1. 引言
沸腾是指液体内部生成汽泡或气相并由液态转变为气态的一种剧烈的汽化过程 [1],沸腾过程中同时存在汽化潜热传热、气液置换传热以及微对流传热等多种传热机理,因此能够在较小温差下达到很高的传热系数。沸腾传热的高传热效率使其在核能、锅炉等多个领域有着广泛的运用。沸腾传热的强化是一个重要的前沿研究领域,许多学者针对强化沸腾传热方法开展了研究。现有的强化沸腾传热方法主要包括改变沸腾工质特性、外加矢量场以及改变表面特性(改性表面法)。与前两种方式相比较,改性表面法集合了易操控、易批量生产、无外加能耗、附加影响小等诸多优点,有望满足核能系统苛刻的技术限制要求。鉴于此,本文对基于表面特性的沸腾传热强化技术进行了综述和分析,伴随着改性表面制备工艺以及表面特性精细化测量技术的进步,预计该领域的研究将迎来进一步快速发展。
2. 表面粗糙度对沸腾传热的影响
表面粗糙度是发热面的基本特征之一,研究者很早就开始关注粗糙度对沸腾传热的影响。早在1936年,Jakob [2] 就发现表面粗糙度和表面腐蚀氧化程度对沸腾传热曲线有非常显著的影响。
1960年,Kuihara等 [3] 以水、丙酮、正庚烷、四氯化碳和二硫化碳等多种工质在不同粗糙度表面上进行了池式沸腾实验,研究表面粗糙度对沸腾传热系数的影响规律。实验发现,有效核化点数量随表面粗糙度的增大而增多,同时沸腾传热系数也随之增大。作者认为核化点数量的变化是引起沸腾传热系数变化的主要原因,并提出沸腾传热系数与加热面上汽柱数量的1/3次幂成正比。
1971年,Tolubinskiy等 [4] 以水为工质,在采用不同工艺加工的不锈钢管上进行了池式沸腾实验,实验工况为压力P = 0.4 MPa,过冷度
= 20 K,热流密度q = 25~100 kW/m2。研究发现,粗糙度较大(Ra = 0.8~3.2 μm)的冷拉管的传热系数比粗糙度较小(Ra = 0.1~0.4 μm)的抛光管高出约1.5倍,这与Kuihara等提出的粗糙度影响沸腾传热规律相吻合,即相同热工参数条件下沸腾传热系数随粗糙度的增大而增大。
1977年,Grigor’ev等 [5] 以液氮为工质,实验研究了不同粗糙度铜表面的沸腾传热规律,实验在热流密度q = 10~4000 W/m2范围内进行。研究发现,粗糙度为1 μm和2.5 μm的铜表面的传热系数几乎相同;而粗糙度为0.2 μm的铜表面的传热系数则只有前两者的1/5左右。即在一定范围内粗糙度的增加会导致传热系数增大,而超出这一范围后粗糙度的增加将不再影响传热系数。这与之前研究中对粗糙度影响沸腾传热规律的认识产生了一定的分歧。
2004年,Pioro等 [6] 对已有的研究成果进行了梳理,提出表面粗糙度并不直接影响沸腾传热系数,而是通过影响汽泡核化点数量进而间接影响沸腾传热系数。也就是说只有当粗糙度的增加会导致新核化点的产生时,才会对沸腾传热系数产生影响。如果改变粗糙度后产生的空穴被液体所填满,则无法成为稳定的核化点,也就无法对沸腾传热系数产生影响。Pioro还进一步指出润湿性、空穴形状及空穴尺寸等表面特性参数才是决定一个空穴能否成为稳定核化点的主要因素,而这些因素的改变会对沸腾传热系数产生直接影响。
根据Pioro提出的这一观点,近年来针对表面特性影响沸腾传热过程研究的重心逐渐从粗糙度转移到了润湿性和表面微观几何结构等方面。
3. 表面润湿性对沸腾传热的影响
在研究不同改性表面沸腾传热规律的过程中,许多学者注意到表面润湿性会对沸腾传热过程产生影响。
1993年,Wang等 [7] 在接触角介于18˚~90˚的不同竖直铜板上开展了可视化池式沸腾实验研究,实验压力为1.013 bar,实验装置见图1。为了控制表面接触角的大小,在对加热铜板进行表面处理时严格控制其氧化程度,以达到调整表面特性的目的。实验结果显示,随表面润湿性的增强,沸腾传热系数减小,同时临界热流密度增大。Wang等采用电子显微镜对处理完成后的加热表面空穴数密度进行了采集,并给出了核化点密度关系式:
