1. 引言
近年来,我国电商行业发展迅猛。在2021年我国电商交易额达42.3万亿元,比上年增长19.6%,网上零售额13.09万亿元,比上年增长14.1%;2022年,全国网上零售额13.79万亿元,同比增长4% [1] 。由于电商行业的高速发展,其订单业务量也在高速增长。2016~2021年,我国电商行业订单业务量迅速增长,保持20%以上的增长速度;2021年,全国电商业务量累计完成1083.0亿件,较2020年增长29.9% [2] 。2022年1~11月,全国电商业务量累计完成1002.1亿件,同比增长2.2% [3] 。
随着电商订单业务量的总体大幅增长,商品货物仓储的工作量也随之增加,这也引起仓储作业中诸多问题的产生。比如:仓库设备和物流技术相对滞后,无法应付大量仓储作业,从而造成仓储作业的效率低下;在库过程中,商品保管不当可能造成货物损坏,从而提高物流成本和人力成本等,增加返工,降低效率;或是由于仓储流程的衔接安排不合理,导致大量商品出入库不顺畅,产生堵塞现象,使仓储作业效率低下。因此,对电商企业而言,仓储是保管企业货物并负责接收与配送的一个关键节点,其衔接货物由起发地送至客户手中的过程,如果在仓储作业环节中产生效率问题时,就会对时间和资源造成巨大的浪费,使得商品出现滞留无法按时送到客户。
为了分析与解决电商企业在仓储作业过程中所面临的问题,本文以X生鲜电商作为研究对象,该企业在不断扩大自身规模时,也因为业务量的增加产生仓储方面的问题,尤其是仓储作业流程效率低下的问题。此外,由于仓储作业流程具有多个环节,为了更加具象地观察X公司的仓储实际操作流程,以便确认流程中瓶颈所产生的问题,本文运用Flexsim [4] [5] [6] [7] 进行仿真分析,利用三维建模工具建立一个较为真实的电商仓库作业场景,并通过运行数据分析找出X公司仓储作业流程中瓶颈存在的问题,进而提出相应的优化方案并进行效果验证,以此提升X公司仓储作业流程的效率。
2. 文献综述
2.1. 仓储作业流程优化
现代物流体系中,仓储占据至关重要的地位,也是生鲜电商企业须进行规划和优化的关键点。目前生鲜电商仓储存在着诸多问题,如运作速度较慢、库存水平较高以及信息化水平低等。对于生鲜电商的仓储管理而言,需确立一套高效的出入库和存储作业流程是仓库运营的基础,为企业提供良好运营环境的同时也能够显着提升企业的管理水平和能力。
当前关于仓储流程的优化问题,已有众多学者展开深入研究,而采用Flexsim仿真建模的方式进行分析是一种常见的分析方法,如王志强 [4] 针对仓储作业流程中货物堆积和拣选效率低下的问题,采用AS/RS取货规则进行重新优化,并利用Flexsim建模找到仓储入库过程中出现的货物堆积问题,且验证货物堆积问题优化方案的可行性。Kudelska [5] 探讨拣货效率和员工工作量对仓储系统流程的影响,并利用Flexsim对仓库布局进行建模,以优化技术和组织创新,改善企业自有的仓库设施和流程。汪燕 [6] 利用Flexsim模拟MC公司的仓储流程,发现入库和分拣效率低下、错误率较高,人员和工作配置不够合理,且存在大量不必要的工作环节,并运用Flexsim验证方案的有效性。于笑 [7] 运用Flexsim对焙赞电商物流仓储系统的作业流程进行建模,并通过数据分析发现仓储流程的瓶颈,分析其潜在原因并提出相应的解决方案,最终重新构建优化仿真模型,验证优化方案的有效性。
除了使用Flexsim仿真建模外,数学建模也是一种有效的分析方法,如刘娟 [8] 从仓储出入库及存储流程中的潜在问题出发,运用Petri网的状态方程配合其他数学计算辅助分析方式来进行研究,并运用ECRSI法来对公司仓储过程进行优化,从而使目前仓储流程中存在的问题得到切实可行的处理,从而提升仓库的运作效率。吴锦梅 [9] 对电商物流园内仓储的货位进行研究分析,采用层次分析法和多目标规划相结合的方法建立模型,用遗传算法对模型进行求解,最终得出仓储货位的优化结果。
虽然数学建模具有严谨的逻辑性,但Flexsim卓越的三维图形展示特性,更易被企业管理人员所接纳和运用,而且Flexsim仿真环境下的各种模型真实可靠,无论是在仿真驱动器、统计数字分析,还是图形代表方面都表现出切实可行的效果,另外在虚拟技术领域,其性能也超越其他同类软件 [10] 。
