1. 引言
汽车制造业的生产总值和利润占装备制造业的一半,去年我国汽车出口量超越日本成为世界汽车出口第一大国,当前汽车行业正在从燃油汽车向新能源汽车转型,产品的更新换代速度在不断加快,这就对汽车的研发设计效率提出了新的要求,汽车生产制造过程中的四大工艺有冲压、焊装、涂装和总装,其中的一个重要环节就是焊装 [1] 。
传统的焊装夹具设计方法主要依托于设计人员丰富的设计经验,该过程需要耗费较大的人力和物力,且效率较低,难以满足当前汽车生产速度的要求。为了提高焊装夹具设计效率,国内外学者对焊装夹具设计进行了大量研究。天津大学卢文轩针对复杂夹具存在组装效率低、规范化程度低等问题,构建夹具实例多层次型划分,并利用夹具编码对装配特征属性进行分析,提高了案例检索效率,实现了组件与元件的快速装配 [2] ;烟台大学的于万诚为了缩短夹具设计前置时间,利用已有的夹具三维装配模型进行新的夹具设计,提出了三维装配模型参数化反问题的概念 [3] 。国外针对于汽车焊装夹具的研究要早于国内,Zahid Faraz等人对车身金属板件设计了可重构夹具,可用于车身的定位,很好地限制了车身在焊接时的变形和位移,提高了夹具的通用性和复用率,为使用同种夹具为多种型号白车身进行定位提供了可能 [4] ;Kumar等人运用案例推理技术,并在此基础上对实例自动设计与修改进行研究,使用特征识别技术来对工件的设计信息进行提取加工特征 [5] ;Nasr等人提出了一种基于几何功能约束的搜索策略来选择定位和夹持特点的组合夹具设计系统 [6] 。
汽车焊装夹具相关研究有很多,研究方法各不相同,借助CATIA二次开发提高设计效率的研究较少,本文在已有的研究基础上,针对现阶段焊接夹具设计过程中出现的周期长,复用率低,设计难度高,工作量大等问题,以汽车行业应用最为广泛的CATIA软件作为三维建模平台,在.NETFramework的开发框架中,以C#语言进行系统开发,实现夹具的参数化设计和辅助设计功能。
2. 焊装夹具的作用与组成
2.1. 焊装夹具对车身的作用
白车身(body in white)相当于汽车的骨架,如果按照车身术语标准和教科书上的定义的话,白车身是车身结构件及覆盖件焊接总成,并包括前翼板、车门、发动机罩、行李箱盖,但不包括附件及装饰件的未涂漆的车身。还有一种定义是,白车身是完成焊接但未涂装之前的车身,不包括四门两盖等运动件。焊装夹具主要完成对车身的定位、夹紧、支撑等工作,以保证整个焊装过程的进行,图1为车身焊装时的结构。
1-车身,2-BASE板,3-焊装夹具,4-焊枪
Figure 1. Body welding structure
图1. 车身焊装结构
2.2. 焊装夹具的组成
夹具基板、夹紧机构、定位装置还有辅助系统这四部分构成了汽车的焊装夹具。夹具底板(BASE)是放置夹具元件、自动焊枪、举升器等夹具组件的底盘。夹具底板是焊接夹具的基础元件,它的精度直接影响定位机构的准确性;定位装置是由固定销、插销、移动销等五类工件所构成的。定位元件必须要有非常强的刚性和硬度,不然频繁使用汽车焊装夹具会造成元件的磨损,为了可以及时快速修复定位元件,对夹具提出了柔性的要求,要尽量使主定位元件是可以替换的 [7] ;夹紧机构分为快速夹紧机构与气动夹紧机构两种,这两种夹紧机构各有自己的特点。在一些对于精度要求比较低的焊接件里面,定位和夹紧能够同时实现,这样就不需要专门的定位元件,多出的空间可以使用其他机构;常见的辅助机构包括举升机构、旋转机构、翻转机构、滑台等。
3. 系统的可行性及总体架构
3.1. 系统的可行性
CATIA是一种广泛用于CAD (Computer Aided Design)和CAM (Computer Aided Manufacturing)的软件嵌套,由法国达索系统公司开发,CATIA二次开发是利用该软件的开发工具和接口,对CATIA进行定制和扩展,以满足特定的设计和制造需求,广泛的应用于航空航天、汽车等各种领域,本系统通过Automation 接口对CATIA进行二次开发,利用CATIA对焊装夹具进行参数化设计,该软件不仅提供了系统参数,同时设计人员也可以通过用户参数自行定义新类型的参数,并借助公式等工具将其与系统参数建立关系,从而通过用户参数来驱动系统参数,以便进行快速的设计变更和参数化建模。CATIA软件中的参数非常全面,除了常用的几何参数如点线面,物理参数如长度、温度、速度等,还有无量纲参数,字符型参数、布尔型参数等 [8] 。
