1. 引言
随着21世纪全球经济迅猛发展,人们对高质量生活需求的大幅度增长,碳中和战略意义深远,LED作为节能、环保的照明技术,得到了人们广泛的应用,LED集成技术和微封装技术也在不断进步。随着芯片功率的不断提高,面积不断缩小,集成度越来越高,这种趋势导致了在有限体积内产生了更多的热量,若散热不及时,过多积聚的热量将导致大功率LED工作温度升高,影响大功率LED的正常工作,严重时甚至会使大功率LED失效 [1] - [3] 。
LED向小型化和大功率方向发展,大功率LED温度每升高8℃,可靠性下降10%;温度升高80℃时的寿命只有温度升高50℃时的1/6。可见温度是影响大功率LED可靠性最重要的因素之一,这就需要在技术上采取措施限制大功率LED的温度升高。
热电分离铝基板(如图1所示)是目前大功率LED常用的一种导热承载体、光学支撑和电气性能连接体,其主要热量传导路径可概括为:大功率LED→锡膏→金属基板→导热硅脂→散热器,完成一个导热散热过程。在此热量传导路径中,金属基板的导热性能与散热器的散热性能是目前学者们研究的重点内容。因此,围绕如何大幅提升金属基板的导热能力与散热器的散热能力(如图2所示)是众多学者们关注的焦点。
2. 大功率LED散热封装用高导热石墨/铝复合散热基板
随着电子元器件功率密度的不断提高,对热扩散和热沉的性能要求也越来越高。热解石墨(PG) [4] 是一种很有前途的热沉材料,因为它的导热系数大于铜的400%,而重量仅为铝的80%。然而,这种材料的各向异性分子结构意味着三个轴中只有两个轴具有这种良好的热导率。第三个轴可以比其他轴小两个数量级。这种各向异性行为,激发了人们对PG巨大热性能效益的应用研究。
PG有几种类型。Thermal PG (TPG) [5] 最常用于描述具有最高热导率的形式。理想的热性能是由于PG的晶体结构比其它任何形式的PG都具有更高的有序度。因此,它被称为高取向PG。参考用于实现这种高度有序状态的工艺,也将其描述为退火PG。除了热效益外,PG还具有比普通材料更低的热膨胀系数的优势,从而可能消除对散热器和电子元件之间的热界面材料的需求。
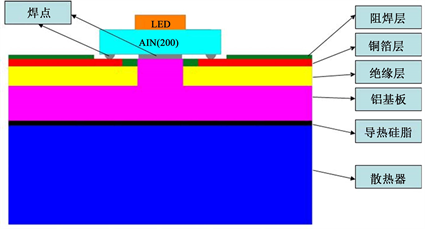
Figure 1. Structural diagram of traditional thermoelectric separation aluminum substrate for high-power LED heat dissipation packaging
图1. 大功率LED散热封装用传统热电分离铝基板结构图
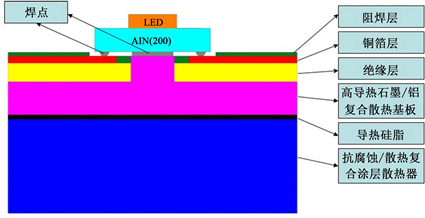
Figure 2. High thermal conductivity graphite/aluminum composite heat dissipation substrate and corrosion-resistant/heat dissipation composite coating for high-power LED heat dissipation packaging
图2. 大功率LED散热封装用高导热石墨/铝复合散热基板及抗腐蚀/散热复合涂层
高导热热解石墨(如图3所示)是热解石墨经特殊热处理过程制备获得的一种新材料,该材料高度各向异性,在面内的热导率可达1600 W/(m∙k),是金属铜的四倍以上,铝的八倍以上,而密度仅为铜的四分之一左右(<2.3 g/cm3)。高导热热解石墨是目前已知比热导最高的材料,是解决我国新一代大功率军工电子散热问题的首选材料。
