1. 引言
自后注浆技术在委内瑞拉Maracaibo大桥工程的应用以来 [1] ,距今已有半个多世纪的研究历史。目前随着后注浆技术的发展和应用不断深化,在注浆方式上可分为开式注浆和闭式注浆两大类 [2] [3] 。然而,单一的注浆方式存在着一定的问题:1) 开式注浆方式虽然在提升桩基承载力方面具有一定效果,但其浆液的可控性较低,且单桩承载力的波动性较大,这些因素使得实际注浆效果难以达到设计要求 [4] ;2) 闭式注浆法虽然能提高承载能力,但由于桩底的胶囊限制了大部分浆液向土层的有效渗透,因此其注浆效果不足;同时,浆液与土体难以形成有效的结合体,这导致了桩基承载力的波动性增大。为此,复合式后注浆技术应运而生,并被应用于实际工程中。
复合式后注浆技术兼顾了开式和闭式注浆的优点,创新性地在桩端引入了中空钢板胶囊,同时在其上设置环形挡板,共同形成一个环形约束结构,实行“开式–闭式–开式”循环的注浆技术 [5] 。目前国内许多学者通过现场试验、室内模型试验、有限元模拟和理论计算等方法研究了复合式后注浆对桩承载特性的影响。张晓华等 [6] 通过太原西北二环高速公路桩基工程项目的现场试验分析了复合式后注浆钻孔灌注桩的承载性能,并通过数值模拟探讨了注浆量、注浆体强度及长径比对承载力的影响规律;牛浩宇等 [7] 通过室内试验探讨了桩端开式、闭式、复合式注浆对桩基承载力的影响,并分析了桩端浆液压力在注浆过程中的产生和消散过程;周亚龙等 [8] 基于现场试验在球形扩张理论的基础上提出了针对复合式后注浆钻孔灌注桩荷载沉降关系的计算方法;张升进 [9] 研究了不同注浆量下桩端复合式后注浆钻孔灌注桩的承载特性,同时通过有限元软件模拟了长径比、地层强度等对桩基承载性能的影响。
当前,对于复合式后注浆钻孔灌注桩的研究多集中在现场试验,室内模型试验研究较少。同时,对于复合式后注浆钻孔灌注桩,注浆压力是影响注浆效果的关键因素之一,它直接关系到注浆能否有效改善桩基性能,促使浆液更远距离地扩散到桩周土体中,使得桩周土体的密实度提高,优化土体结构,改善大范围土体性质,从而提高桩体的承载能力。因此,本文通过室内模型试验,在单一注浆量的条件,分析了不同注浆压力下复合式后注浆钻孔灌注桩的轴力和侧摩阻力分布以及桩侧阻和端阻的发挥性状,进而探讨了注浆压力对复合式后注浆钻孔灌注桩承载性能的影响。
2. 室内试验
2.1. 模型试验装置
本次模型试验场地位于兰州交通大学岩土大厅,模型箱长1.2 m,宽1.2 m,深1.2 m,模型桩的布置见图1,模型箱内侧壁与试桩间的距离满足要求,可以消除边界效应 [10] ;此外,模型箱侧壁为亚克力板或者钢板,可以承受较大的荷载而不产生变形。模型试验共设置6根试桩,其中2根为试注桩,1根为未注浆桩,编号为S1;3根为复合式后注浆桩,编号为S2~S4,注浆压力分别为0.1 MPa、0.3 MPa和0.5 MPa。
模型试验试桩均采用直径为40 mm、长度为0.8 m、长径比为20的铝合金钢管空心桩。为增大桩端与地基土的接触面积,防止水泥浆液进入管桩内部,在铝管桩底部使用2 mm厚的铝片进行封底。沿模型桩的桩身以0.1 m的间距纵向对称布置应变片,每根单桩需布置16个应变片,用502胶水将应变片粘贴在准备好的模型桩上,待粘贴牢固后使用硅橡胶包裹应变片防止其受损。
模型试验用土选用兰州黄土,根据土工试验可得其基本物理力学参数:最大干密度为1.76 g/cm3,最优含水率为16.6%,黏聚力为29.6 kPa,内摩擦角为23.7˚。填筑过程中,控制填土含水率为10.8%左右,压实度为80%。采用分层填筑的方式,每层10 cm均匀填于模型箱内。每一层填筑完成后需用夯锤压实并刮毛后,方可铺设下一层土;填筑至距模型箱底35 cm时,完成桩端土铺设。通过拉线定位确定好模型桩的设置位置,使用工具在每个桩位处挖掘5 cm深的小洞,确保模型桩底端能够正确放入预定位置。继续填土压实,直至填土高度达到100 cm。
