1. 引言
发展清洁能源,实现“双碳”目标,需要储能技术的支持,因此近年来电力储能技术的研究开发一直是能源科技领域的重点领域之一 [1] 。张光玉 [2] 提出了一种基于溶液浓度差的电力储能系统,通过浓缩溶液以化学能形式完成储能、再通过缓压渗透(PRO)或反向电渗析(RED)释放出储存的能量。He W等 [3] 进行了此类储能系统的可行性分析,Rui Long等 [4] 进行了基于反渗透和缓压渗透(RO-PRO)电力储能系统的理论分析,得出理想情况下系统往返能量效率可达38.27%。虽然还低于抽水蓄能,但该系统布署灵活,方式不受地理因素限制,值得进一步深入研究,提高其性能,以便为电力储能提供新的技术选择和支持。
PRO工艺利用半透膜将浓缩的溶液(驱动液)储存的化学能转化为水力能。PRO膜过程中,由于驱动液的持续稀释和溶质向原料液的扩散,膜两侧溶液盐度梯度动态变化 [5] ,驱动液和原料液操作参数如浓度、操作压力、流量等对PRO过程的能量输出均有一定影响 [6] 。研究表明,优化驱动液侧的液压、驱动液流量有助于提高能量输出 [7] [8] 。但在实际工程中,PRO所能采用的实际操作压力受膜组件承压能力的制约。此外,前述研究大多忽略了膜两侧浓度极化和反向盐通量的影响,这导致实际功率与理论计算功率相差甚远。基于此,我们构建了一个包含浓度极化、溶质反向渗透以及各种机械损失 [9] 的PRO释能模型,并采用PSO优化算法进行不同初始储能溶液浓度下PRO释能过程的优化研究,以便为PRO过程确定膜组件数、液压和驱动液、原料液流量比等最佳运行参数,提高PRO释能过程效率。
2. PRO释能模型
PRO释能过程如图1所示。浓驱动液在低压泵的作用下流入压力交换器,压力升高后经过增压泵进一步增压后进入正渗透膜,在膜另一侧原料液中的水透过渗透膜与浓驱动液混合,驱动液被稀释,流量增加为
。随后被稀释的高压驱动液分流,流量为
的稀释驱动液流入压力交换器,流量为
的稀释驱动液流入透平带动发电机发电。
2.1. PRO过程通量模型
PRO过程水通量以及反向盐通量模型式采用(1)、(2)计算 [10] [11] [12] [13] :
(1)
(2)
其中:
为水通量
和
分别为驱动液和原料液渗透压,
和
分别为驱动液侧和原料液侧边界层的传质系数,A为膜的水渗透系数,B为膜的溶质渗透系数,K为溶质传阻系数,
和
分别为驱动液侧和原料液侧溶液浓度,
为驱动液侧和原料液侧液压差。
PRO过程中,膜两侧溶液的浓度极化和膜对溶质的不完全截留是影响实际PRO释能过程的两个主要因素。如图2所示,考虑上述因素,依据能量守恒、质量守恒建立微元PRO过程控制方程。
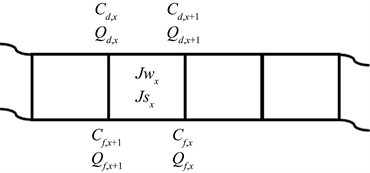
Figure 2. Schematic diagram of microelement PRO process
图2. 微元PRO过程示意图
(3)
(4)
(5)
(6)
其中:
分别为驱动液侧
处和x处流量、原料液侧
处和x处流量,
分别为驱动液侧
处和x处浓度、原料液侧
处和x处浓度,S为每一分段所对应面积。
模型中室温下(25℃)溶液渗透压和溶液运动粘度通过OLI Analyzer软件导出。为在计算模型中实现渗透压和粘度随溶液浓度改变而动态变化,通过MATLAB进行拟合。结果见表1。拟合结果校正决定系数(Adjusted R-square)均为1。
