1. 引言
压实是沥青混凝土路面施工的最后一道工序,良好的路面质量最终也要通过压实来体现 [1] 。压实不足会引起沥青路面的早期失效,缩短道路使用寿命 [2] [3] ,此外,路面压实均匀性不佳也是引起大面积裂缝的主要原因 [4] 。研究表明每增加1%的压实度,道路的承载能力相应的提升约10%~15%,因此压实程度对路面质量起着决定性作用。压实从本质上讲就是集料的空间位置重新排列,骨料位置发生迁移、旋转以获取更大密度,研究集料的运动特性以及迁移演化规律能够从细观层次很好地解释压实机理 [5] 。
智能颗粒传感技术与传统检测压实技术有所不同,它是一种集应力、温度、加速度、欧拉角一体的新型传感器。Liu和Huang等人 [6] 最先开发了智能颗粒传感技术并应用于描述铁路道碴颗粒在荷载作用下的运动行为。由于初代智能颗粒尺寸过大,研究人员开始尝试减小颗粒尺寸并逐步应用于研究沥青混合料压实过程中 [7] [8] ,Wang等 [7] 将智能颗粒嵌入试件不同位置以记录旋转压实过程,结果表明中部位置的集料受到更有效的压实。Wang和Shen等 [8] 将智能颗粒和沥青混合料一起接受碾压,通过实时监测沥青混合料内部温度以及加速度变化来控制压实质量。Dan等 [9] 利用智能颗粒监测旋转压实过程,从细观层次揭示了颗粒运动响应与沥青混合料压实程度之间的关系,通过对比分析试样高度变化和颗粒平均应力,采用颗粒垂直应力来反映沥青混合料的压实程度。
离散元法是一种评价非连续介质材料力学的分析方法,近年来利用数值模拟方法仿真沥青混合料试验成为热点。离散元模型可以较好地模拟沥青混合料的级配以及空隙分布,研究人员通过建立二维模型来模拟沥青混合料颗粒运动规律 [10] ,以此来揭示压实机理。为了更好地分析颗粒力学特征以及迁移规律,学者们采用三维数字化建模技术 [11] 以及三维扫描技术 [12] 来生成与真实集料相似的不规则颗粒表征虚拟骨料,获得了更为精确的沥青混合料颗粒运动特征。
在压实试验中放置合适数量的智能颗粒,可以直观地反映颗粒运动姿态变化,但这项工作会受设备测试成本较高的限制。同时沥青混合料试验本身具备离散特性,由于每次试验无法保证选用同一数量、形状以及粒径的集料,试验结果会存在一定误差。此外,大部分虚拟试验得到的颗粒迁移演化规律无法在室内试验中得到有效论证。
本文将智能颗粒(SmartRock)与离散元仿真模拟有机结合,在沥青混合料内部放置智能颗粒,实时监测粗集料的三向加速度以及欧拉角。同时,利用离散元软件对压实过程进行有效模拟,并探究粗集料的迁移规律。对比分析智能颗粒监测数据以及模拟结果,从颗粒细观运动响应层面解释沥青混合料在压实过程中粗集料的迁移演化规律。
2. 基于智能颗粒的压实试验
2.1. 智能颗粒
智能颗粒(SmartRock)由耐高温和高强度材料3D打印而成,尺寸为23 mm × 23 mm × 23 mm。其具有与真实集料相近的接触刚度、惯性矩和等效重度,与沥青的粘附性达到5级,并且智能颗粒与沥青混合料具有良好的变形协调性,在外力作用下会发生类似于粗集料颗粒的运动。智能颗粒大小与粒径范围为19~26.5 mm的集料相符,因此在本试验中智能颗粒为混合料级配的组成部分。智能颗粒内部装有加速仪、陀螺仪、指南针磁场传感器、压力传感器等电子设备并无线传输到云端储存。
