1. 引言
随着全球科学技术的不断进步,电子产品的迭代速度正在突飞猛进,而每年电子废弃物正在以惊人的指数型增长 [1] 。其中,废弃印制电路板(Printed Circuit Boards,以下简称PCB)是其中最复杂、最具有危害性的组成部分,如若处理不当,其对环境所造成的实际污染会更为严重 [2] 。以PCB中的铜组分为例,伴随着PCB生产过程中蚀刻工艺的优化和进步,铜组分在PCB中的实际占比已经突破30%,成为PCB中占比最大的组成成分 [3] [4] 。根据我国工业和信息化部印发《“十四五”软件和信息技术服务业发展规划》中显示,印制电路板行业仍将会作为我国新一代电子信息产业技术的未来重要发展领域之一。因此,随着电子产业的高速发展,在未来必会有大量的PCB堆砌,如若弃之不理或只使用掩埋的方式,必然会造成大量铜元素的浪费,同时也会引发极其严重的铜污染事件,对人体和生态环境造成严重威胁。同时,由于PCB回收行业背后所蕴藏的巨大战略价值,如何从PCB中高效回收铜元素,且有效避免对环境造成二次污染,已经需要逐步的引起社会和市场的高度认知 [5] [6] 。
目前,现有的传统处理模式都是从传统物理处理工艺和化学处理工艺上衍生而来,而新型的生物冶金和超临界流体技术仍然处于实验室阶段。对于市场而言,面对复杂的PCB污染问题,亟需一种高效且符合市场需求的全新处理模式,因此,超低温处理模式最为符合现阶段的市场需求。超低温处理模式最早出现在美国和日本等发达国家,且随着科技的进步,在欧洲市场已逐步成为主流 [7] [8] 。德国DBURC公司所开发的四段式机械处理工艺,即预破碎、液氮冷冻后粉碎、筛分、静电分选工艺,其整体会回收效率相较于之前的低温处理模式,已经有较为明显的提高,同时该处理工艺在破碎PCB时,也能够在一定程度上防止有害气体和二次污染产生,但该处理模式目前所使用到的最低温度仅有−100℃,所以对于超低温处理模式而言,仍然有较大的提升空间 [9] [10] 。因此,本研究提出了一种全新的超低温处理工艺,即在单一超低温处理基础上,引入室温298 K与超低温77 K之间的循环处理工艺,首先探讨了298/77 K循环处理技术所引起的温度变化,对于PCB内部结构所造成的实际影响,进而测试了PCB内部结构发生变化之后的力学性能变化趋势,并研究了静电分析和离心分选对于298/77 K循环处理工艺的实际回收率影响,之后引入磁选工艺流程,完成对于PCB中铜组分的回收和资源化研究。
2. 实验部分
2.1. 实验材料和仪器
为保证实验数据的严谨性,实验所使用的标准实验仪器,全部按照或参照性能测试项目的标准进行测试,基本参数如下表1所示:
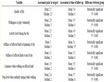
Table 1. Name of main experimental instruments
表1. 主要实验仪器名称
2.2. 性能表征
为保证实验的严谨性,采用thermo scientific Apreo 2 C型扫描电镜对PCB样品内部结构进行SEM表征。之后分别在298 K、210 K、180 K、120 K、77 K、298/77 K (298/77 K处理模式:即先将PCB浸泡在液氮内15天,之后取出等待PCB温度升至室温298 K后,再放置于液氮中等待PCB温度降至77 K后取出,反复循环共计30次为止)共6种处理模式下测试PCB的力学性能变化,并确定最佳处理方式。