2.2. 复合式注浆过程
本次模型试验采用课题组内设计的压力注浆系统,该系统的关键组成部分包括了空气压缩机、压力容器、注浆管、水泥浆料、真空泵、调节阀门以及排气阀,整个注浆系统如图2所示。模型试验注浆材料选用专门的水泥压浆料,基于已有的模型试验成果,注浆量选取3 L,水灰比为0.8,为防止浆液分层和沉降,确保注浆过程中浆液的均匀性,在水泥浆液中掺入5%的膨润土,以取得更好的注浆效果。
注浆时先打开注浆筒盖,倒入预定量的水泥浆液。此时,测量并记录浆液平面到注浆筒顶部的距离,以便于计算注入的浆液量;盖上筒盖并紧固螺栓,确保注浆筒密封,以防浆液泄漏;开启阀门,让水泥浆液流入并填满注浆管,直至浆液接近阀门位置。然后关闭阀门,防止空气进入系统;启动空气压缩机,将注浆筒内的压力提升到所需水平,然后关闭空气压缩机,以保持压力稳定。
需要注意的是,整个注浆过程中要不断摇晃压力罐以防止水泥浆液分层离析。在开式注浆过程结束后,应立即封闭注浆阀门,以避免浆液被空气压送至桩基外围。完成闭式注浆后,应等待一段时间再移除阀门,避免浆液重新返入注浆管中。整个注浆过程应尽量保持注浆压力一致,使得注浆保持匀速。整体注浆过程见图3。
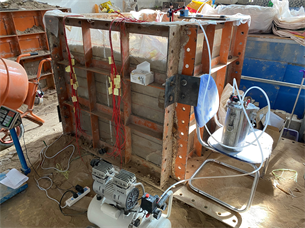
Figure 3. Composite post-grouting of model pile
图3. 模型桩复合式后注浆
2.3. 静力加载过程
注浆10 d后进行静载试验,以确保水泥浆液与模型土固结。在加载开始之前,应使用工具对外露的注浆管进行处理,确保桩顶的桩头平整。整个静载试验通过千斤顶加反力梁的方式进行加载,加载过程中应时刻注意桩顶百分表的读数。采用分级加载的方式,预估未注浆桩的极限承载力约为500 N,因此分级荷载为50 N;复合式后注浆钻孔灌注桩的极限承载力约为2000 N,因此分级荷载为200 N。
试验采用慢速维持荷载法,在施加每个荷载级别之后,分别在第5分钟、第15分钟和第30分钟记录桩顶的位移数据,随后每隔30分钟进行一次记录。当桩顶沉降量每小时不超过0.1 mm,并且连续两次观测值较为接近时,即可认为桩基沉降趋于稳定,可以施加下一级荷载。
当模型桩发生以下任一情形时,可认定为已经发生破坏,试验可以终止 [11] :
1) 在特定荷载级别下,桩顶的沉降量达到前一荷载级别下沉降量的5倍;
2) 在某特定荷载作用下,桩顶的沉降量为前一级荷载沉降量的2倍,并且在24小时之后沉降量未表现出稳定趋势;
3) 桩顶沉降量超过40 mm。
3. 模型试验结果与分析
3.1. 荷载–沉降关系
图4是4根模型试桩的荷载–沉降关系曲线,从图中可知,4根试桩S1、S2、S3、S4的极限承载力分别为550 N、1400 N、2000 N和2400 N,对于3根复合式后注浆钻孔灌注桩,在荷载–沉降曲线前半段,随着荷载的增加,桩顶位移增长较为缓慢,此时的荷载沉降呈线性关系。随着桩顶荷载的增加,荷载–沉降曲线逐渐呈现非线性,并出现明显拐点并达到了极限承载力。通过对比可以看出复合式后注浆能显著提高桩基承载能力,提高幅度在255%~436%之间;同时,极限荷载下4根试桩S1、S2、S3、S4的沉降分别为19.13 mm、11.83 mm、10.84 mm和12.05 mm,由此可见,复合式后注浆能有效控制沉降。
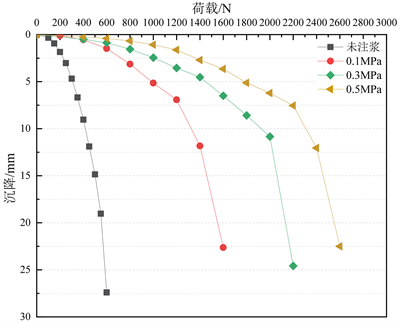