为表征颗粒在运动过程中的姿态变化,智能颗粒采用两个不同的坐标系,即全局坐标系(XYZ)和局部坐标系(xyz),如图1所示。欧拉角可以用来确定定点转动刚体位置的3个一组独立角参量,这三个角分别是俯仰(Pitch),偏摆(Yaw),翻滚(Roll),Pitch表示绕X轴旋转的角度,Yaw表示绕Y轴旋转的角度,Roll表示绕Z轴旋转的角度。
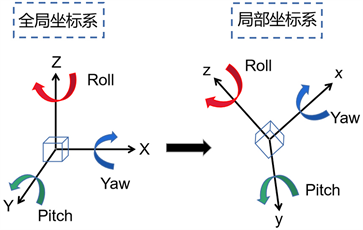
Figure 1. Euler angle characterization of the particle attitude
图1. 欧拉角表征的颗粒姿态
2.2. 试验材料
试验沥青所用70#基质沥青,其相关技术指标见表1;集料为产自浙江省兰溪市的石灰岩,细长扁平颗粒含量满足要求,集料压碎值为21.4%,洛杉矶磨耗损失为19.6%;矿粉由石灰岩粉磨加工而成,表观相对密度为2.682。
考虑到智能颗粒尺寸因素,本试验选用AC-25型粗粒式矿料级配,其矿料合成级配如表2所示。
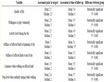
Table 1. Performance index of 70# base asphalt
表1. 70#基质沥青性能指标
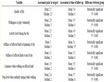
Table 2. AC-25 mineral aggregate gradation
表2. AC-25矿料级配
2.3. 压实试件的制备
沥青混合料的拌合温度设置为160℃,拌合及装料过程参考《公路工程沥青及沥青混合料试验规程》(JTGE20-2011)进行。在装料过程中,将智能颗粒埋置于试样中部位置。本次试验采用TSY-1000A型压力机,压实温度为150℃,压力机预加载0.1 MPa,确保压头和沥青混合料之间充分接触,以0.25 MPa/s的速度均匀加载至55 MPa,成型样品的直径为150 mm,具体如图2所示。
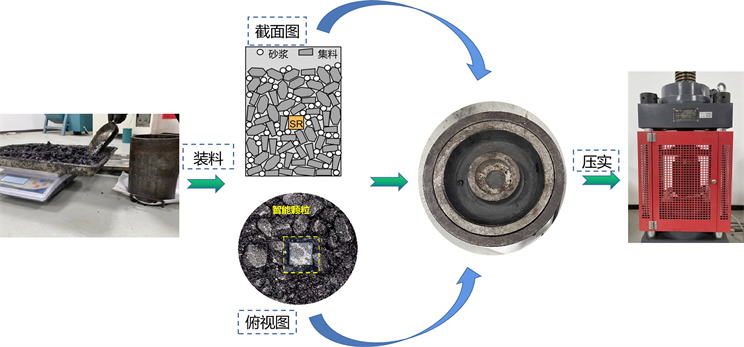
Figure 2. Compaction process of asphalt mixture
图2. 沥青混合料压实过程
在本研究中,将当前空隙率与最终空隙率的比值来表征试件的压实程度,试件的体积一旦确定,通过公式(1)和(2)可以计算得到试件的空隙率 [13] 。
(1)
(2)
式中,
为试件当前的体积比重;W为试件的重量(g);V为试件当前的体积(cm3);γw为水在21℃时的密度(1.0 g∙cm−3);AVcur为试件当前的空隙率;AVfinal为试件压实后的空隙率;
为试件压实后的比重。
2.4. 含智能颗粒的沥青混合料性能评估
参照上述流程制备A、B两组沥青混合料试件,每组有三个平行试件,其中A组试件为普通试件,B组试件为含智能颗粒的试件,采用MTS万能材料试验机对两组试件进行单轴压缩试验,试验温度为20℃,加载速率为2 mm/min,最终测得的抗压回弹模量和抗压强度如表3所示。