2.3. 金属粉末回收实验
对PCB进行预处理之后,放入金属研钵进行粗碎,之后进一步使用破碎机进行破碎,再转入高能球磨机细碎,之后使用符合泰勒筛制100目和200目的筛网进行筛分,并筛分为6组:A1A2组为尺寸大于0.147 mm的粉末样品,B1B2组为0.147 mm~0.074 mm的粉末样品,C1C2组为小于0.074 mm的粉末样品,将A1、B1和C1组粉末样品进行静电分选,将A2、B2和C2组进行离心分选,分别筛分出金属粉末。
2.4. 铜组分回收实验
针对PCB中铜组分的回收和资源化处理,可以利用不同组分的磁性差异,选择使用磁选的方式来回收。其中,磁选实验所使用的PCB试样,取自经上述实验所确定的最佳处理条件后,所分选获得的PCB粉末样品。将PCB金属粉末首先使用低温超导磁选机,并利用菱形钢棒介质网作为分选材质,经0.8 T中磁场去除铁杂质后,继续将磁场强度提升至5 T后,进行一次初步扫选(粗选),之后提高磁选机的磁场强度至7 T,进一步扫选(磁选)分离铜组分,流程如图1所示 [11] 。
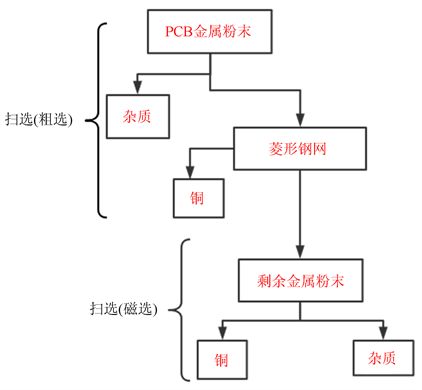
Figure 1. Magnetic separation process of copper
图1. 铜的磁选流程
3. 结果与讨论
3.1. 温度对PCB内部结构的影响和力学性能变化趋势
选择在298/77 K循环处理模式下,使用扫描电镜对PCB内部结构进行表征,并引入298 K、77 K处理模式进行对比。
(a)
(b)
(c)
Figure 2. Microstructure of PCB in different modes: (a) Microstructure at 298 K; (b) Microstructure at 77 K; (c) Microstructure under 298/77 K cyclic treatment
图2. PCB在不同模式下的内部结构微观形貌:(a) 298 K条件下的微观形貌;(b) 77 K条件下的微观形貌;(c) 298/77 K循环处理条件下的微观形貌
如图2所示,PCB试样在298/77 K循环处理的条件下,可以呈现出更加错综杂乱的“块斑状”裂纹形貌。另引入热膨胀系数对比,如图3所示,当PCB的处理模式发生改变时,频繁的温度变化可以使PCB内部结构自身体积膨胀变化增大,更易增加PCB内部结构的偏转和扭曲。因此,综合考虑其原因在于PCB在极限低温状态下,其内部结构中分子链会被加速冻结,分子运动速率出现下降,从而导致脆性状态增加,同时在测试过程中,利用液氮作为降温介质时,在摩擦过程中产生的热量会被介质带走,加速了对分子链运动的抑制 [12] 。
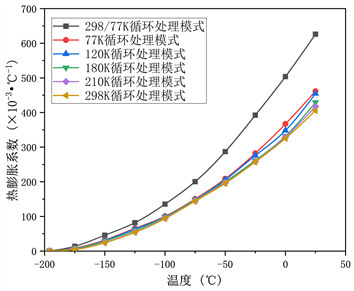
Figure 3. PCB thermal expansion coefficient comparison
图3. PCB热膨胀系数对比
为保证实验严谨性,继续选择在环境试验箱中喷淋液氮,维持温度并进行力学测试实验。
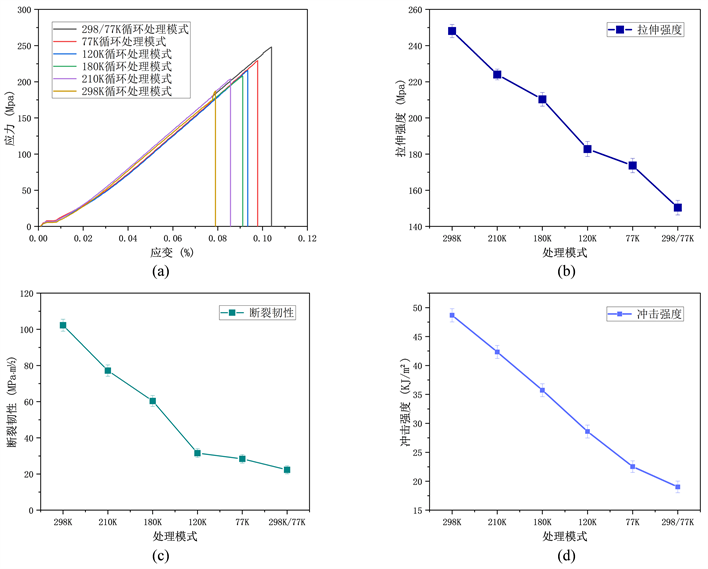