2.2. 仓储作业成效评价
对于现代生鲜电商企业而言,进行仓储作业效果评价是一项关键任务,在企业找到仓储流程中的瓶颈并提出相对应的解决方案后,效果评价可以从多角度验证方案的可行性,从而让企业有更明确的方向,帮助企业在仓储过程中实现成本降低、商品质量保证以及仓库管理水平提升等目标,促进有效的人员安排和岗位责任制,及时解决生鲜商品变质、破损等问题,从而提高顾客的满意度,扩大生鲜电商企业在市场上的占有率。Gómez et al. [11] 通过对仓库管理综合质量指标的评价,並建立改进后的新管理系统提升管理水平。张的 [12] 对重庆JDSL电子商务物流中心经营过程中出现的问题进行归纳,并从提高经营的整体观念、合理地进行人员配置、强化对承运人的规范化经营等方面进行探讨。刘潇潇 [13] 建立一个系统化的数据化运作管理的定量分析体系,并以此为基础对该企业仓储过程进行分析与评价,从而实现电商企业与电商仓储企业之间的共赢。张帆 [14] 利用Flexsim对分拣中心业务流程进行模拟,并定性、定量化地对原来的业务流程进行分析,找出其中的缺陷后进行优化改善,最后对改善后的业务流程进行评估分析。
综上所述,大多数的仓储作业成效评估研究局限在理论验证上,首先提出仓储流程存在的问题,再提出优化措施,并用理论模型或仿真模拟方法验证优化措施可行性,导致发现问题的部分仍然缺乏数据支撑,并且对生鲜电商仓储作业流程的研究较少。因此,本文考虑X生鲜电商公司仓储作业现状,运用Flexsim运行数据找出X公司仓储作业流程中存在的问题,提出优化方案,同样利用该软件验证方案的可行性,从而对仓储作业中存在的问题进行优化。
3. 基于Flexsim的X公司仓储作业流程现状与问题分析
3.1. X公司仓储作业Flexsim模型建立
图1为X公司仓储运作流程,包含:货物入库前期工作主要有仓储设备设施的检验以及入库工作人员的安排,入库人员接收到上游供应商的发货通知,并对其信息进行登记和处理;货物入库环节中,货物到库后由质检人员对其进行质量检查与称重,并统计登记相关信息,对于不合格货物进行退货处理;在库环节则是对入库货物进行分拣、上架、包装、贴签等操作;在收到客户订单后,将加工完成的货物按照客户要求进行装运出库。

Figure 1. Warehouse operation process flow of X enterprise
图1. X公司仓储运作流程
根据X公司仓储系统实际运作情况、设备布局以及人员安排,在Flexsim中建立相应仓储模型(图2),Flexsim临时实体与实际物流系统中的对象对照情况如表1。在Flexsim中,商品在抵达仓储系统后,经过分解器的拆包分解,由叉车运入质检暂存区等待质检。随后,入库质检人员将其送入处理器,执行质检称重任务。对于质检不合格品,实施退货处理;而剩余商品则进入待入库暂存区等待上架。这时,入库叉车会将这批合格的商品上架存放,而分拣人员则会根据顾客订单进行商品分拣,并通过处理器的称重打包处理,将商品送入待贴签暂存区,由贴标签人员完成对处理器的贴签操作,贴完标签的商品则进入待出库暂存区域,等待装车、发运和配送。
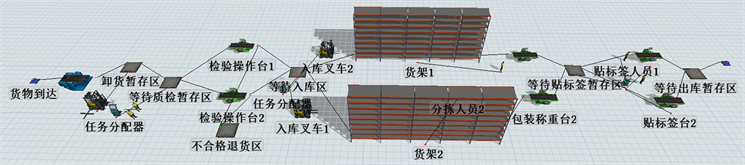
Figure 2. Simulation model layout of Flexsim
图2. Flexsim仿真模型布局
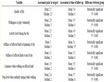
Table 1. Physical design of warehouse operating system
表1. 仓储操作系统实体设计
根据对X公司仓储实地数据的搜集,设定以下参数:将货物设置为按时间间隔到达仓库,并设置每日到达次数为三次。在该模型中,距离度量单位设置为米,时间度量单位为秒。设置仓库入库每车的到货量服从U (400, 500)的均匀分布,这代表每车货物的到达数量在400~500件之间,同时暂存区容量设置为100单位;叉车容量设置为10件,处理器预置时间为0,表示货物一到达处理器便可开始进行操作;同时,在分拣过程中,包装称重处理的加工时间和贴标签处理的加工时间则分别设定为40秒和5秒。