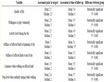
Table 3. Comparison of uniaxial compression test results of asphalt mixture
表3. 沥青混合料单轴压缩试验结果对比
含智能颗粒的沥青混合料与普通沥青混合料的测试结果差异较小,说明在压实过程中智能颗粒未对试件结构造成明显影响。
3. 压实试验的离散元模拟
3.1. 沥青混合料离散元模型建立
(a) 重力平衡后的堆积态
(b) 切割后的未压缩状态
Figure 3. Virtual model of asphalt mixture
图3. 沥青混合料虚拟模型
沥青混合料是一种由集料、沥青砂浆(粒径在2.36 mm以下的细集料与沥青胶结料形成的混合物)和空隙构成的三相混合物。由于计算效率的限制,离散元模型不可能模拟所有粒径的集料,故本文将粒径2.36 mm以下的集料和矿粉一起集成到沥青砂浆中考虑,用圆球颗粒简化模拟沥青砂浆。沥青混合料的集料通常为不规则形状,模型中生成clump来模拟集料的不规则特性。通过编制一定算法输入骨料级配数据,生成与真实沥青混合料试件相似级配的骨料和沥青砂浆,同时在模型中生成尺寸与智能颗粒相同的方形clump,视作粒径范围为19~26.5 mm的集料,详细说明见1.1。最终重力堆积形成松散试样的高度略高于实际试件高度,将试样模型进行切割,如图3所示。
3.2. 材料细观力学特性
本文选用线性刚度模型模拟集料间的接触行为,选用Burgers模型模拟砂浆颗粒间和集料与砂浆之间的接触力学行为。试验采用的集料为石灰岩,参考Wang的研究成果 [14] ,集料的弹性模量取为39.3 Gpa,泊松比取值为0.23,集料的接触刚度可由式(3)和式(4)计算得到,如表4所示。
(3)
(4)
式中,kn,ks分别为法向接触刚度和切向接触刚度;E为集料的宏观弹性模量;r为颗粒单元的半径;μ为集料的泊松比。
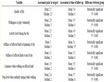
Table 4. Meso-parameters of aggregate contact model
表4. 集料接触模型细观参数
参考文献 [15] 所求得的Burgers模型在150℃时的宏观参数,通过宏观参数与微观参数的转换关系,本文最终所采用的Burgers模型细观参数如表5所示。
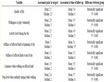
Table 5. Meso-parameters of Burgers model
表5. Burgers模型细观参数
3.3. 边界条件及压实过程模拟
根据已建立的沥青混合料离散元模型,生成方形骨料,1和2号、3和4号、5和6号分三组压实,每次压实的加载方式保持一致,每组颗粒的位置如图4所示。为模拟压实试验加载条件,顶部wall作为加载板,底部wall作为固定板,圆柱状wall作为试件模具,约束试件的侧向位移。虚拟试验的加载方式与真实试验相同,顶板施加竖直向下的作用力,以0.25 MPa/s的速度均匀加载至55 MPa。
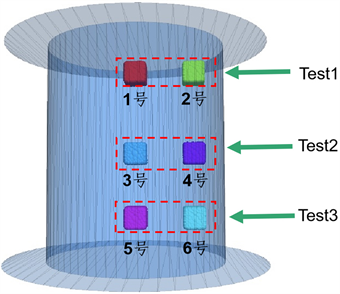