尽管高导热热解石墨从比重、散热性上已经具备取代现有热管理材料的条件,但目前却鲜有高导热热解石墨在电子产品中的实际应用。主要是受以下两个因素影响:1) 高导热热解石墨属二维材料,强度低,抗弯强度不足20 MPa,尤其在二维平面方向,其剥离强度极低,这为其在实际构件的应用制造了难题;2) 高导热热解石墨难焊接,无法与电子器件实现组装。传统的焊料无法对高导热热解石墨形成良好的润湿,少数为实现高导热石墨与其它构件的连接,采用粘接的方式,但粘接界面巨大的热阻,使得高导热石墨作为热沉的传热效果明显下降。针对上述问题,少数科研工作者针对高导热热解石墨与铜、铝等传统热沉材料的连接开展了研究工作,但由于涉及的材料间物性差异巨大,大部分研究成果处于基础研究阶段,研究进展缓慢,成本高,工艺复杂,无法进行实际构件的制造。
最近的研究考察了PG在选择性热沉应用中的性能优势。在一个案例中,Dogruoz和Arik [6] 考虑了电力电子应用中翅片式热沉的优化设计。采用解析热路模型,综合考虑几何结构和材料选择的变化以及对风扇功率需求的影响,对10 kW整流器散热器的结构进行优化。他们报告说,在风扇功率为20 W的情况下,TPG将冷却系统性能指标(即每单位体积的热导率)提高了50%。这相当于热阻降低了20%。然而,Dogruoz和Arik认为,如果考虑成本和可制造性,铝可能仍然是首选,这意味着他们正在寻求TPG性能效益 > 20%的应用。
计算模型也被用来研究翅片式换热器。根据单位质量的冷却性能,使用优值图来比较几种不同材料的相对效益。与传统材料和碳泡沫相比,TPG被发现具有最高的热性能,尽管碳泡沫因其重量轻而具有优越的性能。对于0.1 mm厚度的翅片,TPG显示热阻降低约50%。我们观察到,它们的优点一般是通过使用稀疏间距的薄翅片来最大化。
除翅片式散热器应用外,Xiong等人 [7] 还对TPG作为热扩散器的性能进行了研究。实验测量了使用30 μm厚扩散器时手持设备的外壳温度。与铝相比,TPG的温度降低了16%,尽管功率增加了71%。Xiong指出,TPG在厚度方向上较低的热导率阻止了局部热点的产生,并产生了比其他材料更均匀的温度。
尽管每项研究都提供了对PG在特定应用中的性能的深入了解,但在概念或初步设计过程中使用这些信息是很有挑战性的。DanielSabatino等 [8] 试图将TPG热沉与铝热沉进行比较,并对结果进行概括,从而为一系列应用提供初步设计指导。具体而言,通过数值模拟将TPG的性能与用于散热应用的铝的性能进行比较,并使用分析模型将翅片散热器的性能进行比较。该结果确定了TPG能产生显著的热、重量或尺寸效益的几何结构和操作条件组合。结果表明,对于典型的翅片宽度,当翅片厚度小于1 mm时,翅片高度比可达到 < 0.6。如果可以制造这些厚度的翅片,TPG的使用将在类似板翅的应用中表现出最大的效益。
Richard J. Lemak等 [9] 对PYROID®HT石墨的一系列金属化方法进行了评估,这些方法适用于芯片和其他散热部件的焊接。结果表明,在二维和三维热扩散中,HT石墨可以克服非各向同性结构,其有效导热系数比铜钼热扩散器高5~10倍。在确定因温度偏移而产生的应力水平时,弹性模量与热膨胀系数一样重要。
Chih-Yung Wen等 [10] 通过实验研究了单质子交换膜燃料电池(PEMFC)中热解石墨片(PGS)的热性能。这种具有高热传导率的PGS用作热散热器,减少冷却系统的体积和重量,并降低和均匀燃料电池反应区域的温度。PGS降低了电池的最高温度,提高了电池在高阴极流速下的性能。有PGS的电池的温度分布也比没有PGS的电池更均匀。这项研究的结果表明了PGS在燃料电池系统热管理中的应用前景。
