1. 引言
为了减少环境污染和电能传输过程中的能源损耗,并且在电力运用过程提高操作人员的安全性,无线电力传输技术得以提出并获得广泛地应用。传统的有线充电技术由于需要手动拔插、人工连接,蓄电池组和充电导线也随之频繁移动,从而导致设备本身容易老化、破裂,不仅造成了能源损失而且也给用户使用过程中带来较大的安全隐患。无线充电技术 [1] 的应用很好的解决了这几方面的问题。
电动汽车无线充电技术的本质是电能交流–直流之间的转换、电能–磁能的转换、频率选取的转换三个方面 [2] [3] ,其基本原理的示意图1如下。
基本的电动汽车无线充电系统包括交流电源、整流滤波模块(原、次级),升频模块、补偿网络(原、次级)、电磁线圈(原、次级)。整流滤波模的原级模块主要是对电网或电源的能量进行交–直变换并对交流电能进行平整。升频模块主要是将原有的工频升级为KHz~MHz级别,从而减少空隙中的耦合损耗。补偿网络用于解决耦合机构引起的漏感而形成的无功功率,当无功功率较大时,传输的有效功率即会降低,从而降低传输效率 [4] 。原、次级电磁线圈之间进行了电场能到磁场能再到电场能的转换,电动汽车进行感应式无线耦合时空气间隙一般在10~50 cm之间。为了响应绿色出行的生活方式和实现节约能源的目的,学术界将提高电动汽车无线能量传播的效率作重点研究方向。本文通过线圈材质选择、线圈结构几个方面对当前关于电动汽车无线充电技术提高效率的原理和成果进行了分析和总结,并对该领域未来的研究
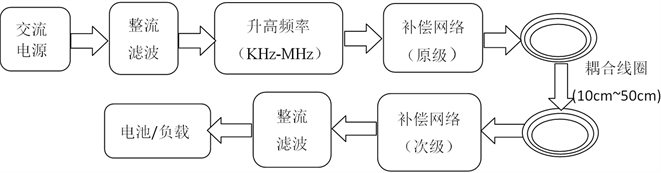
Figure 1. Basic structure of wireless power transfer system in EV
图1. 电动汽车无线充电基本结构图
方向进行了展望。
2. 线圈材质
无线充电电动汽车系统中,对线圈材质的选型要求主要是解决线圈本身趋肤效应和邻近效益而引发的能量损耗,导线的趋肤效应是指当导体中存在交流电或导体处交变电磁场时,导体内部电流分布不均匀,从而使得电流分布于导体表面的现象。导体的邻近效应指的是存在高频电流的两个导体彼此间存在反向电流时,导体内部的电流会集中于导体临近侧流动。趋肤效应在数值上的公式形式可由波导方程具体获得,波导方程 [5] 具体形式如下(1):
(1)
式(1)中σ表示电导率,μ为真空磁导率,式中的
为传导电流密度和位移电流密度的比值,由此可得(2):
(2)
用δ表示透入深度,即趋肤效应,其值如下(3):
(3)
2.1. 超导材料线圈
超导材料具有在绝对温度下小电阻甚至无电阻的特点,是近期研究者关注的热点。通过选择内阻值小的材料,可以使Q因子下降 [6] [7] [8] [9] ,由于耦合原、次级线圈频率一致,以共振频率为基础而制成的线圈对于无线传输过程十分必要。而频率的表达式如(4):
(4)
(5)
Q因子的实际意义在此处则表征为能量比率,
表示通过实际线圈耦合所传输的能量,
表示实际线圈中损耗,I. S. Jeong的研究团队 [10] 通过选取在开式温度93 K条件下能够正常实现超导的材料,在液态氮的条件下建立了实验温度条件,并且在阻抗、电感等特性上与以铜为材质的线圈进行了对比,其结果如表1。
可以明显看出超导材料的阻抗特性和Q因子优于以铜为代表的普通材料,但由于当前学术界研究发现的超导材料都需要在特定温度下才能发挥出超导特性,材料本身在常温条件下不能实现超导状态,因此其不能得到广泛运用。石墨烯是一种二维晶体,呈现蜂窝状,具有良好的导电、导热效应,目前在电池储能方面具有良好的应用前景 [11] [12] ,是未来电动汽车无线充电线圈选择的理想材料。
2.2. 利兹线圈
对于诸如线圈、电感器或变压器等电感元件,采用独立绞合线可以用来降低工作频率较高的应用中的传导损耗,同时也可以减少涡流损耗。利兹线内部结构可以描述为多股线圈形成的细导线捆束,这种多线细化的模式,使得磁场中的趋肤效应限制在细线本身的小范围内,从而达到大捆线圈低损耗的效果。同时该模式也使电流密度均匀分布于大截面积导线上,减少了导线本身的内阻抗。如图2所示。
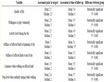
