1. 引言
随着纺织机械的不断发展,作为编织行业的重要设备并丝机的需求量日益增大,人们对并丝机性能的研究也日益重视 [1] 。对于并丝机而言,评价其性能的关键在于丝线的缠绕排列的质量,运动学理论运用到并丝机部件对并丝机性能及效果的研究有重要意义 [2] [3] 。运用运动学分析方式主要分析丝线在并丝机排线架往返过程当中丝线在不同速度,不同运动阶段以及线轴不同层数上的排列分布情况,由于丝线运动过程中其受力时刻在发生变化,选择将不同过程微元化,分析其在极短时间内的运动 [4] 。为了评价丝线实际分布排列情况,利用深度学习和图像识别,可以对丝线在排列过程中的堆叠交叉瑕疵进行检测,从而评估并丝机实际性能及并丝效果,针对该研究情况,通过高速相机结合理论分析实现了丝线不同阶段运动分析得出相关结论,且基于深度学习的检测平台完成了对丝线实际运动瑕疵数的定性检测。
2. 排线架与丝线运动研究
并丝机工作的主要部件为排线部件,排线部件由排线架和主轴共同构成,主轴的转动与排线架的往复运动配合,从而实现丝线有序的排列在主轴,排线部件也是并丝机性能评价的关键。
如图1在本文并丝机排线部件中,导向轮位置固定,主轴由伺服电机驱动自转,排线架由伺服电机驱动完成左右的不断往复,两者配合实现并丝。
1、空线轴;2、排线架;3、丝线;4、导向轮
Figure 1. Schematic diagram of wiring components
图1. 排线部件简图
排线架与丝线运动理论
在并丝过程中,排线架在伺服电机的作用下在空线轴的行程内做往复运动,将丝线有序排列。由于电机运动特性,其正反转一定伴随着加减速,排线架在线轴两端正反转时,在极短的时间内由于速度发生变化,与其他运动过程相比排线架会造成丝线在两端的堆叠,图2所示整体上看分为两个过程边缘加减速段与中间匀速段。
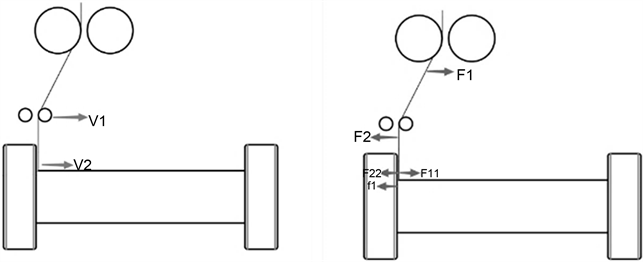
Figure 2. Diagram of the movement of the wire rack and silk wire
图2. 排线架与丝线运动示意图
丝线在线轴上的实际运动,与排线架的理想运动有着明显不同,把排线架的运动视作丝线运动的理想情况则丝线实际运动受多种因素影响。
本文对丝线的实际研究过程从丝线在空线轴左端反向开始向右运动起到丝线下一次运动反向前止,在第一,三层丝线上运动,且分别在主轴电机1000转和1500转速度下进行。如图3所示丝线绕线处受力为着力点力的分力,整个过程按照其受力与运动分为三个过程。第一过程丝线刚刚反向速度从0开始加速达到一个值该过程张力F11最大,阻力f1和张力F22较小,整个过程加速,第二过程第一阶段主要是由于丝线第一过程在堆叠处运动,进入第二过程时其所受阻力突变,使其进行减速,随后阻力f2突变结束恢复正常,此时张力F11最大,在丝线张力F11,F22与阻力f共同作用下再进行一个加速过程。第二过程第二阶段张力F11,F22及阻力f3三者达到了达到相对平衡运动同样达到一个相对平衡的状态,丝线速度在一个速度上下波动,当丝线运动到竖直状态时第二过程结束。第三过程区别于前两个过程的点在于丝线越过竖直位置前,排线架只对丝线有一个支持力,没有主驱动力,但该过程中丝线除受到张力和摩擦阻力外还受到排线架的推力F3,且由于所以在该过程丝线会进行加速后再达到相对平衡。同时在不同层数下运动受到的摩擦阻力不同,不同速度下运动,排线架运动速度不同,导致张力增加或者释放的速度不同,在丝线运动过程中受到的各个力始终处在变化之中,在三个运动过程中均选择极短时间段,该过程可以近似将变加速度视作恒定加速度进而通做定性分析,故而从以上角度确定研究重点。
