1. 引言
单晶硅作为一种重要的半导体、光电传感器和红外光学材料,广泛应用于大规模集成电路、光伏发电、红外成像或检测等行业 [1] [2] 。它是一种硬脆材料,硬度高(12~14 GPa),但断裂韧性低(~1 MPa·m1/2),这使得单晶硅难以加工 [3] 。单晶硅的延性加工深度一般在90 nm~200 nm以下,因此当采用较大的切削深度时,会出现严重的脆性断裂和微裂纹向加工表面扩散。此外,未加工硅片的原始表面通常呈平面形状,这大大增加了深层微结构的材料去除率 [4] 。尽管已经应用了传统和非传统的加工方法来加工硅,但在单晶硅上获得具有光学形状精度的结构仍然是一项艰巨的任务,因此探究切削参数与单晶硅表面质量的关系,通过优化加工参数提高加工表面质量,从而为工业实际加工过程进行指导至关重要。
葛梦然等 [5] 对单晶硅与玻氏压头的压痕接触变形进行了理论分析和实验研究,该结果为单晶硅的金刚线精密切片和精密磨削工艺参数的优化提供了一定的理论指导。崔杰等 [6] 对单晶硅材料进行纳米压痕实验,表明单晶硅超精密切削加工应选择合理的载荷,并充分考虑弹性回复的影响。王龙等 [7] 开展了单颗金刚石磨粒切削单晶硅片的微米划痕实验,单晶硅破碎损伤随着加载压力或切入深度的增大而越加严重,伴随释放的声发射信号强度增大。陈自彬等 [8] 设计高速划刻单晶硅的玻氏压头试验装置,并进行单晶硅片划刻试验,实测其径向裂纹萌生的划痕深度,其划痕深度计算值与试验测量值一致性较好。姚同等 [9] 建立单晶硅车削实验,结果表明,主轴转速对表面粗糙度影响最显著,主轴转速越大,表面粗糙度值越小。
Fang等人 [10] 和Zhang等人 [11] 表明,塑性切削模式下的单点金刚石车削(SPDT)是一种可行且有效的方法,可将单晶硅超精密或纳米加工成复杂形状,同时保持高精度和工业所需的镜面。然而,实现高精度的表面质量需要适当的加工参数。Yan等人 [12] 指出,只有当未变形的切屑厚度小于临界延性–脆性转变(DBT)深度(范围从100 nm到500 nm)时,才能实现韧性切削。此外,韧性切削很难在整个切削过程中持续。Uddin等人 [13] 发现,由于工件的硬度,用于Si加工的SPDT的金刚石刀具会受到严重磨损,导致表面质量恶化,无法产生单晶硅部件所需的表面粗糙度。Yan等人 [14] 发现,当加工单晶硅的切削深度在30 nm和120 nm之间时。在加工形成的光滑切削表面下有多晶Si、位错和微裂纹等现象。因此,需要考虑探究加工参数来提高单晶硅的可加工性。
国内外学者对于单晶硅超精密切削加工实验研究已经做了深入研究,但是由于基础实验并不能清晰的展示单晶硅材料与刀具的相互动态作用过程,因此采用数值模拟的方法是一种理想的选择。然而,单晶硅超精密切削模拟研究方法因受限于理想化模型与时空尺度差异等因素,还存在一些亟待优化解决的复杂难题。鉴于上述情况,在本文报道的研究中,建立了单晶硅三维超精密切削数值模拟模型,通过模拟不同加工参数(切削深度、切削速度、刀具角度)下的切屑不同形态表征单晶硅材料去除机理,更深入地研究了加工参数与加工表面质量的基本关系。
2. 单晶硅超精密切削数值建模
2.1. 材料本构模型及断裂准则