Table 1. Comparison of electrical characteristics of superconducting and copper materials
表1. 超导材料和铜材料的电特性对比
(a) (b)
Figure 2. (a) Coupling double-disc coil current density distribution model for Litz wire; (b) A model of induced current density distribution of a copper wire coil acting on a single conductor
图2. (a) 平面板利兹线圈耦合时的电流密度分布模型;(b) 铜质螺线圈在单导线作用下的感应电流密度分布模型
铜线和利兹线的趋肤效应仿真结果有着明显的区别。采用铜作为导线材质时,导线内部电流密度分布会明显偏离导线中心,而在利兹导线的仿真模型中会呈现出较均匀的分布情况。P. Asbeck等研究者 [13] 对利兹线存在的趋肤效应和邻近效应的数值表达形式进行了细致的推导,由于趋肤效应的正交性和邻近效应的反向性,利兹线束中会产生损耗,该损耗可以分别计算 [14] 。每束利兹线上的趋肤效应损耗由直流损耗中的附加系数表示。直流损耗和趋肤效应损耗的总和可以表示为式(6):
(6)
其中
是捆绑级别i上的趋肤效应因子。线中的趋肤效应损失由
表示。总的趋肤效应在数值上的一般符号是
(7)
(8)
(9)
其中
和
是第一类贝塞尔函数,
是利兹线束趋肤深度,
是自由空间的渗透率,
是相对磁导率,f是频率,
是束或束的电阻率。直流电阻是
(10)
其中
是绞合线中的股数。
对邻近效应的数值运算结果为:
(11)
其中趋肤效应的因数值G的数值形式为:
(12)
但实际上利兹线在布置于耦合线圈的结构中时,会出现线捆的扭曲现象,因而导致实际的趋肤效益和邻近效应与J. A. Ferreira团队 [15] 构建的双模型仍有偏差。而研究者Budhia M [16] 等对这一特殊现象进行了数值近似计算,并证明了扭曲现象引起的偏差可以忽略。
2.3. 材料选型的总结与对比
对耦合线圈材料的选择考虑的因数一般较多,除了导体本身电导率这一基本导体因数,各种导线在磁场中的趋肤效应、邻近效应、导体本身的价格、导体自重都是需要考虑的因素,表2列出了各种材质导线的优劣。在实际的电动汽车无线充电过程中耦合线圈中间存在10~50 cm的间隙,此间隙可以为利兹线圈散热提供空间。选取超导体作为耦合线圈材质时需要匹配相应的温度条件,该温度远超于常温范围,因此当前超导材料未能普及使用,而选取利兹结构的线圈可以降低趋肤效应,从而减少导线内阻损耗,具有更加现实的运用前景。
3. 线圈结构
近年来通过改变耦合线圈的立体结构一直是提升无线电能传输效率的有效方法,也是自无线电能传输兴起以来的研究热点,当前在线圈结构领域存在两种研究思路:改变线圈立体结构、线圈间添加非空气介质材料。
仅从线圈的绕制方式可以将磁耦合结构分为最基本的3种。分别是环形线圈,螺线管线圈和8字形线圈,其中8字形线圈也称为DD线圈(如图3)。这3种线圈各有各的特点。环形线圈是最早采用的磁耦合结构,其绕制方便,分析简单。虽然环形线圈的耦合较差,但是铁损和铜损也很小。研究人员 [15] [16] 随后提出了双DD结构,双DD结构相比单D结构具有更好的偏移修正能力。为了解决偏移修正过程中线圈之间耦合而出现的抵消点,该文章研究人员还提出了补充方案,在DD线圈中添加另一个与两个D线圈盘均匀分割且正切的线圈,以弥补实际程中耦合偏移导致传输效率的下降。为了解决原级和次级线圈大小一致而导致的线圈边缘的漏磁现象,韩国科学院的学者提出了大小线圈结构 [17] ,该结构不仅在满
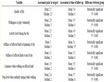
Table 2. Advantages and disadvantages of coupling field made by different material wires