3. 实验分析
3.1. 实验设备
如图4所示,实验基于一台并丝机设备,选择的丝线直径为0.2 mm,与线轴转速为1000和1500 r/min,丝线在线轴丝线的第一和三层上运动,整个运动过程通过高速摄像机进行拍摄。
(a) 第一过程 (b) 第二过程第一阶段
(c) 第二过程第二阶段 (d) 第三过程
Figure 3. Actual motion diagram of silk thread
图3. 丝线实际运动受力图
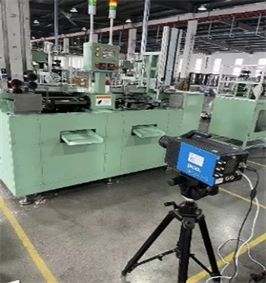
Figure 4. Wire coupling equipment and experimental equipment
图4. 并丝设备及实验装置
基于高速相机分析软件TEMA,得出丝线位移与速度图像导出其运动相关数据,通过对其运动图像及数据进行综合分析得出丝线运动的科学结论。
3.2. 实验图像及数据分析
在主轴1500转,在线轴第一层丝线上进行试验,使排线架与丝线从线轴左侧运动,得出如下图实验图像与数据。
图5所示丝线整个过程位移图,由于加速度变化总体上丝线呈现波动上升状态。
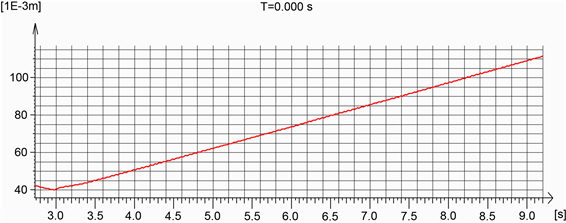
Figure 5. Wire coupling equipment and experimental equipment
图5. 并丝设备及实验装置
如图6丝线运动的速度图像示,三个过程速度变化符合理论分析过程,反映了丝线加减速及波动,表1显示为丝线在0.1 s内各过程以标尺为参考在图像内运动位置,表格内选择初始位置结束位置以及中间三个位置。
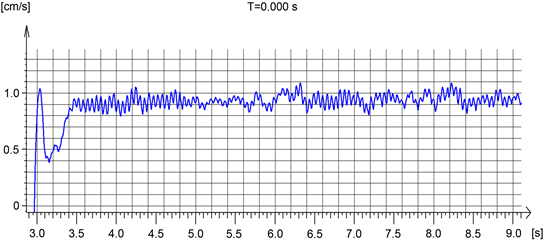
(a) 全过程图
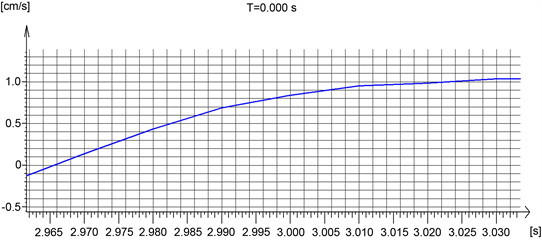
(b) 第一过程图
(c) 第二过程图
(d) 第三过程图
Figure 6. Wire velocity V/T diagram
图6. 丝线速度V/T图
根据表1位移数据与运动图像,第三过程整体位移量最大,第二过程稳定阶段次之,第一过程与第二过程初期其位移量最小,由于二过程初期,其受力变化最大,所以该过程运动位移量最小。
图7为1500转理论运动情况排线架直接由电机驱动除了加减速阶段其余阶段在不考虑机械振动情况下为匀速,如果丝线和排线架运动完全一致,那么为最理想情况。
表2为排线架在两个过程的0.1 s内运动位置,表格内选择初始位置与结束位置以及中间三个位置。
综合图6,图7及表1,表2的对比,与理想情况相比,丝线运动在第三过程排线架外力施加使丝线整体运动速度增加所以其运动最为接近理想情况,反映在并丝机上在该过程并丝效果最好,合乎本文理论,也符合实际。图8和图9所示为主轴1500转下丝线在第三层丝线上运动的图像与数据。
位移图像整体上依旧是呈现波动上升的状态,需通过图8与表3的数据更为直观的反映其运动情况。
图8,图9可知在第三层上丝线运动的三个过程同样遵循在第一层上运动的规律证明三个过程理论的合理,且层数增加速度波动增大位移量减小。
(a) 排线架位移图
(b) 排线架速度图
Figure 7. X/T&V/T diagram of cable rack motion
图7. 排线架运动X/T&V/T图
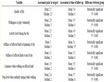
Table 2. Cable tray displacement data