Figure 4. Schematic diagram of square particle position
图4. 方形颗粒位置示意图
3.4. 模型可靠性验证
记录室内压实过程中试样随压力变化的压实程度,与离散元模拟结果进行比较,如图5所示。当压实力大于25 MPa时,试件的空隙率开始缓慢下降,当压实力超过40 MPa后,试样的空隙率变化不明显。R2为93.27%,表明模型能够有效模拟沥青混合料的压实过程。
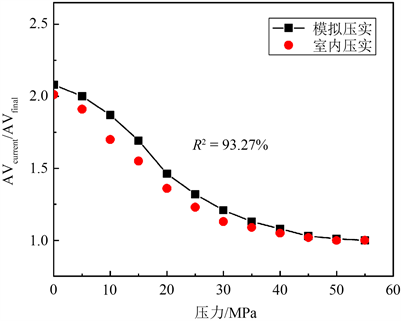
Figure 5. Comparison of compaction degree between indoor compaction and virtual compaction
图5. 室内压实与虚拟压实的压实程度对比
4. 粗集料的迁移演化规律分析
4.1. 智能颗粒监测结果分析
沥青混合料的压实过程是在外荷载的作用下,混合料从松散、塑性状态逐渐演变成具有高强度、粘聚状态的一种过程,从本质上讲就是粗集料的空间位置发生重新排列。通过智能颗粒传感器监测的欧拉角和加速度数据来表征粗集料的运动状态,并根据粗集料运动特征的不同将压实过程分为初始、波动和平稳三个时期。在压实过程中智能颗粒记录的欧拉角时程曲线如图6所示,压实过程中每个阶段的欧拉角极差用β表示。
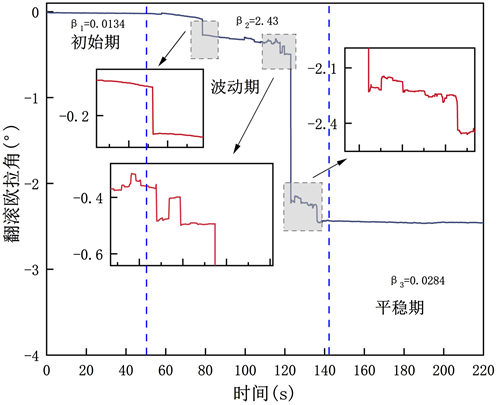
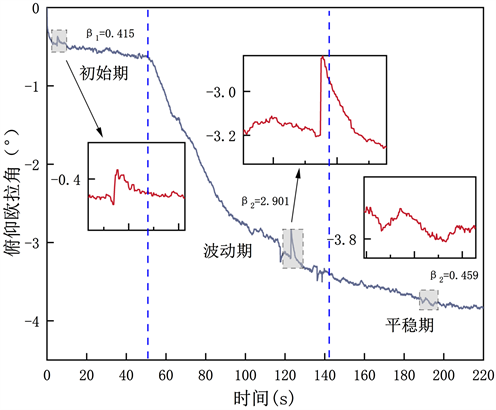
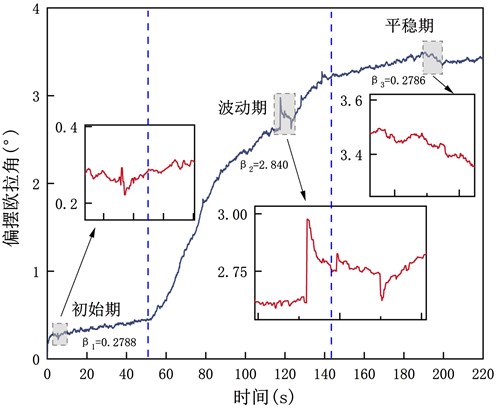
Figure 6. Euler angle time-history curve
图6. 欧拉角时程曲线
颗粒欧拉角的转动程度与压实阶段具有相关性,在波动期颗粒的姿态变化较为显著,而初始期和平稳期无明显转动。偏摆角与俯仰角在变化趋势上较为相似,都以一定幅度缓慢转动,而翻滚角则以突变为主,在波动期的70 s~140 s发生了多次突然转动,在其他时期并无明显变化。沥青混合料在压实初始时期,主要以顶部微小压实为主,竖向压力在传递过程中发生了损耗,位于中部的智能颗粒在水平方向未发生明显转动,在垂直方向上的偏摆角和俯仰角变化较小,且变化程度相当。随着竖向压力的增大,智能颗粒的转角幅度逐渐增大,可以发现垂直方向发生明显转动,在这一时期发生了约为3˚的垂直滚动。水平方向的转动角度在120 s时发生了一次明显突变,转动幅度为2.3˚,并且此时颗粒在垂直方向也相应产生小幅度滚动。
(a) 0 s
(b) 100 s
(c) 200 s
Figure 7. Schematic diagram of relative posture of particles
图7. 颗粒相对姿态示意图
在压实后期,随着试样压实位移的增大,粗集料之间相互嵌挤,使得集料不容易发生滑移,智能颗粒转角相对平稳,颗粒在垂直方向仅在180~190 s之间有一次小幅度的波动,水平方向无明显转动。190 s之后颗粒的欧拉角在三个方向上不再发生明显波动,说明此时试样的中部位置已相对密实。观察图7的颗粒姿态示意图,可以发现颗粒在压实过程中主要以竖直方向的滚动为主,颗粒的水平转动仅在波动期的后半程较为明显,说明这一时期颗粒以水平方向的空隙填充为主。