3.2. 模型运行结果分析
根据模型模拟货物到库直至装上配送车出库的过程,最终得到的模型运行时间为8.62小时,该结果与实际操作环境情况相似,说明系统中实体参数的设定值与实际操作环境具有一致姓。随着模型的模拟运行,在入库环节中开始出现大量货品堆积。因此,导出等待质检暂存区、等待入库暂存区的货物停滞时间以评估仓库入库效率、以及选择分拣人员和贴标签人员利用率,用以检测分拣作业人员配置合理性。
首先,针对入库流程站存区系统运行数据(表2)进行分析,结果显示货物在等待质检暂存区的最短停滞时间为4.18秒,最长停滞时间为1627.75秒,平均停滞时间为1555.50秒。货物在等待入库暂存区的最短停滞时间为5.49秒,最长停滞时间为14.67秒,货物的平均停滞时间为10.29秒。由此可见,质检暂存区的货物停滞时间远高于入库暂存区,显示质检暂存区下游(人工质检环节)速度慢、效率低,造成该暂存区堵塞。因此,输入货物的速度远大于输出货物的速度,这无疑会影响入库的效率。
对入库商品进行质量检验,主要目的是保证商品质量、检查到库商品是否在运输途中出现破损、丢失以及是否符合相关单据的信息要求。根据对X公司仓储的实地调查,其检验商品主要有以下指标:① 品名数量检验,即入库商品是否与相关单据的品名、规格以及数量一致;② 质量检验:检查到库生鲜是否具有相关检验检疫书面合格报告;③ 重量检验:对商品进行称重,检查其重量是否符合相关单据信息;④ 包装检验:即检查包装与外形是否有缺陷、商品有无损伤。该检验过程需要核对多项信息,根据现场工作情况,一位入库质检员处理完成一件生鲜产品的时间大约需要40秒;而每次每车运来的货物约为600件,到货后由卸载叉车将货物运送至质检暂存区,叉车每趟能运送10单位货物,大约需要50秒,经计算可得平均每个货物由入库卸货至进入质检暂存区所需要的平均时间为5秒,可见质检环节的货物输入速度大于人工处理的货物输出速度,导致质检暂存区堵塞。
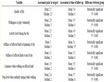
Table 2. Operating data of the temporary storage area before optimization
表2. 优化前暂存区运行数据
接着,针对分拣流程运行数据进行分析,由于入库、分拣和贴标签的过程均是由工作人员进行的,因此导出相关流程工作人员的空闲率与利用率来分析该流程效率(表3)。从表3可知,分拣人员1、2的空闲率分别为22.56%和23.64%、贴签工作人员1、2的空闲率分别为75.56%和79.38%,显示该分拣作业流程人员配置存在缺陷、分拣人员工作量较大、且贴标签的工作量小,而受到员工配置不合理的影响,整体仓储作业效率的正常运转也会受到影响。
由于X公司仅有2个分拣员进行仓储分拣工作,且主要是通过人工分拣,自动化机械操作很少,从而导致分拣员的工作量过大;此外,仓库在接收到客户订单后才能打印订单信息,导致分拣人员需要从大量堆积的货物中取出客户订单上要求的重量规格,并且需要多次称重直到符合订单要求才可发出,尤其在订单量较大的时候十分影响分拣效率。因此X公司在正式分拣之前还采用预分拣,即先将堆积在一起的货物按不同重量规格进行小单位包装和称重(分为5斤、10斤、20斤等规格),再根据接收到的客户订单信息,选取不同小单位包装进行正式分拣或直接送至待贴签暂存区等待贴标签。
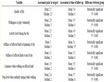
Table 3. Operating data of the warehousing staff before optimization
表3. 优化前仓储工作人员运行数据
虽然预分拣能提升主动性和工作效率,但也存在一些问题。由于客户订单中大批量订单占比较大,这导致X公司在预分拣过程中,重量较大的货物分拣量较大,而重量较小的货物因分拣量不足以满足客户订单数量,因此分拣人员只能取出部分已包装完成的大批量货物进行拆包装,拆分成若干小批量货物,分别称重检验后再重新进行包装(图3)。例如,预分拣后5斤单位包装白菜的数量不足以满足客户订单的数量,而分拣出的10斤单位包装的白菜数量过多,这时则需要将先前预打包好的10斤白菜取出,进行拆包装处理,并称重出2个5斤白菜,再分别进行重新包装和投框,这无疑会导致不必要的步骤增加,浪费时间的同时也会大大耗费人力物力,严重影响该环节的工作效率。而分拣完成后的货物送至贴标签工作台,贴签操作简单,完成一件货物贴签只需5秒左右,这就会导致分拣速度明显慢于贴签速度,而分拣和贴签的工作人员数量一致,就会造成X公司仓储工作人员安排不合理的问题。