3.2. 系统的总体架构
基于系统的便捷性,实用性及数据传输的安全性考虑,本系统综合了车身焊装夹具设计流程的特点,现代计算机信息技术和数据存储技术来设计系统架构。系统基于界面层、业务逻辑层、和数据访问层的三层架构模式。
1) 表示层
表示层主要表现为用户使用的客户端界面,基于Visual Studio开发环境中的Winform应用,用户通过界面的操作发出指令或者触发事件与系统交互,后台响应用户指令触发相应的CATIA执行对应的操作。
2) 业务逻辑层
业务逻辑层主要实现对用户模型的调用修改,权限管理及通过CATIA二次开发技术实现的夹具设计,里面包括夹具方案规划、定位点特征提取、实例参数化设计、工装辅助设计等功能。
3) 数据访问层
数据访问层主要实现数据资源的访问,数据库底层存储的为夹具知识库的基础信息。本系统采用MySQL数据库作为数据存储,MySQL以其开源性、体积小和高效性等特点得到广泛应用 [9] 。通过界面层对数据库访问,确保了数据信息实时更新和扩展。
3.3. 系统运行流程
用户通过登录界面进入系统后,进行选项的初始化工作,之后打开车身工艺文件,对工艺信息进行提取,对用户选择的RPS信息进行解析保存,然后系统打开工艺文件对应的车身三维模型对RPS信息进行快速创建,然后给出对应的装夹方案进行规划,并添加对应的夹头或定位装置,然后根据用户输入的信息得到夹具解决方案,在不满足位置要求或者存在干涉的情况下,对匹配到的单元实例进行基于尺寸约束的参数化的设计来对干涉位置进行规避,调整实例与车身的安全距离,实现自适应的参数化设计。在整个过程完成后,对于一些常见的重复性的操作,还开发了工装智能辅助设计功能,包括零件属性赋值、BOM信息导出等。图2为车身夹具参数化设计的系统的运行流程。
4. 基于参数化设计的夹具尺寸调整
4.1. 夹具单元实例的参数化建模
传统的参数化建模往往针对单个零件,但是对于整个成熟夹具单元实例模型而言不需要针对单个零件定义参数化的模型,而是在整个完整的单元装配体模式下进行结构尺寸参数化定义。CATIA对模型参数化的构建提供了两种方式:纯粹的二次开发程序驱动参数化和变量驱动参数化。前者使用Automation开发中提供的造型接口来对模型特征进行建立,在进行特征建模的同时将模型特征相对应的参数信息用作API接口的属性,构建模型的过程才是该种模式的主要内容,参数信息知识模型构建过程中的变量,该方法适用于原始的建模方式,不需要获取工程模板,但是其工作量较大 [10] 。变量驱动的参数化模型的构建只需要获取标准模板文档中的变量,通过给变量赋值来实现标准模板的参数化驱动,这种方式的代码量不大只需要获取变量属性即可,而且实例库中的实例刚好可以用来当做标准模板,免去了构建大量标准模板所耗费的时间,因此本系统采用变量驱动的参数化来作为单元调整求解的手段。图3展示两种方式的区别。
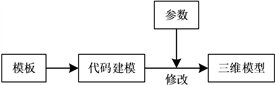
(a) 程序驱动建模 (b) 变量驱动建模
Figure 3. Difference between the two parameter-driven methods
图3. 两种参数驱动方式的区别
不同类型的夹具单元模型,构建的参数会存在一定侧差异,以单点压紧单元中定义的尺寸变量为例,我们能得到与其相关的三维模型中的参数变量结果如图4所示。
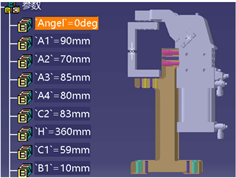
(a) 尺寸参数定义 (b) 尺寸对应的参数变量
Figure 4. Parametric model of single-point clamping unit
图4. 单点夹紧单元参数模型
4.2. 基于尺寸约束的参数化变形设计
4.2.1. 尺寸约束关系建立
对各个尺寸对应的几何元素和零件关系进行分析,找出各个关联尺寸之间的关系,建立尺寸链关系,形成基于尺寸的约束模型。以图4中的模型为建立单元的尺寸约束关系,整个单元模型的夹紧点为基准点,根据尺寸变化的优先级一次确定主参数,首先主参数为A1,假设主参数的变化量为Δ,则和A1具备约束关系的尺寸为A3,此时应该使A3的变化量同为Δ,同时A1和A3具备正向的尺寸关系,同理A4、C2和H也具有正向的尺寸关系。