美国竞争力研究所的Shuhua Zhang等 [11] 采用有限元分析对由k Technology Corporation (kTC)制造的由APG材料和铝密封组成的k∙CoreTM样品进行评估和建模。试验得到的测试样品热导率为540 W/(m∙k),是基准铝样品(200 W/(m∙k))的2.70倍。APG“效益”被定义为APG样品和基准样品之间的温差与基准样品和环境之间的温差之比。封装后的APG的效益高达51.67%。该研究有助于更好地理解这种新型热材料如何应用于电子冷却。
美国Momentive公司的Wei Fan等 [12] 将高导热热解石墨(TPG)芯集成到绝缘金属基板(IMS)中,有望同时实现TPG的高导热性和IMS的电功能性。与传统的铜芯IMS相比,TPG芯IMS的导热系数提高了近2倍,重量减轻了30%。通过热分析发现,在稳态和功率循环下,结温显著降低(11℃),这是由于在平面和整个厚度范围内的热扩散得到改善。该研究还证明了这种TPG-core IMS结构对现有IMS生产和功率模块组装的可制造性和兼容性。TPG和IMS的集成为增加热负荷、提高可靠性、简化模块设计、降低组装成本和步骤数量铺平了一条新的封装路线。
在军用上,经过调研了解到,美国已经将超高导热退火态热解石墨材料与金属一体化复合成功应用于航空、航天领域。但该技术被美国等西方国家严格限制,我们无法查询到更多的相关信息。目前国际上只有美国的Momentive、kTC等少数公司掌握了高导热石墨与金属的一体化复合技术,并推出了系列化产品。但这些公司都对我国实行了技术封锁。
目前国内研究石墨/金属复合材料的人比较少,且研制出的石墨/金属复合材料性能很少关注机械强度。因为它有着一些难以解决的问题,比如制备它有着比较大的难点,工艺复杂程度高。目前有关碳素材料的研究热点大多放在石墨烯上,但石墨有其自己的优点,相比石墨烯,其价格低廉,产业化转移快。制备有关石墨高导热复合材料的方法有压力熔渗法,放电等离子烧结法,真空热压等。
童伟等人 [13] 使用压力熔渗法成功研制出高导热石墨/铝复合材料,石墨片的体积分数的增加可使复合材料的面内热导率明显提高,并且密度和热膨胀系数都会下降,在石墨/铝复合材料中石墨体积分数为73.4%时,它的面内热导率可达到402 W/(m∙k),热膨胀系数可降低到5 × 10−6/K,高热导率,低热膨胀系数,热学综合性能好。这种采用压力熔渗的方法有着工艺简单,造价低,适合大规模生产,而且可制备大尺寸样品。但是也有一些问题,它需要金属液体进入到增强体间隙中,这样才能提高致密度,减少孔隙,提高复合材料的性能,然而鳞片石墨增强体之间的空隙几乎没有,这样导致金属液很难进去,进而影响石墨/铝复合材料的性能。
杨海宁等人 [14] 研究了Al4C3在不同工艺条件下的生长规律,结果表明Al4C3顶端与铝基体之间的界面为粗糙界面,其生长机制为连续生长,而Al4C3的(0001)面与铝基体的界面光滑,其生长机制为沿面生长。两种生长机制在不同的生长驱动力作用下,具有不同的相对生长速率。因此在不同的材料制备工艺条件下,Al4C3的形态也表现出不同的特点。顾明元等人比较了不同制备温度和冷却速率下Al4C3的形貌,其中在制备温度较低(熔体温度708℃)和冷却速度较快(8.2℃/min)的样品中,Al4C3的平均长度为0.35 µm,平均长度比为10,而在制备温度较高(熔体温度748℃)和冷却速度较慢(3.7℃/min)的样品中,Al4C3的平均长度为0.65 µm,平均长宽比为5。