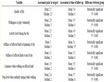
Table 1. NaCl fitting results γ = a 1 x 4 + a 2 x 3 + a 3 x 2 + a 4 x + a 5
表1. NaCl拟合结果
2.2. 通量模型验证
利用MATLAB编程进行上述PRO通量方程和控制方程的分段离散化数值计算,并利用Yasuhiko等的实验研究数据 [14] 进行验证。结果表明,计算结果与实验数据较为一致(图3)。计算中,驱动液和原料液为1M NaCl和去离子水,膜面积为70.2 m2,溶质渗透系数B为0.035 L/(m2∙h),水渗透系数A为0.27 L/(m2∙h∙bar),膜结构参数S为1038 μm。
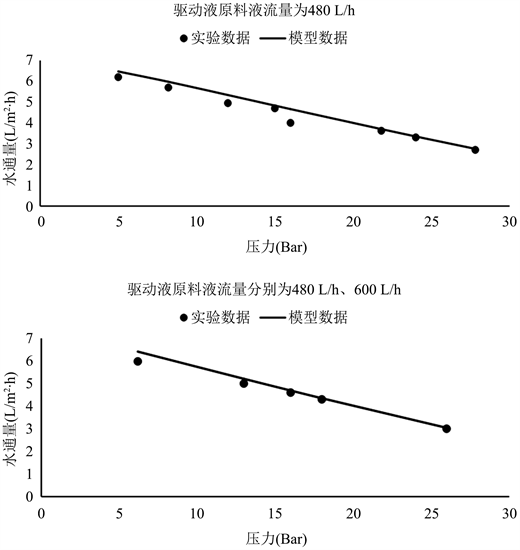
Figure 3. Comparison of experimental and simulated values
图3. 实验数值和模拟数值对比
2.3. 净功计算模型
PRO过程消耗能量为机械损耗和膜通道阻力损失。机械损耗数据见表2。膜通道阻力损失可由达西–威斯巴哈方程计算得出 [15] 。PRO过程净功值由式(7)~(11)得出 [9] [15] 。
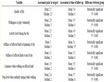
Table 2. PRO process mechanical efficiency
表2. PRO过程机械效率
(7)
(8)
(9)
(10)
(11)
其中:
分别为PRO产能功、驱动液低压泵消耗功、原料液低压泵消耗功、驱动液增压泵消耗功、净功,
分别为驱动液膜前压力、驱动液侧压力损失、原料液侧压力损失,
分别为水轮机、发电机、泵、电机、PX压力交换器效率。
3. PRO释能过程优化的目标函数
储能密度是所有储能系统中较为重要的一个性能参数,对基于溶液PRO过程的新型电力电储能系统,如式(12),定义储能密度为单位体积浓溶液所能产生的最大能量(NSE),并作为本研究的优化目标:
(12)
为获得较高的储能密度,必须使PRO过程输出的能量最大化,为此需要采用合适的优化算法优化PRO过程操作参数。
4. PRO优化方法
智能算法能以较少的计算成本处理问题,能够提供全局最优解并且具有较高的搜寻能力。PSO算法依靠粒子速度进行搜索,并且把最优粒子信息传递给其它粒子,搜索速度快。所需调整参数少,易于工程使用,已被广泛应用于能源等领域的系统优化 [16] [17] [18] [19] 。在优化系统参数问题上体现出一定优越性,因此本文采用智能算法中的粒子群算法进行PRO过程优化。
对于储能浓缩后的驱动液盐度,膜面积、液压、驱动液流速是影响过程能量输出的最关键参数。采用PRO膜的参数为:单支膜组件面积为35.1 m2、溶质渗透系数 为0.035 L/(m2∙h),水渗透系数 为0.27 L/(m2∙h∙bar),膜结构参数S为1038 μm [14] 。膜面积大小很大程度上影响PRO过程,膜面积过小时,系统所产生的能量不足以抵消机械损失,膜面积过大时,由于沿流道盐度梯度逐渐减小,造成水通量减小,以至于导致系统平均功率降低。但是膜面积参数由制模厂家决定,不可能随时变动,因此优化时选用一到四支膜组件作为面积变量。之前大多数研究认为