单晶硅是在常温状态下一般表现出硬脆性特点的单晶体材料,图1给出了单晶硅典型的宏观应力示意图。在力的拉伸、压缩作用下,单晶硅的变形和破坏损伤与应力极限有着相当密切的关系。单晶硅微元上任意一点的应力都可以用三个正应力
与剪切应力
进行描述,如图1所示。单晶硅的材料性能可以使用下式表达:
(1)
式中,
是正应力,
是剪切应力

Figure 1. Stress schematic diagram of single crystal silicon elements
图1. 单晶硅微元的应力示意图
但是单晶硅在精密切削过程中会存在一个塑性域的临界值,当切削深度在这个临界值之间浮动时,单晶硅的切削会经历塑性–脆性的转变,因此本文采用Drucker-Prager本构(D-P本构模型)对单晶硅模型进行定义。D-P准则屈服面并不随着材料的逐渐屈服而改变,因此没有强化准则,塑性行为被假定为理想弹塑性,然而其屈服强度随着侧限压力(静水应力)的增加而相应增加,另外,这种材料考虑了由于屈服而引起的体积膨胀 [15] 。
D-P本构模型如下:
(2)
式中,
和
分别是应力第一不变量和应力偏量的第二不变量
主应力形式表示为:
(3)
(4)
对于单晶硅的切削过程而言,
,再利用主应力之间得求解关系式:
(5)
因此,由式(2-3)与式(2-4)转化为式(2-5)与式(2-6):
(6)
(7)
该D-P本构模型可以很好的描述将单晶硅切削时的塑性–脆性转变过程。
2.2. 单晶硅普通切削有限元建模思路及边界条件
本文采用有限元分析软件ABAQUS/Explicit模拟单晶硅材料的正交切削行为。由于单晶硅在实际切削中存在塑性域,当刀具在塑性域以上进行切削时,单晶硅材料不会产生很大的缺陷。一旦切削深度越过塑性域极值,那么单晶硅将会切削到脆性层,切削表面会产生很大的缺陷。因此本文研究在不同工艺参数(切削深度、切削速度、刀具几何参数)下单晶硅材料切削表面质量情况。
单晶硅切削整体普通切削有限元模型如图2所示,工件代表性体积单元的几何尺寸为10 µm × 2 µm (长 × 宽)。并且为了更好对工件进行切削,将工件分为切削区以及非切削区,切削区进行网格细化,使用C3D8R,C3D8R:八结点线性六面体单元,减缩积分,沙漏控制,网格尺寸为0.008 µm;非切削区不进行网格细化,同样使用C3D8R,C3D8R:八结点线性六面体单元,减缩积分,沙漏控制,网格尺寸为0.5 µm。本文只考虑不同工艺参数下单晶硅材料切削的表面质量,加工参数如图2所示。不考虑刀具磨损对有限元结果带来的影响,在模拟中使用的刀具以前角、后角和圆角半径r为关键参数进行建模,并且将刀具设置成刚体。在刀具上赋予参考点RP控制刀具的切削方向和切削速度,刀具前角−20˚,后角10˚,圆角半径为8 × 10−2 µm。刀具采用网格尺寸为0.2 µm。工件的底部与左侧完全固定,自由度为0 [16] 。
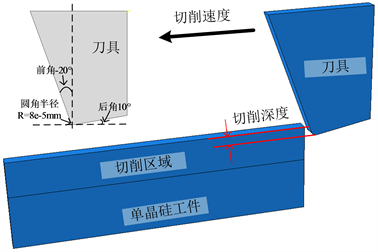
Figure 2. Schematic diagram of three-dimensional cutting model for monocrystalline silicon
图2. 单晶硅三维切削模型示意图
3. 单晶硅超精密切削工艺参数对表面完整性的影响