(1)
其中Dc表征某一过热度
下的最小成核空穴直径。该关系式适用工况为P = 0.1 MPa、Dc < 5.8 μm、
> 12℃。
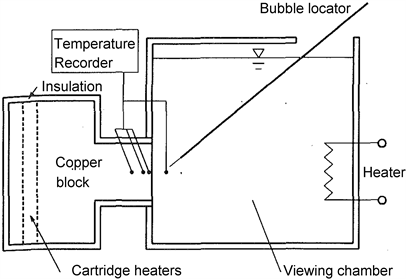
Figure 1. Schematic diagram of experimental device of Wang et al
图1. Wang等实验装置示意图
2009年,Phan等 [8] 以301不锈钢薄片为基底,采用纳米涂层技术制备了不同润湿性表面,接触角范围覆盖了20˚~110˚,并在常压下开展了池沸腾实验研究。Phan等人采用的纳米涂层技术在改变润湿性的同时不会对表面微观结构和化学特性产生影响。研究发现,与未改性表面相比,疏水性表面成核所需的热流密度更低,并且核化汽泡不易脱离,由于高热流时加热面被汽膜覆盖,作者未能获取稳定工况下的传热特性实验数据。对于亲水性表面,随润湿性增强,汽泡脱离直径增大,而脱离频率减小。当接触角小于30˚时,传热系数随接触角的增大而减小;当接触角在30˚~90˚范围内时,传热系数随接触角的增大而增大。Phan等人提出了“微观接触角”和“宏观接触角”的概念对上述实验现象进行了解释。
2010年,Forrest等 [9] 通过化学处理法在镍丝表面制备了粗糙度相同的超亲水、亲水和超疏水纳米涂层,见图2。在以去离子水为工质开展池式沸腾实验后发现,亲水表面的临界热流密度高于疏水表面,但传热系数却低于疏水表面。Forrest等的实验结果与Wang得到的润湿性影响沸腾传热规律完全一致。Forrest认为,纳米多孔结构与表面化学特性的共同作用引起了沸腾传热特性的变化。
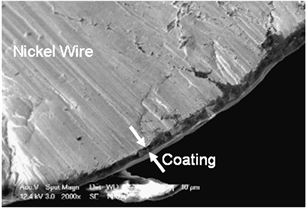
Figure 2. Nano coating under scanning electron microscope
图2. 扫描电子显微镜下的纳米涂层
Betz等 [10] 通过在亲水表面上局部加工疏水点结构,制备出一种同时具有亲水性和疏水性的表面结构。通过实验发现,与普通光滑表面相比,这种混合润湿性表面的临界热流密度和沸腾传热系数分别提高了65%和100%。
2013年,Yang等 [11] 通过溶胶凝胶法制备出具有不同润湿性的改性铝表面,其接触角分别为5˚、75˚、150˚,见图3和图4。经池式沸腾实验后发现:疏水性表面成核时的壁面起始过热度最小;当壁面过热度相同时,亲水性表面的热流密度最大,且汽泡产生率和形状会严重影响热流密度;当热流密度较高时,亲水性表面上汽泡较少,液体与加热表面接触面积更大,可以传递更多热量。Yang实验中发现的规律与Wang与Forrest等刚好相反。
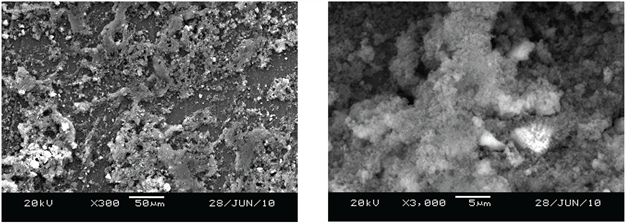
Figure 3. Modified aluminum surface under scanning electron microscope
图3. 扫描电子显微镜下的改性铝表面
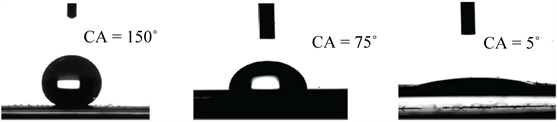
Figure 4. Contact angel of aluminum surface modified by different wettability
图4. 不同润湿性改性铝表面的接触角
赵鹏飞等 [12] 通过烧结、化学制备等多种工艺制备了疏水性表面和超疏水性表面,并以去离子水为工质开展常压下的池沸腾实验。研究发现,在一定热流密度范围内,疏水改性后的表面能够提高沸腾传热系数,而超出这一热流密度范围后,疏水改性后的表面反而会恶化传热。