图8为智能颗粒在压实过程中的加速度变化数据,在压实初始时期,在竖向压力作用下,颗粒主要发生竖向运动。颗粒的Z向加速度明显大于X向与Y向加速度,加速度在X向和Y向的峰值分别为0.2 g和0.25 g,而垂直方向上的加速度峰值为0.38 g。随着试样密实程度的增大,Z向加速度迅速增大,加速度峰值为0.48 g,水平方向的加速度较竖向加速度变化较小,在波动期X向和Y向加速度峰值分别为0.24 g和0.36 g,三向加速度在这一时期呈现出先增大后减小的变化趋势。在压实后期,试样逐渐密实,压实相同的高度需要更大的压力,三向加速度的幅值逐渐减小,颗粒运动开始变得平和、缓慢。
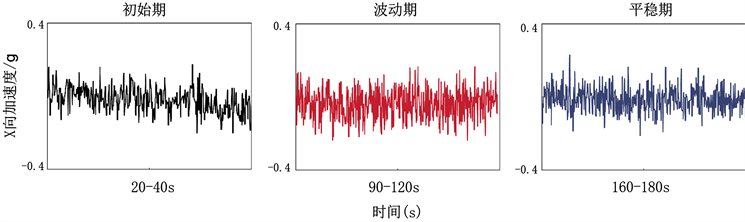
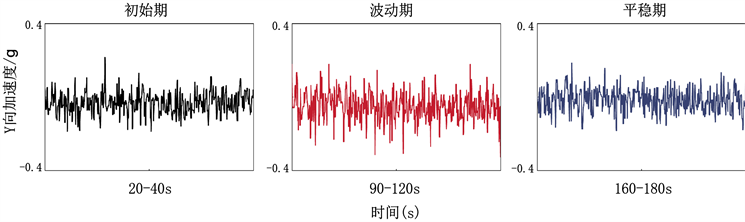
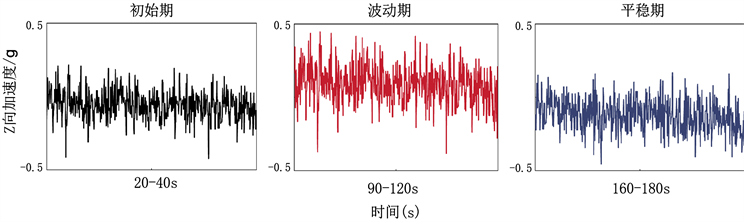
Figure 8. Acceleration time-history curve
图8. 加速度时程曲线图
4.2. 离散元仿真结果分析
分析压实过程中颗粒的空间位置、平动速度、相对姿态等指标来探究集料的迁移演化规律,颗粒的运动情况如图9所示。起始点是指颗粒在未压实前的空间位置,结束点是指加载至指定压力时颗粒的空间位置,并标明了颗粒在压实过程中的最大速度,需要注意的是颗粒的运动速度是一个瞬间的概念,并非在整个压实过程中都保持这个速度。蓝点代表颗粒在压实过程中投影至ZY平面的位移轨迹,绿点代表颗粒在压实过程中投影至XZ平面的位移轨迹,红点代表颗粒在压实过程中投影至XY平面的位移轨迹。
颗粒在不同阶段表现出的转动方式有所差异,但同一阶段不同位置处颗粒的转动模式却呈现出一定的相似性。在压实的初期,由于此时竖向荷载较小,颗粒以微小转动为主,所有颗粒的姿态变化并不明显。随着竖向压力的增大,松散试样迅速被压缩,颗粒主要发生竖直方向的滚动,位于试件顶部以及中部位置的1号、2号、3号和4号颗粒在竖直面内的滚动尤为明显,并且位于同一埋深处的3号和4号颗粒滚动模式相似程度较高。随着试样高度的下降,颗粒在竖向方向上相互嵌挤,约束了颗粒在竖直方向的转动能力,通过观察颗粒的姿态变化可以发现,颗粒主要以水平方向的转动和迁移为主,说明此时颗粒运动以水平方向的空隙填充为主,这与智能颗粒监测的运动变化较为相似。在压实后期,位于中部位置的3号、4号颗粒在水平面内的转向相反,并且3号颗粒的转向幅度明显小于4号颗粒,说明此时4号颗粒所处的边缘位置处并未压实,而3号颗粒的中部位置处已相对密实。位于底部的颗粒在整个压实过程中发生的旋转幅度较小,运动特征不明显,因此位于试样中上部的颗粒可较好地评判压实程度。
