1. 引言
Al-Mg合金中厚板具有中等强度、低密度、抗腐蚀等特性,被广泛应用于海洋船舶、油罐车、运煤敞车等交通装备领域 [1] [2] 。热连轧是制备铝合金中厚板的重要工序,现代Al-Mg合金中厚板热连轧生产中,各工厂希望合理设计热连轧工艺参数,利用铝材热连轧后的卷取余热实现自退火,并控制成品组织性能,省去传统生产流程中的再结晶退火、冷轧、清洗、成品退火等工序,实现降本增效 [3] 。诸多学者结合热连轧工况特征研究了热变形参数对铝合金组织性能的影响。黄星星 [4] 通过盐浴退火试验研究了Al-4.5Mg合金的静态再结晶行为,并构建了静态再结晶动力学模型,借助3003铝合金实际生产中的工艺参数分析了Al-4.5Mg合金热连轧后的静态再结晶特征,为Al-4.5Mg合金热连轧工艺制定提供了依据。史博等 [5] 建立了7085铝合金流变应力本构方程,并对7085铝合金多道次热轧过程进行仿真分析与试验验证,指导了7085铝合金工艺参数优化。陈振华等 [6] 根据应力随应变、变形温度和应变速率变化的数据及有限元仿真,对6082铝合金的4机架热连轧规程进行优化,对实际生产具有指导作业。可见,研究热连轧工艺参数对铝合金组织性能调控具有重要意义。本文以某1 + 4热连轧生产线制备5 mm厚Al-4.8Mg合金中厚板为背景,研究不同热终轧工艺参数对Al-4.8Mg合金组织性能的影响,为热连轧工艺参数的设计提供参考。
2. 实验方法
实验材料为5组5 mm厚Al-4.8Mg合金中厚板,中厚板制备工序为:将厚度为620 mm的铸锭进行420℃/2 h + 500℃/12 h均匀化处理后热粗轧至23 mm,然后经4连轧机组热精轧至5 mm厚。5组试样的材料成分、均匀化工艺、热粗轧工艺一致,热精轧压下率一致,但热精轧采用不同轧制温度与速度,其中热精轧最后道次轧制温度与速度如表1所示,即结合工业生产实际情况按照低温低速、中温中速、高温高速的思路设置了5组不同的热终轧工艺参数。
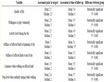
Table 1. Five different hot finish rolling processes
表1. 5组不同的热终轧工艺