2019年,马强等 [13] 采用化学刻蚀、修饰的方法,制备了四种不同润湿性表面,通过开展池沸腾实验研究发现,当壁面过热度较低时,疏水性表面的传热系数高于亲水性表面,而当壁面过热度较高时,疏水性表面得传热系数低于亲水性表面。这主要是因为低热流密度时,疏水性表面的沸腾起始点早于亲水性表面,相变带来较大的传热量;而高热流密度时,亲水性表面汽泡脱离直径较小,脱离频率快,因此传热系数较大。
大量实验研究表明,表面润湿性与沸腾传热特性的一般规律为:随润湿性增强,传热系数减小,临界热流密度增大;通过在亲水表面合理布置疏水点制备的混合润湿性表面能够同时提高沸腾传热系数和临界热流密度。但也有部分学者通过实验发现与此相悖的规律,这主要是由于沸腾传热性能是多种表面特性参数共同作用的结果,只关注润湿性与沸腾传热性能的关系弱化了其他表面特性参数的影响,具有一定的局限性。此外,改性表面影响沸腾传热规律的根本原因是不同表面微观结构和物理特性对汽泡核化产生影响,因此研究表面微观结构对沸腾传热过程的影响具有重要意义。
4. 表面微观结构对沸腾传热过程的影响
上世纪七十年代,美、日两国的研究者开始在沸腾表面加工凹坑等微结构以提高电子器件液冷技术的沸腾传热性能。此后伴随表面微加工技术的兴起,关于改性表面的研究重心也逐渐从常规尺度转移到了微纳尺度。
Rainey等 [14] 采用微米级的固态颗粒对加热表面进行了改性处理,得到了多孔的表面涂层结构,见图5,并在常压下以FC-72为工质开展了池式沸腾实验研究。研究结果显示,该多孔涂层表面的沸腾传热系数最大提高了300%,同时临界热流密度最大提高了64%。
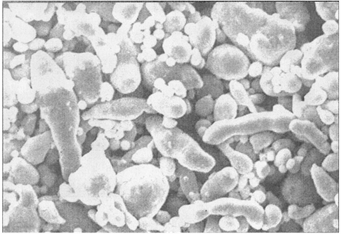
Figure 5. The SEM image of porous coating surface
图5. 多孔涂层表面的SEM图像
2002年,Honda等 [15] 采用微电子加工技术,在硅芯片表面分别加工出微针翅阵列(图6)、纳米级粗糙度表面以及具有纳米级粗糙亚结构的微针翅阵列,并以FC-72为工质开展池式沸腾传热性能实验。实验结果显示,三种微纳结构改性表面均能强化芯片的沸腾传热性能。在热流密度较低时,纳米级粗糙表面的传热系数高于微针翅阵列表面;而在热流密度较高时,微针翅阵列表面的传热系数高于纳米级粗糙表面。在这三种表面中,具有纳米级粗糙亚结构的微针翅阵列表面强化沸腾传热效果最为明显,同时其临界热流密度达到了光滑芯片表面的1.8~2.3倍。
2009年,Chen等 [16] 分别以超疏水性TiO2纳米管阵列表面(图7)和普通Ti金属表面为加热面开展了可视化池沸腾实验研究。研究发现在稳定核态沸腾阶段,TiO2纳米管阵列表面的过热度比普通Ti金属表面低两倍。作者认为是TiO2纳米管阵列表面较大的核化点密度和更大的实际传热面积导致了传热的强化。通过对两种表面池沸腾汽泡动力学特性进行观察发现,在相同工况下,TiO2纳米管阵列表面的核化点密度大于Ti金属表面,并且核化初期TiO2纳米管阵列表面的核化汽泡尺寸远小于Ti金属表面,而汽泡脱离频率则大于Ti金属表面。
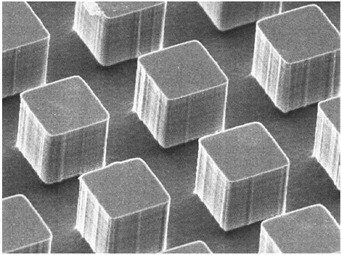
Figure 6. The SEM image of micro fin array silicon chip
图6. 微针翅阵列硅芯片表面的SEM图像
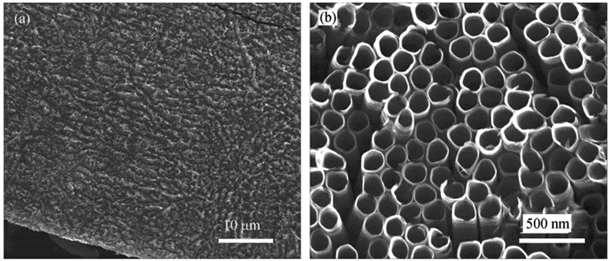
Figure 7. The SEM images of surface with TiO2 nanotube arrays
