1. 引言
力矩线圈作为惯性传感器检测元件的一部分,是惯性传感器的敏感元件,力矩线圈引出线与摆片中心盘引线镀金区的连接是惯性传感器内外电气连接的重要组成环节,其连接可靠性直接影响惯性传感器的工作性能。
力矩线圈装配过程包括线圈骨架内侧涂覆绝缘漆、线圈绕制、引出线整形、绕组表面涂覆绝缘漆等。现有线圈骨架内侧和绕组表面涂覆绝缘漆均采用在10倍显微镜下手工涂覆,存在耗时长效率低的问题。通过设计绕线机辅助工装、引出线整形工装,线圈骨架和绕组表面涂覆绝缘漆工序选用新的涂覆方法等,确定目标为线圈引出线折弯呈弧形,无死折现象,漆包线断裂或引出线根部损伤比例降低一倍;骨架内侧和力矩线圈表面涂覆绝缘漆两个工步工作效率提高一倍 [1] [2] 。
2. 过程分析
力矩线圈引出线根部受力环节主要在线圈引出线整形工序,分析原因如下:
1) 在线圈引出线整形工序在10倍显微镜下采用镊子进行整形,整形弧度小,无法保证一次成功,多次弯折漆包线,引出线根部反复变形造成引出线根部漆皮剥落甚至超出断裂强度,如图1所示。整形完成后用快干胶将引出线始端和末端固定在漆包线端面上,以后工序引出线根部不会受力。
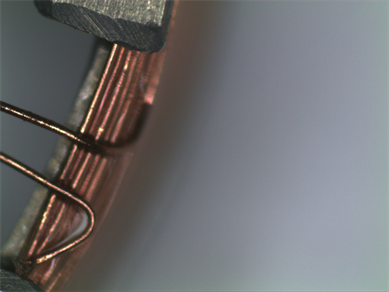
Figure 1. Paint peeling at the root of the coil lead wire
图1. 线圈引出线根部漆皮剥落
2) 骨架内侧和力矩线圈表面均需涂覆绝缘漆,涂漆部分如图2所示,由于涂覆采用细毛刷手工蘸取绝缘漆整圈涂覆,涂胶量依靠操作经验涂覆,手工涂覆工时长、工作效率低。
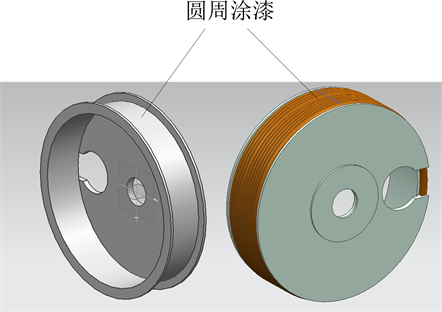
Figure 2. Schematic diagram of coil painting section
图2. 力矩线圈涂漆部分示意图
为提高力矩线圈成品率和浸漆效率可以采用以下方法:
1) 设计整形工装代替原有整形方式,整形一次成功,漆包线折弯过渡平缓,成型一致性好。
2) 采用自动化设备代替手工浸漆,在不划伤绕组漆皮的前提下,自动浸漆方式要保证整个骨架内侧和绕组表面均涂覆绝缘漆,并且绝缘漆不能涂覆到骨架壁上,新的浸漆方式能显著提高浸漆工序的工作效率。
3. 方案确定
1) 整形工装
设计专用整形工装如图3所示,工装可用部分无法倒角,工装成型未经过超细研磨较锋利,有漆包线划伤风险。
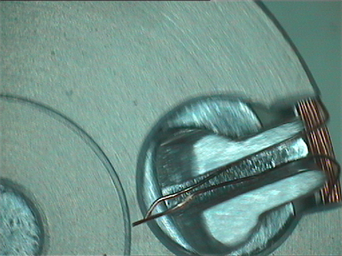
a) 整形工装 b) 线圈放在整形工装上
Figure 3. Shaping tooling
图3. 整形工装
另外需防止与漆包线接触部分工装划伤漆包线,设计时此部分高出线圈骨架,实际加工时无法加工,如图4所示。后工装加工完成使用前,工装开槽部位、与漆包线接触部分均在显微镜下进行去刺,打磨,通过超细研磨的开槽部分表面光滑,使工装在整形过程中不磨损漆包线。
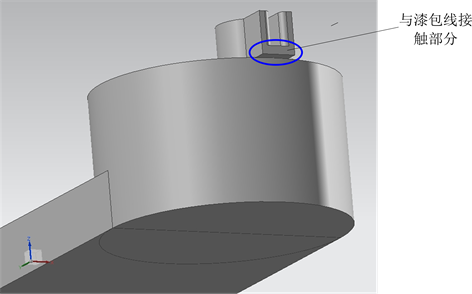
Figure 4. Schematic diagram of the grinding part of the shaping fixture
图4. 整形工装研磨部分示意图
2) 自动涂覆代替手工涂覆
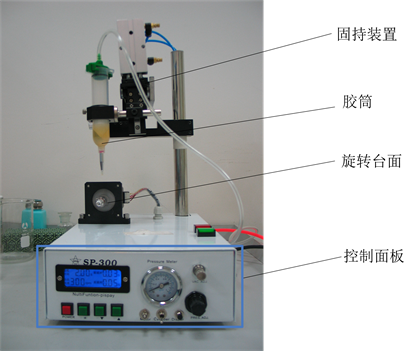
