1. 引言
本文分别基于AnsysWorkbench和Pro/Mechanica对一长为4500 mm的风力发电机叶片,叶片厚为0.02 m,其中叶根端固定,压力面承受20 Pa风压的叶片进行静态机构分析和模态分析,得出其应力、应变以及挠度、疲劳特性等参数。在整个分析过程中,选择材料为系统默认的不锈钢材料及自定义铝合金材料,其中铝合金材料特性为:弹性模量E (75 × 103 MPA)、泊松比μ (0.25)、密度(2.7 g/cm3)。模型如图1。
2. 基于Ansys对叶片的静态机构和模态分析
2.1. 静态结构分析
2.1.1. 材料属性的定义
要对发电机叶片进行Ansys分析,首先必须在项目工作栏中创建任务栏,并且把工具栏中的Static Structure拖入其中,建立和项目A相关联的项目B。然后,必须对零件(此处即发电机叶片)进行材料定义,方能进行后续的分析工作。本文分别把材料定义为默认属性下的结构钢和自定义铝合金材料(即弹性模量E = 75 × 103 MPA、泊松比μ = 0.25、密度 = 2.7 g/cm3)。
2.1.2. 网格划分
在定义了材料属性以后,需要在Ansys中对叶片进行网格划分,在划分网格是要注意,首先要为网格划分添加控制尺寸,此处为其添加的Element Size为1 mm。在控制尺寸添加以后,只要执行Mapple Face Meshing (绘制面网格)指令即可画出合适的网格。在设置完成以后,只需对模型进行网格处理便会自动生成划分的网格,网格效果如图2所示。
2.1.3. 施加载荷与约束
如果要对一个物体(此处为风力发电机叶片)进行一系列求解计算,在划分网格之后,就要对物体进行约束的添加和载荷的施加。因为考虑到整个风力发电机叶片的受力面只有前端的那一个迎风面,因此,载荷只施加在这个表面上面(如图4),且联系到实际情况以后该载荷定为均布载荷,大小按条件中给出的20 Pa来计算。同样的,根据设计的需求和实际,把固定约束加在叶片和风力发电机连接的圆端处(如图3)。
2.1.4. 结果分析
经过对等效应力、叶片结构疲劳特性、叶片疲劳结构安全按系数等数据的计算,对于自定义铝合金材料制成的叶片(即弹性模量E (75 × 103 MPA)、泊松比μ (0.25)、密度(2.7 g/cm3)),其各项分析结果如下图5~8所示。
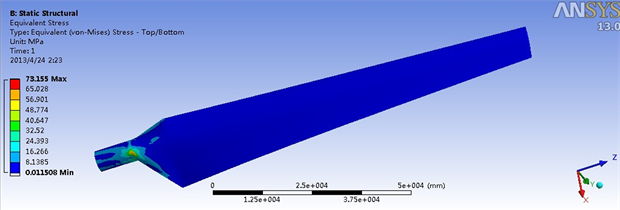
Figure 5. Custom material stress analysis contour map 1
图5. 自定义材料应力分析云图1
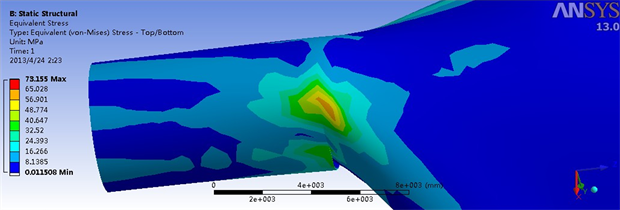
Figure 6. Custom material stress analysis contour map 2
图6. 自定义材料应力分析云图2
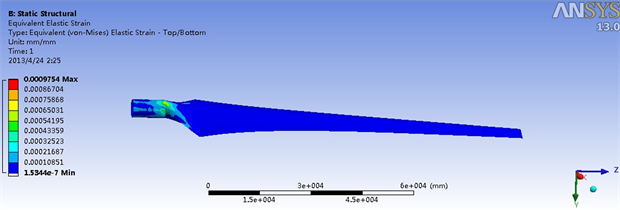
Figure 7. Custom material strain analysis contour map 1
图7. 自定义材料应变分析云图1
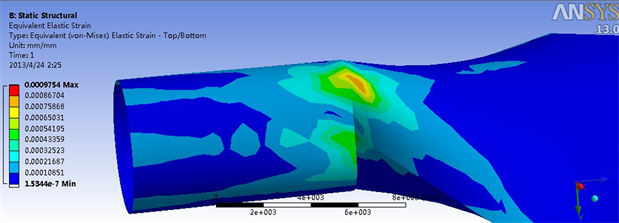
Figure 8. Custom material strain analysis contour map 2
图8. 自定义材料应变分析云图2
由以上分析可知,在转角处应力应变出于较大值,但是仍处于安全范围之内。
2.2. 预应力模态分析
在此之前,静态结构分析中已经对叶片的静力进行了求解,本节将通过对叶片的模态及有预应力的模态进行分析,得出该风力发电机叶片从第一阶到第六阶的模态振型,并且可以得出不同情况下的模型固有频率。
