1. 前言
能源短缺和环境污染是当今世界汽车工业发展面临的两大挑战,因此开展新能源汽车的研究已是刻不容缓 [1] 。进入新世纪以来,我国的排放法规逐渐规范化与严格化,在吸取欧盟排放法规经验的基础上进行了适当修改,更加符合我国机动车的实际运行工况。从长远来看,纯电动汽车的零油耗、零排放特点使得其成为车企未来发展的方向 [2] 。另一方面,我国也将电动汽车产业列为重点发展的新型战略产业,希望通过发展电动汽车来促进我国汽车产业的结构调整和技术进步,最终实现汽车产业的“弯道超车” [3] 。
目前有许多学者对纯电动汽车集成化技术进行一系列研究。杜克强等人综述了纯电动汽车在高速电驱动系统方面的发展现状 [4] 。赵泽西等通过改善有限元分析方法,对新能源汽车集成式变速箱从加载方式,接触,连接方式等方面进行深入剖析 [5] 。胡新举对电动商用车电池箱箱体进行不同工况下的力学强度分析,并进行优化设计,为以后电动汽车快换电池箱的设计改进提供理论依据 [6] 。施一敏以汽车电器部件的线束为重点研究对象,提出了四种线束轻量化的技术设计方案并加以论证 [7] 。李济霖针对目前电池能量分配单元,研制了一款可在线电路重构的集成化测试系统,有效解决了电动汽车BDU集成化自动测试设备匮乏的问题 [8] 。卢文轩等阐述了电驱动系统的研究现状,介绍了主流驱动系统的集成方式及技术特点,对电驱动系统采用集成化设计的优势与弊端进行了分析 [9] 。中国的新能源汽车产业目前已经呈现出了高速发展的局面,从数量上看中国的新能源汽车已经达到了世界的领先水平。然而从技术层面上来说,中国新能源汽车的技术水平和制造工艺技术还相对比较落后,许多方面还亟待改善 [10] 。针对小型纯电动乘用车的制造体系,质量保障体系,实现产品的批量化生产还研究较少。因此研究整车产品的工程化集成设计,关键零部件的集成开发及测试能力建设,产品试制及质量评价等具有重要意义。
基于以上原因,本文开展小型纯电动乘用车集成设计方法研究,研究开发一款小型化、轻量化和满足国家各项电动汽车安全要求的城市代步纯电动汽车,能够提升能源利用率和公共道路使用率,便于人们在市区活动使用,以缓解目前困扰汽车工业的两大难题。
2. 工艺方法
2.1. 技术原理及系统主要特性
本文开发的城市微型代步电动汽车,其基本电气及网络框架如图1所示。系统通讯节点包括整车控制器、电机控制器、电池管理系统、车载充电机、数字仪表、远程监控终端等。
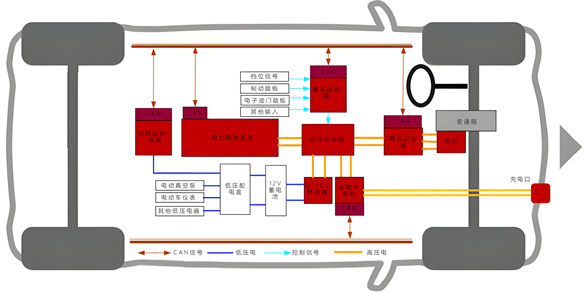
Figure 1. Electrical and network frame diagram
图1. 电气及网络框架图
整车选择上汽通用五菱技术某款纯电动汽车,在成熟的整车布置、底盘、车身、内外饰系统的技术基础结构上,新能源汽车的具体组成还包括:整车控制系统、电机驱动系统、动力电池及充电系统、高压系统、辅助部件、远程监控系统等,系统成熟可靠,具备如下优点:
(1) 围绕安全进行整车的布置优化设计。
(2) 系统中的关键信号:互锁信号、使能信号等除了通过总线传输,还通过硬线传递给VCU,保证足够的可靠性。
(3) 整车控制系统基于V流程开发,应用层与底层独立开发,定义了标准接口,在设计时最大程度上考虑了整车安全设计要求,确保整车控制系统的可靠性。