图7. TiO2纳米管阵列表面的SEM图像
2014年,Dong等 [17] 通过观察微柱、微坑、纳米线、纳米孔四种不同尺度微结构单晶硅表面在乙醚中的池式沸腾过程,发现微米结构表面与纳米结构表面在强化沸腾传热时的机理并不相同:微米结构表面主要是通过增加有效传热面积实现强化沸腾;而纳米结构表面则是由于毛细力作用吸引周围液体再润湿干斑区快速降温阻止了液膜形成,从而降低过热度,延缓了沸腾的恶化。
2015年,Kim等 [18] 对普通表面和十二种不同尺寸的微纳结构表面的沸腾过程进行了对比实验研究,发现与普通表面相比,微纳结构表面沸腾传热系数最高提高300%,临界热流密度最高提高350%。Kim认为微纳结构表面强化沸腾传热的原因主要有两方面:一是微纳多孔的存在增大了表面传热面积,二是微结构表面毛细力促进了周围过冷液体向干斑区的回流。定量分析结果表明,有效传热面积提高对强化沸腾的影响在30%以下,而毛细力的强化传热作用在70%以上。
近年来,国内针对表面微观结构影响沸腾传热也开展了大量研究工作。2017年,胡柏松 [19] 等通过线切割工艺加工微槽,再采用阳极氧化法制备TiO2纳米管阵列,得到了微纳结构耦合表面。通过开展池沸腾实验研究发现,与光滑表面相比,微纳结构耦合表面的歘人呢系数和临界热流密度分别提高了158.3%和50%。作者分析认为,微纳耦合表面比表面积更大,并且微结构为汽泡生长提供了支撑,有效避免了加热面被汽膜覆盖,此外微纳耦合表面在高过热度时具备较多活化核心,这些因素共同导致了微纳耦合表面的传热强化。
随着表面改性工艺的发展,表面微观结构的加工也逐渐迈向精细化。2019年,伏泊霖 [20] 等人利用飞秒激光技术在光滑铜表面制备了微槽纳米复合结构,通过控制激光技工区域来改变微纳结构占比,从而实现对表面沸腾传热特性的控制和优化。通过对多种微纳结构拼接表面进行池沸腾实验,验证了微纳结构占比可以实现沸腾传热系数和临界热流密度的调控,并且当微纳结构占比为3/4时传热系数和临界热流密度提升最为显著。作者还从汽泡生长脱离角度对微纳结构拼接表面强化传热进行了分析:拼接表面能够有效阻碍汽膜的形成,而微纳结构区域的强毛细力作用可以促进汽泡的脱离。汽泡的持续产生和快速脱离最终促成了沸腾传热的全面强化。
综合以上研究可以发现,通过加工表面微观结构能够改变沸腾传热特性,并且不同量级微观结构作用于沸腾传热的效果和机理有所差异。研究认为,微米级微结构表面主要依靠其较大的比表面积来强化热量传递,而纳米级微结构则通过增大毛细力来加速汽泡脱离和液体回流从而强化传热。
虽然目前针对微观结构表面的研究已经取得了一些阶段性的研究成果,但目前的研究主要还集中在定性研究上,关于微结构型式和几何参数与传热特性之间的定量关系还有待深入的探索发掘,关于不同尺度微观结构作用于强化沸腾传热的机理还有待进一步的研究。
5. 结论
本文回顾了近年来关于表面特性对沸腾传热过程影响的研究成果,主要结论如下:
1) 粗糙度、润湿性以及表面微观结构均对沸腾传热过程产生影响,总结现有实验研究发现,一定范围内,沸腾传热系数随粗糙度增大而增大,随润湿性增强而减小;临界热流密度随润湿性增强而增大;相较于光滑表面,在表面加工微观结构能够提高沸腾传热系数和临界热流密度;
2) 在已有的改性表面影响沸腾传热过程相关研究中,大多学者采用了开展实验、观察现象和总结规律的方法,但对于各表面特性参数影响机制的深入挖掘较为欠缺;表征表面特性影响的理论分析手段尚未建立;
3) 伴随精细化加工技术的发展,未来能够实现表面特性多尺度参数的精细控制,进而开展不同表面特性参数影响沸腾传热规律的定量研究。此外,在研究表面特性影响时,将宏观的粗糙度、润湿性等参数与微观的几何特征参数耦合考虑,有助于更全面地认识各参数的作用机制与内在联系。