Figure 4. Load-settlement relationship curve of model pile
图4. 模型桩荷载–沉降关系曲线
图5是不同注浆压力下极限承载力的提高幅度,从图中可知,模型桩的极限承载力随着注浆压力的增加而增大,但其提高幅度并不是线性的。当注浆压力过大时,承载力提高幅度减小,这是因为过大的注浆压力使得桩端胶囊形成的空腔过大,水泥浆液不足以填满空腔,同时过高的压力导致浆液在土体中扩散迅速,影响浆液与土体的有效结合。因此,当注浆量一定时,存在一个最佳的注浆压力范围,可以实现承载力的最大化提升。
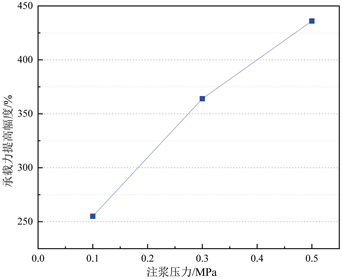
Figure 5. Increase in bearing capacity of model pile
图5. 模型桩承载力提高幅度
3.2. 桩身轴力分析
根据桩身应变值,计算得到各级荷载下复合式后注浆桩的桩身轴力分布如下。
图6为3根复合式后注浆模型钻孔灌注桩在各级荷载作用下的桩身轴力图。由图可以看出,随着桩顶处外部荷载的增大,桩身轴力在整体趋势上随着深度的增加而逐渐减小。轴力曲线的斜率是分析桩侧摩阻力变化的关键指标:斜率越大,意味着在相邻两测点之间的轴力差异较小,表明该段桩身的侧摩阻力较小;通过对比三幅轴力图,可以看到随着注浆压力的增加,其轴力曲线斜率出现明显变化的高度距桩端越来越大,同时上半部分曲线斜率较下半部分大,这是因为在第一次开式注浆过程中,浆液在注浆压力作用下发生上返 [7] ,同时从图6也可以看出,注浆压力增大,轴力急剧衰减范围越大,这是因为上返高度变高,桩端附近及桩侧上返区的土体抗剪强度增加,提高了桩身的桩侧摩阻力,其桩身轴力在竖向的衰减也就越来越明显。
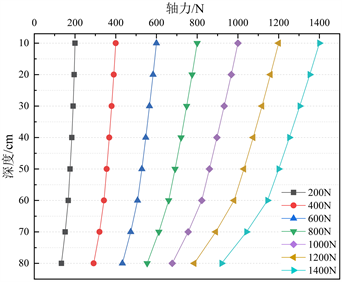
(a) S2试桩
(b) S3试桩
(c) S4试桩
Figure 6. Axial force distribution of model pile under various loads
图6. 各级荷载下模型桩桩身轴力分布
3.3. 桩身侧摩阻力分析
计算得到复合式后注浆桩各段的平均桩侧摩阻力,并绘制出3根试桩侧摩阻力沿桩身的分布图。
图7为3根复合式后注浆模型钻孔灌注桩的沿不同深度的桩身侧摩阻力分布。由图可以看出,随着桩顶外部荷载的增加,同一桩身截面处的桩侧摩阻力不断增加,在整体趋势上,桩侧摩阻力沿着桩身随着深度的增加不断增大。由于荷载在桩身顶部先产生作用并逐渐向下传递,因此当桩顶作用荷载较小时,桩身的上半部分侧摩阻力较早发挥作用;当桩顶荷载逐渐增加至极限时,桩身侧摩阻力逐渐趋于稳定。
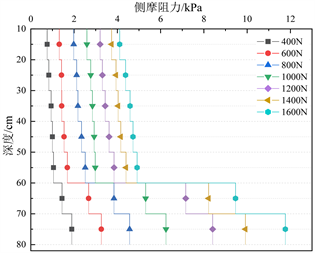
(a) S2试桩
(b) S3试桩
(c) S4试桩
Figure 7. Average side resistance distribution of each section of model pile under various loads
图7. 各级荷载下模型桩各段平均侧摩阻力分布
同时对比三张图可知,复合式后注浆钻孔灌注桩桩侧摩阻力在一定的范围内出现了突增,这是因为水泥浆液在注浆压力的作用下沿着桩身发生了上返,显著增强了桩侧土体的抗剪强度,水泥浆液的注入使得桩侧土体受到挤压,桩侧土体对桩身的法向应力增大,从而提高了桩侧摩阻力;同时,桩侧摩阻力增强段的高度随着注浆压力的增加而增加,这是因为更高的注浆压力有助于克服地层中的阻力,浆液更容易被压入土层更高的部分,提高浆液在土层中的流动性和扩散范围。
3.4. 桩侧阻力发挥特性
