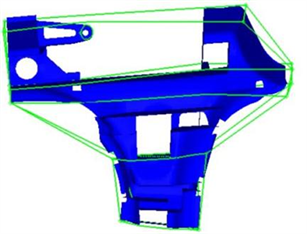
Figure 10. B-pillar joint CBS structure outer profile
图10. B柱上接头CBS结构外廓线
材料属性定义:选择材料卡片MAT1并代入常温下35%玻纤含量0˚玻纤取向的PA6/SGF复合材料参数创建材料,具体参数如表9所示。
定义载荷和约束:在T型概念结构中部区域创建一个REB2单元,对REB2单元施加一个7000 N的力,载荷沿着Y轴正方向。将CBS结构的三个角上的螺栓孔进行约束,定向冲击位置为CBS结构中部区域。
拓扑优化模块 [14] 建立:
1) 创建设计变量:设计变量为设计空间中的单元密度,即图11中T型结构四面体单元密度;
2) 定义响应:定义体积分数和柔度为两个响应;
3) 定义约束:为了尽量减小T型概念结构优化后的体积,定义约束为体积分数小于0.3;
4) 定义优化目标:优化目标设定为Min问题,目标为最小柔度即最大刚度。
基于变密度方法的拓扑优化模型为:
(1)
其中,C为柔度值;
为载荷向量;
为刚度矩阵;
为位移列向量;V为体积;
为优化后的体积;
为材料密度即设计变量,值为
之间。
优化结果:如图12为单元密度值在0.5以上的加强筋拓扑密度图。
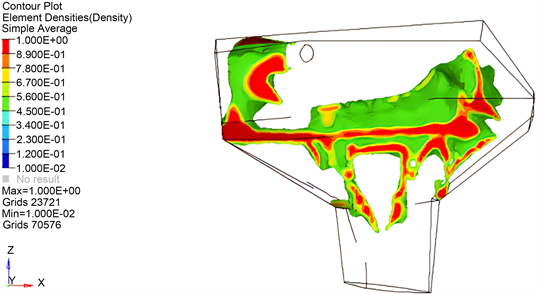
Figure 12. Topological density diagram of stiffeners
图12. 加强筋拓扑密度图
根优化结果建立新模型:根据拓扑优化结果,结合优化前的B柱上接头CBS结构,得到最终的优化结果如图13所示,模型总质量为527.8 g。
耐撞性分析:对优化后的CBS结构进行模流分析,并赋予材料属性,设置和CBS结构耐撞性分析同样的定向冲击工况,约束CBS结构的三个角,赋予锤头13,411 mm/s的Y轴正向冲击初速度,如图14所示,并提交Ls-dyna计算求解。图15为优化后的CBS结构入侵量变化曲线,最大入侵量为49.21 mm;图16为优化后的CBS结构碰撞力变化曲线,碰撞力峰值为5168.13 N。可以看出优化后CBS结构的耐撞性较原结构有了很大的提升,但质量略有提高(具体参数见表10),不符合轻量化的要求。下面将对优化后的CBS结构进行多目标优化设计,在不提高质量的前提下提高耐撞性。
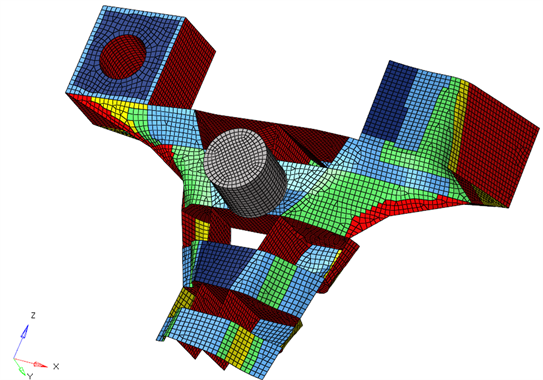
Figure 14. Simulation of crashworthiness of CBS structure after optimization
图14. 优化后CBS结构耐撞性模拟
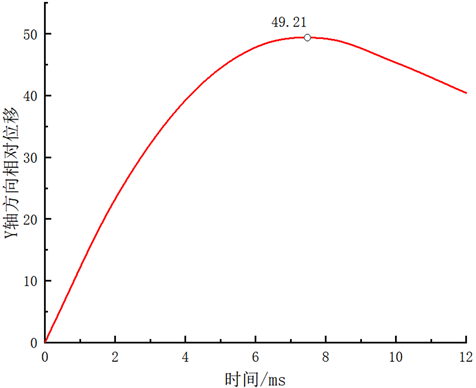
Figure 15. Intrusion change curve after optimization
图15. 优化后入侵量变化曲线
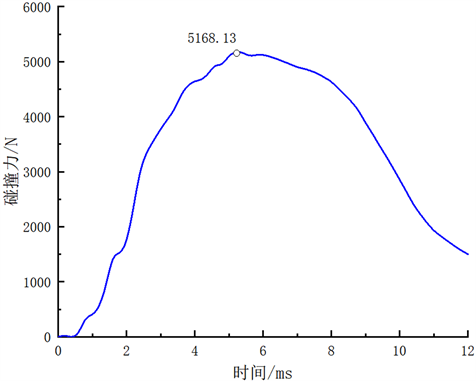
Figure 16. Collision force change after optimization
图16. 优化后碰撞力变化曲线
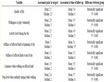
Table 10. Comparison of CBS structural parameters before and after optimization