Figure 4. Characterization of mechanical properties of PCB: (a) stress-strain curves in different modes; (b) tensile strength in different modes; (c) fracture toughness in different modes; (d) impact strength in different modes
图4. PCB力学性能表征:(a) 在不同模式下的应力–应变曲线;(b) 在不同模式下的拉伸强度;(c) 在不同模式下的断裂韧性;(d) 在不同模式下的冲击强度
如图4所示,在6种不同处理模式中,PCB在经过298/77 K循环处理后,应力–应变曲线呈现出更加明显的脆性性质。因此,继续测试PCB内部结构改变后的力学性能,其中,拉伸强度降为150.3932 Mpa,断裂韧性降为22.3428 MPa∙m½,冲击强度降为19.0248 KJ/m2,相较于298 K传统处理模式分别降低29.98%、78.15%和60.92%。所以可以证明,PCB内部结构发生变化后,其自身多项力学性能均实现大幅降低 [13] [14] 。因此,最佳处理条件可以设置为298/77 K循环处理模式。
3.2. 静电分选和离心分选对产出率的影响
结合上述实验所确定条件,结合静电分选和离心分选,分别对6组PCB粉末进行筛分。
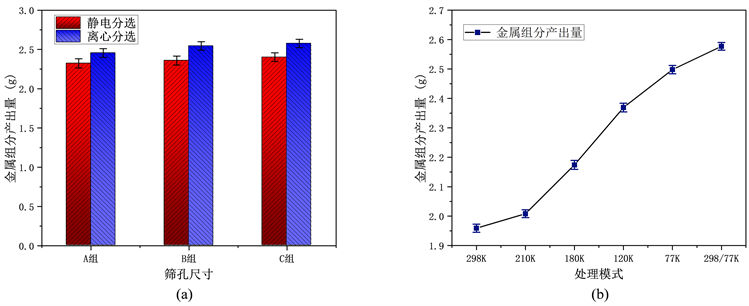
Figure 5. (a) Actual metal component output; (b) Output of metal components in different modes
图5. (a) 实际金属组分产出量;(b) 不同模式下的金属组分产出量
如图5所示,C组PCB金属粉末的回收量达到2.577 g,实际回收率最高,且离心分选的回收效率也高于静电分选,结合内部结构和力学性能变化趋势,分析其主要原因在于:第一,PCB经过频繁且急剧的温度变化后,内部塑性变形积累;第二,PCB内部结构呈现玻璃态,脆性增强,进而易于破碎回收。因此可知,PCB在经过298/77 K循环处理后,继续选择使用200目筛网筛分,并利用离心分选方式,可获得最佳细碎效果 [15] [16] [17] 。
3.3. 298/77 K循环处理对PCB中铜组分回收率的影响
如图6(a)所示,低温超导磁选机在0.8 T的中磁场环境中,首先去除的杂质为铁,其总量为24.7206 g,约占PCB金属组分总量的15.98%,而在磁选机磁场强度继续提升至5 T后,在PCB金属粉末中,铜组分的粗选产出量为79.8396 g,约占PCB金属组分总量的51.64%。因此,通过初步扫选(粗选)可以有效去除PCB金属粉末中的大部分的杂质铁,可以为后续二次扫选(磁选)回收铜组分提供便利。