在对单晶硅超精密切削模拟后的加工表面进行评估之后,截取加工表面的切削区切屑形态、面下变形及应力分析以及加工表面三维形貌,分别确定不同切削参数下切削区域及加工表面的变形大小和质量,以达到通过参数优化加工表面质量的目的。
3.1. 切削深度对表面完整性的影响
图3显示了不同切削深度下的单晶硅切削模型模拟的切屑形貌和最终加工表面状态。可以明显看出这三种模型的刀具切削刃下方的和沿着进给方向的单晶硅在切削过程中的切屑形态及最终加工表面状态极其不同,在图3中可以清晰地看出刀具的圆角半径处出现高应力区域,该区域围着刀具的圆角半径形成一个类多边形区域,切削深度越大,高应力区域越明显,此时在切削过程中积累的应变能由刀尖的下方开始释放,造成单晶硅材料断裂。在整个切削过程中,这种情况是动态变化的,并且随着切削时间和刀具切削阶段而变化 [17] 。
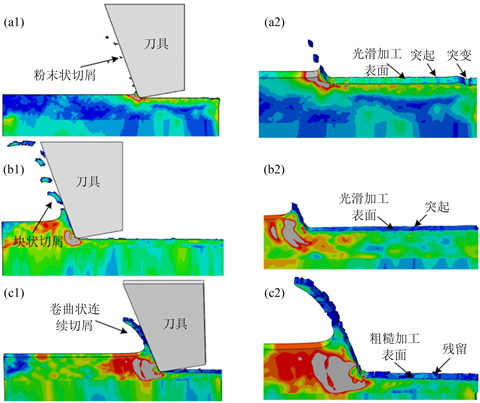
Figure 3. The chip morphology and machining surface state at different cutting depths: (a1) and (a2) are schematic diagrams of the cutting morphology at a cutting depth of 50 nm; (b1) and (b2) are schematic diagrams of the cutting morphology at a cutting depth of 100 nm; and (c1) and (c2) are schematic diagrams of the cutting morphology at a cutting depth of 150 nm
图3. 不同切削深度下的切屑形态和加工表面状态:(a1) (a2)是50 nm切削深度下的切削形态示意图;(b1) (b2)是100 nm切削深度下的切削形态示意图;(c1) (c2)是150 nm切削深度下的切削形态示意图
在图3(a1)中,单晶硅在切削过程中呈现粉末状切屑,这是由于切削深度太小导致的。但是虽然在三种模型中,此模型的切削深度最小,但是在这个模型的最终加工表面上存在更广泛的材料残留和加工下表面的变形。最终加工表面表现最明显的要在进口处,由于刀具挤压作用,单晶硅塑性域塑性变形造成材料凹坑突变(如图3(a2)所示)。在图3(b1)中,在此切削深度下单晶硅切削过程的切屑呈块状切屑,这是由于随着切削深度的增加,刀具的切削量增加,在不同的切削深度,整个切削区域的切屑形成区域是不均匀的。虽然切削深度增加了,但是在此参数下的加工表面反而更加光滑,而且并没有图3(a2)所示的塑性域突变造成的凹坑,而是仅仅有一些微突起(如图3(b2)所示)。随着切削深度的增加,单晶硅的切屑形态也随之变化,如图3(c1)所示,在此切削深度下,单晶硅的切屑呈现连续的卷曲状。这是由于随着切削深度增加,塑性增加,但是并没有超过塑性域的尺寸范围,因此会产生类似于切削金属物质一样的卷曲状切屑。但是这种卷曲状切屑在实际加工中将严重影响操作安全、加工质量及刀具寿命等等,因此卷曲状切屑在实际的生产加工中并不受欢迎。并且随着切削深度的增加,加工表面可可以明显的看出材料在去除过程中的撕裂及残留(如图3(c2)所示)。并且切削深度的不同,使得切削区域的Mises等效应力的分布也极为不同。在切削厚度为50 nm、100 nm,最大等效应力从剪切面方向向两侧逐渐减少分布,材料是剪切滑移塑性流动。切削为150 nm未加工材料受力开始不均匀,最大等效应力分布在刃口与材料接触的局部区域,并且极不均匀,材料变形形态复杂。