Figure 3. Pre-sorting and sorting process
图3. 预分拣及分拣流程
4. 基于Flexsim的X公司物流仓储作业流程优化
4.1. 流程优化方法及模型
根据上述分析结果找到的问题,其相应的改善方式说明如下。首先,采用RFID自动识别技术来取代货物入库流程中的称重、人工质检、手动填写相关单据并录入系统等环节。优点在于能够穿透纸张、塑料等非金属材料识别商品重量、品种、温湿度、气体成分信息,无需通过接触,通过系统对信息进行收集和比对,且相比于人工操作中的多层检查,该技术速度更快,精准度更高,使该环节能得到高效、准确的控制 [15] 。根据X公司仓储实际运作情况,建议选取工作频率为13.56 MHz的高频RFID进行优化对该环节进行改善。相比于低频RFID设备,高频RFID更为精确和快速,可以进行多标签辨识,存储容量可达8k以上,并且阅读识别距离更远为1米左右,符合实际场地等待质检货物到RFID阅读器的距离;而相比于超高频RFID设备,高频的优势在于成本更低、具有更强的穿透非金属介质的能力,且对于含水量较高的商品,不容易被遮挡,该条件尤其适用X公司含水量较高的生鲜产品 [16] 。
因此,X公司只需将RFID阅读器安装于仓库入库口,利用叉车将放有待质检货物的托盘直接送至RFID阅读器下方,RFID阅读器即可快速自动检索和检验被质检货物的所有相关信息,并将其直接录入系统中,即可立即呈现货物的信息,这样就能快速地对不合格产品进行处理。因此,仅需指派一位员工将不合格品投放至不合格品退货区,这样即可大幅节省人力和时间成本,同时还能有效避免因为人工操作而出现的差错问题。在Flexsim中,射频技术的应用仍由处理器进行表达,只需重新调整处理器的质检时间,并将每件商品的质检时间设定为7秒。
其次,针对X公司分拣过程人员分配不合理的问题,可对涉及到的人员进行重新安排。由于分拣人员的工作量以及分拣速度明显低于贴标签人员,故增加分拣人员至3名,同时减少1名贴标签人员。另外还可以对预分拣流程进行改善,由于预分拣流程中存在的重复作业,可以将货物预分拣包装单位均设置为5斤,当遇到10斤、20斤以上的订单,只需直接将预分拣的若干批5斤货物进行合并,无需进行拆包装、称重等繁琐步骤。此时,分拣人员的速度也相应提高,在Flexsim中将分拣环节作业设置为30秒/件。最后,优化后预分拣与分拣流程如图4,对应的Flexsimz仿真模型布局如图5。

Figure 4. Pre-sorting and sorting process after optimization
图4. 优化后的预分拣及分拣流程
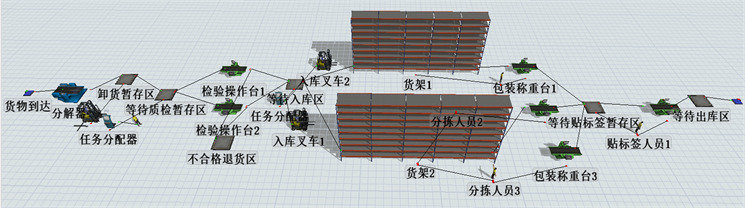
Figure 5. Simulation model layout of Flexsim after optimization
图5. 优化后的Flexsim仿真模型布局
4.2. 优化后模型运行数据分析
优化后的模型(图5)保持与优化前的模型(图2)相同的运行时间,得到等待质检暂存区、等待入库暂存区及工作人员的运行数据,如表4与表5。
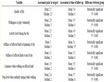
Table 4. Operating data of the temporary storage area after optimization
表4. 优化后暂存区运行数据
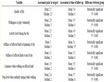
Table 5. Operating data of the warehousing staff after optimization
表5. 优化后仓储工作人员运行数据