对石墨/铜复合材料热性能的研究国内普遍使用高导热碳纤维或天然鳞片石墨与金属铜复合 [15] - [19] 。目前,制备具有良好综合性能的石墨/铜复合材料主要面临三方面的问题:石墨与铜不反应、不固溶、不相互扩散,导致石墨与铜间的润湿性非常差,润湿角达140˚,使得制备高体积分数的石墨/铜复合材料非常困难。其次,由于石墨/铜复合材料界面热阻较大,也严重制约了石墨/铜复合材料高热传导性能的发挥。第三,由于纤维形状及鳞片石墨原料热性能的各向异性,所制备的复合材料的热性能大多呈现出明显的各向异性。沿纤维轴向或片层方向的热导率较高,而垂直于纤维轴向或片层方向的热导率仍很低,作为电子封装材料使用时必须采用特殊的封装设计方式。
华中科技大学的许尧等人 [20] 采用复压复烧及真空热压法制备了鳞片石墨/铜复合材料,石墨体积分数为40%时复合材料垂直压制方向的平面热导率达到了378 W/(m∙k)。尹延国、焦明华等人采用化学镀铜工艺在石墨颗粒表面镀铜,通过粉末冶金方法制备石墨/铜复合材料并分析了其结构、摩擦磨损性能。研究结果表明,石墨颗粒表面镀铜有利于改善复合材料的界面结合,使其力学性能得到提高,复合材料显示出优良的润滑减磨效果。
尽管高导热热解石墨从比重、散热性上已经具备取代现有热管理材料的条件,但目前却鲜有高导热热解石墨在电子产品中的实际应用。主要是受以下两个因素影响:1) 高导热热解石墨属二维材料,强度低,抗弯强度不足20 MPa,尤其在二维平面方向,其剥离强度极低,这为其在实际构件的应用制造了难题;2) 高导热热解石墨难焊接,无法与电子器件实现组装。传统的焊料无法对高导热热解石墨形成良好的润湿,少数为实现高导热石墨与其它构件的连接,采用粘接的方式,但粘接界面巨大的热阻,使得高导热石墨作为热沉的传热效果明显下降。针对上述问题,国内少数科研工作者针对高导热热解石墨与铜、铝等传统热沉材料的连接开展了研究工作,但由于涉及的材料间物性差异较大,大部分研究成果处于基础研究阶段,研究进展缓慢,成本高,工艺复杂,无法进行实际构件的制造。
近年来,金刚石增强铝基复合材料由于具有很高的热导率(350~670 W/m∙K),成为高导热、低膨胀铝基热管理材料的研究热点。然而,金刚石极高的硬度给材料的加工带来了很大的困难,此外昂贵的价格也大大限制了该材料的应用。除了金刚石以外,石墨材料同样具有极高的潜力。理论上,石墨晶体沿基平面具有极高的热导率(~2000 W/m∙K),而且在α轴向上具有近零的热膨胀系数。如果将石墨材料与铝或铜按一定的方式和配比制备成石墨–铝或铜复合材料,则有望获得高导热、低膨胀的性能,以及优良的可加工性,具有极为广泛的应用前景。对于解决制约高功率器件发展与应用的瓶颈,满足航空航天微波集成电路、功率模块、军用射频系统芯片以及高功率LED照明等领域散热的迫切需求,以及提高武器装备的水平有重要的现实意义。但我国直到近年来才开始有研究机构和企业对石墨/金属复合材料进行了开发研究,而国外企业已有相应牌号的产品出现。国内对石墨/金属复合材料热性能的研究起步比较晚,材料性能与国外产品相比还存在较大差距。
3. 抗腐蚀/散热复合涂层
大功率LED一般采用铝合金散热基板,在有空气流动的环境下具有良好的散热效果,但如果把这种散热器用在密闭环境,传导和对流散热则很差,而依靠辐射方式进行散热尤为重要。通过在铝散热基板外表面设计高发射率辐射散热涂层(图4),是解决大功率电子器件(如大功率LED)散热性差的必要途径。如果通过辐射散热使大功率LED结温降低10oC,则寿命将提高2倍以上,光能量也显著增加。
“集成化、小型化、模块化”是电子器件的重要发展方向,因此,如何解决大功率器件的有效散热成为关键技术难题。功率模块工作时,一部分转化成为热能。如LED的功率模块的光效一般只有100 LM/W,其电光转换效率大约只有20%~30%左右。也就是说大约70%的电能都变成了热能。一般工作在小电流IF < 10 mA,或者10~20 mA长时间连续点亮LED温升不明显。每当结温升高10度,则波长向长波漂移1 nm,且发光的均匀性、一致性变差。更为严重的是,过高的温度会降低LED灯泡中电子元件,特别是电容部分的寿命,从而使整个LED灯泡的寿命降低。功率模块的过热失效,是导致该器件失效或影响其工作寿命的首要原因。通过功率模块的散热结构与辐射降温涂层设计,是解决大功率电子器件散热性差的必要途径。