(4) 电机控制系统进行了结构优化设计,提高了驱动电机系统的功率密度和驱动效率。
(5) 电池包采用一体式的结构设计,并布置在整车中部,进行全面的碰撞安全分析,并方便装配及维修。
(6) 高压配电系统集成式设计,线束可靠,确保整车高压安全和成本优化。
(7) 整车关键零部件系统经过严格的电磁兼容、高低温、震动实验,生产过程严格一致性质量控制。
(8) 具备远程信息采集、诊断、管理功能,专业的售后服务队伍,强大的售后保障能力。
2.2. 工艺流程
本文开发的微型代步电动汽车,其生产制造主要经冲压、焊接、涂装、总装车间四大工艺生产环节,见图2。在整车制造过程中,执行严格的过程质量检验,同时在车辆下线后进行整车质量检测,确保交付到客户的产品质量。在生产过程中,采用精准的ERP系统进行计划发布,采用高效的LES系统进行物料拉动,确保制造过程的快速响应、高效运行。
图3是涂装生产工艺流程图。主要承担乘用车及新能源车白车身的前处理、电泳底漆、涂密封胶、喷UBC胶及裙边胶、喷中涂、喷面漆和精饰等工作。采用无人操作工艺段设置为单线与手工操作工艺段设置为双线相结合的布线方式。
总装车间主要承担新能源车型的装配、部件分装、整车调试、返修和部分检测工作。总装车间由车身储存线、主装配线、检测返修区、部件分装区和物料储存区等几部分组成,车门、电池、电机、仪表板模块分装工作地设在部件分装区。检测线、返修区集中布置,将噪声排烟集中处理,有利于车间整体环境。车间工艺平面布置以保证生产线装配工位和装配作业面积为前提,合理规划物流和作业空间,提高生产效率。其生产工艺见图4。
多类型纯电动汽车混流生产工艺重点研究纯电动汽车的技术共性及生产质量关键控制项,针对其特点,对专用件的总装工艺专门设计,实现多类型纯电动汽车的混流生产。
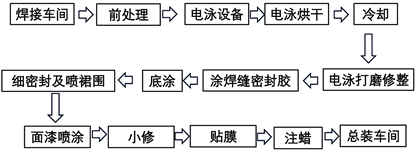
Figure 3. Painting production process flow chart
图3.涂装生产工艺流程图
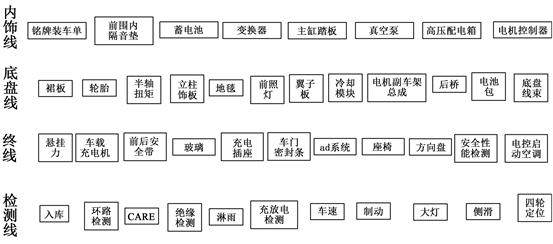
Figure 4. Final assembly production process flow chart
图4. 总装生产工艺流程图
3. 结果及讨论
3.1. 整车开发研究
整车动力系统采用最常见的前置前驱方式,电池包放置在整车中部,位于座椅下方,有效减轻各个方向的碰撞冲击,确保高压系统安全。整车动力架构如图5所示。
E100车身整车框架如图6所示。车身结构采用上部2纵 + 2横,侧面A柱 + B柱,下部4纵 + 6横的承载式车身结构。车身前后保护针对碰撞设计有优化的传力路径,能有效的在吸收能量的同时将多余的能量传递下去;动力电池放置在车身座椅地板下,车身大梁设计成一个“回”形框,提供动力电池安装点及保护动力电池。整车强度、刚度满足目标。