综合考虑单晶硅不同切削深度下的切屑形态及最终加工表面状态,选择50 nm的切削深度更能满足加工的需要。
在单晶硅切削有限元模拟模型中可以清楚的看到50 nm切削深度下的最终加工表面存在塑性变形造成的突起,100 nm切削深度下的最终加工表面存在微凸起,150 nm切削深度下的最终加工表面明显的看到单晶硅去除时造成的材料撕裂。这个问题是影响单晶硅切削加工表面的质量的重要因素之一。接下来,提取了刀具在刚接触到单晶硅材料、刀具挤压材料,造成材料的塑性变形、在刀具的挤压作用下,材料撕裂,直到单晶硅材料断裂成屑的动态过程,如图4所示。其中,图4(a)显示,由于刀具是负前角刀具,刀具的前刀面刚接触到材料,刀具前刀面对材料进行挤压,因此沿着刀具与材料挤压接触的区域造成材料产生塑性应变及高应力区域。图4(b)显示刀具的前刀面对材料进行挤压的同时刀具的圆弧半径已经对材料进行挤压切削。可以明显看出材料产生了很大塑性变形,此时的塑性变形及材料接下来的成屑过程取决于刀具沿工件上运动轨迹的剪切滑动产生的,在切削过程中在工件上形成了剪切区域。并且在后刀面接触材料时,由于后刀面的挤压作用与单晶硅材料典型的塑性域塑性属性有很大关系,材料被挤压然后变形 [18] 。图4(c)可以明显的观察到,由于刀具与工件的挤压应力引起的高度压缩区域在切削区域迫使挤压变形的材料沿着图4(b)所示的剪切区域撕裂,继而变成切屑。图4(c)单晶硅材料已经断裂成为切屑,但是在刀具切除一块材料成屑,继续切除另一块材料的过程中会造成材料的残留,这是因为刀具存在圆角半径,刀具的圆角半径处处堆积的材料明显多于其他区域,增加了材料的韧性,并且存在圆角半径的刀具并不是直接把材料剪切去除,而是圆角半径的挤压去除,材料不可避免的沿着圆弧半径滑移,造成材料的一部分残留。
3.2. 切削速度对表面完整性的影响
由于在以切削深度为50 nm的单晶硅切削表面质量最好,因此本研究以定切削深度为50 nm,根据研究文献表明,50 nm仍然在单晶硅塑性域的范围内,并不会引起单晶硅大规模的脆性裂纹破坏。以切削速度为变量进行单因素的切削有限元模拟研究单晶硅材料的切屑状态和表面加工状态 [19] 。
三个图像分别显示了不同切削速度下的单晶硅材料的切屑形态及最终加工表面状态(包括稳态切削阶段和切入侧不稳定切削区域的状态),每个切削区域的形态都随着切削速度的变化而变化。图5显示切削速度为50 mm/s单晶硅切削模拟表面形貌,如图所示,在切入侧不稳定切削阶段,有少许的材料残留以及表面波动,这是由于刚开始切削时,刀具与材料相互摩擦,造成材单晶硅材料的塑性流动。再加上刀具刚切入时,切削力突然增大,造成刀具与材料之间的相互作用增大,因此造成切入侧加工表面不平稳。

Figure 4. Chip formation process during contact fracture between monocrystalline silicon and cutting tools