最近几年国内外企业与研究机构非常关注高发射率涂层辐射散热新方式,而目前金属基板(如LED)辐射散热涂层材料是有机树脂粘结高发射率填料制成的涂料。那么高发射率涂层对散热基板辐射降温效果如何呢?美国Sarang V. Muley教授 [21] 2014年发表在JOM上的文章重点评述了传统电子器件材料
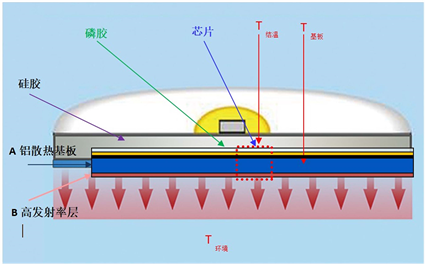
Figure 4. Schematic diagram of high-power LED heat dissipation substrate and packaging structure
图4. 大功率LED散热基板及封装结构示意图
通过高发射涂层强化散热热管理的重要性。台湾Yi-An Sha等 [22] 用特殊的高辐射陶瓷相与高分子相复合涂覆,在13瓦的LED灯珠铝散热基片上制备了于4~14 μm红外波段均具有高发射率的涂层,通过辐射散热使涂层后LED灯珠的结点温度比无涂层的降低13.5℃,光能量增加了14%。
有机高分子粘结的高发射率辐射散热涂层有诸多缺点,因此市场上很少在大功率器件的散热系统中应用,主要原因是:1) 第一,有机粘结相如丙烯酸共聚树脂、聚乙烯缩酸类树脂、环氧树脂、有机硅胶脂等做为高辐射填料的网状连接基体,有机相热导率很低,相当于热障碍层,不利于散热;2) 有机相发射率低,不利于提高涂层整体发射率值;3) 有机相耐热性能和热稳定性差,容易老化失效,特别是受热时因热膨胀系数差别大,与铝散热基片贴合不理想;4) 辐射散热涂层需要先吸热,然后将热量转为红外辐射发射出去,从而达到散热的目的,但涂层和散热片之间因热膨胀差别大微观上存在贴合间隙,导致产生很大的接触热阻。总之,因散热不良而导致芯片结温迅速上升和有机粘结基体碳化变黄,从而造成器件的加速光衰直至失效,甚至因为迅速的热膨胀所产生的应力造成开路而失效。
美国等西方国家已经将微弧氧化技术应用于军事方面。西方国家对于高可靠功率器件的防护技术非常关注,并做为一种重要的战略性国防军工技术,一直严格保密并限制出口。尤其海洋气候环境中使用的电子元器件壳体在服役过程中对材料的要求越来越高,越来越苛刻,不但要求具有优异抗腐蚀性能,还需要优异的散热性能。因此,利用微弧氧化电解液中高发射率、高导热纳米组元的掺杂设计,在高导热铝基板原位生长构建含SiC与AlN协同强化导热与发射率的纳米Al2O3基全新结构复合涂层,以获得导热/高发射率辐射散热多功能陶瓷涂层,将是未来发展的方向。
4. 结论与展望
大功率LED的散热问题对其性能和可靠性具有重要影响。高导热热解石墨作为一种理想的热管理材料,在导热性能上展现出巨大优势,但其低强度和难焊接性是当前应用的主要障碍。通过优化复合材料制备工艺和界面处理技术,有望克服这些难题,推动高导热石墨/金属复合材料在大功率LED散热领域的应用。同时,高发射率辐射散热涂层和微弧氧化技术为提升密闭环境下电子器件的散热性能提供了新的解决方案。
未来,随着材料科学和制备技术的不断进步,高导热石墨/金属复合材料的性能将得到进一步提升,其在大功率LED及其他高功率电子器件中的应用将更加广泛。此外,多功能导热/辐射散热涂层的研究也将不断深入,为提升电子器件的散热性能和可靠性提供更多可能性。同时,国际间的技术合作与交流将促进相关技术的快速发展,推动全球电子散热技术的革新与进步。