首先,由于是在有预应力的模态分析环境下,所以只需要在前一小节的静态结构分析的前提下再加入创建新的预应力模态分析项目(Response Spectrum),即将Response Specturm拖入项目管理区中,待项目B中的Solution呈高红亮时即可保证相关联的数据可以共享。
在完成了上面这部的工作以后,只要按顺序利用Total Deformation命令向项目树中添加模态即可,例如Total Deformation-Mode 2对应二阶模态,Total Deformation-Mode 3对应三阶模态,以此类推。设计树中的项目添加完成以后只需对每个模态进行求解即可得到各阶模态分析的结果,如图9~14,与此同时,在Mechanical图形窗口的下方,也可以观察到模型的固有频率,如图15。当整个预应力模态分析过程完成以后,风力发电机叶片的各阶模态均可以由分析结果直观的读出并记录下来,为以后使用。
本节中所做的预应力模态分析都是当风力发电机材料为自定义铝合金时候的数据(即材料弹性模量E (75 × 103 MPA)、泊松比μ (0.25)、密度(2.7 g/cm3))。
3. 基于Pro/Mechanica对叶片的静态机构和模态分析
Pro/Mechanica中对风力发电机叶片的分析
Pro/Mechanica虽然与Ansys的分析思路有相同之处,但是就如第一节中所叙述的,PRO/Mechanica有着他本身的优势,一是对简单物体的分析结果可以十分精确,二是对于非专业使用CAE软件的工程师,Pro/Mechanica无疑更容易操作上手,能够更简便得出所需要的结果。因为Pro/Mechanica的分析过程是先做好前处理工作,后续可以直接的出多个结果,所以,本节将会具体阐述整个分析的过程。
材料定义
在Pro/Mechanica中如果要对一个物体进行各项分析,第一步最适合对该物体的材料特性进行定义,因为一旦材料确定了,后续的确定属性单元,应力应变,疲劳强度等等的分析才能进行 [1] ,因此,根据本文中风力发电机叶片自定义铝合金的各项材料特性系数(即材料弹性模量E (75 × 103 MPA)、泊松比μ (0.25)、密度(2.7 g/cm3)),现进入材料属性设定页面,选择一种材料对它的属性进行编辑,例如此处的杨氏弹性模量,泊松比,密度等等参数,参数设置如图16。除此之外还可以设定拉伸屈服应力、拉伸极限应力、压缩极限应力等与材料相关的参数。另外,在材料特性确定以后,还有最后一步,就是把材料的属性赋予当前的模型,即风力发电机叶片。
壳单元设置
应用壳单元可以模拟结构,该结构一个方向的尺度(厚度)远小于其它方向的尺度,并忽略沿厚度方向的应力 [2] ,本文所分析的是风力发电机叶片,根据定义分析的时候把该叶片定义为壳单元。
在Pro/Mechanica中定义叶片为壳单元的具体过程为在菜单栏插入中选择壳单元,在选中了所有面之后根据本例中的设计要求,即叶片厚度为20 mm,材料选择为上一小节中设定的steel。
施加载荷与约束
此处所加的载荷和约束与第二章在Ansys中分析时所加的载荷与约束基本思想相同,都是在风力发电机叶片的圆端面加1个固定约束,在受风力的表面加上1个均布载荷,其中均布载荷大小为20 Pa。载荷与约束添加以后的总体模型界面如图17所示。
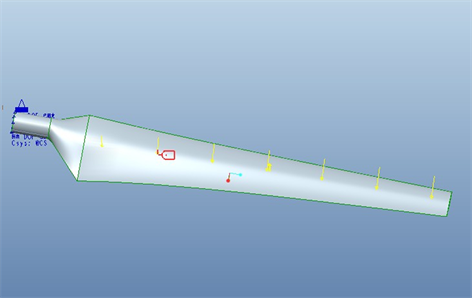
Figure 17. Pressure loads and constraints in the model
图17. 模型中的压力载荷和约束