和
时,PRO过程有最优发电量 [20] [21] 。
5. 结果与讨论
5.1. 驱动液压力优化
驱动液压力是控制PRO工艺产能的关键操作参数,一方面由式(1)可知驱动液压力直接影响PRO膜过程水通量大小,另一方面由式(7)可知驱动液压力直接影响PRO发电过程最终净发电量大小。选用
情况下,使用PSO算法对液压进行优化。并将优化后的系统与未优化系统(
)进行比较。
(a) 不同盐度梯度PRO过程优化后压力与未优化压力对比
(b) 不同盐度梯度PRO过程优化后净发电量与未优化对比
(c) 不同膜组件数下液压优化过程带来的净发电量增加情况
(d) 3M-0M浓度梯度下不同膜组件数量液压优化后与未优化时驱动液浓度变化情况
Figure 4. Hydraulic optimization results
图4. 液压优化情况
由图4(a)可见,对于任意的盐度梯度,最优液压均小于
,驱动液和原料液的盐度差越大,最优压力与
的差异就越大。4M-0M盐度梯度下,最优液压与
相差2619 Kpa,而1M-0M盐度梯度下仅相差293 Kpa,这是因为在跨膜水通量相同的情况下,驱动液的浓度越高被稀释的程度就越大,其渗透压减小的程度也越大,从而导致最佳液压变化程度较大。1M-0M盐度梯度下的最佳液压为2100 Kpa,膜组件数量变化对最佳液压影响不显著。但对于其它的盐度梯度,最佳液压随着膜组件数量的增加先减小后增加。为了分析这种现象原因,选取3M-0M盐度梯度,在最优压力下,膜组件中驱动液浓度的变化见图4(d),一组膜组件在最优压力下驱动液没有完全稀释,因此还有多余能量没有释放,而两组膜组件在最优压力下驱动液不能进一步被稀释,再增加膜组件只会增加阻力并不会增加水通量,甚至会变成反渗透,因此驱动液被稀释完全的情况下再增加膜组件就会使最优液压变高。由图4(b)显示,对于所有盐度梯度,经过PSO优化液压后均能提高净发电量。盐度梯度越高,PSO优化后净发电量提升的效果越好,盐度梯度越低,净发电量提升程度越小。3M-0M、2M-0M、1M-0M浓度梯度,PRO系统随着膜组件数量增加,净发电量也不断增加,但是每增加一个膜组件所带来的净发电量的提升越小。4M-0M盐度梯度,PRO系统在三个膜组件时净发电量达到最大,加入第四个膜组件后,其净发电量相比三个膜组件时有一定程度减小,出现这种现象的原因是在一定压力下,驱动液在第三个膜组件时已经完全稀释,再增加膜组件不会在多产能反而会因为流动阻力的存在多耗功。图4(c)显示,经过PSO优化液压,PRO系统的净发电量增加了1%~14.35%。盐度梯度越大优化效果越好。对于2M-0M、1M-0M浓度梯度,优化效果随着膜组件数量的增加而增加。对于4M-0M、3M-0M盐度梯度,三个膜组件时优化效果达到最好,但是第四个膜组件时,优化效果下降。
适当增加PRO模块的改善了化学能转化为机械能的过程,从而使盐度梯度资源的能量产量最大化。总体而言,盐度梯度为4M-0M时PRO工艺的发电量最大,为2.34 kW∙h/m3,盐度梯度为1M-0M时发电量最小为0.3372 kW∙h/m3 (图4(b))。经过优化PRO工艺的能量输出略有提高(1%~14.35%),最佳操作压力也有明显下降。这表明优化后的PRO过程比正常PRO过程需要更低的压力运行。此外,由于PRO工艺在较低的水压下工作,优化后的PRO工艺对膜的承压能力性能要求变低。经过液压优化后,驱动液出口的溶液浓度不确定。