Figure 5. Appearance of rotary painting device
图5. 旋转式涂漆装置外观
本项目采用自动涂覆装置涂覆绝缘漆代替手工涂覆,考虑到绝缘漆的流动性与圆周涂覆,自动涂覆装置采用工件旋转式涂覆,通过调节压缩空气的压强与作用时间来控制点胶量,即改变气压大小和点液时间的长短调节出绝缘漆的体积 [3] [4] 。出液口选用特氟隆材料制作的毛刷,不会划伤骨架和绕组漆包线。调节出漆时间、出漆压力等参数控制出漆量,通过调整毛刷接触面积保证绝缘漆圆周涂覆过程中骨架内侧和绕组漆包线尤其是边缘部分均匀涂覆绝缘漆。旋转式涂漆装置主要包括控制面板、旋转台面、固持装置、胶筒等。控制面板设定步进电机转速、步进电机旋转方向(正转、反转)、一个周期涂漆时间、出漆前延时、出漆后延时、出漆的压力大小等参数。旋转台面用来固定线圈,工作时步进电机带动线圈旋转,电机转速可调。固持装置在压缩气体作用下做往复运动,开始涂漆时向下运动到工作台面的工件处,涂漆结束后向上运动回到最初位置。涂漆机外观如图5所示。
为了使其用于力矩线圈浸漆,对装置进行如下改造:
1) 改变旋转电机位置
旋转台面的步进电机原来在机箱中,可以带动工件在XY平面中360˚旋转,力矩线圈涂漆过程中需要在XZ面中即竖直面中旋转,后对此装置进行改造,将步进电机旋转90˚放置在机箱外面、利用水平仪调平后固定,连接步进电机电源线和信号线,工作正常,可以在XZ平面中的360˚旋转。
2) 设计线圈定位夹具
线圈定位工装决定在涂覆过程中线圈运动轨迹的圆周精度,涂覆完成后线圈要求易于拆卸。在不划伤引出线的前提下,线圈定位方式采用骨架内腔方式对线圈定位,为确保线圈在工装上不发生位置移动,放置好线圈后,用磁铁将线圈固定,涂漆完成后,用胶布粘将线圈粘下,如图6所示。
4. 方案实施
1) 整形工装在实际使用过程中不损伤漆包线,两者引出线整形图片如图7所示。整形工装可以保证整形一次成功,整形形状一致性好,引出线过渡较缓,避免多次弯折漆包线。
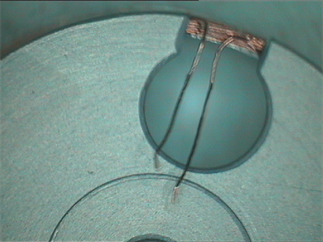
a) 镊子整形形状 b) 整形工装整形形状
Figure 7. Comparison of two shaping methods
图7. 两种整形方式对比
2) 针对使用绝缘漆流平性较好,线圈绕组采用通过精确调控气压控制绝缘漆点大小和用量,自动涂漆装置涂漆过程为:
a) 设定涂漆参数、包括转速、涂漆时间、涂漆压力值等,调整毛刷和力矩线圈的相对位置,保证毛刷接触后整个涂漆面,并且不碰到线圈骨架壁上,同一批次设置一次,后续不需要调整;
b) 线圈放在定位夹具上,用磁铁固定;
c) 启动开关,毛刷从初始位置运动到涂漆位置,在气压作用下均匀流出绝缘漆,一个周期结束,毛刷离开工件回到初始位置,如图8所示;
d) 去掉固定用磁铁,将工件从固定工装上取下。
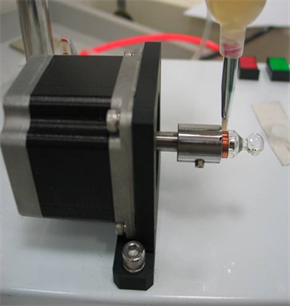
a) 毛刷初始位置 b) 毛刷涂漆位置
Figure 8. Brush position during painting process
图8. 涂漆过程中毛刷位置
绝缘漆作为绕组表面的保护层,增强了绕组的绝缘性能和机械性能,提高了绕组的防潮能力。针对绕组表面绝缘漆涂覆,在不同的参数下进行涂漆试验,用精密电子天平(分辨率0.1 mg)测定浸漆前后浸漆量,对比手工涂覆方式,如表1所示 [5] [6] 。