表10. 优化前后CBS结构参数对比
4.4. 基于NSGA-II算法的多目标优化
在进行精益化结构设计时,将B柱上接头CBS结构分为三个部分:加强筋结构、外包络面结构以及内包络面结构,如图17所示。优化B柱上接头CBS结构三部分结构的厚度值都为2.5 mm。
(a) 加强筋 (b) 外包络面 (c) 内包络面
Figure 17. Optimizing the three parts of the CBS structure of the B-pillar joint
图17. 优化B柱上接头CBS结构三个部分
为了不发生突变,这3个结构的厚度值应设计得尽量靠近,因此精益化结构设计的加强筋结构厚度值在2.3~2.7 mm之间,外包络面结构厚度值在2.7~3.3 mm之间,外包络面结构厚度值在2~2.3 mm之间。
以内包络面结构厚度t1、加强筋结构厚度t2、外包络面结构厚度t3为设计变量,以优化后的质量
小于原B柱上接头CBS结构质量518.7 g为约束,以入侵量
(单位:mm)最小和碰撞力峰值
(单位:N)最小为目标函数,建立数学设计模型如下:
(2)
QPRS:精益化结构设计引入了NSGA-II算法对优化B柱上接头CBS结构进行优化,目的是得到一个既满足轻量化要求又满足耐撞性要求的车身接头。在运用NSGA-II算法进行精益结构优化设计前采用二次多项式响应面(Quadratic Polynomial Response Surface,QPRS)构建近似模型。为了保证QPRS的精度,本文采用最优拉丁超立方试验设计(Optimal Latin Hypercube Design, Opt LHD) [15] 对内包络面结构厚度、加强筋结构厚度、外包络面结构厚度变量区间抽取80个样本点。将80个样本点三部分结构的厚度值代入优化B柱上接头CBS结构模型计算,表11为抽取的样本点及响应值。
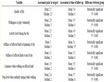
Table 11. Sample points and response values
表11. 样本点及响应值
将样本点及其响应值代入QPRS模型 [16] ,QPRS模型函数表达为式(3)所示。式中t为自变量即三部分结构的厚度值,
,
,
是未知参数,构成列向量
。
(3)
本文通过最小均方差(Root Mean Square Error, RMSE)来验证QPRS模型的精确度。RMSE的函数表达为式(4)所示,RMSE的值越接近0,则说明近似模型的精度越高。质量、最大入侵量和碰撞力峰值3个响应量的RMSE分别为0.0007、0.0381和0.1392,表明QPRS模型达到了非常高的精度,可代入NSGA-II算法进行精益优化设计。
(4)
NSGA-II:NSGA-II算法一方面降低了计算的复杂程度,另一方面保留了最为优秀的所有个体,具有运行速度快,解集的收敛性好的优点 [17] 。NSGA-II优化算法参数如表12所示。
经过1000次迭代得到最优解方案为:内包络面结构厚度为2.0775 mm,加强筋结构厚度为2.3001 mm,外包络面结构厚度为3.2996 mm。预测响应值质量为516.14 g,最大侵入量为52.44 mm,碰撞力峰值为516.14 N。由于厚度精度过高不利于实际工程的加工,所以内包络面结构厚度取2.07 mm,加强筋结构厚度取2.3 mm,外包络面结构厚度取3.29 mm。将上述优化点的变量值代入优化B柱上接头CBS结构模型中进行求解计算得到的质量为517.5 g,最大侵入量为52.25 mm,碰撞力峰值为517.5 N。如表13所示,优化点的预测值与计算值的相对误差都非常小,在可以接受的范围内。