表2. 排线架位移数据
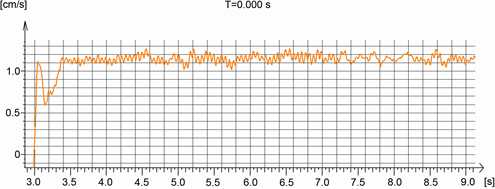
(a) 整个过程V/T图
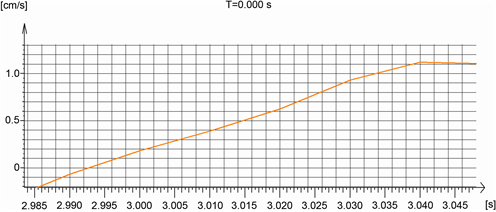
(b) 第一过程V/T图
(c) 第二过程V/T图
(d) 第三过程V/T图
Figure 8. Silk thread in the third layer V/T image
图8. 丝线在第三层V/T图像
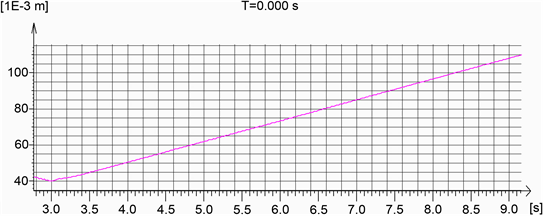
Figure 9. Silk thread in the third layer X/T image
图9. 丝线在第三层X/T图像
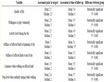
Table 3. Silk line displacement data in the third layer
表3. 丝线在第三层位移数据
1000转丝线在第一层上进行实验与1000转理论情况下进行对比。
如图10,在1000转状态下,丝线在位移和速度图像上的整体规律与1500转相似区别在于速度整体变小。
由表1,表2与表4的数据,由于排线架速度也变小,丝线在移动过程中张力F1和F2的释放变慢,所以在同样时间段丝线整体受到合力相对更大,丝线实际位移与速度在该转速下更加接近理论情况。
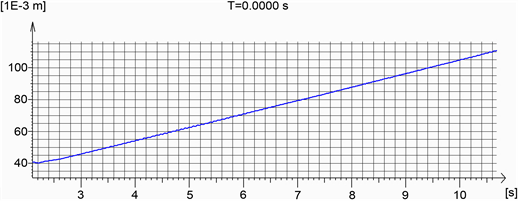
(a) 丝线X/T图
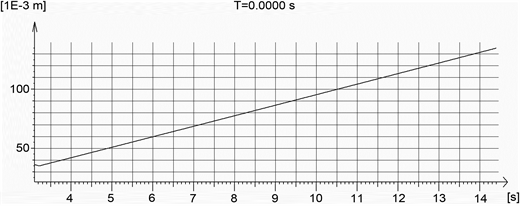
(b) 排线架X/T图
(c) 丝线V/T图
(d) 排线架V/T图
Figure 10. Actual and theoretical V/T&X/T images of 1000 turns silk
图10. 1000转丝线实际与理论V/T&X/T图像
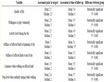
Table 4. Silk thread at 1000 turns a layer
表4. 丝线在1000转一层
由于丝线运动过程加速度在不断变化,上述图表中位移图像主要通过其波动程度来显示速度的变化情况及丝线运动的整体趋势,速度图像和表位移数据来验证丝线在不同阶段运动理论。
图11所示为丝线在不同阶段下的排列状态,速度越慢层数越少其丝线排列越理想。
(a) 1500转第一层 (b) 1500转第三层 (c) 1000转第一层
Figure 11. Silk motion comparison image
图11. 丝线运动比较图像
4. 基于深度学习的丝线瑕疵检测
4.1. Yolov8目标检测原理
如图12,YOLOv8算法目标检测原理如图所示,输入图片首先被分成S × S个网格单元,S的取值与最后输出的检测特征图尺寸相同,这样做的好处是使每个划分单元格都有一个对应的向量来描述目标检测结果。每个网格将会生成B个预测框,每个预测框都包含三类信息:目标置信度、类别以及位置坐标信息。目标置信度(P0)是指该预测框中是否存在检测目标的概率。C个类别信息(P1, P2, P3, …, PC)是指预测框中检测目标所属类别的概率,本文需要单种瑕疵,因此C为1。位置坐标信息为(tx, ty, tw, th),其中tx和ty表示预测框中心相对于网格左上角坐标的偏移值,tw和th表示预测框宽、高相对于锚框宽、高的缩放比例。通过上述信息可以将输入的整张耐压软管编织增强体瑕疵图片转换成一个S × S × [B × (4 + 1 + 1)]的向量。