5.2. 驱动液流量比优化
驱动液流量和原料液流量之比对PRO过程的性能有着重大影响。实验室规模的实验表明,PRO过程的性能高度依赖驱动液和原料液流量 [8] 。因此使用PSO优化驱动液流量和原料液流量之比,从而在PRO工艺中,在1到4个膜组件、
和
条件下产生最大能量输出。驱动液原料液流量之比
见式(13)。
(13)
其中:
为驱动液和原料液流量比,
为驱动液侧流量,
为原料液侧流量。
图5(a)所示,优化后的PRO过程中,任意盐度梯度驱动液与原料液最佳流量比都小于0.5,盐度梯度越大,流量比越接近0.5,流量比还随着膜组件数量的增加而增加。单个膜组件情况下,1M-0M盐度梯度最优流量比为0.064,4M-0M盐度梯度最优流量比为0.200,显然盐度梯度越大,最佳流量比越大。这是因为盐度梯度越大,驱动液越容易被稀释,而增大流量能在一定程度上减小驱动液被稀释程度。在4M-0M盐度梯度下,PRO过程使用单个膜组件时最佳流量比为0.200,而在四个膜组件时最佳流量比为0.433。原因是增大驱动液流量可以抵消后续PRO模块中驱动液的稀释。图5(b)所示,任意的盐度梯度下,优化后的PRO过程净发电量虽然会随膜组件数量增加而略微减小,但整体上保持稳定。未优化过程则不同,对于3M-0M、2M-0M、1M-0M盐度梯度,净发电量随着膜组件的增加而增加,4M-0M盐度梯度,净发电量随着膜组件的增加先增加而后减少。为解释上述现象原因,选择3M-0M盐度梯度进行膜内驱动液浓度变化研究(图5(d))。未优化时,任意数量膜组件的PRO过程中,驱动液没有被稀释完全,还有剩余化学能没有利用。经过PSO优化流量,使得在任意数量膜组件的PRO过程中,驱动液被完全稀释(驱动液出口浓度所对应的渗透压等于驱动液侧所加压力),能量利用率达到最高。但随着膜组件数量的增加,PRO过程中沿程阻力也变高,所以会造成膜组件数量增加时,净发电量会有较小幅度下降。图5(c)所示,盐度梯度越低,膜组件数越少驱动液流量优化效果越好,1M-0M盐度梯度,一个模组件情况下,优化后的净发电量提升了222%。而对于4M-0M盐度梯度,四个膜组件的情况下优化后净发电量仅仅提升了0.8%。
驱动液流量优化实质上是在一定的外加压力和原料液流量时,找到一个合适的驱动液流量,使得PRO过程后,驱动液出口浓度所对应的渗透压与外加压力相同(驱动液不能进一步稀释)。驱动液出口浓度可由液压确定。
(a) 不同盐度盐度梯度PRO过程优化后与未优化流量比
(b) 不同盐度梯度PRO过程优化后与未优化净发电量情况
(c) 不同膜组件数下流量比优化过程带来的净发电量增加情况
(d) 3M-0M盐度梯度下不同膜组件数量流量优化后与未优化时驱动液浓度变化情况
Figure 5. Draw solution optimization results
图5. 驱动溶液优化结果
6. 结论
本研究采用PSO对PRO工艺的性能进行了评估,优化了驱动液侧压力和驱动液流量两个PRO过程关键操作参数。与未优化的PRO工艺相比,优化后的PRO工艺的能量输出提高了1%~222%。优化研究表明,理论PRO工艺中的最佳操作压力和流量比在非理想PRO工艺中并不适用。与理想的PRO系统相比,优化后的PRO工艺可以在较低的压力下、较低的驱动液、原料液流量比下操作。
NOTES
*通讯作者。