从表4可知,优化后货物在等待质检暂存区的最短停滞时间为3.18秒,最长停滞时间为257.75秒,平均停滞时间为101.36秒;而货物在等待入库暂存区的最短停滞时间为2.43秒,最长停滞时间为7.04秒,平均停滞时间为2.45秒,入库的货物数量共1418件,与出库的货物数量相同。从表5可知,优化后增加一位分拣人员3,三位分拣人员的空闲率分别为27.59%、28.94%、33.56%,所对应的利用率分别为72.41%、71.06%、66.44%,而贴标签人员1的空闲率与利用率分别为36.75%和63.25%。
4.3. 优化前后模型运行数据比较分析
比较优化前后的待质检暂存区内货物停滞时间、人员利用率、货物出入库数量,可得出以下结论。
4.3.1. 入库效率提高
由表6可得,入库货物等待质检暂存区的最短滞留时间相比于优化前,在优化后缩短23.92%;同时,最长停滞时间相比于优化前,在优化后也缩短84.17%。仓储货物的输入和输出量由优化前的1216件增加到1418件,即在同一有限时间内,经优化后出入库的货物数量增加16.61%。在仓储入库作业过程中,货物等待质检暂存区停滞的平均时间相较于优化前缩短93.48%。由此可见,优化后的模型呈现出更高的入库效率,其运行时间与优化前相同,同时货物的入库量也得到显着增加,且入库停滞时间也大幅度缩短,说明引入RFID技术对入库效率的提升是一项可行的优化方案。
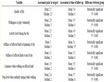
Table 6. Comparison of operating data of the temporary storage area before and after optimization
表6. 优化前后暂存区运行数据比较
4.3.2. 通过合理的人员配置,有效地减少不必要的劳动
由表7可得,优化前两位仓储分拣人员的平均空闲率为23.10%,对应的平均利用率为76.90%;在优化后,增加一位分拣人员后,三位仓储分拣人员的平均空闲率增加至30.03%,而对应的平均利用率下降为69.97%。另外,优化前两位仓储贴标签人员的平均空闲率为77.47%,对应的平均利用率为22.53%;在优化后,减少一位贴标签人员后,剩余一位仓储贴标签人员的平均空闲率下降至36.75%,而对应的平均利用率则上升为63.25%。结果显示,在进行优化之前,分拣人员的数量相对较少,但其所承担的工作量较大。同时,贴标签人员的工作流程单一,而人员分配量却与分拣人员数量相等,这会导致分拣人员的工作量过多,而贴标签人员的空闲率较高,没有对这些人员进行合理的使用。优化后,X公司的仓储作业效率得到提升,同时分拣人员的工作量分布也变得更加合理,四个工作人员的利用率趋于均衡。因此,对人员的重新分配可以使各工作人员所分配到的工作量趋于合理;同时删除预分拣作业流程中拆包装、再称重等繁琐的环节,也大大减轻分拣人员的工作负担,使仓储作业的效率提高,也助于降低仓储运行成本,提高企业利润。
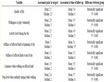
Table 7. Comparison of operating data of the warehousing staff before and after optimization
表7. 优化前后仓储工作人员运行数据比较
5. 结论与不足
本文经实地考察X公司仓储流程的现状,发现该公司也因为业务量的增加而产生仓储作业流程效率低下的问题。为优化X公司仓储流程,本文利用Flexsim仿真软件对其构建模型,通过分析运行数据发现其存在人员配置不合理、人工质检环节效率低、分拣环节出现不必要工作等问题,并针对该问题提出解决方案,即人员再分配、引进RFID技术以及对分拣流程进行改善,针对优化后的方案修改仿真参数,重新建立出优化后的仓储流程模型,对比优化前后数据,验证优化方案效果,可知本文所提出的优化方案的确能提高仓储作业流程运行效率。
然而,本文针对X公司仓储效率的优化虽在一定程度上能提高仓储作业的运行效率,但该仿真模型仍有些不可控的因素并未考虑,如订单量激增、爆仓等情况。因此,未来的研究中还需要通过建立其他更完善的模型从而对仓储作业的所有流程环节进行进一步研究。