针对电池箱问题,本文设计了一种新型的动力蓄电池箱体,实现多种动力电池电芯的兼容性装配(三元/软包,圆柱/软包/方形)。并且在不同电量需求上同样实现兼容性装配(80 km/100 km/133 km/180 km/210 km/230 km/250 km),实现整车在动力蓄电池系统总成外包络不变的情况下实现多种续驶里程的需求和切换。并且实现了在不同电量需求下与整车充电端不同功率的随意组合和切换。并且在性能上满足整车防腐,零部件防腐,火烧,振动,冲击,挤压等多种安全性能。开发了一种带保护和绝缘功能的动力电池护板方案,实现动力蓄电池系统总成的碎石冲击和外壳防护。为了实现轻量化,采用ABS工程塑料(PC + ABS)一体注塑成型,既具有优良耐热耐候性、尺寸稳定性和耐冲击性能,又避免过多使用金属钣金件,提高模组集成效率,提升动力电池系统能量密度。同时电芯采用陶瓷隔膜与功能电解液协同运用,建立电池与电池管理系统失效模型,形成电池多级的安全防护策略,并利用后台大数据监控预警,提高动力电池系统安全性。
驱动系统关键零部件的集成一体化能够显著降低整车重量,带来续航的提升,行业内已形成较为清晰的技术路线:由最初单体的电机、电机控制器、减速器构成分体式驱动系统设计,逐渐向电机和减速器集成形成二合一电驱动桥设计发展,然后,发展到一体化集成电机、电机控制器、减速器的三合一集成电驱,最终演化成集成多功率模块的电驱系统。当微小型纯电动汽车量产后,将针对其特点,并结合用户的需求和最关注的痛点,积极探索适合于微小型纯电动汽车商业推广的新模式、创造出新能源汽车推广应用与智慧交通以及智慧城市共同发展的新生态。其技术路线如图7所示。
如图8所示,基于Ansys/Ansoft电磁场有限元分析对驱动电机开发:得到磁场分布及各种性能曲线、图表等,分析系统的可控性、稳定性以及鲁棒性。其中包括2D磁场分析、3D磁场分析、效率MAP、扭矩曲面图等。以优化多工况下的径向和切向电磁力幅值为目标,建立了噪声非线性模型,控制电磁谐波带来的转矩脉动,同时,基于对减速器的高转速下的齿轮热变形扭振响应分析模型,进行了齿轮参数修形,降低了NVH噪声问题发生概率,提升了集成一体化驱动系统的舒适性、稳定性。通过电机系统性能参数仿真计算,可以得到对电机系统的深入理解,在此基础上可以开展对电机系统的研究,满足微小型纯电动车用电机系统的开发要求。
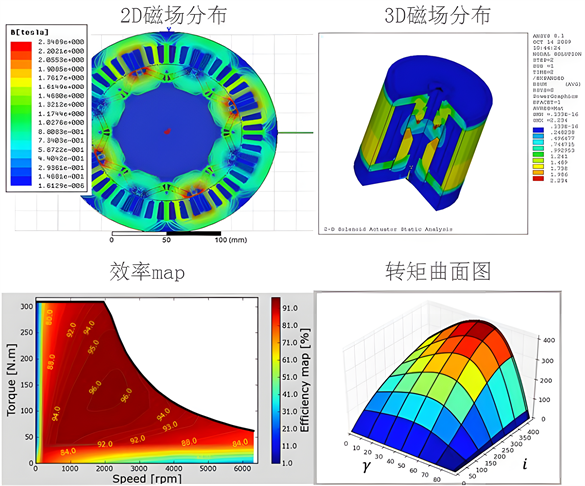
Figure 8. Schematic diagram of finite element analysis of magnetic force of drive motor
图8. 驱动电机磁力有限元分析示意图
3.2. 所达到的技术性能指标和水平
如图9,本文结合三综合振动试验设备,开发了特定的试验夹具和工装,并搭建了台架来实现整车模拟振动综合测试,包含动力电池、试验夹具、固定工装及连接调试接口、传感器及探头、试验台及充放电机等。通过台架搭建及模拟测试,在解决整车路试试验的困难的同时,实现包括GB38031-2020《电动汽车用动力蓄电池安全要求》在内的多项国家强制性及企业标准检测能力。保证了振动能量的真实传播,并在电池振动的同时可同步对工况充放电测试及全程状态监测,使试验过程更贴近实际路试,保障了产品的可靠性。
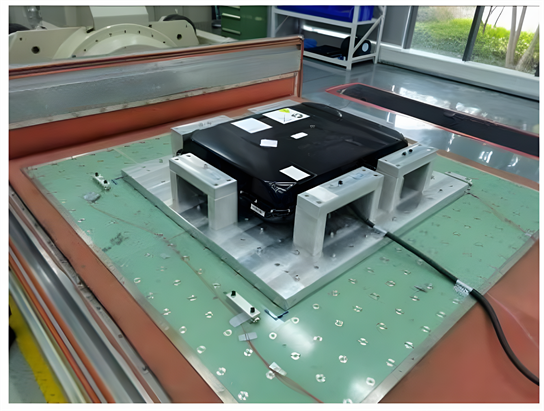
Figure 9. Power battery three comprehensive vibration bench test