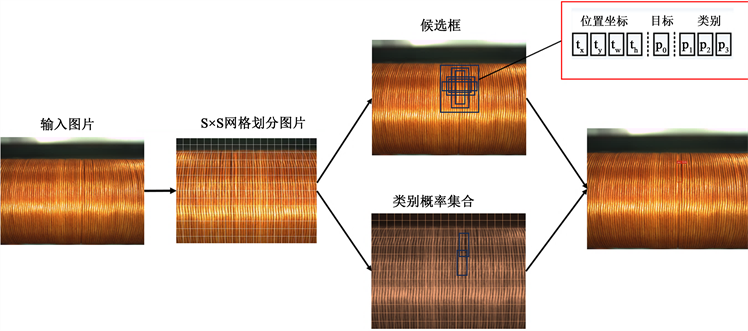
Figure 12. YOLOv8 object detection principle
图12. YOLOv8目标检测原理
4.2. 创建样本量与数据集
首先需要做的就是样本量的采集,经工业相机对并丝线轴丝线进行拍摄1500张左右,如图13通过labelimg对图片中瑕疵做标签处理,由于本次基于深度学习的检测意在分析其丝线运动过程中产生的瑕疵情况,而运动过程中由于阻力的影响瑕疵情况多为交叉和堆叠,所以主要针对拍摄的特征明显,清晰的瑕疵进行标记生成数据集 [5] 。
4.3. 数据集训练与图像
对采集好的图片和标签好的数据集进行处理,在pycharm中训练模型选择Yolov8,根据样本数据量选择训练250轮,可以得到较为理想的检测精度与损失情况。
如图14,丝线训练后预测瑕疵的精确率占所检测图片的71.7%,所有图片当中进行检测的图片大约占77%,基本可以满足丝线检测识别的要求。
如图15,在训练过程中随着轮数增加,其损失图像逐渐趋于平稳的图线,主要包括边缘损失与目标损失。
4.4. 检测平台与检测过程
如图16检测包括工业相机,开发板及显示器,拍摄丝线瑕疵同时做出检测,检测丝线运动瑕疵。
实际检测过程中首先将工业相机放置于指定位置,使线轴完全进入相机视野,随后打开检测平台进入检测界面,启动并丝机使其以相对较低的速度进行排线,其目的在于保证丝线在工业相机现有曝光度下拍摄到更加清晰的丝线瑕疵,在并丝机开始运动的同时平台选择瑕疵检测,开始检测进入检测状态从而将检测到的丝线瑕疵存到默认文件夹。
图17为检测装置操作界面,选择瑕疵检测该状态下会检测数据集中所包含的瑕疵特征,时间间隔为控制工业相机拍摄的时间间隔,实际检测过程中为了保证瑕疵数准确,时间间隔不宜太大,NMS&置信度关系到检测精度,调节越高检测精度越高,但是检测数量可能会下降,拍摄及检测到瑕疵的图片均会在平台检测结果与拍摄图片处显示。
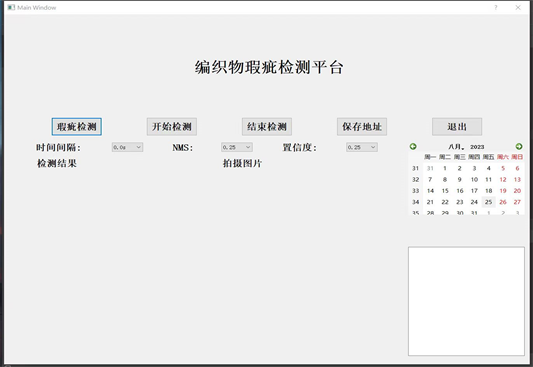
Figure 17. Defect detection platform operation interface
图17. 瑕疵检测平台操作界面
4.5. 试验检测结果
图18为部分检测结果,该图为在检测过程中检测到的瑕疵图片,瑕疵位置在图上自动标记生成,通过对比检测到的瑕疵数量来判断丝线排列状态。
5. 总结
本文以并丝线轴丝线为研究对象,研究了丝线在各个阶段的运动状况且进一步在基于深度学习的检测平台下对丝线排布的状态进行检测,综合各试验得出以下结论:
(1) 丝线运动会经历三个过程在第二过程包含两个阶段,与理想情况对比丝线在第二过程第一阶段的运动堆叠量最大,并丝效果最好的阶段为第三过程,次之为第二过程第二阶段。
(2) 同速下主轴丝线层数的增加,丝线的运动位移量减小堆叠大约在0.2 mm,不会造成丝线过分堆叠。
(3) 在同层不同速情况下,由于丝线张力释放速度的变化,随着速度减小,丝线在三个过程中的位移量与理想情况更为接近,堆叠量更少。
(4) 排线架的反向需加减速,所以丝线在第一过程的堆叠不可避免但在速度越小铺丝层数越少的时候同时间下第一过程运动效果越好。
(5) 在基于深度学习的检测平台下,检测的瑕疵相似度基本上在60%~70%左右,综合分析检测到的图片确定随着并丝机丝线层层铺设出现堆叠交叉等瑕疵增多,但总体上瑕疵数在可接受范围内,丝线的排布基本上稳定有序。
参考文献