通过观察颗粒迁移轨迹在各个平面上的投影散点可知,颗粒位移主要发生在压实的前中期。由于竖向荷载在向下传递过程中发生能量的损耗,上部位置处的颗粒运动迫使下部颗粒相应的发生运动,因此远离荷载位置的颗粒运动显得平缓。颗粒竖向迁移比例及侧向迁移量如图9所示,其中侧向迁移量是指X向和Y向的合成迁移量。位于顶部中间位置的1号颗粒在所有颗粒中垂直位移最大,在垂直方向的位移超过了32.8 mm,占试样压实位移的60.8%。位于顶部边缘位置处的2号颗粒可能受到边界效应的影响,在竖向荷载作用下较1号颗粒更容易发生侧向迁移。观察第二次以及第三次压实,同样也发现了相似的迁移趋势,即位于边缘处的4号、6号颗粒发生的垂直位移小于3号、5号颗粒,而侧向位移大于3号、5号颗粒,其中位于底部边缘处的6号颗粒在水平方向上位移了4.85 mm。此外,结合图10中颗粒的姿态示意图,可以发现顶部位置的颗粒在压实过程中倾向于发生竖直面的滚动以及向下迁移,而底部位置的颗粒倾向于发生水平方向的堆移以及转动。
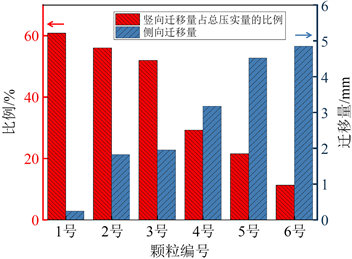
Figure 10. Vertical migration ratio and lateral migration amount of particles
图10. 颗粒竖向迁移比例及侧向迁移量
4.3. 粗集料迁移行为对压实度的影响
为分析粗集料迁移方式对压实度的影响以及减小边界效应的影响,生成一个直径为300 mm的大尺寸试件,不改变试件高度,并在水平方向排布测量球以计算空隙率,测量球的存在不会对颗粒移动产生任何影响。为保证计算结果的准确性,测量球的直径应大于材料最大公称粒径的2倍,直径选为60 mm。如图11所示,依据试件最终压缩高度,将试样分为上中下三层,在试样的上下两层分布测量球。
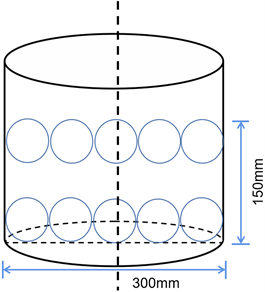
Figure 11. Schematic diagram of measuring ball arrangement
图11. 测量球布置示意图
以AC-25混合料为例,将试件高度压缩至150 mm,最终压实状态下空隙率的模拟分布结果如表6所示。上下层集料由于迁移方式的不同,空隙率分布也有所差异,上层空隙率均值为14.95%,下层空隙率均值为16.49%。由前文分析可得,上层集料在压实过程中主要发生竖直方向的迁移以及滚动,在水平方向上的堆移较小,导致上层位置的细集料相对处于一个有限的水平区域内进行迁移,部分空隙无法被填充,致使试样上层空隙分布不均匀,压实均匀性较差,空隙率极差达2.05%。位于下层的集料易受到底部约束的作用,向下迁移的同时向两侧发生偏移,集料的水平迁移能力较强,下层的压实均匀性较好,空隙率极差为0.95%,但整体压实度低于上层。
5. 结论
本研究旨在分析沥青混合料中粗集料在压实过程中的迁移演化规律。基于智能颗粒对沥青混合料进行压密行为表征,并建立相应的离散元模型加以分析,得到以下主要结论:
1) 沥青混合料中埋设智能颗粒对试件级配以及性能影响较小,且智能颗粒监测的加速度和欧拉角响应数据可以作为评价沥青混合料压实状态的关键指标。相较于压实后期,集料在前中期的运动响应尤为强烈,说明在实际施工时一定要注重初压环节,使沥青混合料尽快处于稳定状态,在外力作用下不会发生推移。
2) 同一试件不同区域的集料运动规律有所差异,且集料的迁移行为会对沥青混合料压实度和压实均匀性造成影响,试件上层和下层的平均空隙率相差1.54%,因此在压实过程中应根据道路分层选择合适的施工方式。