对所制备的5组试样进行力学性能、成形性能、抗晶间腐蚀性能测试,并对中厚板纵截面的金相组织、扫描组织、透射组织进行检测。力学性能按照GB/T 228.1-2010 (金属材料拉伸试验–第1部分:室温试验方法) [7] 标准在DDL100电子万能材料试验机上进行。成形性能参照GB/T 232-2010 (金属材料弯曲试验方法) [8] 标准在BHT 3165弯曲试验机上进行弯曲性能测试。抗晶间腐蚀试验参照GB/T 26491-2011 (5xxx系铝合金晶间腐蚀试验方法–质量损失法) [9] 标准执行。在型号为AXIO Scope A1的金相显微镜观察试样的金相组织。采用ZEISS MA10型场发射扫描电子显微镜检测试样断口形貌及第二相特征,并利用Oxford EDS型能谱仪对第二相颗粒进行能谱分析。采用FEI Tecnai G2 20型透射电子显微镜(Transmission Electron Microscope, TEM)观察试样透射组织。
3. 实验结果与分析
3.1. 材料性能
1) 力学性能
表2为试样室温拉伸力学性能测试结果,在终轧温度为250℃时,材料平均抗拉强度、屈服强度分别为337.3 MPa、243.7 MPa,延伸率为17.7%,随着终轧温度的提升,材料强度下降,延伸率提高。当终轧温度由250℃提高到350℃时,平均抗拉强度为300.8 Mpa,屈服强度为141.4 MPa,延伸率为26.5%,平均抗拉强度降低了11.1%,屈服强度降低了41.9%。
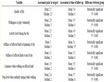
Table 2. Mechanical properties at room temperature of Al-4.8Mg alloy
表2. Al-4.8Mg合金室温拉伸力学性能
2) 成形性能
选用弯曲半径2.5 mm的模具对板材进行弯曲,如图1所示,终轧温度为250℃所制备的板材弯曲至108˚时产生了裂纹,终轧温度为280℃所制备的板材弯曲至132˚时产生了裂纹,当终轧温度达到300℃及以上时,弯曲至180˚未产生裂纹,但板材弯曲180˚后变形纹较为严重,而终轧温度320℃、350℃所制备的板材试样弯曲后表面依旧光滑细腻,表现出更优的成形能力。
3) 抗晶间腐蚀性能
试样的晶间腐蚀速率如表3所示,由表可知,随着终轧温度的提升,材料晶间腐蚀速率明显下降,当终轧温度为250℃时,晶间腐蚀速率最大为11.29 mg/cm2,当终轧温度提高到350℃时,其值下降至3.86 mg/cm2。工业上,船板用Al-Mg合金对腐蚀性能的要求相对最高,要求晶间腐蚀速率 ≤ 15 mg/cm2,显然,5种工艺制备的材料均达到船用版的性能要求,说明5种工艺所制备的材料耐晶间腐蚀性能较好。