图9. 动力电池三综合振动台架测试
本文开发的电动汽车搭载锂离子动力电池和永磁同步电机,能够满足最高车速不小于100 km/h,续驶里程不小于150 km的性能目标。产品满足国家各项标准要求,实现最小车身尺寸满足碰撞法规要求。整车主要参数如表1。
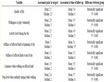
Table 1. Main parameters of the vehicle
表1. 整车主要参数
如图10电驱系统测试台架所示,通过驱动电机系统路谱台架耐久测试方法研究,解决了当前可靠性测试场景与用户实际使用场景差异大、验证强度不足等问题,更真实、高强度地验证驱动电机系统可靠性。通过非消声背景下驱动电机系统台架NVH测试方法研究,解决了公司当前驱动电机系统NVH台架测试资源紧张、委外测试费用高的问题,可以在多阶段、更充分地验证驱动电机系统NVH性能,提前辨识啸叫风险,缩短项目开发周期。
如图11,在环(HIL)仿真测试设备,通过搭建测试环境达到模拟整车运行工况及环境的效果,依据整车控制器功能规范编写测试用例并进行测试,成功缩短测试周期、节约测试成本、实现极端工况测试。
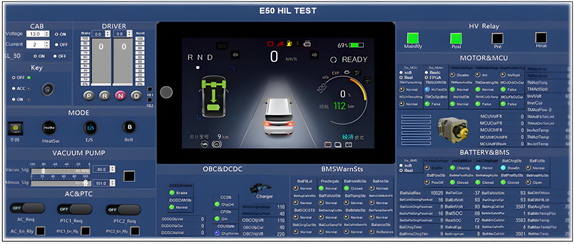
Figure 11. HIL test bench operation interface
图11. HIL 测试台架操作界面
3.3. 展望
本课题开发的纯电动汽车在行业中的同类型产品中处于性能领先地位,符合用户城市用车需求,具有能源转化效率高、能源不依赖燃料、车辆“零排放”等特点,符合国家新能源发展战略。与产品自身相比以及根据新能源汽车发展趋势,本产品仍存在一些优化空间。
(1) 电动汽车的使用离不开充电环节,但充电过程相比燃油汽车存在充电基础设施不足、充电时间长等特点,由此带来的里程焦虑影响了电动汽车的发展普及。本产品可以通过进一步提高充电功率,减少充电时间,消除用户里程焦虑,使用户对电动汽车使用更安心。
(2) 可以通过优化电池内部布置,采用更高能量密度电芯,进一步提高电池包能量密度,增加电池电量从而增加车辆续驶里程。
(3) 研究无人驾驶车是推动智能网联汽车发展,是落实《中国制造2025》,助力汽车产业供给侧结构性改革的重要举措。依托本产品进行无人驾驶技术研究,将有助于推动企业以及柳州新能源产业以及智能驾驶技术发展。
4. 结论
本文为解决汽车能源利用率低和城市交通拥挤等问题,对城市代步纯电动汽车进行开发研究。产品根据市场调研,明确了整车各项参数,并围绕电动车关键零部件搭建整车电子电气架构;在车身结构、电池布置等进行优化设计,实现最小车身尺寸,并通过《电动汽车碰撞后安全要求》标准要求;对各零部件、整车进行了完善的试验验证,充分验证了整车的动力性、经济性、可靠性、安全性等各项性能,产品满足国家各项法规标准要求。开发的产品车长仅2490 mm,小巧玲珑,无论是停车还是行驶,仅需占用两辆电动自行车的空间,在市区行驶灵活自如,节约城市道路资源,缓解拥堵问题,展现出强劲的市场竞争力,一经上市便广受用户喜爱,创造了显著的社会和经济效益。同时,储备了新能源汽车研发技术,并促进了新能源汽车技术的推广和应用。
参考文献