由于本次模型试验使用铝管作为模型桩体的材料,而铝管弹性模量较大,桩身即使在荷载作用下也只会发生微小的形变,因此假定桩身相对位移等于桩顶位移。
图8为不同注浆压力下的复合式后注浆模型桩侧摩阻力发挥性状。由图可以看出,当桩–土相对位移较小(2 mm)时,桩侧阻力发挥迅速。这是因为注浆后浆液在桩侧土体中迅速扩散,增强了桩侧与土体的粘结强度,提高了桩侧的有效应力,从而加快了桩侧摩阻力的激发。此时的荷载较小,尚未对桩端土体产生变形和压缩,因此桩端阻力的发挥相对较慢。
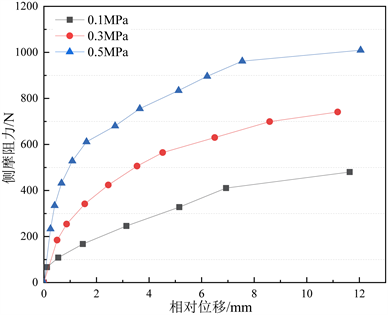
Figure 8. Relationship curve in model pile between side resistance and relative displacement of pile-soil
图8. 模型桩侧摩阻力与桩–土相对位移的关系曲线
当桩–土相对位移达到2 mm时,在0.1 MPa、0.3 MPa和0.5 MPa下的侧阻分别达到180 N、270 N和620 N,注浆压力越大,侧阻的发挥也越快。这是因为增大注浆压力有助于浆液更深入、更均匀地渗透到周围土体中。这种渗透作用加强了桩身与周围土体之间的粘结力,从而使桩侧阻力更快达到最大值。
当桩–土相对位移达到8 mm时,桩侧阻力的发挥趋势逐渐趋于平缓。这是因为当荷载达到一定水平后,桩土之间的摩擦力和粘结力达到饱和状态,即使荷载继续增加,由于摩擦和粘结强度已经达到其物理极限,其桩侧阻力的增长趋于平缓。
3.5. 桩端阻力发挥特性
图9为不同注浆压力下复合式后注浆模型桩桩端阻力的发挥性状,由图可以看出,当桩–土相对位移较小(2 mm)时,不同注浆压力下的桩端阻力发挥曲线大致相似。这是因为在较低的荷载下,桩端土体的变形和应力状态受到注浆作用的效果不明显。由于桩端阻力的发挥更多依赖于桩端土体的承载能力和变形特性。在低荷载条件下,桩端土体的变形较小,因此注浆压力对其影响有限,对复合式后注浆钻孔灌注桩端阻力的发挥不如桩侧阻力敏感。
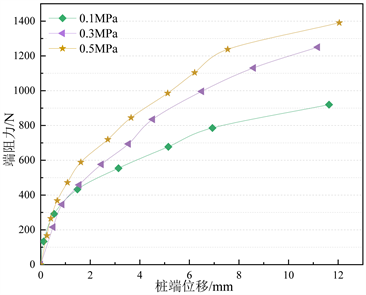
Figure 9. Relationship curve in model pile between pile tip resistance and pile tip displacement
图9. 模型桩桩端阻力与桩端位移的关系曲线
当桩–土相对位移达到8 mm时,相较于桩侧阻力发挥逐渐趋于平缓,桩端阻力的发挥仍然有很大的提升空间。这是因为桩端阻力与桩端土体的压缩和承载能力有关,随着荷载的增加,桩端土体的变形和压实程度逐渐增大,因此桩端阻力的提升潜力更大,且在更高的荷载下仍有显著的提升空间。
4. 结论
1) 桩端复合式注浆技术能有效提高模型桩的承载力,提高幅度在255%~436%之间。承载力的提高幅度与注浆压力呈正相关且非线性。在单一注浆量的情况下,存在最有效注浆压力能实现承载力的最大化提高。
2) 复合式后注浆模型桩桩身轴力沿着桩身随深度的增加而减小,在浆液上返界面出现突变;在注浆作用下,浆液上返增强了桩侧土体的抗剪强度,提高了桩端及浆液上返段的桩侧摩阻力;桩侧摩阻力增强段的高度随着注浆压力的增大而增加。
3) 复合式后注浆钻孔灌注桩端阻和侧阻的发挥并不一致。对于桩侧阻力,当桩–土相对位移较小时,桩侧阻力发挥迅速,注浆压力越大,侧阻的发挥也越快。当外部荷载达到一定水平后,桩侧阻力发挥逐渐趋于平稳;对于桩端阻力,当桩–土相对位移较小时,不同注浆压力下的桩端阻力发挥曲线大致相似,当桩–土相对位移较大时,桩端阻力的发挥仍有较大的提升空间。
基金项目
甘肃省优秀研究生“创新之星”项目(2023CXZX-529)。