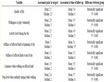
Table 3. Intergranular corrosion rate of Al-4.8Mg alloy
表3. Al-4.8Mg合金晶间腐蚀速率
3.2. Al-4.8Mg合金微观组织
1) 金相组织
图2为5种试样纵截面的金相组织照片,由图可知,热终轧工艺参数对材料自退火行为影响显著,随着终轧温度的提高,金相组织逐步由纤维状演变为等轴状。如图2(a)所示,当终轧温度为250℃时,材料纵截面晶粒组织明显沿变形方向拉长呈纤维组织,说明终轧温度为250℃时,卷取余热不足以驱动试样发生静态再结晶。随着终轧温度的提高,纤维组织含量减少,当终轧温度提高至320℃时,如图2(d)所示,纤维组织已基本转变为再结晶组织,仅在试样中心部位能发现纤维组织痕迹。当变形温度进一步升至350℃时,静态再结晶更加充分,晶粒已全部转化为等轴晶粒。
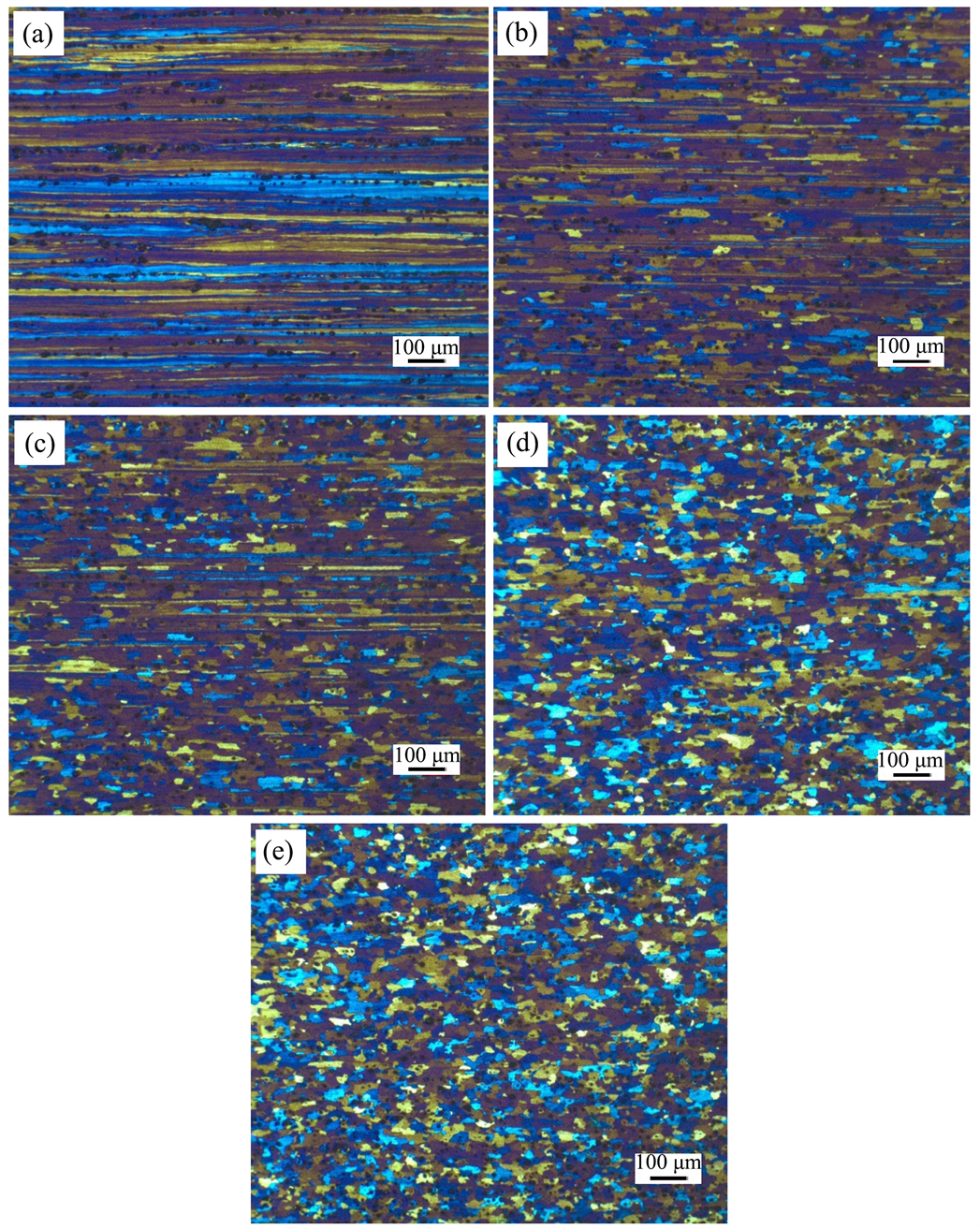
Figure 2. Metallographic of Al-4.8Mg alloy under different process. (a) Process A; (b) Process B; (c) Process C; (d) Process D; (e) Process E
图2. 不同工艺下的Al-4.8Mg合金金相照片。(a) 工艺A;(b) 工艺B;(c) 工艺C;(d) 工艺D;(e) 工艺E
Al-4.8Mg合金在高温高速轧制条件下,内部更容易积累能量,形成动态再结晶,此外,材料轧制完成瞬间能形成更多的高能不稳定亚晶组织,有利于轧制后亚晶快速吸收能量发生静态再结晶晶粒 [2] 。当轧制温度与轧制速度低至一定程度时,材料在轧制过程所累积的能量通过动态回复释放,轧制完成后所处环境温度较低,材料所吸收的能量对静态再结晶的驱动作用有限 [2] 。因此,终轧温度为250℃的样品未发生再结晶,变形出最大的抗拉强度,随着终轧温度提升,材料静态再结晶程度提升,力学强度下降。同时,细小再结晶晶粒可提高材料的变形协调性,使得图1中试样E表现出更佳的弯曲成形性能。
2) 扫描组织