图4. 单晶硅与刀具接触断裂成屑过程
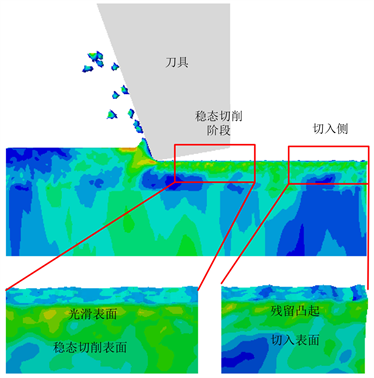
Figure 5. Simulated surface morphology of monocrystalline silicon cutting at a cutting speed of 50 mm/s
图5. 切削速度为50 mm/s单晶硅切削模拟表面形貌
图6显示切削速度为100 mm/s单晶硅切削模拟表面形貌,在切削速度为100 mm/s时,最终加工表面与切削速度为50 mm/s的单晶硅切削模拟加工表面大致相同。同样在切入侧存在残留凸起,最终加工表面较为光滑。
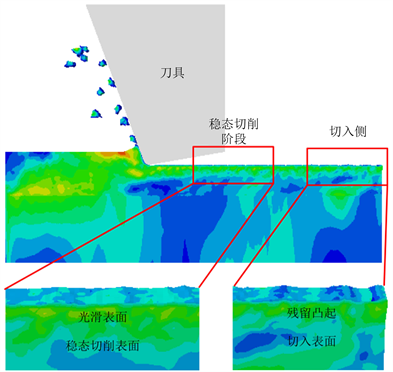
Figure 6. Simulated surface morphology of monocrystalline silicon cutting at a cutting speed of 100 mm/s
图6. 切削速度为100 mm/s单晶硅切削模拟表面形貌
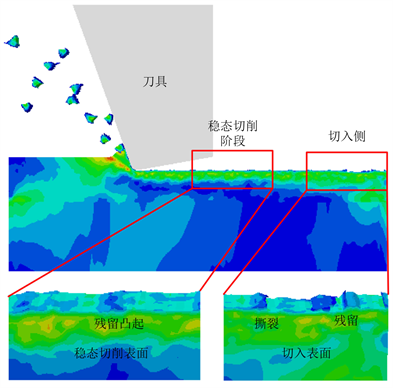
Figure 7. Simulated surface morphology of monocrystalline silicon cutting at a cutting speed of 150 mm/s
图7. 切削速度为150 mm/s单晶硅切削模拟表面形貌
图7显示切削速度为150 mm/s单晶硅切削模拟表面形貌,在切削速度为150 mm/s时,最终加工表面与切削速度为50 mm/s的单晶硅切削模拟加工表面有很大不同。具体表现在切入侧的材料撕裂和残留以及最终加工表面突起更加明显。在切削速度为150 mm/s时,材料的去除原因主要是通过减小塑性而增加脆性。由于刀具的切削刃在切削过程中渗透进单晶硅材料表面,对应于较脆的切屑形成。因此切入侧的材料直接撕裂,不会产生很大的塑性变形的塑性流动。当在切削过程中,切削速度超过某一临界值时,塑性变形增强导致材料流动剧烈,以至于导致材料微裂纹形成和扩展。并且随着切削速度的增加,材料的变形时间将变得更加短暂,甚至来不及有很大的塑性变形单晶硅就开始断裂。
4. 结论
本文在切削数值模拟过程中,通过建立切削模型,分别对不同的切削深度和切削速度进行模拟仿真,研究了切屑形态以及加工表面形貌,并对刀具与材料接触直到单晶硅动态断裂成屑过程以及最终加工表面材料残留情况进行了详细的解释。
1) 对不同切削参数下加工表面形貌进行分析,切屑形态随着切削深度的增加而从粉末状、块状逐渐演变成卷曲长条状切屑。这是由于单晶硅在塑性域切削时,50 nm切削深度下,单晶硅容易诱发塑性撕裂,导致粉末状切屑形态,并且随着切削深度的增加,切削表面质量呈现出低–高–低趋势。
2) 刀具与材料接触在挤压过程中诱导材料塑性大变形,并且产生剪切应力带。在刀具的继续挤压下,切屑沿着剪切应力带在前刀面剪切滑移,断裂成屑。由于圆弧半径的存在,材料是挤压断裂,并不是直接剪切去除,因此一部份材料随着圆弧半径滑移,残留。
3) 在切削过程中,切削速度超过某一临界值时,塑性变形增强导致材料流动剧烈,导致材料微裂纹形成和扩展。