表2. 不同材质的耦合线圈的优劣对比
足充电过程中线圈的抗偏移要求,同时也消除了有效漏磁,避免了电能浪费。
为了进一步减少电动汽车底盘处次级线圈与电源端初级线圈之间的距离从而减少间隙损耗,研究者 [18] 设计了上下轴动机械臂并在该臂下端贴装次级线圈,使传输效率进一步得到提升(如图4(a))。Z. Luo 团队 [19] 通过在线圈盘间加装不同结构的铁磁材料从而引导磁场线更多的传穿过次级线圈来实现效率的提高。对次级线圈加装铁磁介质(如图4(b)),增加了线圈的制作成本和自重,虽然能一定程度上提升传输效率但铁磁材料本身也会形成电场和产生热量,造成电能的损耗。
4. 减小耦合线圈能量损耗的突破点
1) 立体结构的线圈设计问题 [20]
与普通的平面板线圈结构设计相比,立体结构的线圈设计能够使得能量接收线圈最大程度捕捉捉磁场线,从而在不增加自身内阻损耗的同时实现了电能传输效率的进一步提升,由于受到汽车底盘高度的限制,立体线圈结构的弯曲角度宜设置在0~30度的角度范围,以实现最好的承接耦合。
2) 导体的内阻损耗问题 [13] [14]
石墨烯以其良好的导电、导热效应特性为当今此材料学科界的热门话题,石墨烯合成才料做成导体必然是无线充电线圈材质选择的主要聚焦点,通过选取这一材料,电动汽车无线充电效率将得到大幅的提升。
(a) (b)
(c) (d)
Figure 3. (a) Single D coil structure; (b) DD coil stricture; (c) DDQ coil structure; (d) Huge-small coil structure
图3. (a) 单D线圈结构;(b) DD线圈结构;(c) DDQ线圈结构;(d) 大小先线圈结构
(a)
(b)
Figure 4. (a) Schematic diagram of the secondary coil grasped by the robot arm; (b) Secondary coil ferromagnetic medium
图4. (a) 机械臂抓接的次级线圈示意图;(b) 次级线圈加装铁磁介质示意图
(a) (b)
Figure 5. (a) Coupling primary coil; (b) The overall structure of the optimization model
图5. (a) 契合结构的原级线圈;(b) 优化模型的整体结构
3) 耦合线圈之间对准问题 [19] [20] [21]
原、次级线圈之间严格对准时,能够减少边缘电磁场能量损耗,从而使能量传输效率能够达到最大化,原次线圈之间如何实现对准是提高电动汽车能量传输的有效手段。针对减少线圈能量损耗的突破点,本文提出了一种综合优化模型的概念,具体设计示意图5。
原级耦合线圈结构是立体类阿基米德螺旋结构,线圈内部的四组定位感应线圈用于耦合大线圈之间的横向平面偏差修正,修正方法是通过将小感应线圈中的四组信号传输给控制器,控制器再控制电控位移轴位移从而实现原、次级线圈对齐。机器臂作用是使得垂直方向上两耦合线圈间的距离进一步减少从而使得其耦合效率进一步提高。在原、次级线圈耦合前,低压小线圈需要进行感应对准。该操作能将线圈中的对准率提高到98% [20] ,通过机械臂的下降作用能将距离减少3~8 cm [18] 。
通过原次级线圈之间的立体契合结构来减少能量损耗目前还没有团队做出实质的成果,其主要瓶颈在于对立体线圈产生的电磁场的精确仿真与数据分析,但随着提高效率手段的精细化,这一研究点必定会是各个无线电能传输研究团队的重要突破点。
5. 结论
本文针对国内外关于电动汽车无线充电耦合线圈间减少能量损耗的相关文章进行了综述,特别是对线圈材质选择、线圈结构等方面进行具体分析,得出了在电动汽车无线充电耦合线圈间减少能量损耗方面亟待解决的问题。并在此基础上提出了耦合线圈类阿基米德立体结构,原级线圈贴装四组小感应定位线圈的结构,机械臂控制次级线圈升降的结构。从而组成了线圈耦合的综合优化模型,为以后该行业研究人员提供了整体的前景思路。
参考文献
NOTES
*通讯作者。