网格划分
由于风力发电机叶片的结构分析在圆端面较为复杂,因此,在画网格时候对端面处进行细微划分,模型除端面以外处的网格可以相对放宽标准。细微画网格时需要使用AutoGem控制,此处类型选择边分部,选中左端面的各边,同时把节点数设为300个。对其进行网格划分以后,共创建了5284个元素和3804个节点。在模型上划分完的网格显示如图18。
求解计算
在准备工作一切就绪以后,只需进入分析和设计研究新建1个静态分析即可对其进行应力和应变的求解,求解以后的结果在结果窗口中可以再下拉菜单中选择应力、位移、应变能等等参数进行观察,本文选取了其中的应力和应变进行观察。
经过计算以后得出应力应变的值如图19、图20所示。
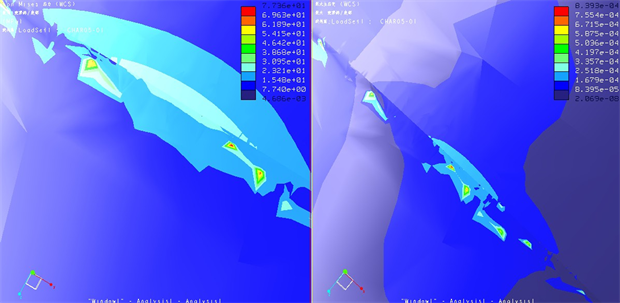
Figure 20. Stress and strain comparison detail chart
图20. 应力、应变比较细节图
用同样的方法对其施加预应力模态分析,可得出如图21所示的结果。
由应力应变的分析图可以看出,在左端面圆端处,有不是很明显的应力集中,如需对此风力发电机叶片进行优化设计,可对此处进行优化,使其强度增加。
4. 对比与优化
4.1. Ansys Workbench与Pro/Mechaniaca分析结果对比
从第二章和第三章的分析结果可以看出在Ansys Workbench中分析出的应力应变等参数与在Pro/Mechanica环境下分析出的参数相比,应力相差为4 MPa,应变相差104。
目前的有限元分析主要依赖软件如ANSYS,它在求解算法效率上有优势,但在复杂模型建模上存在局限。三维设计软件(如Pro/ENGINEER)通过数据交换解决这一问题,优化了模型建模和分析流程。Pro/ENGINEER的MECHANICA模块直接使用模型数据进行有限元分析,提升了模型一致性和分析效率。Pro/MECHANICA基于P方法,优于传统的H方法,能更精确拟合几何形状,提高计算精度,减少网格单元数目,自动收敛求解 [3] 。因此,下文使用Pro/Mechanica对风力发电机叶片进行优化。
4.2. 风力发电机叶片的结构优化
本文选择在Pro/Mechanica中对风力发电机叶片进行结构优化,经过对风力发电机叶片的工作状态和结构分析,可以看到,在与机身连接的弯曲处应力处于最大位置,因此,分别进行2种方案的优化,1) 对整个风力发电机叶片进行加厚,把原来20 mm的壁厚增加至50 mm;2) 只对连接处进行加厚,同样把20 mm的厚度增加至50 mm。分别对此两种方案进行分析,得出的结果如表1所示,模型分析结果如图22、图23所示。
分析所得结果可以看出,如果对整体进行加固即方案一,那么所得的应力和应变相对于方案二较大,但是最大位移和旋转角度都比较小。因为在第二章Ansys分析中曾经对风力发电机的叶片结构疲劳寿命和叶片结构疲劳安全系数进行过分析,在连接处容易发生疲劳变形,易发生危险,而在叶片主体处没有疲劳风险。因此权衡两个方案的利弊,可以得出风力发电机叶片的较好优化方案为对连接处进行结构加强,即加厚,具体加厚数据可以用灵敏度分析法计算出最佳结果。
5. 结论
本文采用了Ansys和Pro/Mechanica这两种有限元分析软件 [1] ,对风力发电机的叶片进行了深入的静态结构分析以及预应力模态分析。通过这些分析,我们详细比较了叶片在受到风力作用时的应力分布、应变情况、挠度反应以及长期使用中可能出现的疲劳特性。通过软件对比及选择,运用Pro/Mechanica对风力发电机叶片的结构优化进行了分析,提出了一种优化设计的解决方案。