图3为5种试样沿纵截面的扫描电镜组织照片。照片中均分布着大量不规则块状或颗粒状的第二相粒子,尺寸约1~8 μm,采用EDS能谱对粗大第二相粒子的微区成分进行了分析,其结果如表4所示,EDS检测结果表明,这些粒子主要为Al(FeMnCr)Si相,说明铸锭多道次热轧后铸锭中的Al(FeMnCr)Si粒子被轧制破碎,并沿轧制方向分布。从扫描电镜组织可以看出,5种试样第二相粒子的尺寸、分布及成分没有明显的差别。这是因为本章所制备的材料其合金配料、熔铸工艺相同,均匀化温度低于Al(FeMnCr)Si粒子的溶解温度 [10] [11] ,均匀化过程难以将铸锭中的Al(FeMnCr)Si粒子回溶到铝基体中,使得铸锭轧制前保留了相同的第二相特征。热轧过程中经多次高温往返轧制,Al(FeMnCr)Si粒子逐渐沿轧制方向破碎,但试样总轧制变形量一致,虽然热终轧工艺不一致,但热变形温度均低于Al(FeMnCr)Si相的回溶温度,因此,5种试样的第二相粒子整体特征基本一致。
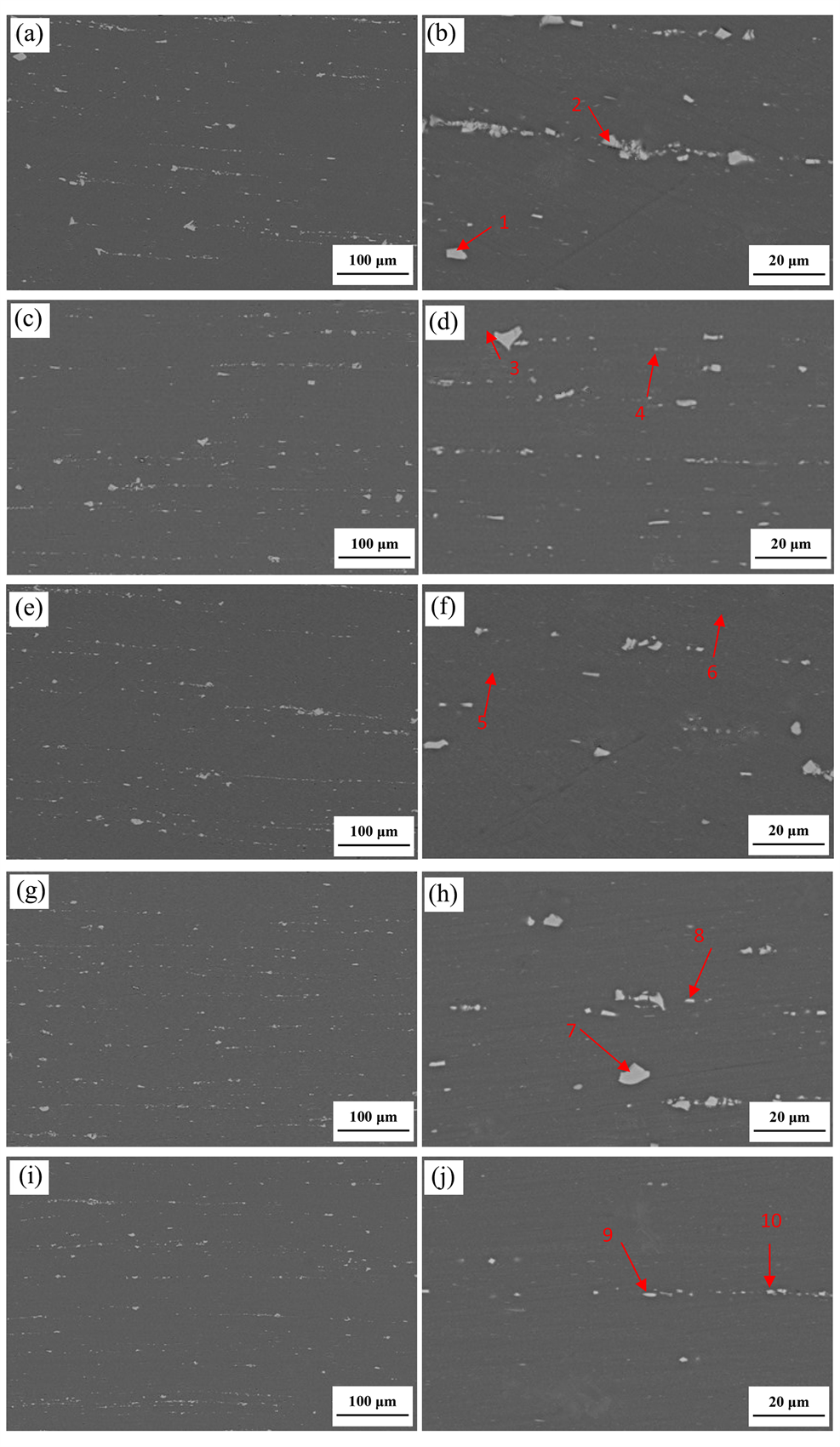
Figure 3. SEM images of Al-4.8Mg alloy under different process. (a) and (b) Process A; (c) and (d) Process B; (e) and (f) Process C; (g) and (h) Process D; (i) and (j) Process E
图3. 不同工艺下的Al-4.8Mg合金SEM形貌。(a)和(b) 工艺A;(c)和(d) 工艺B;(e)和(f) 工艺C;(g)和(h) 工艺D;(i)和(j) 工艺E
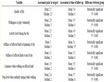
Table 4. EDS analysis results of the second phase of Al-4.8Mg alloy
表4. Al-4.8Mg合金第二相EDS能谱分析结果
3) 透射组织
图4为试样的TEM照片。如图4(a)所示,当终轧温度为250℃时,照片中分布着大量位错及位错胞状组织,提高终轧温度后位错逐渐减少。当温度提至320℃时,如图4(e)所示,晶界非常清晰,位错胞状结构基本消除,仅在晶内存在少量位错。Al-Mg合金热轧过程中,位错随着应变增大快速形成的同时,也随着变形能的积累不断转化为亚晶组织和再结晶晶粒,热轧结束后,在卷取余热的自退火作用下位错和位错胞状结构进一步消除。因此,图4(d)与图4(e)中的位错胞状结构基本消失。