同时,经过初步扫选(粗选)后,铜组分的实际产出率已经超过50%,基本符合常规PCB在实际生产过程中常见的铜组分占比,但考虑到为进一步提升分离效率,避免PCB中铜组分的浪费,因此将磁选机的磁场强度继续提升至7 T,并进一步分离剩余PCB金属粉末中的铜组分,实际分离效果如图6(b)所示。在进一步扫选(磁选)阶段中,剩余PCB金属粉末中的二次出铜量为9.3313 g,结合初步扫选(粗选)阶段,两次扫选共计出铜量为89.1709 g,约占PCB金属粉末总质量的56.67%,即占PCB总质量的29.49%,同常规PCB在实际生产过程中所使用的铜组分占比基本相似。而在二次扫选(磁选)过程中,杂质铁的二次产出量为0.0789 g,结合初步扫选(粗选)阶段,两次扫选共计出铁量为24.7995 g,约占PCB金属粉末总质量的16.04%,同样也符合常规PCB在实际生产过程中所使用的铁组分占比 [18] [19] 。同时,为保证实验的严谨性,同样引入298 K、210 K、180 K、120 K和77 K处理模式所获得的PCB金属粉末作为对比,获得六种处理模式的实际出铜量,如图7所示。
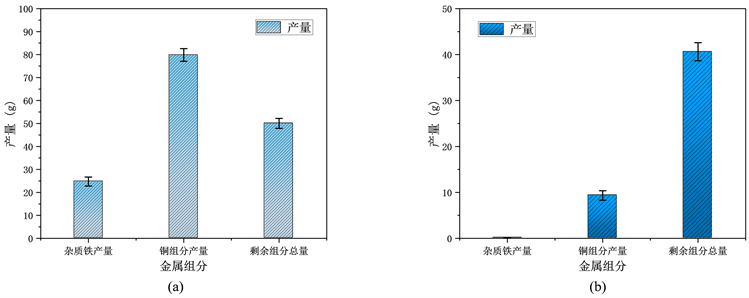
Figure 6. (a) Roughly select the amount of copper; (b) Magnetic separation of copper content
图6. (a) 粗选出铜量;(b) 磁选出铜量
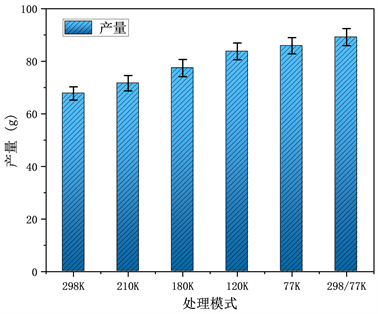
Figure 7. Copper output under different treatment modes
图7. 不同处理模式的出铜量
由图中可见,温度频繁且急剧的变化,对PCB内部结构造成了实际的影响,也影响到后续PCB中各组分的实际回收情况。当PCB经过298/77 K循环处理和离心分选之后,其PCB金属粉末中实际出铜量,相比其余五种模式,均实现了不同幅度的增长,尤其是相比于298 K常温处理模式和77 K超低温处理模式,分别同比增长了31.59%和3.81%,达到了较为理想的铜组分回收效果 [20] [21] 。另,根据SEM表征结果和结合现有理论,分析其回收率提升的主要原因在于,第一,PCB在经过298/77 K循环处理和离心分选之后,其金属粉末的实际产出量增高;第二,PCB在经过液氮浸泡15天和298/77 K循环处理之后,由于其内部结构中所存在的大量微裂纹,因此对磁选过程起到了一定的帮助作用,更加利于后续回收 [22] 。
针对PCB中铜组分的资源化处理,考虑到当下市场的实际需求,即市场对单质铜的需求较高,因此在结合市场实际需求和保证实验的严谨性的前提下,引入ICP电感耦合等离子体发射光谱仪,对经磁选后所获得的铜组分进行分析,如图8所示。
由图中可见,经过初次扫选(粗选)和二次扫选(磁选)后所获得的铜组分,考虑到误差范围的影响,其基本符合单质铜的相关标准,能满足单质铜的实际市场使用需求,因此实现了对于PCB金属粉末中铜组分的回收和资源化处理 [23] [24] [25] 。
4. 结论
从各项指标变化来看,PCB内部结构受温度影响较大,且力学性能改变较为明显,而在PCB金属组分回收过程中,使用离心分选且筛孔尺寸越小,所得金属组分产出量也越高,同时,在引入初次扫选(粗选)和二次扫选(磁选)回收铜组分时,也有不错的效果。但该处理模式在许多方面仍有不足之处。例如,若在77 K的基础上继续突破最低温度,或可进一步提升实际效果;除此之外,该处理模式的研究仍处于实验室阶段,对于推向于市场仍需进一步的确定。
NOTES
*第一作者。
#共同通讯作者。