4.2.2. 尺寸约束信息存储
在获取到模型的几何参数变量信息之后将其变量存储到数据库中,将实例模型中具有关联关系的尺寸进行存储,并且存储以字符串的形式。
4.2.3. 建立模型约束
对各个约束尺寸的变化区间规则进行建立,对于实例中的每一个约束尺寸都不会是无限变化的,而是具备一个变化区间,同时对于尺寸集也具备变化的优先级。以单点夹紧单元模型为例,各个尺寸的变化范围如表1所示,根据这些尺寸的变化来建立模型的变化范围。
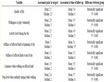
Table 1. Model constraint relationships
表1. 模型约束关系
4.3. 模型实例优化
夹具实例单元尺寸参数变化时,可能会与其他组件发生干涉,为了避免干涉情况,保证夹具实例单元与车身钣金件、焊枪及其他夹具单元的位置关系在安全范围内,需要对夹具实例单元进行静态干涉检查。静态干涉检查是指在装配体结构形式下,检查装配体的各个零件之间的相对位置关系是否存在干涉,当存在干涉时,以不同的颜色显示干涉类型、干涉部件、干涉量等 [11] 。图5为干涉检查。

(a) 干涉检查信息输入 (b) 干涉检查结果
Figure 5. Interference check
图5. 干涉检查
当夹具单元与其它组件产生干涉时,对夹具单元进行尺寸参数修改或者旋转角度修改,再继续进行干涉分析,在尺寸和角度变化范围内,直至夹具单元找到合适的位置。但是在实际过程中,夹具单元参数数量多且范围大,以参数A1为例,从高到低的这么多数没进行一次参数修改都要进行干涉分析,这种顺序修改寻找最优解的效率极低。为了能够提高效率,本系统采用二分法对夹具单元进行修改,判断A1处在最低值、最高值的干涉情况,若最高值不存在干涉,最低值存在干涉时,取中间值继续进行判断干涉情况;若最低值最高值都存在干涉,则根据参数优先级关系,修改参数A2,实现具体流程图如图6所示。
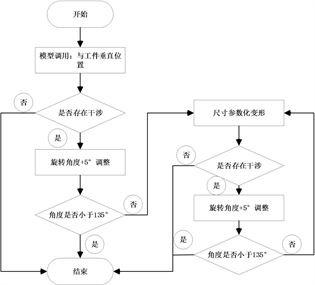
Figure 6. Parametric deformation adjustment process
图6. 参数化变形调整流程
5. 实现案例
首先进入到初始化界面,选择正确的二维工艺文件图,同时选择格式列表,工具信息和工具版本,然后系统自动打开该文件,并将CATIA软件嵌入到系统界面当中。图7为模型创建后界面。
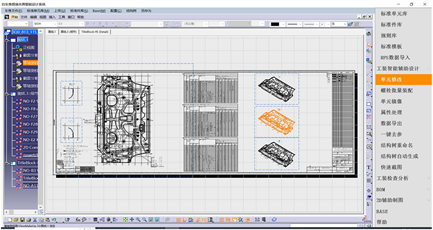
Figure 7. Interface after model creation
图7. 模型创建后界面
进入到二维工艺文件之后就要对夹具方案进行规划,包括定位点信息解析,定位点特征的自动创建以及夹具方案的输出,首先系统根据用户输入的组名来获取得到夹具单元所在组的信息,包括定位点的位置、方向等信息,然后再根据用户输入的气缸信息和其他参数与系统创建的知识库中的案例对比,得出合理的方案,对不符合条件的实例进行参数化设计操作,来完成自适应设计。图8展示了其运行过程。
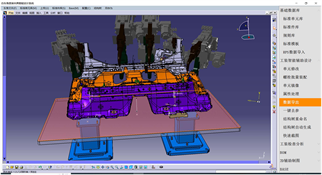
(a) 参数化求解 (b) 最终输出方案
Figure 8. Fixture design process
图8. 夹具设计过程
6. 结论
在汽车制造行业中,车身焊装夹具是整个车身制造工艺中重要的组成部分,每一代的车型升级过程中,焊装夹具的重新设计要占据很长时间,本文基于CATIA软件进行二次开发,进行白车身焊装夹具设计系统的开发和参数化研究,并进行系统测试,得出了以下结论:
1) 当前汽车制造业中焊装夹具设计存在复用效率差、设计效率低等问题,白车身焊装夹具设计系统可以集成不同的夹具设计方法,缩短企业研发周期。
2) 基于尺寸约束的参数化设计可以在不满足装夹工况的条件下通过参数修改实现自适应设计,并通过干涉检查验证方案的合理性。
3) 零件属性赋值和BOM信息导出等车身夹具辅助设计功能可以减少一些重复劳动,提高产品设计效率。