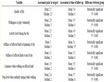
Table 13. Comparison of predicted and calculated values of optimization points
表13. 优化点的预测值与计算值对比
优化B柱上接头CBS结构精益化结构设计后,对其进行耐撞性分析。计算结果显示:最大入侵量为52.25 mm,与原B柱上接头CBS结构的入侵量历程曲线对比如图18所示;碰撞力峰值为4263.26 N,与原B柱上接头CBS结构的碰撞力历程曲线对比如图19所示。
通过精益化结构设计后的B柱上接头CBS结构与原B柱上接头CBS结构各项参数对比如表14所示。
最终优化设计后的B柱上接头CBS结构与原B柱上接头CBS结构相比,在不提高质量的前提下,最大入侵量和碰撞力峰值都有大幅降低,提高了其耐撞性能。当发生翻滚碰撞时,可以增大成员的头部空间和减少冲击力,从而保护乘员。
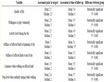
Table 14. Comparison of CBS structure crashworthiness parameters before and after optimization of B-pillar joints
表14. 优化前后B柱上接头CBS结构耐撞性相关参数对比
5. 总结与展望
5.1. 全文总结
本文研究对象为某款电动MPV上的B柱上接头CBS结构,是一个由PA6/SGF复合材料注塑形成的T型零件。基于车身耐撞性能CBS结构拓扑优化设计的主要内容和创新点如下:
1) 考虑玻纤含量、玻纤取向、应变率及温度4种因素,对PA6/SGF复合材料进行全矩阵拉伸实验设计分析得到:随着玻纤取向角度的增大,PA6/SGF复合材料各项材料力学参数(弹性模量、屈服强度、抗拉强度)都会减小且呈现出减幅降低的趋势;随着玻纤含量的增加,PA6/SGF复合材料各项材料力学参数呈现出先增大后减小的趋势;随着环境温度的升高,PA6/SGF复合材料各项材料力学参数都会逐渐减小;随着应变率的增大,PA6/SGF复合材料的各项材料力学参数都会有所增大。
2) 本文以定向冲击方向为基准,根据映射在B柱上接头CBS结构上的玻纤取向分布,将B柱上接头CBS结构分为5个区域并赋予相应的材料属性。之后基于玻纤取向的B柱上接头CBS结构进行有限元建模,并通过定向冲击试验验证了有限元模型的有效性。
3) 通过对B柱上接头CBS结构进行拓扑优化及精益化结构设计后,不提升质量的前提下,最大入侵量和碰撞力峰值分别下降了14.5%和59.28%。通过本文的优化方法,大幅提高了B柱上接头CBS结构的耐撞性能。
5.2. 研究展望
1) 为了更加精确地研究玻纤含量、玻纤取向、应变率及温度对SGF-PA6复合材料力学性能的影响,还可以增加更多的变量因素。比如增加20˚、50˚、70˚等玻纤取向,10%、30%、50%等玻纤含量,以及其它温度与拉伸应变率。本文由于经费和时间有限,只选取了有代表性的变量因素进行拉伸实验。
2) B柱上接头CBS结构通过结构优化后未说明螺栓孔的位置与大小,若要考虑B柱上接头CBS结构与B柱与车顶梁间的装配关系时,需要进一步深入地研究。