参数A:转速180 rpm,涂漆时间2 s,出漆压力0.10 MPA;
参数B:转速180 rpm,涂漆时间4 s,出漆压力0.05 MPA;
参数C:转速180 rpm,涂漆时间3 s,出漆压力0.08 MPA;
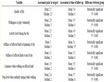
Table 1. Changes in torque coil weight values for different coating methods
表1. 不同涂覆方式力矩线圈重量值变化
从试验结果可得:
a) 手工涂覆方式涂漆量离散性大,自动涂覆方式涂覆量一致性高于手工涂覆;
b) 使用参数B时,在保证绝缘漆不溢出的情况下,涂漆量适当,适用于力矩线圈表面涂覆。
线圈骨架内侧涂覆绝缘漆主要起绝缘作用,绝缘漆漆膜均匀即可,利于后续在骨架上绕制漆包线。经测试,转速为180 rpm,涂漆时间2 s,出漆压力0.05 MPA时绝缘漆膜均匀性较好,与手工涂覆相比,两者涂漆量如表2所示。由表2可得,自动涂覆方式涂覆量一致性高于手工涂覆方式。
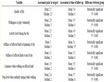
Table 2. Comparison of weight values of coil skeleton coated with insulation paint
表2. 线圈骨架涂覆绝缘漆后重量值对比
5. 效果检查
将1100个力矩线圈装配在摆片上组成摆组件后进行3个温度冲击后在10倍显微镜下观察摆组件上1100个线圈引出线根部,无磨损、漆皮剥落现象,根部损伤比例为0,低于优化前水平 [7] [8] 。
随机抽取10个经历环境考核后的摆组件测定试验前后摆组件阻值变化,如图9所示(试验前后测试均在室温进行):
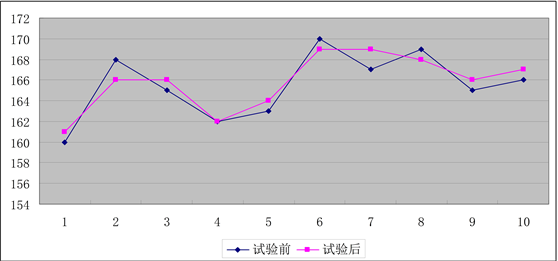
Figure 9. Changes in resistance values before and after the test
图9. 试验前后阻值变化情况
由图9可知,试验前后摆组件阻值变化趋势正常,说明使用整形工装后引出线连接可靠,线圈无断裂情况发生,证明优化方案有效。
在未使用显微镜和在10倍显微镜下观察自动涂漆装置涂覆完成后的工件,绕组空隙填充较好,无气泡,骨架壁上没有绝缘漆,如图10所示,对绕组进行拆解发现绕组边缘漆包线上均挂有绝缘漆。在10倍显微镜下仔细观察已涂覆绝缘漆的骨架表面,骨架表面漆膜为无色透明,漆膜完整,无裂缝,如图11所示。
a) 力矩线圈目视图(左为已涂覆绝缘漆,右为未涂覆绝缘漆)
b) 10倍显微镜下已涂覆绝缘漆的线圈
c) 10倍显微镜下未涂覆绝缘漆的线圈
Figure 10. Coil after coating
图10. 涂覆完成后的线圈
a) 10倍显微镜下已涂覆绝缘漆的骨架
b) 10倍显微镜下未涂覆绝缘漆的骨架
Figure 11. Skeleton before and after coating
图11. 涂覆前后的骨架
6. 结论
适应性改造旋转式精密涂漆装置,设计了线圈定位工装,确定了涂漆参数;力矩线圈引出线折弯呈弧形,无断裂,漆包线断裂或引出线根部损伤比例极大降低 [9] 。
采用自动涂覆装置进行骨架内侧与线圈表面涂漆均为4个/min,与手工涂覆绝缘漆相比(8个/min),效率提高50%,并且大大降低了操作者的劳动强度。