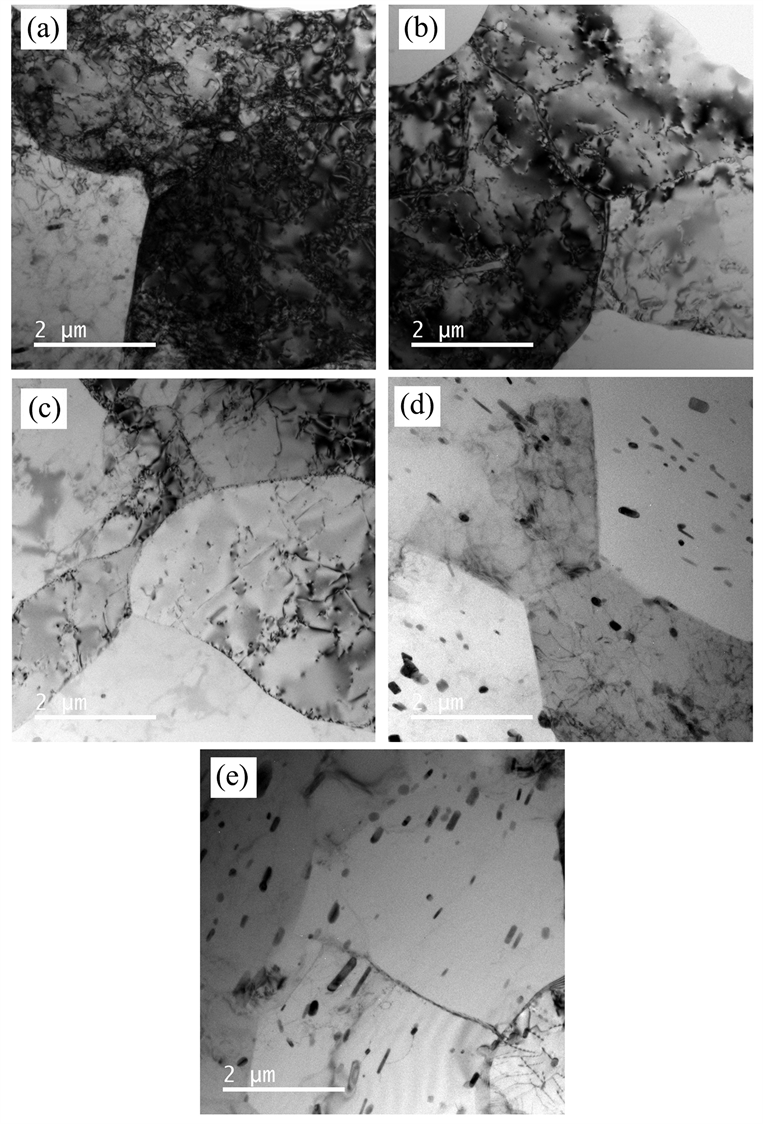
Figure 4. TEM images of Al-4.8Mg alloy under different process. (a) Process A; (b) Process B; (c) Process C; (d) Process D; (e) Process E; (f) Process F
图4. 不同工艺下的Al-4.8Mg合金TEM照片。(a) 工艺A;(b) 工艺B;(c) 工艺C;(d) 工艺D;(e) 工艺E;(f) 工艺F
在Al-Mg合金中,Mg元素在基体中的溶解度较大,主要析出相β相(AlMg相)在室温下难以析出 [4] ,因而具有优异的抗腐蚀性能。5组试制材料的化学成分一致,扫描电镜观察到的第二相特征基本一致,可认为化学成分和第二相粒子在腐蚀试验过程中对材料的影响基本相当。由于热连轧工艺不同,2组试样抗腐蚀性能存在一定差异,试样E抗腐蚀性能最优。研究发现 [12] ,铝合金抗腐蚀性能与其位错、亚结构和晶内储能显著相关,位错密度越大、亚结构含量越多,其晶内储能越高,试样在腐蚀环境中更容易腐蚀。由图4可知,试样A晶粒组织中保留了大量亚晶,且其位错密度明显高于试样E,可见试样E晶内储存的能量在静态再结晶过程中释放更充分,而试样A晶内残留了更高的能量,相对更容易被腐蚀。
4. 结论
1) Al-4.8Mg合金在热终轧温度为250℃条件下,材料平均抗拉强度、屈服强度分别为337.3 MPa、243.7 MPa,随着热终轧温度的提升,材料金相组织逐步由纤维状向等轴再结晶晶粒转变,使得材料强度下降、变形协调性提升,当终轧温度为350℃时,材料平均抗拉强度降至300.8 MPa,屈服强度降至141.4 MPa,但表现出更佳的弯曲成形性能。
2) 当Al-4.8Mg合金热终轧温度由250℃提升至350℃时,扫描电镜下观察到的形貌及第二相特征无明显区别,但透射电镜下观察到的位错密度明显下降,说明晶内储能降低,表现出更好的抗腐蚀性能,材料腐蚀速率从11.29 mg/cm2降至3.86 mg/cm2。
基金项目
湖南省科技人才托举工程项目(2022TJ-N19),湖南省重点研发计划项目(2022GK2041)。